ОСНОВНА ЧАСТИНА. УДОСКОНАЛЕННЯ ТЕХНОЛОГІЇ ТЕРМІЧОЇ ОБРОБКИ ПІДВІСОК ГВП, Загальні відомості про термічну обробку, що використовується - технологія термічної обробки підвісок гальмівно-важільної передачі електровозу, виготовлених із сталі 45
Загальні відомості про термічну обробку, що використовується
У проекті
Під термічною обробкою розуміють комплекс операцій нагрівання й охолодження сплаву, які здійснюються за певним режимом з метою зміни його будови та отримання заданих властивостей.
Основою термічної обробки є зміна структурно-фазового складу дислокаційної структури сплаву, яка може бути досягнута шляхом використання таких ключових факторів, як наявність в ньому алотропічних перетворень або залежного від температури обмеження взаємного розчинення компонентів.
Фундаментальною основою технології термічної обробки, що гарантує отримання очікуваних результатів, є її режим. Він включає в себе наступні елементи: температуру нагрівання, швидкість нагріву до заданої температури, час витримки при цій температурі та швидкість охолодження. Конкретні величини, що характеризують кожний з елементів режиму термообробки, залежить від хімічного складу оброблюваного сплаву, розміру деталі та цільового призначення виконуваного виду термічної обробки. Варіюючи ці величини, можна істотно змінювати фазову та дислокаційну структури сплаву і надавати йому задані властивості.
Від температури нагріву залежать характер перетворень, що відбуваються в сплаві, та сама можливість отримання після термообробки необхідної структури. Вона вибирається в залежності від хімічного складу сталі та цілі використаної термічної обробки.
Швидкість нагріву вибирається таким чином, щоб забезпечити мінімальні втрати часу на нагрів, і в той же час її величина повинна виключити виникнення в оброблюваної деталі небезпечних термічних напружень, які можуть призвести до викривлення і розтріскування деталі, що спостерігається при занадто швидкому нагріванні. Швидкість нагріву залежить від теплопровідності оброблюваного сплаву, яка, в свою чергу, визначається його хімічним складом.
Час витримки деталі по досягненню заданої температури повинен бути достатнім для її прогріву від поверхні до серцевини у найбільшому перетині, а також для повного завершення в сплаві тих, що мають дифузійний характер структурно - фазових перетворень, які повинні відбуватися в ньому при заданій температурі.
Швидкість охолодження при термічній обробці є дуже важливим елементом, від якого залежать особливості отриманої сплавом фазової та дислокаційної структури. Вона повинна бути достатньою для протікання в сплаві необхідних перетворень, але не надто великою, щоб уникнути небезпечних термічних та фазових напружень, які можуть викликати розтріскування або деформацію (викривлення) деталі.
По технології виготовлення підвісок для отримання заданих механічних властивостей були обрані такі види термічної обробки, як гартування та високий відпуск.
Подвійна термічна обробка сталі, яка складається із гартування та наступного високотемпературного відпуску (при 500 - 670 0С), називається покращенням.
Покращенню підлягають середньовуглецеві (0,3 - 0,5 %С) конструкційні сталі, до яких пред'являються високі вимоги по межі витривалості та ударній в'язкості. Покращення значно підвищує конструктивну міцність сталі, зменшуючи чутливість до концентраторів напруження, збільшує роботу розвитку тріщини та знижує температуру порогу холодноламкості. Однак зносостійкість покращеної сталі внаслідок зниження твердості не висока.
Гартування - це ТО, яка полягає у нагріві сталі до температури, що перевищує температуру фазових перетворень, витримці при цій температурі та подальшому охолодженні зі швидкістю, яка перевищує критичну мінімальну швидкість охолодження. Основною метою гартування є отримання високої твердості, зміцнення. В основі гартування лежить аустенітно - мартенситне перетворення.
Оптимальний інтервал гартівних температур вуглецевої сталі представлений на рисунку 2.1 [8].
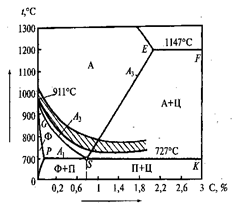
Рисунок 2.1 - Інтервал оптимальних температур для гартування вуглецевих сталей
Для досягнення максимальної твердості при гартуванні прагнуть отримати мартенситну структуру. Мінімальна швидкість охолодження, яка необхідна для переохолодження аустеніту до мартенситного перетворення, називається критичною швидкістю гартування. Швидкість охолодження визначається видом охолоджуючого середовища.
Вибір конкретного гартівного середовища визначається видом виробу. Наприклад, для підвісок із сталі 45 використовується вода з температурою 20 - 30 0С, а для сталі 40Х - вода - масло 20 - 50 0С.
Важливими характеристиками сталі, необхідними для призначення технологічних режимів гартування, являються загартовуваність та прогартованість. Загартовуваність характеризує здатність сталі до підвищення твердості при гартуванні і залежить головним чином від вмісту вуглецю в сталі. Загартовуваність оцінюють по твердості поверхневого шару стального зразка після гартування.
Прогартованість характеризує здатність сталі загартовуватись на необхідну глибину. Прогартованість оцінюється по відстані від поверхні виробу до шару, в якому міститься не менше 50% мартенситу. Залежить прогартованість від критичної швидкості охолодження: чим менша критична швидкість гартування, тим вище прогартованість. На прогартованість також впливає хімічний склад сталі, характер гартівного середовища, розмір та форма виробу та інші фактори.
Прогартованість деталей із середньо вуглецевої сталі при гартуванні в маслі нижче, ніж при гартуванні в воді. Прогартованість різко зменшується із збільшенням розмірів заготівки.
Стан загартованих деталей відрізняється дуже сильною не рівноважною структурою. Це обумовлено підвищеною концентрацією вуглецю у твердому розчині, високою густиною дефектів кристалічної будови, а також внутрішнім напруженням. Із-за цього загартована сталь хоч і володіє високою міцністю та твердістю, одночасно з цим має практично нульовий запас в'язкості. Ударні навантаження можуть викликати швидке руйнування деталі. Тому завжди гартування деталі підлягає додатковій термообробці - відпуску.
Відпуск - це заключна операція ТО сталі, яка полягає в нагріві нижче температури перлітного перетворення (727 0С), витримці та подальшому охолодженні. При відпуску формується кінцева структура сталі. Метою відпуску являється отримання заданого комплексу механічних властивостей сталі, а також повне або часткове усунення гартівних напружень.
Високий відпуск проводять при 440 - 650 0С для досягнення оптимального поєднання прочностних, пластичних та в'язких властивостей. Структура сталі представляє собою однорідний сорбіт відпуску із зернистою будовою цементиту. Високотемпературний відпуск застосовується для конструктивних сталей, деталі з яких підлягають дії високих напруг та ударних навантажень.
Відпуск легованих сталей проводять при більш високих температурах, ніж вуглецевих, щоб прискорити дифузію легуючих елементів. Хром являється одним із тих легуючих компонентів, які затрудняють процес розпаду мартенситу при нагріві. При однаковій температурі відпуску міцність та пластичність легованих сталей вища, ніж у вуглецевих.
Так як у проекті було запропоновано замінити сталь 45 на 40Х для виготовлення підвісок, то, слідуючи з цього, ми змінюємо і сам технологічний процес термічної обробки.
Після гарячого штампування вже готові поковки завантажуємо в піч Ц-105А у спеціальному пристосуванні, деталі розміщуємо у вертикальному положенні для рівномірного прогріву. Далі нагріваємо підвіски до температури 850 0С та витримуємо при цій температурі 2 години. Для забезпечення кращої прогартованості та уникнення внутрішніх напружень охолодження виробів проводять почергово у двох середовищах: спочатку деталі занурюємо в воду, засікаємо певний час, визначений експериментально, доводимо метал приблизно до температури 400 0С (трохи вище Мн), потім швидко переносимо їх в масло, де і відбувається кінцеве охолодження до температури приблизно 40-50 0С.
Нагрів поковок для відпуску проводимо у печі ПН-34М до температури 570 0С, витримуємо 2,5 години, а потім охолоджуємо у воді до кімнатної температури. Після ТО деталі підлягають механічній обробці. Режим термічної обробки підвісок із сталі 40Х наведено на рисунку 2.2.
Після такої термічної обробки сталь 40Х повинна мати кращі механічні властивості, ніж сталь 45 (див. табл..1.4 та рис.1.3).

Рисунок 2.2 - Графік режиму термічної обробки підвісок із сталі 40Х
Перевагами гартування підвісок у двох середовищах є: забезпечення оптимальної швидкості охолодження, яка запобігає розпад переохолодженого аустеніту в області температур мінімальної стійкості А, зниження рівня гартівних напружень, уникнення дефектів типу викривлення.
Недоліком цього ж процесу являється необхідність мати високо-кваліфікаційних термістів та висока вартість мінерального масла.
Похожие статьи
-
Підвіски ГВП виготовляють методом гарячого штампування з урахуванням припусків для механічної обробки із конструкційної вуглецевої якісної сталі 45,...
-
Після охолодження деталей до температури цеху проводиться контроль зразка на: твердість - твердомір ТК-1 - на попередньо підготовленій (зачищеній)...
-
При визначенні режимів термічної обробки слід враховувати технологічні та механічні властивості сталі, технічні вимоги до виробів в умовах їх...
-
Опис виробу У сучасних галузях виробництва практично повсюдно використовуються поковки - чорнові деталі, за своїми розмірами і формі дуже близькі до...
-
Завод ДП НВК "Електровозобудування" - державне підприємство, яке забезпечує своєю продукцією Україну та країни СНД. Завод був практично монополістом на...
-
Для проведення термічної обробки підвісок було застосовано таке обладнання: 1. Для гартування - шахтна електропіч (таблиця 1.5). Таблиця 1.5 -...
-
Стислий опис технологічного процесу. Після випуску сталі і її розливання в изложниці (маса зливків буває 8,5-12,5 тонн) останні попадають на ділянку...
-
Характеристика технологічного об'єкта з точки зору автоматизації Задача управління процесом нагріву в колодязях полягає у виборі та забезпеченні режиму...
-
Спечені алюмінієві сплави (САС) отримують брикетуванням, спіканням і деформацією порошків алюмінію та легуючих елементів або порошків стандартних...
-
Спеціальні сорти солоду (карамельний та палений) - Термічна обробка пивоварного солоду
Карамельний солод Використовують для надання пиву характерного солодового аромату і більш темного забарвлення, а також для збільшення стійкості пива, так...
-
Токарна чорнова операція. Виконується на станках токарної групи в два установи. В першому установі знімають метал з поверхонь, що підлягають механічній...
-
Производство стали - Разработка технологического процесса изготовления детали "зубчатое колесо"
Сущность процесса Основными материалами для производства стали являются передельный чугун и стальной лом (скрап). Содержание углерода и примесей в стали...
-
Розглянемо структурні складові алюмінієвих сплавів, схема діаграми стану яких наведено на рис.1. Ті з них, які мають сумарну кількість легуючих елементів...
-
На основе диаграммы состояний "железо - цементит" и построенного графика термической обработки опишите превращения в структуре стали при нагреве,...
-
Низколегированные стали, предназначены для изготовления деталей, работающих в условиях высоких температур (100-600 С) и при давлении газа или пара. Эти...
-
Отпуск стали - Характеристика и структурные методы исследования металлов
Отпуск закаленных углеродистых сталей Отпуском называют термическую операцию, заключающуюся в нагреве закаленной стали до температур, не превышающих...
-
Технологічна схема виробництва - Технологія виробництва ковбас
Технологічна схема процесу (??дод. А). М'ясо в тушах, напівтушах і четвертинах подається на стіл для ручної обвалки (1), де відбувається його...
-
Введение Металлы относятся к числу наиболее распространенных материалов, которые человек использует для обеспечения своих жизненных потребностей. В наши...
-
Схема виробництва рослинних олій За технологічною ознакою технологічні процеси діляться на шість груп: Підготовка до зберігання і зберігання олійного...
-
Конструкционные материалы - Электротехника. Электротехническое материаловедение
Задача 1 . Вычертите диаграмму состояния железо-карбид железа, укажите структурные составляющие во всех областях диаграммы, опишите превращения при...
-
МЕХАНІЧНІ ВЛАСТИВОСТІ - Матеріалознавче підгрунтя застосування спечених алюмінієвих сплавів
Для підвищення механічних характеристик САП і надання цьому матеріалу необхідної форми його додатково піддають динамічному пресуванню, штампуванню,...
-
Технологічна частина, Загальні відомості - Технологія приготування пельменів
Загальні відомості Вироби з борошна мають високу калорійність, приємний зовнішній вигляд, добрі смакові якості, тому користуються високим попитом у...
-
Наименование детали - фланец. Назначение детали - деталь служит для образования разъемных соединений труб. Обозначение материала детали - сталь 45 ГОСТ...
-
Вибір режиму ТО Розрахунок складу бетону. Приймаємо для виробництва виробів портландцемент ІІ-го типу М500. Для даної установки призначаємо ОК=10 см тому...
-
Основна частина - Заправні супи
Загальні відомості по темі: "Заправні супи" Заправні супи поділяють на борщі, розсольники, юшки. Розсольник - обов'язковою складовою частиною є огірки,...
-
Мета термічної обробки солоду - Термічна обробка пивоварного солоду
Свіжопророщений солод для виробництва пива використовувати неможна, так як він має сирий смак та запах, в ньому відсутні ароматичні, забарвлюючі і...
-
Опис механічного обладнання відділення в технологічній послідовності При охолодженні коксового газу виникає зменшення його об'єму, конденсація парів води...
-
Технологічна частина - Проект лінії для виробництва консервів "Асорті №6"
Доставка. Овочі на підприємство доставляють у ящиках по ГОСТ 13353-84. Помідори транспортують у ящиках вагою не більше 15кг, огірки і перець - у ящиках...
-
Плавка в кислой электропечи. - Производство стали
Кислые электропечи футеруют огнеупорными материалами на основе кремнезема. Эти печи имеют более глубокие ванны и в связи с этим меньший диаметр кожуха,...
-
Шляхи підвищення продуктивності обробки - Токарна група верстатів
Трудомісткість верстатної обробки може бути знижена шляхом скорочення машинного або допоміжного часу операції, а також загального скорочення штучного...
-
В результаті проведення процесу проходять складні біохімічні і хімічні зміни. В залежності від перетворень, які відбуваються у зерні у процесі...
-
КИСЛОРОДНО-ФЛЮСОВАЯ РЕЗКА - Газовая резка нержавеющей стали
При обычной кислородной резке высоколегированная хромистых и хромоникелевых нержавеющих сталей на поверхности реза образуется пленка тугоплавких окислов...
-
РЕЗКА НЕРЖАВЕЮЩИХ СТАЛЕЙ, ГАЗО-ДУГОВАЯ РЕЗКА - Газовая резка нержавеющей стали
Применяют следующие виды резки нержавеющей стали: дуговую электрическую: газо-дуговую, кислородно-флюсовую и газоэлектрическую. В данном реферате...
-
ОБЛАСТИ ПРИМЕНЕНИЯ НЕРЖАВЕЮЩИХ СТАЛЕЙ - Газовая резка нержавеющей стали
Нержавеющими называются стали, обладающие высокими механическими свойствами, окалиностойкостью, жаропрочностью, стойкостью против атмосферной, жидкостной...
-
Режим роботи ДБК ш. ім. Орджонікідзе Режим роботи - це встановлений порядок та тривалість виробничої діяльності підприємства та його підрозділів у часі...
-
Так як в завданні немає особливих вимог стосовно габаритів передачі, вибираємо матеріали з середніми механічними характеристиками: для шестерні сталь 45,...
-
Виробництво сирокопченої ковбаси зернистої складається з таких етапів: 1) Підготовка сировини (розморожування (при використанні замороженого м'яса ),...
-
Производство стали - Полная характеристика черной металлургии
Сталями называют сплавы железа с углеродом, содержание которого не превышает 2,14 %. Сталь - важнейший конструкционный материал для машиностроения,...
-
Получение низкоуглеродистой коррозионностойкой стали (процессы AOD и VOD) . - Производство стали
Широкое распространение получают методы производства низкоуглеродистой коррозионностойкой стали вне электропечи. Метод AOD. В электропечи выплавляют...
-
Технология непрерывной разливки стали состоит в том, что жидкий металл непрерывно заливается в верхнюю часть водоохлаждаемой формы -- кристаллизатор,...
ОСНОВНА ЧАСТИНА. УДОСКОНАЛЕННЯ ТЕХНОЛОГІЇ ТЕРМІЧОЇ ОБРОБКИ ПІДВІСОК ГВП, Загальні відомості про термічну обробку, що використовується - технологія термічної обробки підвісок гальмівно-важільної передачі електровозу, виготовлених із сталі 45