Монтаж оборудования - Ремонт токарного станка
Легкие и средние металлорежущие станки поступают на монтажную площадку в собранном виде или с несколькими узлами, снятыми из-за их габаритности, поэтому при монтаже легких и средних станков сборка или полностью отсутствует или составляет незначительную часть общего объема работ.
Монтаж металлорежущих станков начинается после окончания основных строительных работ, изготовления полов и установки мостовых кранов, так как длительное пребывание станка на фундаменте в неоконченном помещении приводит к коррозии обработанных поверхностей, а производство строительных работ при установленных на фундаментах станках может привести к повреждению отдельных их деталей и узлов.
Подъем станков и установка их на фундамент должны произ-водиться осторожно. Обычно заводы-изготовители в паспорте или инструкции по обслуживанию станка указывают места и способы увязки стропов.
Крупные металлорежущие станки поступают на монтажную площадку в виде отдельных деталей и узлов, и сборка их производится на месте установки в соответствии с монтажной схемой и указаниями завода-изготовителя. Подъем и транспортировку деталей и узлов к месту монтажа необходимо производить без ударов и толчков, не разрешается детали станин, стойки, траверсы укладывать друг на друга.
Перед установкой станка на фундамент, нижняя опорная часть станка должна быть тщательно очищена от грязи и следов предохранительной краски или смазки. Перед опусканием станка на фундаменте или станине должны быть установлены комплекты прокладок, высота которых рассчитывается по высотным отметкам. Опускание станка на фундамент необходимо производить осторожно: вначале нужно плавно опустить станок, навести его на фундаментные болты, и проверить взаимное положение болтов и отверстий, затем проследить за предохранением резьбовой части болта от смятия о стенки отверстий станины, а в момент соприкосновения опорной поверхности с подкладками необходимо обратить внимание на равномерное прилегание по всей поверхности. Положение станка, установленного на пакеты подкладок, проверяется и доводится до проектного добавлением или удалением некоторой части подкладок. Грубая проверка положения стайка производится при свободном опирании его на прокладки, а окончательная - при затянутых гайках фундаментных болтов. При монтаже быстроходных станков, к которым предъявляются повышенные требования в отношении вибраций, комплекты временных подкладок после выверки станка заменяются постоянными.
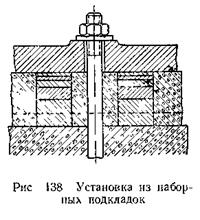
Установка оснований станков на фундаменты, расположенные ниже проектной отметки, с последующей выверкой и подливкой цементным раствором может производиться:
- 1) на наборных металлических подкладках, каждая из которых состоит из двух и более частей 2) на регулируемых клиньях 3) на регулируемых башмаках 4) на домкратах.
Установка оснований на заранее выверенные под проектную отметку металлические детали - балочные каркасы или фундаментные плиты, - забетонированные в фундаменте, может производиться:
- 1) на обработанные металлические подкладки; 2) на обработанные клиновые подкладки с последующей их приваркой одна к другой (рис. 139); 3) без подкладок (на фундаментные плиты).
В зависимости от размеров и конфигурации оснований станков величина просвета между нижней плоскостью основания и верхним уровнем фундамента обычно равна 20-60 мм. Для точной установки оснований применяются подкладки толщиной 0,5; 1; 2; 3 и 4 мм и фольга 0,1-0,5 мм. Подкладки толщиной до 20 мм изготовляются стальными (из листа или полосы), а свыше 20 мм - чугунными литыми.
Металлорежущие станки для точных работ, которые имеют большие размеры станин, устанавливаются на фундаменты непосредственно на регулируемых клиньях или регулируемых башмачках без подливки станины цементным раствором, для возможности периодической проверки станка на точность. Установка координатно-расточных станков производится на тарельчатых винтовых домкратах без последующей подливки станин. Правильная установка станка на фундамент влияет на точность работы станка.
Станки на фундамент могут устанавливаться без закрепления на фундаменте, с закреплением на фундаменте путем подливки цементным раствором или с помощью фундаментных болтов. Поверхность фундамента, на которую подливается бетон, должна быть очищена от масла и грязи, насечена, обдута сжатым воздухом и промыта горячей водой.
По периметру плиты необходимо установить опалубку из досок без щелей на расстоянии 100-150 мм от края фундаментной плиты и на 20-30 мм выше уровня подливки. Трубопроводы, соприкасающиеся с опалубкой, необходимо обернуть толем, для того чтобы после заливки основания остались зазоры, необходимые для свободного перемещения труб при их расширении.
Для заливки основания и фундаментных болтов применяются цементные растворы в соотношении 1 : 3 или 1 : 2 (одна часть цемента и три или две части песка). При величине зазора между основанием и фундаментом более 50 мм применяются растворы с добавлением мелкого гравия (1:1:3 или 1:1:2).
Для подливки машин, передающих на фундамент большие динамические усилия, применяется раствор состава 1:1 из чистого кварцевого песка и портландского цемента не ниже марки 400, при этом перед подливкой бетонируемая площадь подливается жидким раствором чистого цемента (молока).
Заливка фундаментных болтов с анкерными плитами производится одновременно с подливкой основания после окончательной центровки узлов машины. Для сохранения большей эластичности и облегчения замены болтов в случае обрыва рекомендуется залить фундаментные болты на высоте 200-500 мм от низа, засыпать песком остальную часть, после чего подлить основание.
Фундаментные болты с загнутым или заершенным концом заливаются бетоном после центровки узлов машины.
Крепление оснований к фундаменту производится после надежного схватывания бетона (через 10-18 дней). Фундаментные болты затягиваются ключом, а после окончательной затяжки гайки стопорят предусмотренными для этого средствами или производится прихватка электросваркой болтов и гаек между собой и к основаниям.
При монтаже электрической части станка необходимо произвести установку электромотора, пусковой электроаппаратуры и линий электропитания, а также заземление станка. Производится монтаж в соответствии с существующими правилами и нормами.
Изменения в технических процессах изготовления машин в связи с изменением их конструкции требует периодической перестановки станков. Для сокращения времени на производство монтажа электропроводки при перестановке станков необходимо применять наиболее рациональные системы, позволяющие быстро подключить станки к системе питания.
Во избежание несчастных случаев от поражения электрическим током все станки, моторы, приводящие их в движение, аппаратура управления электромотором и электрооборудованием станка должны иметь защитное заземление и зануление. Защитное заземление представляет собой электрическое соединение станка, мотора, электроаппаратуры и земли, имеющее незначительное сопротивление, гарантирующее безопасность человека при прохождении через него тока при повреждении изоляции.
Зануление представляет собой металлическое соединение с за-земленным нулевым проводом металлических частей (станка, электромотора, электроаппаратуры), которые могут оказаться под напряжением.
В сырых помещениях с едкими парами заземляющие провода должны укладываться на подкладки на расстоянии от стены не менее 10 мм. Они также должны находиться выше уровня грунтовых вод
Провода защитного заземления, если они проложены, открыто, окрашиваются в черный цвет, а незаземленные нулевые провода окрашиваются в фиолетовый цвет с поперечными полосам" шириной 15 мм через каждые 150 мм; число полос не менее двух.
При напряжении местного освещения станка выше 65 в необходимо выполнить его заземление или зануление. Кроме выполнения заземления и зануления у станков рекомендуется устраивать изолирующие площадки (деревянные решетки, резиновые подкладки и т. п.), уменьшающие опасность поражения человека при ее прикосновении к станку, находящемуся под напряжением.
Похожие статьи
-
Маршрутная технология процесса изготовления деталей - Ремонт токарного станка
Выбор заготовки: при выборе заготовки для механической обработки заменяемой детали нужно учитывать технические требования, предъявляемые к детали....
-
Охрана труда и промышленная санитария в РМЦ - Ремонт токарного станка
При среднем и особенно капитальном ремонтах объем разборки велик. С началом отделения узлов с машины появляется опасность травмирования рабочих, занятых...
-
Испытание оборудование с проверкой на геометрическую точность - Ремонт токарного станка
После обкатки станка на холостом ходу и испытания под нагрузкой должно быть проверено соответствие нор-мам точности, установленным действующими ГОСТами:...
-
Разборка оборудования - Ремонт токарного станка
Перед разборкой поступающего в ремонт станка его осматривают и фиксируют дефекты, выявленные в процессе эксплуатации. Перед разборкой станка проверяют...
-
Монтаж устройств - Оборудование участка железной дороги устройствами заграждения
Размещение составляющих частей УЗП производится в соответствии с чертежом привязки УЗП к переезду. Подключение основного и резервного однофазного...
-
Ремонт металлургического оборудования Успешное проведение работ по монтажу оборудования зависит от рациональной планировки и организации монтажной...
-
Монтаж оборудования Транспортировка выпарного аппарата Выпарной аппарат транспортируют на железнодорожных платформах отдельными блоками. При перевозке...
-
Испытание и сдача оборудования в эксплуатацию, Обкатка оборудования - Ремонт токарного станка
Обкатка оборудования Отремонтированное и отрегулированное оборудование подлежит испытанию в целях уточнения годности его для дальнейшей эксплуатации....
-
Контроль качества ремонта и методы испытания - Деревообрабатывающие станки и их эксплуатация
Качество капитального ремонта оценивается по факторам, характеризующим ремонт и определяющим качество отремонтированного оборудования. К факторам,...
-
Правила эксплуатации Во время эксплуатации вентилятора необходимо: - проводить системное наблюдение; - проводить периодически технический осмотр. Во...
-
Расчет режимов резания - Ремонт токарного станка
Операция 010. Токарная. Переход 1. Обточить поверхность Ш30+0,35 на длину 155 мм за 3 прохода. Рис. Схема установки заготовки при обработке поверхности...
-
Маршрутная технология процесса восстановления деталей - Ремонт токарного станка
Разработка технологического процесса восстановления изношенной детали состоит из следующих этапов: 1) изучение исходных данных. 2) выбор базовых...
-
Ремонт оборудования, Прием оборудования в ремонт - Ремонт токарного станка
Прием оборудования в ремонт 1) Направленный на капитальный ремонт станок должен быть очищен от грязи и стружки. 2) Масло и эмульсия должны быть слиты из...
-
Расчет припусков - Ремонт токарного станка
2. Расчет припусков на обработку поверхности Ш25h8(-0,33) Технологический маршрут обработки данной поверхности состоит из следующих переходов: 1. Точение...
-
Технологический процесс разборки узла - Ремонт токарного станка
После демонтажа узлов приступают к их подетальной разработке. Прежде, чем разъединить какой-либо подузел, нужно разобраться в его конструкции, чтобы не...
-
Заключение - Ремонт токарного станка
Наличие в достаточном количестве различного первоклассного оборудования еще не решает задачу высокопроизводительной ритмичной работы предприятия. Задачей...
-
Установка СОЖ туманом - Проектирование и применение токарного станка модели 1К660Ф3
Установка предназначена для охлаждения режущего инструмента распыленной жидкостью. Работает следующим образом: - от цеховой магистрали сжатый воздух под...
-
Успешное выполнение ремонта в значительной мере зависит от качества разборки. Разборочный процесс принято изображать в виде технологической схемы. При...
-
Сборка узла, механизма, машины в целом предшествует и комплектация. По технологической карте сборки и дефектной ведомости в комплектовочном отделении...
-
Текущий ремонт - Оборудование участка железной дороги устройствами заграждения
1) Ремонтные работы на УЗП проводятся по необходимости, в случае появления отказов в работе из-за повреждения или поломки какой-либо детали или узла....
-
Устройство и назначение ремонтируемого узла - Ремонт токарного станка
Полуавтомат работает методом обкатки инструмента и изделия. Для осуществления обкатки на полуавтомате предусмотрена кинематическая связь вращения...
-
Дефектация деталей узла и используемый инструмент - Ремонт токарного станка
Дефектная ведомость является документом, обосновывающим метод и трудоемкость ремонта узла. Она составляется (для дипломных работ) на 10-12 деталей,...
-
Компоновка и устройство оборудования, Смазка оборудования - Ремонт токарного станка
Расположение частей полуавтомата и их компоновка представлены на рисунке 1.2 , 1.3 и в таблице 5. Рисунок 1.2. Расположение составных частей полу...
-
Техника безопасности на предприятии - это совокупность мероприятий организационного и технического характера, которые направлены на предотвращение на...
-
Смазывание - это нанесение смазочного материала на трущиеся поверхности для уменьшения сопротивления трению и повышению износостойкости трущихся...
-
Надежность - это комплексное свойство технического объекта (приборы, устройства, машины, системы); состоит в его способности выполнять заданные функции,...
-
При проведении научно-технических расчетов часто используются зависимости вида у (х), причем число точек этих зависимостей ограничено. Неизбежно...
-
Транспортировка и сохранение - Монтаж и ремонт оборудования
Вентиляторы транспортируются в собранном виде. Допускается вентиляторы больших габаритов транспортировать не полностью собранными. Упаковываются с...
-
Стоимость и продолжительность монтажа могут быть значительно уменьшены при внедрении прогрессивных методов организации и производства работ. При этом...
-
ТЕХНИКО-ЭКОНОМИЧЕСКОЕ ОБОСНОВАНИЕ - Монтаж, техническая эксплуатация и ремонт питателя шнекового
От надежности и долговечности технического оборудования зависят производительно - экономические показатели деятельности предприятия. Простой оборудования...
-
Определяем трудозатраты для механической части для провидения капитального ремонта , чел/час Где RМ - категория сложности механической части, RМ = 0,5 р....
-
Назначение, область применения и место установки в производственном процессе Шнековый питатель ПШМ - 1 входит в состав аэрозоль транспортера и...
-
ВВЕДЕНИЕ - Монтаж, техническая эксплуатация и ремонт питателя шнекового
В последние годы в связи с ростом производства построено большое количество новых предприятий оснащенных современными технологиями, новейшим техническим...
-
Определение геометрических размеров основных элементов фланцевого соединения Расчетная температура элементов фланцевого соединения определяется по...
-
Исходные данные Мощность электродвигателя Р1 = 1500 об/мин, N1 = nДв Кинематический расчет Р2 = Р1 - ? ; Р2 = 30 -0,96 = 28,8 кВт, Где ? - кпд,...
-
Выводы - Проектирование и применение токарного станка модели 1К660Ф3
Дипломный проект состоит из шести частей: - конструкторской; - технологической; - специальной; - организационно-экономической; - охраны труда и техники...
-
На каждую операцию технологического процесса назначаем режимы резания согласно нормативным справочникам, а для двух операций (04 Токарная и 38...
-
Регулировку подшипников шпинделя необходимо производить осторожно, не допуская их перегрузки (перетяжки). Регулировка подшипников заключается в выборе...
-
Таблица 2 № Наименование этапа работы Наименование операции Профессия Трудоемкость, час -разряд- 4 5 6 1 Разборка узла Слесарь 3 Бригадир 3 Итого: 6ч 2...
-
Станина Станина состоит из головной части и секций, стыкуемых по длине. На головной части станины установлена передняя бабка. Остальные секции станины...
Монтаж оборудования - Ремонт токарного станка