РАСЧЕТ РЕЖИМОВ РЕЗАНИЯ - Разработка технологии изготовления детали
Рассчитываем режимы резания на 010 операцию, которая состоит из двух переходов: 1 переход - точение черновое в размер O36,51-0,16; 2 переход - точение чистовое в размер 36,146-0,039 на длине 16,4 мм.
Выбираем проходной отогнутый резец с пластиной Р6М5 (сечение державки H ? B = 20 ? 12 мм) по ГОСТ 18868-73.
Геометрические параметры резца: ? = 45°; ?1 = 45°; ? = 6°; ? = 12°; ? = 10°; r = 0,4 мм.
Определение режима резания
Глубина резания определяется в зависимости от величины припуска и требований к качеству обработанной поверхности.
Определяем величину припуска по формуле:

(18)

= 0,755 мм;

= 0,182 мм
Назначаем подачу
Для черновой обработки при наружном точении назначают подачу 0,4 - 0,5 мм/об [3, табл. 11, стр. 266]. Учитывая паспортные данные станка 16К20 [4, стр. 421] принимаем S1 = 0,4 мм/об.
Для чистового точения наружной поверхности назначают подачу 0,25 мм/об [3, табл. 14, стр. 268]. Учитывая паспортные данные станка 16К20 [4, стр. 421] принимаем S2 = 0,25 мм/об.
Скорость резания рассчитывается по формуле:

М/мин (19)
Где Т - стойкость инструмента, мин. Значение стойкости при одноинструментальной обработке - 30 - 60 мин, при работе резцами с напайными пластинами время работы до замены резца принимается равным 60 минут.[3, стр. 268];
Сv, Kv - составляющие коэффициенты; значения коэффициента СV и показателей степени x, y и m выбираем по [3, табл. 17, стр. 269]: - для наружного точения литейных алюминиевых сплавов СV = 328; x = 0,12; y = 0,5; m = 0,28;
T - глубина резания, мм;
S - подача, мм/об;
- произведение поправочных коэффициентов, учитывающих условия обработки, их рассчитываем по формуле:

(20)
Где KMv - коэффициент, учитывающий влияние материала заготовки;
Knv - коэффициент, учитывающий состояние поверхности заготовки;
Kuv - коэффициент, учитывающий материал инструмента;
K?v - коэффициент, учитывающий главный угол в плане резца;
Krv - коэффициент, учитывающий радиус при вершине резца.
=0,9; =1,0; [3, табл. 5,6, стр. 263]; =1,0; =0,94 [3, табл. 18, стр. 271]
[3, табл. 4, стр. 263]
Тогда общий поправочный коэффициент будет равен:

- для чернового точения:

м/мин
- для чистового точения:

м/мин
Частота вращения шпинделя рассчитывается по формуле:

(21)

об/мин;

об/мин.
Уменьшаем подачу до допустимой по паспорту станка n1 = 1000 об/мин; n2 = 1600 об/мин; [4, стр. 421]
Пересчитываем V по принятому nв

(22)

= 119 м/мин;

= 183 м/мин.
Рассчитываем силы резания по формуле:

, кН (23)
Где Cp - коэффициент, учитывающий условия обработки;
X, y,n - показатели степени;
Кр - поправочный коэффициент, учитывающий фактические условия резания.
Поправочный коэффициент рассчитываем по формуле:
Кр = КМ - К? - К? - К? - Кr (24)
Где КМ - коэффициент учитывающий обрабатываемый материал, К? - коэффициент учитывающий главный угол в плане;
К? - коэффициент учитывающий передний угол;
К? - коэффициент учитывающий угол наклона главного лезвия;
Кr - коэффициент учитывающий радиус при вершине.
[3, табл. 10, стр. 265];
Поправочные коэффициенты определяем для тангенциальной силы Pz по [3, табл. 23, стр. 275]: К?р = 1,0; К?р = 1,15; К?р = 1,0; Кr = 0,87.
КрZ = 1,0 - 1,0 - 1,15 - 1,0 - 0,87 = 1,0
Значения коэффициента Ср и показателей степени x, y и n выбираем по [3, табл. 22, стр. 273]:
- для алюминиевого сплава: Pz - Ср = 40; x =1,0; y = 0,75; n = 0.
Pz1 = 10- 40- 0,7551,0 -0,40,75- 1190- 1,0= 151 Н.
Pz2 = 10- 40- 0,1821,0 -0,250,75- 1830- 1,0= 26 Н.
Рассчитываем мощность резания по формуле:

(25)


Мощность на шпинделе станка Nэ=Nд?.
Nд = 10 кВт; ? = 0,8 (по паспорту станка).
Nэ = 100,8 = 8 кВт.
Так как Nэ= 8 кВт > Nmax=0,29 кВт, то обработка возможна.
Основное технологическое (машинное) время - время, в течение которого происходит снятие сружки без непосредственного участия рабочего.

, мин (26)
Где L - путь инструмента в направлении рабочей подачи, мм;
I - количество проходов.
Путь инструмента рассчитываем по формуле:
L = l + l1 + l2 , мм (27)
Где l - размер обрабатываемой поверхности в направлении подачи;
L1 - величина врезания, мм; l1 = 2,0 мм [5, карта 65, стр. 165];
L2 - величина перебега, мм, l2 = 2,0 мм [5, карта 65, стр. 165].
- для наружного точения: L1 = L2 = 16,4 + 2 + 2 = 20,4 мм.


Основное технологическое время для операции 010:
?То = 0,051 + 0,051 = 0,102 мин.

Рассчитываем режимы резания для 020 операции, на которой выполняется шлифование наружной поверхности в размер.
Режущий инструмент - шлифовальный круг ПП 600?50?305 24А 10-П С2 7 КПГ 50 м/с А 1 кл. ГОСТ 2424-83.
Определяем припуск на обработку:

Мм.
По выбранному диаметру круга и паспортным данным станка определяем скорость вращения круга по формуле:

(28)

м/с.
По [6] табл. 161, с. 343 назначаем скорость детали и определяем частоту ее вращения по формуле (1.44): Vд = (27-39) м/мин. Выбираем скорость Vд =28 м/мин:

об/мин.
Найденная частота вращения укладывается в паспортные данные станка.
Рассчитываем радиальную (поперечную) подачу по формуле:
St = St табл - Кst (29)
Где St табл - табличное значение радиальной подачи на ход, мм.;
Кst - поправочный коэффициент на подачу;
St табл = 0,007 мм 6, табл. 163, стр. 346.
Рассчитываем поправочный коэффициент по формуле [6] с. 344:
Кst = Км - КR - КD - Кvк - Кт - К1т - Кh (30)
Где Км - коэффициент, учитывающий обрабатываемый материал;
КR - коэффициент, который учитывает радиус галтели детали;
КD - коэффициент, который учитывает диаметр круга;
Кvк - коэффициент, который учитывает скорость круга;
Кт - коэффициент, учитывающий стойкость круга;
К1т - коэффициент, учитывающий точность обработки;
Кh - коэффициент, учитывающий припуск на обработку;
Км = 1,0; КR = 1,0; КD = 1,0; Кvк = 1,0; Кт = 0,72 К1т = 0,75 Кh = 0,76 6, табл. 165, стр. 348.
Кst = 1,0 - 1,0 - 1,0 - 1,0 - 0,72 - 0,75 - 0,76 = 0,41;
St = 0,007 - 0,41 = 0,003 мм/об.
Определяем радиальную минутную подачу по формуле:
Sм = St - nд (31)
Sм = 0,003 - 250 = 0,75 мм.
Рассчитываем мощность резания по формуле [5] с. 631:
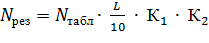
(32)
Где Nтабл - табличное значение мощности резания, кВт;
L - длина активной поверхности круга, при lд < Вк L = lд = 15 мм;
К1 - коэффициент зависящий от твердости круга;
К2 - коэффициент зависящий от обрабатываемого материала;
Nтабл = 0,17 кВт; К1 = 1,16; К2 = 1,0 [5, карта 8, стр. 631];

= 0,3 кВт.
Проверяем рассчитанную мощность резания:
Nдв > ?рез = 10 кВт > 0,3 кВт.
Определяем технологическое время по формуле:

(33)
Где h - припуск на диаметр h=0,146мм;
А - количество врезаний;
K - коэффициент, учитывающий время на обработку галтелей;
К = 1,3 [5, карта 10, стр. 633];

Мин.
Таблица 4 - Сводная таблица режимов резания
№ оп. |
Наименование операции |
Режимы резания | ||||||
D, мм |
L, мм |
T, мм |
S, мм/об |
V, м/мин |
N, об/мин |
To, мин | ||
010 |
Токарная: Черновая Чистовая |
38 |
16,4 |
0,755 |
0,4 |
119 |
1000 |
0,051 |
36,51 |
16,4 |
0,182 |
0,25 |
183 |
1600 |
0,051 | ||
015 |
Токарная: Подрезка торца Черновая Чистовая |
36,146 |
15,7 |
0,7 |
0,12 |
92 |
800 |
0,21 |
28,2 |
15,7 |
0,45 |
0,3 |
88,5 |
1000 |
0,07 | ||
29,1 |
15,7 |
0,3 |
0,2 |
114,2 |
1250 |
0,08 | ||
020 |
Шлифовальная |
36,146 |
15 |
0,073 |
|
Vкр 50 м/с 28 м/мин |
250 |
0,25 |
025 |
Шлифовальная |
29,7 |
15 |
0,15 |
|
|
250 |
0,38 |
030 |
Снять фаски |
36 |
0,6 |
0,6 |
0,1 |
71,2 |
630 |
0,04 |
Похожие статьи
-
АНАЛИТИЧЕСКИЙ МЕТОД РАСЧЕТА НАИВЫГОДНЕЙШЕГО РЕЖИМА РЕЗАНИЯ - Расчет оптимального режима резания
3.1 Глубина резания - определяется из условия обработки: припуска, точности и шероховатости. Припуск на обработку определяется по формуле: Где D -...
-
Токарная обработка Токарная черновая обработка Данному виду обработки подлежат следующие поверхности: - линейные - 3, 6, 21, 24; - диаметральные - 4, 7,...
-
Расчет межоперационных припусков и технологических размеров расчетно-аналитическим методом на механическую обработку поверхности ) мм. Определение...
-
Выбор оборудования Выбираю вертикально сверлильный станок модели 2Н135. Станок предназначен для сверления, рассверливания, зенкерования, развертывания...
-
5.4 Характеристика устройства ЧПУ - Разработка технологических процессов изготовления деталей
Система УЧПУ 2Р22 - оперативная. Предназначена для ввода в память программы на обработку детали с пульта управления, с магнитной ленты или с перфоленты...
-
ТАБЛИЧНЫЙ МЕТОД РАСЧЕТА НАИВЫГОДНЕЙШЕГО РЕЖИМА РЕЗАНИЯ - Расчет оптимального режима резания
Назначение элементов режима резания наиболее просто может быть осуществлено при помощи специальных таблиц, приведенных в общемашиностроительных...
-
Аналитический операция 010 Токарная Глубина резания, мм: T2=1,1мм, i=2. T3=1,15 мм. T4=1,0 мм, i=2. Подача, мм/об: S2=1,3 мм/об [1,стр. 266] SД2 = 1,4...
-
Данному виду обработки подлежат следующие поверхности: - Ш16 с фаской 1Ч45° - 30 и 31 соответственно. Обработка поверхностей будет проходить за 2...
-
Элементы и режимы резания - Технологии машиностроения
К элементам режима резания относятся глубина резания, подача и скорость резания. Глубина резания определяется в основном величиной припуска на обработку....
-
Расчет режимов резания - Ремонт токарного станка
Операция 010. Токарная. Переход 1. Обточить поверхность Ш30+0,35 на длину 155 мм за 3 прохода. Рис. Схема установки заготовки при обработке поверхности...
-
Выбор вида получения заготовки можно оценить по коэффициенту использования материалов по формуле [4, 39]: Ким = , (2) Где Ким - коэффициент использования...
-
Маршрутная технология процесса изготовления деталей - Ремонт токарного станка
Выбор заготовки: при выборе заготовки для механической обработки заменяемой детали нужно учитывать технические требования, предъявляемые к детали....
-
Выбор инструментальных приспособлений произведен по методике изложенной в [13]. Исходные данные: конструкция крепежной части; конструкция посадочного...
-
Определение предельных значений режимов резания При мм/мин - фрезерование пазов за один проход; Дисковая фреза: D=125мм; B=20мм; t=0,6мм; z=22;...
-
ТЕХНОЛОГИЧЕСКИЙ АНАЛИЗ РАБОЧЕГО ЧЕРТЕЖА ДЕТАЛИ - Разработка технологии изготовления детали
Под технологичностью конструкции изделия понимается совокупность свойств, проявляемых в возможности оптимальных затрат труда, средств, материалов и...
-
Производительность обработки " G " определяют числом деталей, изготовляемых в единицу времени: (шт./мин), Т Шт - время обработки, складывается из...
-
Введение, Режим резания и геометрия срезаемого слоя - Режимы резания
Резание технологический трение От современных машин требуются высокие эксплуатационные и технико-экономические характеристики, надежность работы. Проходя...
-
Данному виду обработки подлежат следующие поверхности: - шпоночный паз (10Н9 глубиной 7) - 27. Глубина резания (мм) пов. 27 будет равняться глубине паза....
-
Данному виду обработки подлежат следующие поверхности: - линейные - 4, 16, 7, 9, 13, 19; - диаметральные - 3, 6, 17, 8, 14; - фаски - 2, 5, 10, 12, 15,...
-
ПОСТРОЕНИЕ НОМОГРАММ ОТДЕЛЬНЫХ ЗАВИСИМОСТЕЙ - Расчет оптимального режима резания
Формулы, используемые для расчета режима резания, могут быть выражены графически, в виде номограмм, что в ряде случаев значительно упрощает расчет....
-
Припуск - слой материала, удаляемый с поверхности заготовки в целях достижения заданных свойств обрабатываемой поверхности детали. Припуск на обработку...
-
ВВЕДЕНИЕ - Расчет оптимального режима резания
Сущность технологии изготовления деталей машин состоит в последовательном использовании различных технологических способов воздействия на обрабатываемую...
-
Оценка технологичности детали по точности выполняется с учетом среднего квалитета точности (формула 4.1) и коэффициента точности обработки (формула 4.2)....
-
Глубина резания при сверлении, мм: t =0,5-D, [4, с. 276] Где D - диаметр отверстия, мм. Глубина резания при зенковании, мм: t=0,5-(D-d); t2=0,5-9=4,5 мм....
-
Порядок выполнения заданной детали. Обработка заготовки на токарно-винторезном станке (черновая) I-центра; II-заготовка; III - резец черновой токарный...
-
Заземлению подлежит цех где находится оборудование роторного измельчителя работающее под напряжением 380 В. Грунт-суглинок. Измерения проводились при...
-
Технологическая карта включает в себя все основные технологические операции восстановления. В качестве исходных данных для разработки технологической...
-
Проверяем пригодность роликоподшипников конических однорядных по ГОСТ 333-79, условное обозначение - 7202. Проверим пригодность подшипника по [8;c.103]:...
-
Выбор оптимального режима резания - Режимы резания
Качество и эффективность изготовления деталей машин зависят от рационального проведения процессов обработки заготовок резанием, которое достигается в...
-
Расчет режимов резания - Кинематический расчет привода главного движения станка мод. ВМ127М
Все расчеты производятся по формулам и сводятся в таблицу 1 Таблица-1. Технологические возможности и режимы резания. Материал Технологические операции...
-
Оценка предельно-необходимых инвестиций В условиях рыночной экономики залогом успешной деятельности промышленного предприятия является выпуск...
-
2.1 Выбор материала режущей части (пластины) Для черновой обработки по корке при относительно равномерном припуске или без корки и ударов, а также для...
-
Рассчитываем сменную производительность станка (линии) при выполнении соответствующих технологических операций. 1. Форматно-раскроечный станок Formula...
-
Расчет времени отжига Для расчета времени отжига нам необходимо знать верхнюю и нижнюю границу отжига, а также термостойкость стекла. Эти данные можно...
-
При расчете потребного количества оборудования необходимо привести формулы для расчета производительности с расшифровкой входящих в них параметров и...
-
На каждую операцию технологического процесса назначаем режимы резания согласно нормативным справочникам, а для двух операций (04 Токарная и 38...
-
Размерные цепи и их уравнения Составим уравнения операционных размерных цепей в виде уравнений номиналов. В общем виде это выглядит: [A] = IAI, (3.1) Где...
-
Заварка ламп является основной сборочной операцией при изготовлении ламп. Она заключается в герметичном соединении собранной ножки с колбой. Процесс...
-
Для Токарных работ выбираем токарный станок с ЧПУ модели 16К30Ф3С32 Наибольший диаметр изделия, устанавливаемый над, мм Станиной 500 Суппортом 320...
-
Расчет времени отжига Для расчета времени отжига нам необходимо знать верхнюю и нижнюю границу отжига, а также термостойкость стекла. Эти данные можно...
РАСЧЕТ РЕЖИМОВ РЕЗАНИЯ - Разработка технологии изготовления детали