Вибір схеми технологічного процесу - Аналіз сучасного стану виробництва постійних магнітів
В даний час розроблено декілька технологій отримання магнітних матеріалів зі сплавів Fe-Ni-Al-Со: 1) метод порошкової металургії з подальшим пресуванням і спіканням і 2) ливарний метод.
При ливарному методi сплав розплавляють і виливають у форму. Після твердіння матеріалу виробляється груба шліфовка матеріалу, після чого термообробка і охолоджування, інколи з магнітним полем. При обробці з магнітним полем, получений магніт називається анізотропним. Анізотропні властивості забезпечують максимальну намагніченість і вищий рівень Гауса. Литі магніти, без термообробки в магнітному полі називаються ізотропними. Після термічної обробки і охолоджування матеріал шліфується відповідно до конкретних допусків і намагнічення.
Основним методом отримання магнітів із сплавів Fe-Al-Ni-Co є порошковий. Найбільш широко для виготовлення постійних магнітів застосовують сплави на основі заліза з вмістом 20-33% Ni і 11 - 17% А1, які додатково можуть легованих і іншими елементами, такими як Со, Сі, Ti і ін. Змінюючи склад сплавів і кількісне співвідношення елементів, що входять до їх складу, можна в широких межах регулювати магнітні властивості сплавів. Так, наприклад, збільшення в межах зазначених концентрацій вмісту Ni і А1 призводить до підвищення коерцитивної сили і зниження залишкової індукції. При цьому вплив Ni більш істотно, ніж Аl.
Легування сплавів, що містять близько 23% Ni і 10-15% А1, міддю також сприяє підвищенню коерцитивної сили та залишкової індукції. При більшому вмісті нікелю вплив міді дещо інше. У цьому випадку при підвищенні коерцитивної сили залишкова індукція зменшується.
Коерцитивної сила також підвищується при легуванні сплавів кремнієм і титаном при введенні їх до 1%. Подальше збільшення вмісту титану приводить до зменшення опуклості кривої намагнічування. Позитивний вплив проявляється також у зв'язування вуглецю в стійкі карбіди. Домішка вільного вуглецю навіть в кількостях, що не перевищують 0,1%, значно знижує коерцитивної силу і магнітну індукцію.
Найбільш сприятливий вплив на магнітні властивості залізонікельалюмініевих сплавів надає кобальт. При цьому вплив кобальту на магнітні властивості сплаву також суттєво залежить від вмісту нікелю та алюмінію. Так, при вмісті в сплаві 15 - 19% Ni і 13% А1 кобальт викликає підвищення коерцитивної сили та зменшення залишкової індукції, а при вмісті 21% Ni обидві ці характеристики значно зростають.
Для отримання максимальних магнітних властивостей розглянутих сплавів обов'язковим є їх термічна або термомагнітного обробка, що складається в гартуваннi і відпустці. Загартування повинна забезпечувати велику швидкість охолодження, ніж це потрібно для фазових перетворень, а відпустка - випадання дисперсної фази.
У якості вихідних компонентів для виготовлення магнітів на основі залізонікельалюмініевих сплавів застосовують порошки чистих металів або сплавів, отриманих карбонільні або електролітичним методом, спільним відновленням оксидів, розпиленням рідких металів і сплавів, а також порошки феросплавів, отримані методом подрібнення.
При виготовленні постійних магнітів із сплавів Fe-Ni-Al-Со принципово можливі три варіанти технологічної схеми:
- 1) змішування порошкоподібних складових сплаву у вигляді порошків чистих металів, пресування суміші та спікання виробів; 2) змішування порошків заліза, нікелю, кобальту, міді з порошками лігатури Al-Ni і Al-Fe, пресування і спікання; 3) подрібнення відходів литого сплаву необхідного складу з наступним пресуванням і спіканням.
Недоліком першого варіанту є наявність на частинках порошку алюмінію тонкої плівки оксиду алюмінію, що перешкоджає нормальному спікання. Внаслідок низької температури плавлення алюмінію (~ 660 ° С) і більш високої температури спікання, що забезпечує дифузію між всіма компонентами сплаву, алюміній довгий час перебуває в перегрітому стані, що призводить до його окислювання і азотування газами, що містяться в захисному середовищі спікання. Останні процеси (окрім освіти немагнітних фаз) викликають втрати алюмінію, порушують хімічний склад, що негативно позначається на магнітних властивостях сплавів.
Другий варіант дозволяє усунути недоліки першого - окислюваність і низьку температуру плавлення порошку алюмінію. Це досягається введенням алюмінію у вигляді лігатур.

Рисунок 1.1 Технологiчна схема отримання лігатури Al-Fe
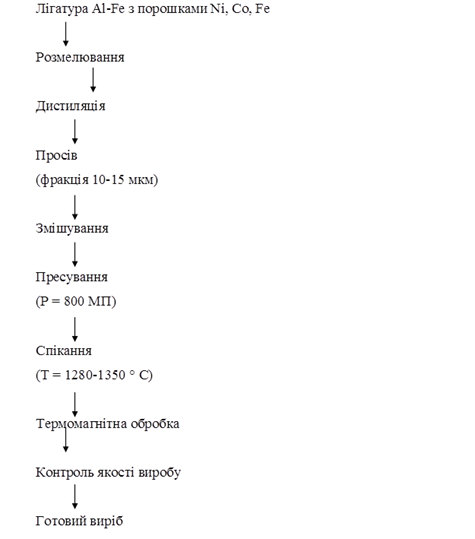
Рисунок 1.2 Технологічна схема виробництва магнітів із сплавів типу Алніко
Найбільш часто для виробництва магнітно-твердих матеріалів використовують карбонільні порошки заліза і нікелю. Застосування порошків зазначених металів, отриманих іншими методами, зумовлює зниження магнітних властивостей одержуваних матеріалів.
За третього варіанту в якості вихідних матеріалів використовують відходи традиційних методів виробництва магнітів литтям з наступною механічною обробкою - ливарні відходи та стружку. У цьому випадку із зазначених відходів шляхом плавлення з наступним розпиленням отримують порошок магнітного сплаву, який і є вихідною сировиною для отримання магнітів методами порошкової металургії.
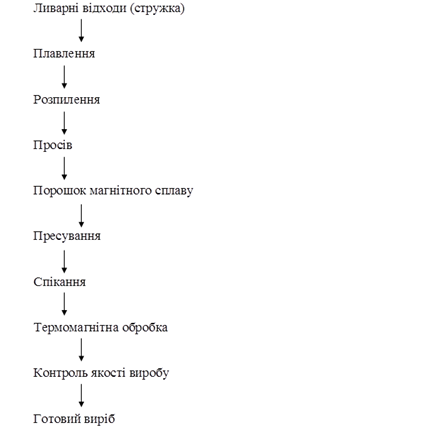
Рисунок 1.3 Технологічна схема виробництва магнітів методом подрібнення відходів литого сплаву
Отриманий таким чином порошок має високу твердість, тому пресування заготовок із нього методами прямого пресування при кімнатній температурі утруднено. Більш доцільно застосовувати гаряче пресування в сталевих прес-формах при температурі 1100-1200 ° С в захисному середовищі. Отримані при цьому магнітно-тверді матеріали за властивостями значно поступаються матеріалами, отриманими по другому варіанту. Це обумовлено тим, що в процесі отримання вихідного порошку розпиленням розплаву, а також при гарячому пресуванні матеріал частково окислюється і, як було зазначено вище, його магнітні властивості погіршуються.
У зв'язку з викладеним третій варіант виготовлення магнітів не знаходить широкого застосування. Початкове ж сировина, яка використовується в цьому випадку, доцільно застосовувати після відповідного очищення і подрібнення як лігатури, вводячи її до складу шихти при виробництві магнітів по другому варіанту.
Для отримання високо щільних магнітів із сплавів альніко можна застосовувати також метод динамічного гарячого пресування (ДГП). Так, наприклад, при виробництві, магнітів із сплавів ЮНДК 24 вихідну шихту пресують при кімнатній температурі у брикети, які потім нагрівають до температури 1200 ° С і ущільнюють з високою швидкістю у відповідності із застосовуваним методом.
Застосування методів порошкової металургії у виробництві постійних магнітів з залізонікельалюмініевих сплавів дозволяє вдосконалювати процес з'єднання магніту з полюсним наконечником за рахунок їх спільного пресування і спікання. Для цього при пресуванні порожнину матриці поділяють спеціальною вставкою на окремі сектори, заповнюють їх відповідними порошками, витягають вставку і після цього здійснюють процес пресування. Під час подальшого спікання відбувається дифузійне взаємодію матеріалу магніту і залізного наконечника з утворенням якісного контакту.
Похожие статьи
-
Вибір та обгрунтування технологічного процесу Згідно із завданням до проектування та потребами багатьох галузей техніки було розглянуто і порівняно...
-
Вступ - Аналіз сучасного стану виробництва постійних магнітів
Порошкова металургія - область техніки, що охоплює сукупність методів виготовлення порошків металів і металоподiбних з'єднань, напівфабрикатів та виробів...
-
Загальна кількість відпадків із сировини розраховується за формолою: В = % (4) Де, ПВС -- загальні питомі витрати сировини В = % Таблиця 3...
-
Схема виробництва рослинних олій За технологічною ознакою технологічні процеси діляться на шість груп: Підготовка до зберігання і зберігання олійного...
-
Апаратурно-технологічна схема виробництва ковбаси сирокопченої може бути надана у вигляді поточно-механізованої лінії виробництва, що зображена на...
-
Загальні відомості про термічну обробку, що використовується У проекті Під термічною обробкою розуміють комплекс операцій нагрівання й охолодження...
-
Термічна ділянка, що знаходиться у виробничому приміщенні ковальського цеху ДП НВК "Електровозобудування" має площу робочої зони 378,25 м2 ,висота - 8 м....
-
Підвіски ГВП виготовляють методом гарячого штампування з урахуванням припусків для механічної обробки із конструкційної вуглецевої якісної сталі 45,...
-
Страви в ресторанах азербайджанської кухні виготовляють відповідно до нормативної документації, що діє в галузі (Збірник Рецептур Національних кухень). У...
-
Виробництво сирокопченої ковбаси зернистої складається з таких етапів: 1) Підготовка сировини (розморожування (при використанні замороженого м'яса ),...
-
Технологічна схема консервування зеленого горошку Опис технологічної схеми Для консервування використовують недозрілі зерна овочевого гороху лущильних...
-
Вуглець дуже впливає на властивості сталі навіть при незначній зміні його вмісту. Таким чином, вуглець являється основним елементом, за допомогою якого...
-
Стислий опис технологічного процесу. Після випуску сталі і її розливання в изложниці (маса зливків буває 8,5-12,5 тонн) останні попадають на ділянку...
-
Сировина ковбасного виробництва та її якість - Технологія виробництва ковбас
Для виготовлення ковбас використовують сировину основну, для масових виробів, різні замінники, матеріали для соління, ковбасні оболонки, допоміжні...
-
Висновок - Обгрунтування та аналіз технології виробництва сирокопченої ковбаси зернистої
Сирокопчені ковбаси відносять до класу делікатесної продукції, вирізняються від інших щільною консистенцією, гострим запахом, приємним солонуватим...
-
Вступ - Обгрунтування та аналіз технології виробництва сирокопченої ковбаси зернистої
М'ясо-молочна промисловість є складовою частиною харчової промисловості України. Забезпечення населення якісними продуктами харчування є одним з головних...
-
Ковбаса була і залишається надзвичайно популярною, та є одним з постійних продуктів в раціоні сучасної людини. Пріоритетними спрямуваннями у виробництві...
-
Якість продукту -- це сукупність властивостей продукції, яку обумовлюють її придатність, задовольнити певні потреби відповідно до призначення. Від якості...
-
Аналітичний огляд - Розробка технології виробництва туалетного мила
Омилення -- це реакція взаємодії ацилгліцеринів з гідроксидами лужних металів, кінцевими продуктами якої є гліцерин і мило: Вітчизняна технологія...
-
Прилади КВП та автоматика Автоматизація виробничого процесу -- це проведення технологічного процесу таким чином, при якому технологічна операція...
-
У реакторах періодичної дії процес, як правило проходить при перемінних температурах у часі. Відповідно до графіка зміни температури весь тепловий процес...
-
Рецептура продукту - Обгрунтування та аналіз технології виробництва сирокопченої ковбаси зернистої
Рецептура ковбаси сирокопченої зображена в таблиці 1.3 Таблиця 1.3 Рецептура ковбаси сирокопченої зернистої Сировина Витрати сировини на 100 кг несолоної...
-
Основними критеріями при виборі обладнання є: вид термічної обробки, хімічний склад та розміри деталей. Для проведення гартування та високого відпуску...
-
Продуктові розрахунки виконують для визначення обсягу виробництва, розрахунку і підбору технологічного обладнання, розрахунку площ камер зберігання...
-
Металургійні та технологічні особливості зварювання алюмінію та його сплавів Для алюмінію та його сплавів застосовують практично всі промислові способи...
-
ВСТУП - Технологія виробництва солоду
Солод - це заздалегідь замочене, пророщене в штучних умовах й при цьому збагачене активними ферментами, зерно різних видів зернових культур. Під...
-
Матеріали з спечених алюмінієвих порошків (САП) складаються з найдрібніших частинок алюмінію і його оксиду А1 2 О 3. Порошок для спікання отримують з...
-
Асортимент продукції - Обгрунтування та аналіз технології виробництва сирокопченої ковбаси зернистої
Сирокопчені ковбаси відносять до класу делікатесної продукції, вирізняються від інших щільною консистенцією, гострим запахом, приємним солонуватим...
-
Карта технологічного процесу на ремонт (додаток 1) вказує на почерговість операцій та докладний опис їх переходів з врахуванням обладнання, матеріалів, а...
-
Історія створення і поширення ковбасних виробів Перші письмові згадки про ковбасу можна зустріти в китайських, вавілонських і грецьких джерелах приблизно...
-
Характеристика технологічного об'єкта з точки зору автоматизації Задача управління процесом нагріву в колодязях полягає у виборі та забезпеченні режиму...
-
5.1. Роботи на виконавчих механізмах регулюючих органів і електроприводах затворної регулюючої арматури виконуються по заздалегідь узгодженій...
-
Принципи раціональної організації робочого процесу - Організація і планування виробництва
Раціонально організація виробничого процесу залежить від певного принципу. До них належать: спеціалізація пропорційність, паралельність, прямо точність,...
-
Режим роботи цеху визначається технологією виробництва продукту, напівфабрикатів, забезпеченістю трудовими ресурсами, а також ступенем шкідливості умов...
-
Загальні положення - Аналіз складу газу
Вимірювання складу газового середовища виконується в різних галузях промисловості, у наукових дослідженнях, при проведенні енергоаудиту, при проведенні...
-
Цивільний захист - Розробка технології виробництва туалетного мила
Цивільна оборона України -- це державна система органів управління, сил і засобів для організації і забезпечення захисту населення від наслідків...
-
ХАРАКТЕРИСТИКА ПРЯЖІ Таблиця 1 Характеристика пряжі Номінальна лінійна густина пряжі, текс Сорт Питоме розривне навантаження, г, с/текс Коефіцієнт...
-
Технологічна схема виробництва олії - Технологічна схема виробництва олії
Виробництво рослинної олії складається з багатьох операцій, під час яких в олійній сировині відбувається складні фізико-хімічні процеси. Спрощену...
-
Жирова основа туалетного мила - Розробка технології виробництва туалетного мила
1 Жири тваринні. Вони є найкращою сировиною для виробництва мил, особливо туалетних. До тваринних жирів відносять яловичий, баранячий, свинячий та...
-
Варіння мильної основи Виготовлення основи туалетного мила із нейтральних жирів періодичним непрямим методом. Цей процес відбувається в котлах 7, 8, 9...
Вибір схеми технологічного процесу - Аналіз сучасного стану виробництва постійних магнітів