Разработка технологического процесса восстановления посадочного отверстия под передний подшипник скольжения промежуточного вала - Разработка участка по ремонту двигателя ЗМЗ-406, входящего в состав АТСК "Плутон"
Для восстановления посадочного отверстия под передний подшипник скольжения промежуточного вала необходимо разработать специальную установку, обеспечивающую режимы, как для растачивания, так и для наплавки. Карта технологического процесса восстановления изображена на листе НРМ ДП 1390000 ТБ4 графической части.
В состав операций внесем расчеты всех режимных параметров, тогда состав операций будет следующим:
005 Дефектовочная. Измерить диаметр посадочного отверстия на нормальный размер, который равен 51мм. Максимальный износ равен 0,5мм.
Приспособление: Нутромер индикаторный 50-100мм
010 Расточная.
Припуск на обработку определяется по формуле:

(5.1)
Где, D - окончательный диаметр отверстия, d - первоначальный диаметр растачиваемого отверстия
H=52.5-51.5/2=0.5мм.
Выбираем подачу при растачивании в зависимости от глубины резания и обрабатываемого материала:
Глубина резания t = 0.5мм.
Материал - чугун
Подача S=0.10мм/об
Скорость резания выбираем в зависимости от глубины резания и подачи:
VР. табл. = 180ммин
Скорость резания необходимо откорректировать, так как условия обработки отличаются от тех, которые предусмотрены в таблицах. Корректирование заключается в умножении табличной скорости на поправочный коэффициенты для настоящих условий резания в зависимости от марки обрабатываемого материала (kм), Характера заготовки и состояния ее поверхности (kх), марки режущей части резца(kм. р.) и применения охлаждения(kох).
Kм для чугуна ( твердость НВ 181-200) равен 0,90
Kх = 0,5
Kм. р.- для материала резца ВК6 равен 0,90
Kох - (растачивание без охлаждения) 1,00
Расчетная скорость резания равна [9 с,86] :
(5.2)
Vрасч=180*0,9*0,5*0,9*1=70м/мин.
Далее необходимо рассчитать силу резания и частоту вращения шпинделя.
Сила резания определяется по формуле:
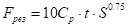
(5.3)
Где,
Ср - коэффициент, учитывающий свойства обрабатываемого материала и условия работы, Ср = 114 (для чугуна НВ 200)
T - глубина резания, t = 0.5мм.
S - подача, S = 0,10 ммоб.
Fрез = 10*114*0,5*0,100,75=100Н
Так же рассчитаем мощность резания:

(5.4)
NР= 100*70/1020*60=0,11кВт
Мощность электродвигателя установки равна:

(5.5)
Где,
- 0,75...0,80 - КПД установки
NДВ = 0,11/0,80=0,15кВт
015. Подготовительная.
В связи с технологическими особенностями обрабатываемого отверстия необходимо произвести ряд операций для подготовки его к наплавке. Необходимо установить керамические заглушки в масляный канал для того, что бы избежать его заплавление. Установить заглушку в предохранительную втулку для обеспечения герметичности с целью заполнения отверстия углекислым газом.
020. Наплавочная
Наплавку целесообразно производить проволокой марки ПАНЧ-11, диаметром 1,4 мм, в среде углекислого газа.
Сила тока дуги, для выбранного диаметра проволоки, определяем по формуле :
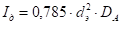
(5.6)
Где,
DA - плотность тока дуги, Амм2
Dэ - диаметр наплавочной проволоки
Значение плотности тока дуги для способа наплавки в среде углекислого газа определяется:
(5.7)
DA= 140-25*1.4=105
Сила тока дуги равна:
Iд=0,785*1,96*105=161А
Напряжение дуги определяем:
(5.8)
Где,
U0- минимальное напряжение дуги, Равное при наплавке в среде углекислого газа 16 вольт
H - толщина наплавляемого слоя, h= 3мм.
Uд= 16+0,04*161*1,36=24В
Скорость подачи электродной проволоки определяем по формуле:
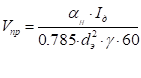
; (5.9)
Где,
Н - Коэффициент наплавки, гА*ч.
-плотность наплавленного металла
Коэффициент наплавки рассчитываем из соотношения:

(5.10)
Н=7+4*1,4=12,6
- принимаем 7,8 гсм3
Тогда, скорость подачи электродной наплавочной проволоки равна:
Vпр=12,6*161/0,785*1,96*7,8*60=2028,6/720,06=2,8ммин.
Скорость наплавки определяем из выражения:
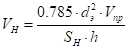
(5.11)
Где,
H - толщина наплавленного слоя
S - шаг наплавки
Шаг наплавки определяется через постоянные параметры
(5.12)
SH=2*1,4=2,8ммоб.
Отсюда следует, что скорость наплавки равна:
Vн=0,785*1,96*2,8/2,8*3=0,51ммин.
Частота вращения мундштука определяется по формуле:

(5.13)
Где,
D - диаметр отверстия равный 52.5 мм.
NM = 1000*0.51/3.14*52.5=3 обмин
- 025. Расточная. Расточить наплавленное отверстие до номинального размера при принятых режимах для операции 010 030. Контрольная. Контролировать диаметр отверстия. Номинальный диаметр посадочного отверстия под подшипник скольжения промежуточного вала равен 51мм.
Для осуществления данного технологического процесса требуется разработать и спроектировать специальную установку.
Похожие статьи
-
Восстановление гильз цилиндров производится по известной технологии, а именно растачивание гильз на ремонтный размер. При растачивании предусматривается...
-
После восстановления и ремонта составных частей необходимо произвести комплектацию деталей с целью обеспечения комплектности для дальнейшей операции...
-
Технологический процесс ремонта двигателя состоит из нескольких операций. В соответствии, рассмотренным в главе1, анализом дефектов двигателя семейства...
-
Для восстановления первоначального зазора или натяга регулируют соединения, обрабатывают детали под ремонтный размер, заменяют соединяемые детали новыми,...
-
Двигатель ЗМЗ-406 - это действительно современный двигатель, являющийся базовым для серии двигателей ЗМЗ-406.3, ЗМЗ-40522.10 Для определения...
-
Для разработки технологического процесса ремонта двигателя необходимо выполнить анализ дефектов и методов их устранения регламентированных заводом...
-
Для увеличения экономической эффективности необходимо дополнять спектр предлагаемых услуг. Исходя из анализа хозяйственной деятельности комплекса,...
-
Для разборки агрегатов и сборочных единиц применяют: - Универсальные передвижные стенды; Электрические (ЭП-1215), гидравлические (ГПМ-14) и...
-
Двигатели, выпускаемые Заволжским моторным заводом Заволжский моторный завод - крупнейший в России производитель двигателей внутреннего сгорания для...
-
АТСК "Плутон" предоставляет следующие услуги: Авторемонтная зона: Гарантийный ремонт автомобилей SUZUKI. Предпродажную подготовку автомобилей SUZUKI....
-
на новые агрегаты -12 месяцев. на новые детали, узлы - 6 месяцев. на замененные запасные части и работы по восстановлению агрегатов, Узлов - 6 месяцев....
-
В состав комплекса входит ряд взаимосвязанных между собой подразделений, классифицируемых преимущественно по видам деятельности: Участок мойки...
-
ТО=(L*i)/(Sм)=(81*1)/(1,024)=79,1 L=длина обработки L=72+7+2=81мм I =число проходов i=h/t=0,1/3=0,03 принимаем =1 H - припуск=0,1м t-глубина резания=3мм...
-
Токарная работа Основное время определяют по формуле (мин), ТО=(75,5*1)/(0,7*250)=0,43 мин L - длина обработки, мм L = + y (мм), L=72+3,5=75,5 Где -...
-
Объем, предоставляемых автокомплексом, услуг в среднем равен 25550 мелких и крупных ремонтов в год. Это значит, что за один день через комплекс проходит...
-
Каждый отремонтированный двигатель должен пройти процесс обкатки, только тогда новые и восстановленные детали, особенно блоки цилиндров, поршни,...
-
Образование автоцентра "Плутон" Торговый лейбл автоцентра "Плутон" известен в городе Новосибирске уже достаточно давно. Автоцентр образовался в 1994...
-
Большинство обслуживаемых в автокомплексе автомобилей зарубежного производства - это видно из таблицы 1. Сегодня принято считать, что ремонт иномарок...
-
Введение - Разработка участка по ремонту двигателя ЗМЗ-406, входящего в состав АТСК "Плутон"
Автосервис - сфера услуг связанная с техническим обслуживанием и ремонтом автомобилей. Бурное развитие автосервиса в России совпало с периодом...
-
Черновое шлифование коренных шеек: Требуемый диаметр: 59,62-0,2 мм; Диаметр шлифуемой детали: 59,9 мм; Используется кругло - шлифовальный станок 3А432....
-
Для гильз, в зависимости от величины износа центрирующих поясков, установлено три маршрута их ремонта. К первому маршруту относят детали с незначительным...
-
Годовой объем работ по каждой операции в отдельности рассчитывают по формуле TГ =tnNКМр(чел/ч) ТГ=5,286*16,82*7000*0,5=311186,82 чел/ч Где t -...
-
Дефект: Износ отверстия под наружное кольцо наружного подшипника Способ устранения дефекта: -ремонтировать 1) Постановка втулки 2) вибродуговая наплавка...
-
Характеристика деталей и условия ее работы - класс детали-круглые стержни - материал - высокопрочный чугун (ВЧ 42-12) - твердость - НВ 140-200 -...
-
Деталь характеризуется по следующим параметрам: - класс детали: полые стержни - материал, из которого изготовлена деталь. Чугун КЧ 35-10-ковкий чугун -...
-
Для токарной операции выбираем токарно-винторезный станок 1Д63А мощность которого N=3 кВт. Переходы: 1. Установить и закрепить деталь 2. Точить...
-
Гильза цилиндр поршневой двигатель В разработке данного курсового проекта предложено приспособление для восстановления внутренней поверхности гильз...
-
Процесс восстановления деталей в авторемонтном производстве является важным элементом, влияющим на технико-экономические показатели выпускаемой...
-
Технологический процесс восстановления деталей составляется в определенной последовательности согласно ТУ на ремонт. Для восстановления деталей...
-
Обоснование размера производственной партии ,шт. (1) Где: q - количество деталей в партии, шт. N - производственная программа изделий в год, шт. N -...
-
Операция - часть технологического процесса выполняемая при обработке определенной детали на одном рабочем месте, одним рабочим до перехода обработки...
-
Исходя из функционального назначения, гильзы цилиндров относятся к главным элементам поршневых ДВС и являются наиболее ответственной деталью ЦПГ. Стенки...
-
Таблица 3- План технологических операций Наименование и содержание операции Оборудование Приспособление Инструмент Рабочий Измерительный 1 2 3 4 5...
-
В процессе эксплуатации автомобиля надежность, заложенная в нем при конструировании и производстве снижается вследствие изнашивания деталей, коррозии,...
-
Дефект Способ устранения № операции Наименование и содержание операции Установочная база Износ шатунных шеек Износ коренных шеек Износ отверстий во...
-
Основой планирования ремонтно - обслуживающих воздействий является определение текущего ремонта. Трудоемкость ремонтных работ выполняемых в мастерской...
-
При выборе оборудования для каждой технологической операции необходимо учитывать назначение обработки, габаритные размеры деталей размер партии...
-
Периодичность ТО-1, км: (2.3) Где - нормативная периодичность ТО-1, км [1]; - коэффициент, учитывающий категорию условий эксплуатации [1]; - коэффициент,...
-
Определяем расчетный коэффициент технической готовности автомобилей по формуле: (2.8) Где - количество дней, готовых к эксплуатации автомобиля за цикл; -...
-
Исходные данные: операция наплавка(010) - деталь: шатунные шейки коленчатого вала ЗМЗ 402; - материал: Высокопрочный чугун; - номер по каталогу:...
Разработка технологического процесса восстановления посадочного отверстия под передний подшипник скольжения промежуточного вала - Разработка участка по ремонту двигателя ЗМЗ-406, входящего в состав АТСК "Плутон"