Система осмотров и ремонта автосцепного устройства вагонов - Технология ремонта автосцепок и ударно-тяговых приборов
Для поддержания автосцепного устройства в технически исправном состоянии и своевременного устранения неисправностей установлены следующие виды осмотров: проверка при техническом обслуживании вагонов; наружный осмотр; полный осмотр.
Проверка автосцепного устройства при техническом обслуживании производится на пунктах технического обслуживания вагонов (ПТО), при подготовке вагонов под погрузку, в соответствии с утвержденным технологическим процессом.
Состояние автосцепки и действие ее механизма проверяют шаблоном 873 По методике, представленной на рис. 8.8. Производится внешний просмотр на выявление износов, трещин и изломов в деталях автосцепного устройства. При этом проверяют следующие параметры: уширение зева (рис. 8.8, А); Длина малого зуба (рис. 8.8, 6); Расстояние от тяговой поверхности большого зуба до ударной стенки зева (рис. 8.8, В); Толщину замка (рис. 8.8, г); проверку действия предохранителя от саморасцепа (рис. 8.8, Д).

Рис. 8.8 Проверка автосцепки шаблоном

Проверку действия предохранителя от саморасцепа сцепленных вагонов производят с помощью специального ломика по схеме, представленной на рис. 8.9.
Для проверки действия предохранителя от саморасцепа ломик заостренным концом вводят сверху в пространство между ударной стенкой зева / одной автосцепки и торцевой поверхностью замка 2 Другой сцепленной автосцепки (положение I) И, поворачивая выступающий конец ломика по направлению стрелки, нажимают заостренным концом на замок.
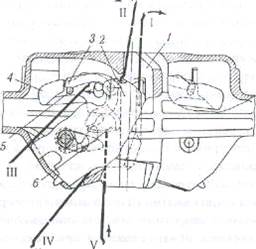
Рис. 8.9. Проверка автосцепки на саморасцеп
Если замок не уходит внутрь кармана более чем на 20 мм и слышен четкий металлический стук от удара предохранителя 3 В противовес 4 Замкодержателя, то предохранительное устройство от саморасцепа исправно. Также проверяют и смежную автосцепку. Иногда ломик не входит сверху, тогда его вводят снизу через отверстие в нижней стенке кармана (положение IV) и, упираясь в кромку отверстия, нажимают на замок в нижней части.
Если при проверке действия предохранителя от саморасцепа замок будет раскачиваться более чем на 20 мм от кромки малого зуба (определяется с помощью заостренной части ломика, имеющей ширину 20 мм) или будет выходить за кромку ударной поверхности малого зуба, то нужно проверить правильность положения на полочке 5 Верхнего плеча предохранителя. Для этого изогнутый конец ломика заводят за выступ замка (положение II) и нажимают на выступающую часть ломика по направлению стрелки, вытягивая замок до отказа из кармана корпуса. Потом следует вновь нажать На замок ломиком, установленным в положение I. Если замок неподвижен или его свободное перемещение значительно уменьшилось, это значит, что предохранитель соскочил с полочки.
Когда автосцепки натянуты и утопить замки при помощи ломика нельзя, надежность работы механизма определяют по состоянию замкодержателя, предохранителя и полочки. Чтобы проверить замкодеп-жатель, ломик вводят в пространство между ударными поверхностями автосцепок сверху или снизу в отверстие корпуса, предназначенного для восстановления сцепленного состояния у ошибочно расцепленных автосцепок (положение V), и нажимают на лапу 6 замкодержателя. Если лапа после прекращения нажатия возвратится в первоначальное положение и будет прижиматься к ударной поверхности малого зуба смежной автосцепки, то замкодержатель исправен.
В случае, когда противовес у замкодержателя отломан, лапа свободно качается и при нажатии на нее ломиком проверяющий не испытывает заметного сопротивления. Заедание замкодержателя внутри кармана корпуса, обнаруживаемое при нажатии на его лапу ломиком сверху, свидетельствует о возможном изгибе полочки для верхнего плеча предохранителя, препятствующем свободному повороту замкодержателя.
Наличие верхнего плеча предохранителя проверяют ломиком, который вводят в карман корпуса через отверстие для сигнального отростка (положение III). Прижимая ломик к замкодержателю, упирают его изогнутый конец в предохранитель и перемещают по направлению к полочке. При этом верхнее плечо приподнимается. Когда ломик отпускают, металлический звук от удара предохранителя о полочку подтверждает, что верхнее плечо предохранителя не изломано. Если ломик при перемещении не упрется в полочку, значит она отсутствует.
Наличие верхнего плеча предохранителя можно определить, если, поворачивая валик подъемника против часовой стрелки, поднять верхнее плечо предохранителя, а затем резко возвратить валик в первоначальное положение. Звук от удара при падении верхнего плеча предохранителя о полочку свидетельствует, что предохранитель не изломан.
При проверке положения осей автосцепок не допускается высота оси автосцепки над уровнем головок рельсов более 1080 мм У локомотивов и порожних грузовых и пассажирских вагонов, менее 980 мм у вагонов с пассажирами, менее 950 мм у локомотивов и груженых грузовых вагонов.
Не допускается разность по высоте между продольными осями сцепленных автосцепок более 100 мм (кроме автосцепок локомотива и первого груженого грузового вагона, у которого допускается разность 110 мм); разность между продольными осями автосцепок смежных вагонов в пассажирских поездах, курсирующих со скоростью до 120 км/ч, более 70 мм, а в поездах, курсирующих со скоростью свыше 120 км/ч -- более 50 мм.
При этом виде осмотра проверяют также расстояние от упора головы автосцепки до наиболее выступающей части розетки, которое должно быть в пределах 60...90 мм при аппарате с полным ходом 70 мм; при укороченных розетках с длиной выступающей части 130 мм и поглощающих аппаратах Ш-2-В, Ш-6-ТО-4, ПМК-110А, 73ZW в пределах 110...150 мм; у восьмиосных вагонов с аппаратами Ш-2-Т в пределах 100...140 мм.
Наружный осмотр автосцепного устройства Производится во время текущего отцепочного ремонта вагонов, единой технической ревизии пассажирских вагонов (ТО-3) для определения работоспособности устройства в целом. Наружный осмотр производится без снятия сборочных единиц автосцепного устройства с вагона.
Автосцепное устройство перед наружным осмотром очищают от загрязнений, выявляют трещины, износы, деформации деталей, проверяют действие механизма и состояние деталей автосцепки шаблоном 940р (рис. 8.10). Проверка исправности действия предохранителя замка на саморасцеп производится постановкой шаблона 940р, как показано на рис. 8.10, А, И одновременно нажимают рукой на замок (по направлению стрелки), пробуя втолкнуть его в карман корпуса автосцепки. Уход замка полностью в карман корпуса указывает на неправильное действие предохранителя замка. Предохранитель действует правильно (верхнее плечо упирается в противовес замкодержателя при нажатии на лапу ребром шаблона), если замок уходит от кромки малого зуба автосцепки не менее чем на 7 мм и не более чем на 18 мм. Для проверки действия механизма на удержание замка в расцепленном положении шаблон 940р прикладывают как и в предыдущем случае (рис. 8.10, Б).
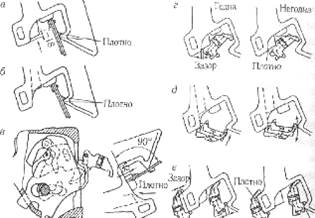
Рис. 8.10. Порядок проверки автосцепок шаблоном 940р
Затем поворотом до отказа валиком подъемника уводят замок внутрь полости кармана и освобождают валик, продолжая удерживать шаблон в зеве автосцепки. Если замок опускается обратно вниз, значит механизм неисправен.
Проверка возможности преждевременного включения предохранителя выполняется при помощи откидной скобы (рис. 8.10, В) Шаблона 940р. Шаблон устанавливают так, чтобы его откидная скоба стороной с вырезом 35 мм нажимала на лапу замкодержателя, а лист шаблона касался большого зуба. Автосцепка считается годной, если при нажатии на замок он беспрепятственно уходит в карман на весь свой ход.
Толщину замыкающей части замка проверяют, расположив шаблон, как показано на рис. 8.10, Г. Если толщина замка больше контрольного выреза в шаблоне, то есть имеется зазор, то толщина замка считается удовлетворительной.
Для проверки ширины зева корпуса автосцепки шаблон располагают, как показано на рис. 8.10, Д. Затем шаблон поворачивают по направлению стрелки, плотно прижимая его опорные грани к малому зубу. Ширина зева считается нормальной, если шаблон не проходит мимо носка большого зуба по всей высоте. Проверка износа малого зуба производится, как показано на рис. 8.10, С. Малый зуб исправен, если его длина больше, чем расстояние между мерительными выступами шаблона, и при надевании шаблона на малый зуб между прямолинейной кромкой шаблона и боковой поверхностью зуба имеется зазор.
Чтобы измерить износы тяговой поверхности большого зуба и ударной поверхности зева, шаблон устанавливают, как показано на рис. 8.10, Е. Износы этих поверхностей будут в норме, если между шаблоном и носком большого зуба имеется зазор. Такая проверка делается в средней части большого зуба по высоте на 80 мм вверх и вниз от середины.
Полный осмотр автосцепного устройства Производят при капитальном и деповском ремонтах вагонов.
При полном осмотре съемные узлы и детали независимо от их состояния снимают с вагонов и передают для проверки ремонта в специальные отделения по ремонту автосцепок ВРЗ или контрольный пункт автосцепки (КПА) депо.
Детали автосцепного устройства очищают от грязи и старой краски в специальных моечных машинах, после чего подают на разборочные стенды, например стенд рис. 8.11.
До разборки автосцепку предварительно осматривают. С помощью системы шаблонов проверяют действие механизма сцепления, а также состояния элементов контура зацепления и других частей корпуса. Зоны корпусов автосцепки, где возможно образование трещин дополнительно расчищают и подвергают диагностированию магнитно-порошковым, вихретоковым или феррозондовым методом.
Перед ремонтом корпуса автосцепки проверяются системой шаблонов: 821 р-1 (рис. 8.12); 892р, 893р, 884р (рис. 8.13) и 827р (рис. 8.14), с помощью которых определяется степень изношенности корпуса автосцепки. Выявляют также изгиб хвостовика и уширение зева, как это показано на рис. 8.2. Если в этих зонах отсутствуют заваренные Или вновь образованные трещины, то для выправки хвостовика и восстановления размеров зева автосцепку нагревают до температуры 800...850 °С и подвергают правке на прессах, один из вариантов Которого представлен на рис. 8.15.
Детали механизма сцепления после разборки также осматривают и проверяют системой проходных и непроходных шаблонов. Детали, признанные годными, передаются на сборку, а детали с дефектами ремонтируют в соответствии с инструкциями.
Выявленные при осмотре и дефектоскопировании трещины подвергают вырубке на всю глубину залегания до целого металла и на 10...15 мм далее видимых границ начала и конца трещины. Операцию разделки трещин перед заваркой необходимо выполнять тщательно, так как обследования показывают, что в случае неполной вырубки трещины в этом месте возникают повторно.

Рис. 8.11. Универсальный стенд для разборки, проверки и сборки автосцепок: / -- пульт управления; 2 -- подвижной стол; 3,4 -- вращающиеся наружные и внутренние гнезда; 5--поворотный кран; Б -- колонна крана; 7, 8 -- шестерни механизма поворота стола; 9 -- несущая обойма; 10 -- вал поворота стола; // -- кулачки колонны стола; 12 -- механический привод вращения крана; 13 -- опоры колонны; 14 -- Поршень пневмопривода; 15, 16 -- валы передачи; 17, 18 -- Кулачки вала и колонны крана
Разделку трещин производят ручным или пневматическим зубилом, кислородной резкой, воздушнодуговой строжкой или электродами типа ОЗР.
Перед заваркой трещин необходимо производить местный предварительный подогрев зоны сварки до температуры 250...300 °С, что обеспечит улучшение сцепления основного металла детали с наплавленным и снизит остаточные термические напряжения от наложения сварочного шва.
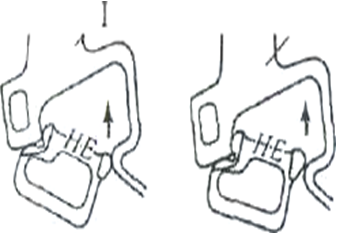
Рис. 8.12. Проверка ширины зева корпуса автосцепкишаблоном 821р-1:
I -- корпус годен; II -- корпус негоден
Если заварка трещин производится непосредственно после электродуговой разделки, дополнительный подогрев не требуется.
Заварку трещин необходимо производить в нижнем положении механизированной сваркой в среде защитного газа СО2 проволокой марки Св-08Г2С или Св-09Г2СЦ диаметром 1,2 мм, а при ручной дуговой сварке следует применять электроды марок УОНИ-13/45 или УОНИ-13/55.
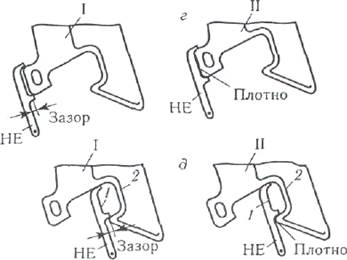
Рис. 8.13. Проверка автосцепки шаблоном 892р, 893р, 884р: о -- длины малого зуба; Б -- расстояние между ударной стенкой зева и тяговой поверхностью большого зуба: I -- корпус годен; II -- корпус негоден.

Рис. 8.14. Пресс для правки корпусов автосцепки: 1 -- станина; 2,3 -- силовые цилиндры; 4 -- нажимные копиры; 5 -- приборы управления; 6 -- гидронасосная станция; 7,8 -- установочнве кондукторы
При наплавочных работах необходимо применять присадочные материалы, обеспечивающие повышенную твердость наплавленных поверхностей порядка НВ 250...450. С этой целью целесообразно использовать порошковую проволоку марки ПП-Нп-14СТ, электроды ОЗН-ЗООМ, а также современные методы наплавки пластинчатыми электродами с легирующими присадками по технологии ВНИИЖТа, индукционно-металлургический способ наплавки и упрочнения, многоэлектродную наплавку и другие.
Ручная дуговая наплавка Является наиболее распространенным способом восстановления. Однако он наименее производителен, так как наибольший ток для наплавки открытой дугой стальным электродом диаметром 4...6 мм составляет только 200...350 А. Увеличение тока приводит к сильному разбрызгиванию металла, перегреву электрода и ухудшению формирования валика. В результате ручной дуговой сварки получается неровная поверхность наплавленного металла, что вызывает необходимость давать припуск на обработку до 2...3 мм.
Механизированную сварку (полуавтоматическую) применяют при сварке деталей, имеющих швы с малым радиусом кривизны, небольшой длины или расположенных в труднодоступных местах, а также при мелкосерийном производстве. При этом используется сварочная проволока, подаваемая в зону сварки подающим устройством шлангового полуавтомата. Защита наплавляемого металла осуществляется флюсами.
Наиболее эффективным способом является способ наплавки порошковой проволоки с помощью шлангового полуавтомата.
Многоэлектродная наплавка Применяется для нанесения слоя металла на поверхность детали с целью их восстановления или упрочнения. Наплавку производят под слоем флюса двумя и более электродами при общем подводе сварочного тока. С увеличением числа проволок ширина и производительность наплавки увеличиваются. Глубина проплавления меньше, чем при наплавке одной проволокой, что способствует снижению чувствительности металла, особенно с повышенным содержанием углерода к образованию трещин, в связи с уменьшением в расплавленном металле ванны доли основного металла.
К полуавтоматическим методам наплавки относится Метод наплавки пластинчатым электродом.Сущность способа состоит в том, что на поверхность детали насыпают слой флюса толщиной 4 мм, который определяет длину электрической дуги. Наплавляемая поверхность располагается горизонтально или с уклоном 2...3° в сторону начала наплавки. Это в процессе горения дуги поможет предотвратить короткое замыкание когда расплавленный металл может подтечь под электрод. На флюс укладывают электрод по специальным упорам флюсо-удерживающего устройства. Электрод представляет собой стальную пластинку, конфигурация и размеры которой должны соответствовать контуру наплавляемой поверхности.
Один конец пластинчатого электрода с помощью держателя соединяется с источником сварочного тока, а другой (обратный) провод этого источника -- через специальные сварочные столы с наплавляемой деталью.
На пластинчатый электрод насыпается слой флюса той же марки толщиной 15...20 мм, необходимый для создания в процессе наплавки шлаковой ванны, обеспечивающей нормальное протекание металлургических процессов и защиту расплавленного металла от окисления кислородом воздуха.
С целью улучшения качества формирования валика, особенно при наплавке широких поверхностей, поверх флюса укладывается прижимная медная или графитовая пластина, обеспечивающая создание давления на ванну расплавленного металла и флюса.
Возбуждение дуги может быть произведено от загнутого конца пластинчатого электрода, соприкасающегося с наплавляемой поверхностью детали в зоне или с помощью металлических опилок, подсыпаемых при укладке электрода.
При замыкании цепи сварочного тока опилки расплавляются, что приводит к возбуждению электрической дуги, которая, перемещаясь по кромке электрода, расплавляет его и флюс.
Преимуществом этого способа является то, что можно восстанавливать изношенные поверхности металлом с повышенной износоустойчивостью, с хорошим формированием наплавленного металла и незначительным припуском на механическую обработку. Это позволит заменить операцию станочной обработки с зачисткой наждачным кругом.
Индукционно-металлургический способ (ИМС) Применяется для восстановления и упрочнения поверхностей деталей вагонов, при котором для нагрева наплавляемых поверхностей и расплавления наплавочного материала используются токи средней и высокой частоты. Сущность индукционной наплавки заключается в нагреве наплавляемой поверхности с помощью индуктора до температуры 1200...1500 °С, локализации энергии в поверхностном слое и расплавлении его вместе с порошковым наплавочным материалом, нанесенным на восстанавливаемую поверхность.
Индукционным способом допускается наносить слои металла толщиной до 5 мм при наплавке, до 3 мм при упрочнении. Тогда толщина слоя наплавленного металла составит 1/3 от исходной высоты насыпаемого слоя порошковой смеси.
При больших износах разрешается сначала наплавлять традиционными способами.
Этот способ позволяет повысить износостойкость поверхностей трения, что увеличивает срок службы детали, резко снижает расходы при эксплуатации восстановленных узлов.
После выполнения наплавочных работ различными способами на корпусах автосцепки и других сборочных единицах выполняют механическую обработку с использованием универсальных и специальных фрезерных, строгальных и долбежных станков со специальной оснасткой. На некоторых ВРЗ применяют специальные станки-полуавтоматы.
Поглощающие аппараты Типов Ш-1-Т, Ш-1-ТМ, Ш-2-Т, Ш-2-В грузовых вагонов при капитальном ремонте должны быть разобраны. При разборке аппаратов необходимо на клиньях и корпусе сделать пометки, чтобы при сборке (в случае исправных деталей) клинья были поставлены на прежние места, что улучшит работу аппаратов, так как поверхности приработаны.
При деповском ремонте разбирают только неисправные поглощающие аппараты с заменой негодных деталей.
Неисправными считаются просевшие поглощающие аппараты, то есть аппараты, у которых расстояние между торцом нажимного конуса и кромкой горловины корпуса аппарата менее 70 мм для аппаратов Ш-1-Т и Ш-1-ТМ, менее 90 мм -- для аппаратов Ш-2-В и менее 110 мм -- для Ш-2-Т.
Аппараты с трещинами или изломами в их деталях, с толщиной стенки горловины корпуса менее 16 мм при выпуске вагонов из капитального ремонта и менее 14 мм из деповского также считаются неисправными.
Нажимные конуса проверяют шаблоном 611 с целью определения износов наклонных поверхностей (не более 3 мм), у фрикционных клиньев измеряется толщина стенки в нижней части, которая должна быть не менее 17 мм для аппаратов Ш-1-Т, Ш-1-ТМ и не менее 32 мм для аппаратов Ш-2-В и Ш-2-Т.
Пружины поглощающих аппаратов осматривают, испытывают и определяют высоту, которая должна быть для аппаратов Ш-1-Т и Ш-1-ТМ наружной не менее 390 мм, а внутренней -- 362 мм.
При поступлении в ремонт вагонов с поглощающими аппаратами Ш-6-ТО-4 производится их осмотр на вагоне. Аппарат считают исправным, если: он плотно прилегает к задним и через упорную плиту к передним упорам; толщина перемычки хомутовоЙ части в отверстии для клина не менее 50 мм; толщина стенки горловины не менее 16 мм; фрикционные клинья плотно прилегают к стенкам корпуса и между ними одинаковый зазор; в деталях отсутствуют трещины в видимой зоне; износ тяговой полосы хомутовой части по толщине не более 5 мм.
При наличии дефектов аппарат должен быть снят и передан в ремонт.
Проверка и ремонт поглощающих аппаратов ПМК-110А и ПМК-110К-23 производится аналогично аппаратам Ш-1-ТМ.
Эластомерные поглощающие аппараты 73ZW''осматривают на вагоне и по клеймам определяют дату последнего технического обслуживания с частичной разборкой или постановки на вагон. Снятие с частичной разборкой аппарата производится при плановых ремонтах после пробега 200--250 тыс. км, но не позднее, чем через 4 года после постановки нового аппарата на вагон или предыдущего осмотра с частичной разборкой.
При отсутствии дефектов, перечисленных в инструкции [17], аппарат считается исправным и демонтаж его не требуется. Доступные части корпуса амортизатора смазывают смазкой РП.
Тяговые хомуты Проверяют внешним осмотром, магнитно-порошковой дефектоскопией и измерениями шаблонами 920р-1 и 861 р-М-Изношенные поверхности и трещины восстанавливают сваркой с последующей механической обработкой в соответствии с требованиями, изложенными в разделе 8.1.4.
После ремонта и проверки на детали наносят в установленных местах клейма, обозначающие условный номер ВРЗ или депо и дату полного осмотра.
Монтаж автосцетюго устройства На вагоне начинается с установки поглощающих аппаратов с хомутом с помощью специальных подъемников между упорами хребтовой балки вагона и закрепления его к хребтовой балке поддерживающей планкой.
Отремонтированный корпус автосцепки с помощью мостового крана хвостовиком вводят в отверстие розетки и после введения хвостовика в проем головной части тягового хомута в отверстие хомута и хвостовика автосцепки вставляют клин и закрепляют его двумя болтами, проходящими через отверстия в нижнем приливе хомута.
После монтажа автосцепного устройства на вагоне производится проверка правильности его установки. При этом проверяются параметры, представленные в табл. 8.1.
Таблица 8.1 Проверяемые параметры автосцепного устройства на вагоне
Проверяемые параметры |
Допускаемые величины после ремонта, мм | |
Капитального |
Деповского | |
Высота продольной оси автосцепки относительно уровня головок рельсов для грузовых вагонов |
1020...1080 |
1000... 1080 |
Разница высот осей автосцепок по обоим концам грузового вагона |
<15 |
<25 |
Отклонение автосцепки вниз (провисание) |
< 10 |
<10 |
Отклонение автосцепки вверх |
<3 |
<3 |
Расстояние от упора головы корпуса до выступающей части розетки: при полностью утопленном положении при выдвинутом положении |
>70 <90 |
>70 <90 |
Зазор между верхней плоскостью хвостовика корпуса и потолком ударной розетки, измеренный на расстоянии 15...20 мм от наружной ее кромки, должен быть в пределах |
25...40 |
25...40 |
Похожие статьи
-
Детали автосцепного устройства в процессе работы подвергаются сложному силовому воздействию, в результате чего в элементах возникают всевозможные...
-
Ремонт автосцепки СА-3 - Ударно-сцепные устройства электровоза
Изгибы хвостовика корпуса автосцепки и уширение зева ремонтируют правкой. Для определения величины изгиба корпус подлежит разметке. Для этого находят и...
-
Повреждаемость поглощающих аппаратов - Технология ремонта автосцепок и ударно-тяговых приборов
Для фрикционных поглощающих аппаратов типа Ш-1-ТМ, Щ-2-В, Ш-2-Т характерны интенсивный износ трущихся поверхностен деталей фрикционной части аппарата...
-
Автосцепка ремонт поглощающий хомут Ремонт автосцепки разделяется на следующие технологические процессы: разборка и определение объема ремонта, правка...
-
Износы и повреждения замка автосцепки представлены на рис. 8.3 А. Естественный, постепенный износ замыкающей поверхности 1 происходит от взаимодействия с...
-
Причины саморасцепов автосцепок - Технология ремонта автосцепок и ударно-тяговых приборов
Система технического обслуживания автосцепного устройства в эксплуатации в основном обеспечивает надежную работу этой сборочной единицы в межремонтные...
-
Основные неисправности и причины их появления Велико влияние исправного состояния автосцепных устройств на безопасность движения подвижного состава. Не...
-
Для обеспечения исправного технического состояния автосцепного устройства производятся следующие виды осмотра и ремонта: Полный осмотр при периодическом...
-
Износы ударной розетки представлены на рис. 8.6, 6. Ударная розетка отливается из сталей 15Л, 20Л, 20ГЛ, 20ФЛ, 20Г1ФЛ. Износ 11 Опорных мест для...
-
При деповском и капитальном ремонте вагонов производится полный осмотр автосцепного устройства. При этом все его съемные узлы и детали независимо от...
-
Повреждаемость тяговых хомутов - Технология ремонта автосцепок и ударно-тяговых приборов
Характерные повреждения тягового хомута представлены на рис. 8.6, А. Трещины / в ушках для болтов, поддерживающих клин, образуются из-за передачи клином...
-
Ремонт упряжных устройств - Ударно-сцепные устройства электровоза
Тяговые хомуты не допускаются к ремонту, если на тяговых полосах имеются трещины независимо от их размера и расположения, с толщиной перемычки со стороны...
-
ЦЕЛЬ И ЗАДАЧИ РАБОТЫ Заданием на письменную экзаменационную работу было предложено описать назначение и конструкцию ударно-сцепных устройств электровоза,...
-
Введение - Технология ремонта автосцепок и ударно-тяговых приборов
Решением Правительства Узбекистана определена программа дальнейшего экономического и рационального развития страны. Большая роль в этой программе...
-
Устройство СИТОВ-1 предназначено для проверки технических характеристик тормоза грузовых вагонов после постройки или ремонта и используется в...
-
Ремонт поглощающих аппаратов - Ударно-сцепные устройства электровоза
Снятые детали осматривают и обмеряют шаблонами. Исправными являются детали без трещин, изломов и с износами не более нормы. Разрешается заваривать...
-
Подготовка к ремонту, Разборка - Ударно-сцепные устройства электровоза
Обязательно снимают автосцепки, тяговые хомуты, поглощающие аппараты, маятниковые подвески, центрирующие балочки. Снятые узлы обмывают в специальных...
-
Технологию контроля состояния деталей и устранения дефектов - Ремонт масляного насоса дизеля 10Д100
Перед ремонтом шестерни необходимо произвести очистку ее от различных видов загрязнений. Шестерня для очистки погружается в ванну с горячим моющим...
-
Проверка крепления карбюратора. 1.2 Очистка приборов системы питания от грязи и пыли. 1.3 Проверка герметичности карбюратора. ТО-1=ЕО+п 2.1...2.2...
-
Разборка-сборка . На крупных станциях технического обслуживания, которые занимаются различными марками автомобилей, могут присутствовать специальные...
-
Основными параметрами производственного процесса являются: - производственная мощность участка; - продолжительность технологического цикла; - режим...
-
Техника безопасности при выполнении слесарных работ - Ударно-сцепные устройства электровоза
Перед началом работы проверить весь инструмент. Слесарные молотки должны быть хорошо насажены. Зубила, бородки не должны иметь трещин и сколов. Проверить...
-
Порядок работ После очистки пятника от грязи, наплывов и коррозионных повреждений производится осмотр на наличие трещин, проверяются размеры и крепление...
-
Диагностирование - Содержание и регламентации системы технических осмотров и ремонтов машин
Диагностирование - Процесс определения технического состояния объекта с определенной точностью (объекты диагностирования -- машина или ее составная...
-
Техническое обслуживание и ремонт подвижного состава, систем электроснабжения и путевого хозяйства На электротранспортных предприятиях Украины...
-
Неисправности тормозной системы - Техническое обслуживание и ремонт тормозной системы
Перечень работ выполняемых при техническом обслуживаний тормозной системы Техническое обслуживание карбюраторов является профилактическим мероприятием,...
-
Осуществляют путем измерения давления в системе гидроусилителя. Для проверки необходимо вставить в нагнетательную магистраль манометр с краном. Замеры...
-
А) первому уровню оплаты труда по ТСР Б) по второму уровню В) по третьему уровню Г) по четвертому уровню При применении сдельно-премиальной системы...
-
В России многолетним опытом автомобильного транспорта и выполненными исследованиями обосновано сформирована система ТО и ремонта. Техническая...
-
Неразрушающий контроль деталей вагонов - Производство и ремонт подвижного состава
Для узла подвижного состава необходимо: 1. Перечислить зоны и возможные методы контроля деталей узла вагона. 2. Изобразить на эскизе все зоны,...
-
Для бесперебойной эксплуатации вагонного парка и содержания его в исправном состоянии на железных дорогах России установлена четкая система технического...
-
При ежедневном техническом обслуживании проверяется [1, 2, 3]: -герметичность соединительных головок; -состояние шлангов подсоединения тормозной системы...
-
Очередность подъемки вагонов определяет старший мастер или мастер ВСУ. Присутствие одного из них обязательно при подъемке и опускании вагонов. Перед...
-
Организация работ Дефектация и ремонт рам вагонов и их элементов производится в соответствии с требованиями пунктов 6.2-6.3 настоящей технологической...
-
Автосцепное оборудование вагона - Подвижной состав железных дорог
Ударно-тяговые приборы предназначены для сцепления вагонов между собой и с локомотивом, удержания их на определенном расстоянии друг от друга,...
-
Валы двигателей и других автомобильных агрегатов являются весьма разнообразными в конструктивно-технологическом отношении и этим определяется различие...
-
Основными видами работ по техническому обслуживанию устройств СЦБ являются: - периодическая проверка взаимозависимостей стрелок и сигналов в соответствии...
-
Основные неисправности якоря тягового электродвигателя и способы их устранения Тяговые двигатели электровозов переменного тока работают в условиях резких...
-
При каждом техническом обслуживании согласно требованиям завода-изготовителя проверяйте состояние элементов передней подвески, обращая особое внимание на...
-
В последне время происходит бурное развитие флуоресцентных методов анализа и создаются новые приборы, работающие на принципе измерения флуоресценции...
Система осмотров и ремонта автосцепного устройства вагонов - Технология ремонта автосцепок и ударно-тяговых приборов