Основний зміст роботи - Розробка молотків кормодробарок з локальним зносостійким покриттям
У вступі приведена загальна характеристика роботи, висвітлена актуальність теми досліджень, сформульована мета, наведена інформація про апробації та публікації основних положень в наукових виданнях.
У першому розділі "Аналітичний огляд існуючих конструкцій, умов експлуатації та способів підвищення довговічності робочих органів ударної дії" розглянуто основні види молоткових дробарок, проаналізовані умови експлуатації їх робочих органів, описані причини формування відмов і способи підвищення довговічності.
Питання підвищення ефективності та надійності дробарок знайшли своє відображення в працях провідних науковців Фабриканта М. Б., Гернета М. М., Мельникова С. В., Бойка А. І., Ревенка І. І., Сідашенка А. І., Балакіра Е., Прокопенка І., Вялих В. А., Гаврилова Н., Звєрєва С., Золотарьова С. В., Тимановського А. В. та інших.
Різні модифікації кормодробарок, що були розроблені в Україні так і за її межами, можна згрупувати в залежності від особливостей конструкторського рішення, принципу роботи та способу завантаження продукту подрібнення до дробарки.
Процес подрібнення відбувається за рахунок багатократного удару молотків по зернам злакових культур. Його виконання в деякій мірі залежить від конструктивних особливостей кормодробарок, але спільним для них є наявність в якості основного робочого органу - подрібнювального ротора з молотками, які відрізняються різною формою і розмірами.
Практикою експлуатації встановлена недостатня довговічність молотків, які інтенсивно зношуються при взаємодії з зерновою масою.
Проблемі підвищення довговічності основних робочих органів сільськогосподарських машин присвячені дослідження Рабиновича А. Ш., Черновола М. І., Сичова І. П., Козаченка О. В., Петрова Ю. М., та інших. Незважаючи на отримані позитивні результати, ступінь підвищення довговічності, як правило, не задовольняє практику експлуатації машин. Нові перспективи відкриває комплексний підхід, який грунтується на раціональному взаємному доповненні конструктивних і технологічних методів направлених на керування формуванням робочих поверхонь при зношуванні.
За матеріалами першого розділу сформульовані задачі подальших досліджень.
В другому розділі "Теоретичні дослідження взаємодії і зношування елементів ударної дії зерновою масою", розглянуто ударно-імпульсне навантаження і зношування робочих поверхонь молотків частинами зерна, що подрібнюється.
Подрібнювальна камера представляє собою об'єм циліндричної форми, з робочими органами ударної дії (молотками), що знаходяться в обертовому русі. Молотки шарнірно закріплені на роторі та обертаються з кутовою швидкістю. Зустрічаючи зовнішній опір з боку зернової маси, вони відхиляються на деякий кут.
Опір руху молотків обумовлюється їх зіткненням з частинами зерна. При таких зіткненнях відбуваються удари між окремими зернинами і робочими поверхнями молотків.
Молоток зіштовхується із зерниною з деякою кінцевою швидкістю. Кут атаки (кут між вектором швидкості удару та дотичною до робочої поверхні в точці контакту зернини з молотком) складає.
Припустимо, що деформоване зерно або окремі його частинки, які виникли в результаті подрібнення, відбиваються від робочої поверхні під кутом в та віддаляються від поверхні зі швидкістю V0..
Представляючи зернину як точку, оскільки її розміри досить малі в порівнянні з робочою поверхнею, а вплив обертального імпульсу після удару можна виключити внаслідок гальмівного впливу потоку зернової маси, напрямок вектору імпульсу сили S при зіткненні можна визначити на основі наступного векторного співвідношення:

,(1)
Де m - маса зернини
Ударний імпульс представляє собою силову характеристику контактної взаємодії зернини з робочою поверхнею молотка. Саме він є енергетичним джерелом процесів, що протікають при контакті зерна з ударним елементом (молотком). Зусилля та енергія, що виникають при ударі з однієї сторони витрачаються на деформацію та руйнування частинок, а з іншої - на спрацювання робочої поверхні молотка.
З позицій зношування молотків представляє інтерес нормальна складова ударного імпульсу. Виходячи з геометричних побудов та вирішуючи трикутник Д АБМ (рис.1) після математичних перетворень маємо:
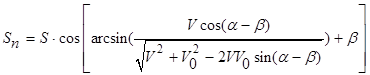
.(2)
При всій невизначеності розподілення складових ударного імпульсу, що впливають на деформацію, руйнування зерна та спрацювання поверхні молотків, можна стверджувати, що величина спрацювання залежить від кількості циклів ударного навантаження робочої поверхні. Зі збільшенням кількості ударних циклів навантаження, величина спрацювання також буде збільшуватись.
Молотки кормодробарок, що серійно випускаються, виготовлені із однорідного матеріалу без зміцнення. По своїй довжині вони спрацьовуються нерівномірно. Периферійна частина молотка, яка максимально віддалена від центру обертання ротора, зазнає зношування в більшій мірі.

Аналіз геометричних параметрів, що набувають молотки в процесі їх спрацювання показують, що з часом експлуатації, після закінчення початкового періоду пов'язаного з припрацюванням, форма молотків може бути описана і формалізована відомими геометричними образами. Профіль робочої поверхні, що спрацьовується, в загальному вигляді описується поліномом другого порядку. Або предметно до вибраної системи координат після відповідних математичних перетворень поліном переходить в рівняння параболи, де р - параметр параболи.
В полярній системі координат, що є більш зручною для подальшого аналізу, рівняння профілю спрацювання, приймає вигляд:

,(3)
Де о - кут повороту полярного радіуса параболи; - полярний радіус параболи.
В перерізі, після проходження припрацювання, початкова прямокутна форма молотка згладжується. Виступаючі кути, внаслідок краєвих ефектів, мають більш інтенсивне спрацювання. В результаті, переріз молотка набуває форму кола, радіус якого дорівнює r=у/2. Для аналізу навантажень та дослідження процесу спрацювання, виділимо на поверхні молотка елементарну площадку dS (рис.3). В загальному випадку її суміжні бокові сторони будуть утворені дугами. Оскільки полярний радіус, який описує профіль молотка при спрацюванні, є величина змінна і визначається рівнянням (3), то можна записати:
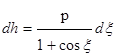
.(4)
Тоді площа елементарної площадки дорівнює:
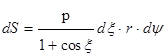
.(5)
На елементарну площадку діє потік зерна, що обумовлює спрацювання матеріалу молотка. Кількість зернин, що попадають на площадку за деякий час Дt, залежить від щільності зернової маси q3, Відносної швидкості V та напрямку орієнтації площадки.
Виходячи з вищесказаного, кількість зернин дорівнює:

.(6)
Елементарним силовим навантаженням, є імпульс сили, що дорівнює зміні кількості руху зернини. Враховуючи, що швидкість удару зернини рівна V, а також вважаючи, що після удару, в потоці, зернини отримують швидкість молотка, для імпульсу можемо записати:
,(7)
Де F - ударна сила; ф - час удару.
За деякий проміжок часу Дt кількість ударів по елементарній площині складає N. Тоді силове навантаження на молоток буде рівним добутку величини імпульсу на їх кількість. Використовуючи рівняння спрацювання, процес втрати маси, а відповідно і геометричних параметрів молотка, можна записати в наступному вигляді:

,(8)
Де qм - щільність матеріалу молотка.
Після скорочень та спрощень рівняння записується у вигляді:

.(9)
Як видно з отриманого рівняння воно не включає параметри елементарної площадки, а має три невідомих величини с, о та t, дві з яких взаємопов'язані рівнянням профілю молотка. Одна з величин, найбільш суттєво впливає на інтенсивність спрацювання - це швидкість V співудару. Підставляючи значення швидкості для роторного молоткового робочого органу отримаємо:

. (10)


Аналітичне вирішення отриманого диференціального рівняння відносно невідомого с не представляється можливим. Рівняння може бути вирішене числовими методами з використанням ЕОМ. Однак для загального аналізу представляє інтерес випадок, коли поверхня молотка максимально навантажена, тобто знаходиться на початковій стадії спрацювання після проходження періоду припрацювання. При цьому робоча поверхня ще не встигла прийняти ту форму, коли кути її атаки частинками зерна будуть найменшими. Тоді ч> 0; , а кут атаки дорівнює.

Вважаючи, що в шарі циркулюючої зернової маси і проінтегрувавши рівняння (10) отримаємо наступний вираз :
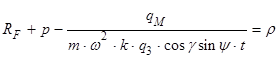
.(11)
Маючи деякі значення напрацювання молотка за проміжок часу t при відомих параметрах, що входять до складу рівняння спрацювання, є можливість розрахувати величину полярного радіуса. Тоді за відомою формулою параболи визначається полярний кут, що відповідає даному значенню полярного радіуса. В результаті отримаємо всі величини (с, о, р, F(хF, уF)) необхідні для побудови профілю молотка, що відповідає напрацюванню за встановлений час t.
Серія таких побудов дає повну інформацію про динаміку зміни геометрії монометалевого однорідного молотка в процесі робот. Однак для реалізації цього необхідні додаткові експериментальні данні про параметри зношування матеріалів потоком зернових частинок.
Виходячи з аналізу спрацювання монометалевих однорідних молотків та огляду існуючих конструкторсько - технологічних методів підвищення довговічності деталей, для дослідження спрацювання зміцнених молотків кормодробарок.
По аналогії зі зношенням монометалевих серійних молотків, відбувається зношування незміцненої частини зміцненого молотка.
Враховуючи відносно невелику ширину зони зміцнення hY= 2rY У напрямку осі ОХ та товщину шарів зміцнення в перерізі, з достатньою для практичних цілей точністю можна вважати, що зміна форми зміцненої зони як в плані, так в перерізі можливо в першому наближенні описати колами відповідних радіусів rY Та rС.
З метою не ускладнення задачі, прийнято, що зміцнені шари нанесені рівномірно та мають однакову товщину У при загальній товщині молотка .
Будемо вважати, що за деякий проміжок часу t, центр кола, що описує профіль спрацювання зміцненої зони, в процесі роботи зміститься на відстань у. Тоді спрацювання зміцненої зони можна розглянути, як переміщення кола вздовж осі ОУ.
Спрацювання зміцненого молотка, що складається з незміцнених та зміцнених частин, може бути представлено відповідною системою рівнянь:
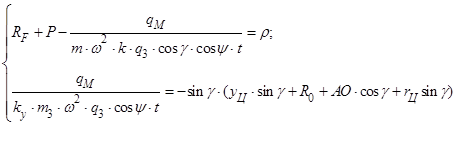
.(12)
Сумісне рішення рівнянь представленої системи описує процес спрацювання зміцнених молотків у вигляді формування переміщення профілю у глибину деталі по мірі збільшення їх наробітку. Як видно із представлених рівнянь, суттєвий вплив на формування геометрії робочої частини зміцнених молотків надає співвідношення зносостійкостей матеріалів основи та зміцнення, яке враховується відповідними коефіцієнтами k та kY. При сталих інших параметрах, які входять до системи (12) від співвідношення коефіцієнтів залежить ступінь зношування матеріалів основи та зміцнення, тобто рельєфність профілю молотка, а від їх абсолютних значень - наробіток на відмову робочої грані.
У третьому розділі "Програма і методика експериментальних досліджень" приведена програма і методика експериментальних робіт. Дослідження проводяться з молотками кормодробарок в реальних умовах експлуатації без зайвого впливу на технологічний процес подрібнення. Таким чином, даний вид активного експерименту не передбачає втручання безпосередньо в самий технологічний процес подрібнення зерна. При цьому досліджуються формозміни профілю серійних та зміцнених молотків, крупність помелу зерна та характеристики роботи електродвигуна приводу кормодробарки.
Для проведення досліджень підготовлюються партії зміцнених молотків в кількості не менше як по 80 шт. кожного виду матеріалу і технології нанесення покриття.
Для оцінки зміни геометрії молотків при їх спрацюванні, враховуючи недоліки попередніх методів (вагового, графоаналітичних, об'ємних та інших), розроблений оригінальний метод сканування поверхні і обробки результатів на ЕОМ.
Автоматизована система складається з апаратних засобів і відповідного програмного забезпечення.
До складу апаратного засобу входять: пристрій формування цифрових відезображень 1 деталей, що досліджуються, пристрій (інтерфейс) введення отриманих відео зображень в комп'ютер 2, а також власне сам комп'ютер 3, який виконує обробку накопичених відеозображень. Програмне забезпечення 4 виконує збір, обробку і аналіз експериментальної відеоінформації про стан робочих органів ударної дії для подрібнення зерна.
Відезображення молоткового робочого органу, яке отримується за допомогою цифрового фотоапарату обробляється вимірювально цифровим комплексом. В результаті вимірювань геометричних величин, з відеозображень фіксуються значення координат точок контуру деталі.
Знімаючи профілі через інтервал наробітку ДQ, визначається динаміка зношення молотків з поступовою зміною зазначених геометричних параметрів від наробітку. На підставі цього будуються залежності типу та інші.
Співставляючи отримані результати зношення і зміни геометрії молотків з якістю помелу зоотехнічними вимогами на приготування кормів, встановлюються граничні значення зносу і вибракувальні параметри молотків.
Якість помелу та енергетичні показники роботи дробарки оцінюються згідно загальноприйнятих методик у відповідності до ГОСТ 13496.8-72 та ГОСТ 7217-86
У четвертому розділі "Експериментальні дослідження динаміки зношування та ефективності підвищення роботоздатності молотків" представлені результати експериментальних досліджень.
Дослідження профілів по трьом характерним ділянкам здійснення ударів: прямого, косого і з ковзанням частинок зерна по робочій поверхні дає можливість кількісної оцінки зміни форм молотків. Залежності зміни кутів атаки від довжини робочої частини серійних молотків. Як видно з отриманих графів, зміни кутів атаки носять нелінійний характер. Зі збільшенням наробітку, підвищується периметр зношування робочої частини молотків. При граничному зношенні величини робочих ділянок складають: для косого удару - 3 мм (16%); для удару з ковзанням - 67 мм (84%).
Отримані результати аналізу динаміки зміни профілів серійних молотків при зношуванні дали можливість виявити вплив наробітку на зміну довжини характерних робочих ділянок молотків. Так, на основі вимірювань і обчислень побудовані відповідні залежності.
Як видно з графіків, залежності принципово відрізняться між собою. Ділянка прямого удару, що відповідає найбільш ефективній передачі кінетичної енергії, яка витрачається на подрібнення матеріалу зі збільшенням наробітку молотка і його зношуванням поступово скорочується. Після наробітку в Q=155 т., ця ділянка взагалі стає відсутньою, поступаючись двом іншим: з косим та ковзаючим ударами. Ділянка косого удару, після наробітку Q=100 т. практично не змінюється до кінця терміну експлуатації молотків. Це вказує на те що, ділянка ковзаючого удару зростає з наробітком в основному за рахунок першої ділянки - прямого удару і частково в наслідок невеликого збільшення робочого периметра молотка. Цим пояснюється тенденція до стабілізації величини ділянки ковзаючого удару при наробітках, що перевищують Q?180т.
Таким чином аналіз зміни форми серійних молотків при зношуванні пояснює причини поступової втрати роботоздатності (формування функціональної відмови) кормодробарки і необхідність проведення своєчасної заміни робочих органів.
На підставі проведених теоретичних досліджень з урахуванням технологічних можливостей локального нанесення зносостійкого покриття, розроблено експериментальний молоток.
Як і для серійних, аналіз профілів зношування зміцнених молотків проводиться по трьом ділянкам характерних ударів: прямого, косого і ковзаючого.
Складність формування робочих профілів зміцнених молотків обумовила і складний характер залежностей змін кутів атаки від довжини робочих ділянок.
Сімейство отриманих кривих вказує на принципово однаковий характер зміни кута атаки. Для всіх стадій зношування молотків з початку він швидко збільшується, досягає екстремуму - максимуму, потім зменшується до локального мінімуму і знову починає зростати асимптотично, наближуючись до значення прямого удару (б = 900). Зміни кривих, насамперед, пов'язані з перерозподілом ділянок особливостей реалізації нанесення ударів при руйнуванні частинок зерна.
Відповідно до аналізу зношення молотків в плані, згідно фронтальної проекції, розглянутої вище, у перерізі А-А формується також нерівний профіль. Але кривизна профілю в перерізі зміцненого молотка має зворотній характер порівняно з серійним. Це обумовлено різною інтенсивністю зношування на ділянках зміцнення по бокам молотка і матеріалом основи, що складає середину перерізу
Аналіз профілю з позицій виявлення ділянок прямого, косого і ковзаючого ударів показав, що в процесі зношування їх частки в загальній довжині робочої зони молотка змінюються. При чому, якщо величина ділянки ковзаючого удару практично залишається на одному і тому ж рівні (15 мм.), то ділянка косого удару постійно зростає за рахунок зменшення ділянки прямого удару.
Принциповою різницею в роботі зміцнених молотків є те, що вони в процесі експлуатації і зношування не втрачають своєї роботоздатності і ефективно виконують свою функцію по подрібненню зернової маси. При цьому основні показники роботоздатності кормодробарки не виходять за агротехнічні вимоги. Таким чином, фактично для зміцнених молотків на всьому терміні експлуатації не характерно формування функціональних відмов дробарки в наслідок зношення робочих граней, тобто локальне зміцнення привело до можливості формування таких профілів, що запобігають втраті основних параметрів роботи дробарки.
Особливості зношування локально зміцнених молотків змінюють уявлення, порівняно з серійними, про граничну величину їх зношування. Використання в якості граничного зношування, досягнення профілем головної осі симетрії молотка, як це прийнято для серійних, не можна вважати доцільним. Для серійних молотків, на останніх етапах роботи, ковзаючий удар домінує над іншими і знижує експлуатаційні показники дробарки. Ймовірно, що для зміцнених молотків доцільно прийняти за граничне зношування, досягнення профілями такого стану, коли зносостійкий матеріал практично вичерпаний і вже не забезпечує керуємого зношування і формування ефективно працюючого профілю.
Виходячи з результатів експериментальних досліджень проведених в реальних умовах рядової експлуатації встановлено, що граничне зношування локально зміцнених молотків досягається при наробітку в 400т. зернової маси. По відношенню до серійних молотків, коли граничне зношення обумовлене наробітком в 250 т., підвищення довговічності при локальному зміцненні складає 1,6 рази.
Зношення серійних молотків приводить до погіршення якості помелу: модуль помелу зростає з М=1,17 мм. до М=1,43 мм. (на 22%). При цьому питомі витрати енергії дещо зменшуються, а саме з 5,61 кВт/т./год. до 5,54 кВт/т./год. Локальне зміцнення молотків при зношуванні призводить до формування виступаючих ділянок матеріалу наплавки, це підвищує ефективність їх роботи. Так, модуль помелу знижується до М=1,06мм., а питомі витрати енергії зменшуються на 7,5% порівняно з новими серійними і новими зміцненими молотками.
В п'ятому розділі "Техніко - економічна ефективність впровадження результатів досліджень" вказано, що локальне зміцнення по кутам робочих граней молотків підвищує їх довговічності в 1,6 рази. Запропонований матеріал і технологія зміцнення доступні для реалізації як на заводах-виробниках, так і на комбікормових заводах тваринницьких комплексів.
При цьому знижуються питомі витрати на тону подрібненої зернової маси, що в порівнянні з серійними молотками становить 14 %. Річний економічний ефект від впровадження молотків, зміцнених точковою дуговою наплавкою дротом ППНП - 80ХС, складає 23998,4 грн., а від впровадження молотків, зміцнених електродом Т-590 - 23186,5 грн.
Навантаження зношування роботоздатність молоток
Похожие статьи
-
Загальна характеристика роботи - Розробка молотків кормодробарок з локальним зносостійким покриттям
Актуальність теми. Тваринництво займає провідне місце у сільському господарстві України, а його продукція є джерелом для харчової та переробної...
-
Основний зміст роботи - Оптимізація технологічного процесу лущення власнокруп'яних культур
Власнокруп'яний культура лущення технологічний У вступі подано загальну характеристику роботи, розкрито сутність і стан наукової проблеми та її значення,...
-
Огляд літератури У розділі наведено аналіз результатів наукових робіт вітчизняних та зарубіжних авторів з питань впливу основних елементів технології...
-
НАУКОВІ ОСНОВИ ФОРМУВАННЯ ВИСОКОПРОДУКТИВНИХ ПОСІВІВ ГОРОХУ (Огляд літератури) Проаналізовано сучасні положення щодо особливостей формування...
-
У вступі розкривається сутність і стан наукової проблеми, її значущість, підстави для розробки теми, обгрунтовується необхідність проведення досліджень....
-
Сучасний стан і завдання по підвищенню врожайності та поліпшення якості гібридного насіння кукурудзи (огляд літератури) Аналіз джерел літератури, в яких...
-
У Вступі обгрунтовано актуальність теми, вказано зв'язок з науковими програмами, сформульовано основні положення, які складають об'єкт, предмет, мету і...
-
Дощування транзитний трубопровід У першому розділі "Аналіз основних напрямків удосконалення та розвитку дощувальних машин в Україні" розглянуто сучасний...
-
Селекція соняшнику на підвищення вмісту олеїнової кислоти (огляд наукової літератури) На основі аналізу сучасного стану і результатів попередніх...
-
У вступі обгрунтовано актуальність обраного напрямку, визначено мету та завдання дослідження, показано наукову новизну та практичну цінність, наведено...
-
Огляд літератури. Складається з 5 підрозділів, у яких наведено дані літератури стосовно заморожування ембріонів, використання кріопротекторів для їх...
-
Сірі лісові грунти лісостепу України та прийоми відтворення їх родючості (огляд літературних джерел). В огляді літературних джерел подається грунтовний...
-
ВСТУП У розділі викладено актуальність теми; зв'язок роботи з науковими програмами, планами, темами; мету і завдання досліджень; наукову новизну та...
-
У Першому розділі дисертації "Теоретичні основи формування економічного механізму раціонального використання та охорони земель сільськогосподарського...
-
Гриб токсикоз продуцент Матеріали та методи досліджень Робота виконувалася в лабораторії мікотоксикології Інституту ветеринарної медицини УААН протягом...
-
Огляд літератури. У розділі надається аналіз літературних джерел щодо підвищення ефективності засобів регулювання шкодочинності бур'янів, системного...
-
Матеріали та методи досліджень. Дослідження проводили з рослинами озимої пшениці сортів Київська 8, Подолянка, Колумбія, Білоцерківська напівкарликова. У...
-
У Вступі обгрунтовано актуальність дослідження, визначено мету й основні завдання, предмет, об'єкт дослідження, висвітлено наукову новизну одержаних...
-
Еколого-біологічні фактори формування високопродуктивних ценозів багаторічних трав (Огляд літератури): У розділі показано роль багаторічних трав та їх...
-
Найважливішою проблемою агропромислового комплексу України на сучасному етапі є збільшення кількості рослинної сировини для одержання в різноманітному...
-
Результати аналізу літературних джерел свідчать, що коренева губка завдає значної шкоди насадженням сосни. Вона викликає строкату гниль і є особливо...
-
Огляд літератури На основі аналізу даних літератури з екологічних питань хімічного захисту рослин від шкідливих організмів показано, що для раціонального...
-
Огляд літератури У розділі подано аналіз наукових джерел вітчизняних і зарубіжних авторів з вивчення анаеробних мікроорганізмів, які здійснюють...
-
У вступі розкрито суть наукової проблеми, обгрунтовано актуальність теми дисертаційної роботи, сформульовано мету і завдання досліджень, показано зв'язок...
-
Для збереження та прискореного розмноження цінних рослинних генотипів доцільно застосовувати мікроклональне розмноження. Даний метод базується на...
-
Актуальність теми. В Україні середня врожайність гречки складає 6,9 ц/га, а валове виробництво її зерна складає близько 274,6 тис. тонн, що не...
-
Заморожування ембріон рогатий худоба Актуальність теми. Кріоконсервування ембріонів відкриває значні можливості для використання методу трансплантації...
-
Генетичний вегетація зерно Лівобережний Лісостеп України, що є одним із основних виробників продовольчого зерна озимої пшениці, характеризується...
-
Методика отримання гаплоїдних структур у культурі in vitro (холодова передобробка, склад компонентів живильного середовища, зокрема 2,4-Д) дає підстави...
-
ЗАГАЛЬНА ХАРАКТЕРИСТИКА РОБОТИ - Агробіологічна оцінка підщепи винограду сорту Таїровський 1
Актуальність роботи. Щеплена культура винограду, незважаючи на всі пов'язані з нею труднощі, є поки що єдиним способом створення довговічних і...
-
Алеломорф молдавський ген зерно Цитоплазматична чоловіча стерильність як приклад нехромосомної спадковості (огляд літератури) Наведено літературний огляд...
-
СУЧАСНІ АСПЕКТИ СИСТЕМИ ЗАХИСТУ ЗЛАКОВИХ КУЛЬТУР В АГРОЕКОСИСТЕМАХ Огляд наукової літератури . Світовий досвід інтенсифікації землеробства за рахунок...
-
НАУКОВІ ОСНОВИ ПІДВИЩЕННЯ ВРОЖАЙНОСТІ ТА ЯКОСТІ ОЗИМОЇ ПШЕНИЦІ ЗА РАХУНОК ЕЛЕМЕНТІВ ТЕХНОЛОГІЇ ВИРОЩУВАННЯ (ОГЛЯД ЛІТЕРАТУРИ) На підставі вивчення...
-
Актуальність теми. Підвищення якості молока, збільшення вмісту в ньому жиру і виходу молочного жиру є важливими складовими удосконалення молочної худоби....
-
Зростання виробництва зерна високої якості та більш раціональне його використання є однією з головних проблем сучасного сільського господарства України....
-
Для використання в рамках прикладних селекційних програм рекомендуються: 1. Технології селекційного процесу зі створення вихідного матеріалу цикорію...
-
Селекція рослина мікроклональний розмноження Рябовол Л. О. Розробка біотехнологічних методів і використання їх для створення вихідного селекційного...
-
Актуальність теми. Вирощування ярого ячменю передбачає використання його зерна в основному на кормові цілі та як сировини для харчової промисловості. В...
-
Основними питаннями в селекції рослин є пошук, добір та збереження джерела продуктивного вихідного матеріалу. Збереження генотипу в умовах in vitro є...
-
Актуальність теми. Під зерновими й зернобобовими в Україні зайнято 13.2 млн. га, або 46.5 % сільськогосподарських угідь. Врожай соломи становить більш 54...
Основний зміст роботи - Розробка молотків кормодробарок з локальним зносостійким покриттям