Ремонт автосцепного устройства - Технологический процесс ремонта грузовых вагонов в Барановичском вагонном депо Белорусской железной дороги
При деповском и капитальном ремонте вагонов производится полный осмотр автосцепного устройства. При этом все его съемные узлы и детали независимо от состояния снимаются с вагона и направляются в контрольный пункт автосцепки (КПА) для проверки и ремонта.
После установки вагона на ставлюги и выкатки тележек из-под вагона слесарь по ремонту подвижного состава разъединяет рычаг и цепь расцепного привода путем отвинчивания контргайки и гайки регулировочного болта.
Слесарь по ремонту подвижного состава демонтирует крепление клина тягового хомута и вынимает клин.
Стропальщик с помощью мостового крана и приспособления снимает с вагона автосцепку, подает ее к конвейеру КПА, устанавливает и закрепляет в гнездо подвесной кассеты. Слесарь КПА подает кассеты со снятыми автосцепками по монорельсу на участок очитки, разборки и дефектоскопирования.
С помощью гайковерта слесарь по ремонту подвижного состава снимает болты поддерживающей планки (кроме двух по диагонали), подкатывает тележку-кассету для смены фрикционных аппаратов, которая должна быть с неистекшим сроком ТО и проверена на холостом ходу, поджимает поддерживающую планку, снимает два оставшихся болта и вынимает поглощающий аппарат из хребтовой балки вместе с тяговым хомутом и упорной плитой. При необходимости слесарь сжимает поглощающий аппарат с помощью передвижного гидропресса.
Стропальщик при помощи мостового крана устанавливает тележку-кассету со снятыми фрикционными аппаратами на передаточную колею КПА.
Слесарь КПА захватывает тележку-кассету на участок осмотра и ремонта поглощающих аппаратов, тяговых хомутов и упорных плит.
Клин тягового хомута, центрирующую балочку и маятниковые подвески слесарь по ремонту подвижного состава относит в КПА для осмотра и ремонта в соответствии с технологическим процессом ремонта автосцепного устройства.
Детали автосцепного устройства подаются после ремонта в вагоносборочный участок комплектно: поглощающие аппараты в сборе с тяговыми хомутами и упорными плитами на тележках-кассетах, головки автосцепки в сборе с цепью и обваренным кольцом в подвесных кассетах по монорельсу.
На ремонтных позициях вагоносборочного участка производится осмотр состояния ударной розетки, упоров, деталей расцепного привода. При необходимости сварщик производит сварочно-наплавочные работы.
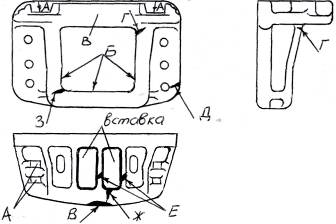
Рисунок 31 ? Дефектация ударной розетки
При ремонте ударной розетки разрешается (рисунок 31):
- А) наплавка изношенных опорных мест А для маятниковых подвесок. При этом используется шаблон 776р; Б) наплавка изношенных поверхностей проема Б; В) наплавка деформированной поверхности в ударной части; Г) заварка трещин Г в верхних углах проема, не выходящих на привалочную поверхность, с постановкой в двух средних углублениях вставок и обваркой их по периметру; Д) заварка трещин Д во фланце; Е) заварка трещин Е на ребрах жесткости в верхней ударной части; Ж) заварка трещин Ж грани ударной части с постановкой в средних углублениях двух вставок и обваркой их по периметру; З) заварка трещин З в нижних углах проема, не выходящих на привалочную поверхность.
При ремонте упоров разрешается (рисунок 32):
- А) наплавка изношенных упорных поверхностей А при износе их более 3 мм. Расстояние между передними и задними упорами должно быть в пределах 622-625 мм. Допускается приварка планок соответствующих размеров, но не тоньше 5 мм; Б) наплавка изношенных мест Б; В) заварка трещин В в ретрах; Г) наплавка изношенных мест Г нижних горизонтальных полок; Д) заварка трещин Д в перемычках объединенных упоров; Е) заварка трещин Е в нижней или средней части упорных поверхностей объединенных упоров, если эти трещины не выходят на привалочную поверхность. Перед заваркой следует подогреть упор до температуры 250 - 300 С0.
Рисунок 32 ? Дефектация упоров
При ремонте кронштейнов расцепного привода разрешается (рисунок 33):
- А) наплавка выработанной поверхности поддерживающего кронштейна в отверстии А для расцепного рычага и места выработки Б в фиксирующем кронштейне; Б) заварка не более одной трещины В в каждом кронштейне; В) заварка разработанных отверстий Г;
При ремонте расцепного рычага разрешается приварка новых частей при условии, что на нем будет не более двух стыков.
Рисунок 33 ? Дефектация кронштейнов расцепного привода
Похожие статьи
-
Основными параметрами производственного процесса являются: - производственная мощность участка; - продолжительность технологического цикла; - режим...
-
Очередность подъемки вагонов определяет старший мастер или мастер ВСУ. Присутствие одного из них обязательно при подъемке и опускании вагонов. Перед...
-
Общие требования при ремонте кузовов грузовых вагонов При всех видах ремонта вагонов на кузовах грузовых вагонов разрешается: [ЦВ-201, п.2.8.1] 1)...
-
Ремонт кузовов вагонов-хопперов моделей 19-7017, 19-7017-01, 19-3116 и других не указанных выше производится в соответствии с требованиями пункта 7.1...
-
Порядок работ После очистки пятника от грязи, наплывов и коррозионных повреждений производится осмотр на наличие трещин, проверяются размеры и крепление...
-
На ремонтных позициях ВСУ бригадир колесно-роликового участка производит входной контроль колесных пар до установки кузова вагона на ставлюги. Ремонт...
-
При деповском и текущем ремонте вагонов разрешается заварка на концевой балке не более трех трещин или одного излома в любом месте балки. [ЦВ-201-98,...
-
При ремонте шкворневых и промежуточных балок грузового вагона разрешается: [ЦВ-201-98, п.2.7.11] Заварка трещин или изломов верхнего листа шкворневой...
-
Все ответственные узлы и детали (тележки, автосцепное и автотормозное оборудование и др.), поступившие для установки на вагон в сборочный цех, должны...
-
Ремонт бортов и закидок платформ производится в соответствии с требованиями пункта 7.1 настоящего технологического процесса При необходимости...
-
На участках средней (базовой) части хребтовых балок, непосредственно примыкающих к нижним листам шкворневых балок, на расстоянии менее 500 мм, а так же...
-
Ремонт кузова и крыши Кузов и крышу вагонов-хопперов для перевозки минеральных удобрений ремонтируют в соответствии с требованиями пунктов 7.1, 7.1.1,...
-
Ремонт кузова и крыши Кузов и крышу вагонов-хопперов для зерна ремонтируют в соответствии с требованиями пунктов 7.1, 7.1.1, 7.1.2 настоящей...
-
Крышу очищают от разрушившегося лакокрасочного покрытия, отслоившейся ржавчины и других загрязнений, осматривают. [ЦВ-587, п. 7.2.3.1] Сварные швы должны...
-
Организация работ Дефектация и ремонт рам вагонов и их элементов производится в соответствии с требованиями пунктов 6.2-6.3 настоящей технологической...
-
Деповской и капитальный ремонт грузовых вагонов производится по истечении межремонтных нормативов, установленных согласно указанию от 11.12.2007 г. №...
-
При деповском ремонте производится частичная окраска вагонов в местах, поврежденных коррозией и с отслоившейся краской. Вновь поставленные детали...
-
Деповской ремонт грузовых вагонов должен выполняться в соответствии с требованиями нормативной документации по охране труда, а именно: "Правил по охране...
-
После установки вагонов на ставлюги на ремонтных позициях тележки подаются на позиции мойки и ремонта в соответствии с разделом 5 настоящего...
-
Ремонт кузова и крыши производят слесари, электросварщики и газорезчики ВСУ, руководствуясь меловыми пометками мастера. Ремонт механизма разгрузки...
-
Заварка не более двух трещин В (рисунок 1) длиной менее 2/3 периметра сечения основных горячекатаных элементов хребтовых балок (двутавр в полувагонах и...
-
Настоящий технологический процесс устанавливает: - порядок выполнения работ по разборке, ремонту, сборке и контролю составных частей и деталей грузовых...
-
Для бесперебойной эксплуатации вагонного парка и содержания его в исправном состоянии на железных дорогах России установлена четкая система технического...
-
Устройство СИТОВ-1 предназначено для проверки технических характеристик тормоза грузовых вагонов после постройки или ремонта и используется в...
-
Ремонт упряжных устройств - Ударно-сцепные устройства электровоза
Тяговые хомуты не допускаются к ремонту, если на тяговых полосах имеются трещины независимо от их размера и расположения, с толщиной перемычки со стороны...
-
Деповской ремонт механизма разгрузки При деповском ремонте разгрузочный механизм осматривают. Неисправные детали ремонтируют. Винтовые приводы...
-
Настоящий технологический процесс описывает процесс ремонта грузовых вагонов в Барановичском вагонном депо Белорусской железной дороги. Настоящий...
-
Анализ неисправностей, устраняемых на участке текущего отцепочного ремонта Текущий ремонт вагонов играет важную роль в обеспечении исправного...
-
Для выполнения качественного текущего ремонта вагонов пункта имеет следующее техническое оснащение: 1-ый путь, длиной 140 м, специализированный на...
-
Производственная мощность депо рассчитывается по формуле: , (2.1) Где N - производственная мощность ТОР, ваг/год; F - годовой фонд рабочего времени...
-
А) ЧР = ?Т/РК Б) ЧР = РК/?Т В) ЧР = РК* Т/tМ Г) ЧР = ТК* tМ/РК Где ЧР - численность рабочих ?Т - общая трудоемкость ремонта вагонов РК -...
-
В этом подразделе пояснительной записки необходимо выполнить планировку участка (отделения), имеющуюся на предприятии по месту практики. Планировка...
-
Проектирование основных участков и отделений - Депо для ремонта пассажирских вагонов
Проектирование вагоноремонтного участка. Вагоноремонтный участок предназначен: - для подготовки вагонов к ремонту, т. е. для их обогрева в зимнее время,...
-
Автосцепное оборудование вагона - Подвижной состав железных дорог
Ударно-тяговые приборы предназначены для сцепления вагонов между собой и с локомотивом, удержания их на определенном расстоянии друг от друга,...
-
Ходовые части вагона - Подвижной состав железных дорог
Колесные пары относятся к ходовым частям и являются одним из ответственных элементов вагона. Они предназначены для направления движения вагона по...
-
Результаты обследования ПТО Вагонное депо Лиски (грузовое) Юго-Восточной железной дороги основано в соответствии с приказом от 11.08.1967г. № 67. На...
-
А) первому уровню оплаты труда по ТСР Б) по второму уровню В) по третьему уровню Г) по четвертому уровню При применении сдельно-премиальной системы...
-
Ремонт автосцепки СА-3 - Ударно-сцепные устройства электровоза
Изгибы хвостовика корпуса автосцепки и уширение зева ремонтируют правкой. Для определения величины изгиба корпус подлежит разметке. Для этого находят и...
-
Технологический процесс ремонта кузовов и кабин в сборе включает разборку, полное или частичное снятие старой краски, дефектовку, ремонт составных частей...
-
ПРЕДИСЛОВИЕ - Депо для ремонта пассажирских вагонов
Деталь вагон ремонт колесный Современный пассажирский вагон представляет собой сложный комплекс разнообразного оборудования, в состав которого входят,...
Ремонт автосцепного устройства - Технологический процесс ремонта грузовых вагонов в Барановичском вагонном депо Белорусской железной дороги