Специальная часть, Вакуумные ионно-плазменные методы нанесения покрытий, Плазмохимическое газофазное осаждение (ПХГО) - Нанесение антидеструкционных покрытий на топливные и кислородные баки космических аппаратов
Вакуумные ионно-плазменные методы нанесения покрытий
В настоящее время существует множество различных способов нанесения покрытий. Наиболее прогрессивными из них являются вакуумные ионно-плазменные методы. Эти методы обладают эффективностью, экологической безопасностью и позволяют наносить высококачественные покрытия из широкой номенклатуры материалов.
По способу формирования ионно-плазменных потоков методы нанесения покрытий делятся на два основных класса - методы плазмохимического газофазного осаждения (ПХГО) и методы физического газофазного осаждения (ФГО).
Проблемой существующих методов нанесения покрытий является либо высокая стоимость оборудования и небольшие скорости осаждения покрытий как в случае ВЧ или СВЧ разрядов, плохая однородность наносимых покрытий, как при использовании дугового распыления, либо небольшие площади обрабатываемых поверхностей, как при лазерной абляции, либо низкая адгезия, как при термическом испарении [1].
Ниже рассмотрены различные методы нанесения тонкопленочных покрытий на подложки большой площади.
Плазмохимическое газофазное осаждение (ПХГО)
Химическое газофазное осаждение является процессом, в котором устойчивые твердые продукты реакции зарождаются и растут на подложке в среде с протекающими в ней химическими реакциями (диссоциация, восстановление и др.).
В этом процессе используются различные источники энергии, такие, например, как плазма, ультрафиолетовое излучение и т. д.
Процесс химического газофазного осаждения, активируемого плазмой (ПХГО), разработан относительно недавно (1974-1978 гг.), главным образом для получения тонких пленок, предназначенных для исследования в микроэлектронике, оптике и солнечной энергетике.
В процессе ПХГО покрытие на подложке образуется в ходе химических реакций, активируемых электрическим разрядом в газовой фазе. Основное преимущество процесса ПХГО заключается в том, что используются относительно низкие температуры подложек (< 300єС), достигаются лучшая покрывающая способность и адгезия, процесс лучше контролируется. Вместо тепловой энергии газы-реагенты активируются быстрыми электронами.
Другим преимуществом процесса ПХГО является то, что часто достигаются более высокие скорости осаждения, чем в процессе обычного (термического) ХГО. И это предоставляет бульшие возможности в выборе различных технологических параметров, хотя контролировать их оказывается сложнее.
Однако осаждение чистых материалов этим методом фактически невозможно (за исключением полимеров), поскольку почти все недесорбируемые газы удерживаются покрытием. Это одно из основных ограничений, которое иногда превращается в преимущество, как, например в случае нанесения аморфного кремния, содержащего Н2.
Другой недостаток - сильное взаимодействие плазмы с растущей пленкой. Высокая скорость осаждения приводит к плохой контролируемости однородности и требует тщательной отладки реакционной установки.
В процессе ПХГО могут быть выделены четыре стадии:
- 1) получение плазмы; 2) химическая диссоциация и разложение в результате столкновений с электронами; 3) транспортная реакция; 4) формирование покрытия на подложке.
Метод ПХГО отличается от распыления тем, что используемые газы состоят из полиатомных молекул обычно с низкими потенциалами ионизации в отличие от, например, аргона при распылении. Применяются также более высокие давления (10-100 Па), что обеспечивает бульшую частоту столкновений и меньшую длину свободного пробега.
Процесс ПХГО характеризуется разложением реагентов в разряде в таких условиях, в которых они обычно остаются стабильными и нереагирующими, например, при низкой температуре. Основной механизм разложения в плазме - диссоциация при столкновениях с быстрыми электронами. Ионизация и диссоциация приводят к тому, что скорости реакций в плазме значительно выше скоростей химических процессов в электрически нейтральной системе даже при высоких температурах.
При нанесении покрытий методом ПХГО используются все модификации тлеющего, ВЧ и СВЧ разрядов.
В работе [2] для нанесения толстых пленок алмаза использовалась углеводородная плазма тлеющего разряда с импульсным током. Установка для нанесения покрытий с диодной системой электродов схематически изображена на рис. 2.
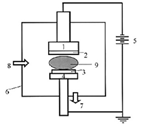
Рис. 2. Экспериментальная установка для нанесения пленок алмаза методом ПХГО
1 - держатель катода; 2 - катод; 3 - подложка; 4 - анод; 5 - источник питания постоянного тока; 6 - вакуумная камера; 7 - насос; 8 - газонапуск; 9 - плазма.
В качестве катода использовалась круглая молибденовая пластина диаметром 13 см и толщиной 1,5 см, нагреваемая до 1000єС. Вольфрамовая подложка диаметром 10 см располагалась на медном водоохлаждаемом аноде. Катод соединялся с источником питания, генерировавшим импульсы с длительностью 1500 мкс и временем между импульсами 15 мкс.
Использование импульсного тока позволило решить проблему дугообразования.
Напряжение и ток изменялись в пределах от 850 до 950 В и от 35 до 50 А, соответственно.
Источником газа являлась смесь метана с водородом, напускаемая со скоростью 200 мл/мин. Рабочие давления лежат в пределах от 13-103 до 26-103 Па (100-200 Торр).
К одной из разновидностей тлеющего разряда относится разряд с полым катодом.
Его достоинством является увеличение плотности плазмы в 100-1000 раз за счет перекрытия зон отрицательного свечения противоположных частей катода. Наиболее простыми формами полого катода являются цилиндрическая трубка или две прямоугольные параллельные пластины. Последняя конструкция наиболее проста для масштабирования и получила большое распространение, в частности, она применялась в работе [3].
Схема используемого источника плазмы показана на рис.3. Для того чтобы отделить реактивный газ от катода, использовался постоянный поток инертного газа через полый катод. Реактивный газ активировался энергетичными электронами из плазмы. Оптимальное рабочее давление данного источника плазмы составляло 100 Па.
Первые эксперименты были проведены с источником плазмы, имеющим высоту 6 см и ширину 4 см (длина катода всегда равнялась 10 см). Затем, высота и ширина катода были уменьшены в 4 раза для того чтобы увеличить плотность плазмы и уменьшить количество распыленного материала катода на подложке. Расход аргона и мощность также были уменьшены в 4 раза.
По сравнению с первым источником скорость нанесения и однородность пленки не изменились. Это объясняется тем, что произошло увеличение в 4 раза плотности плазмы в полом катоде.
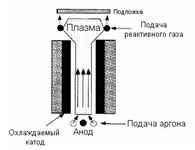
Рис. 3. Источник плазмы с полым катодом
Большинство экспериментов по нанесению гидрогенизированных углеродных (а-С: Н) пленок было проведено со второй конструкцией плазменного источника. В качестве газа-реагента использовался этан.
Параметры процесса нанесения пленок представлены в таблице 1. Было обнаружено, что скорость нанесения пленки повышается с увеличением мощности разряда и расхода этана.
Таблица 1.
Параметры нанесения а-С: Н пленок с помощью тлеющего разряда с полым катодом
Рабочее давление |
80Па |
Расход аргона |
500 мл/мин |
Расход этана |
25 мл/мин |
Мощность |
0,7 кВт (DC) |
Напряжение смещения подложки |
- 400 В (DC) |
Расстояние до подложки |
80 мм |
Скорость нанесения пленки (в центре) |
12 мкм/ч |
Температура подложки |
200єC |
Реализовать нанесение покрытий на подложки большой площади можно за счет увеличения длины линейного полого катода в комбинации со сканированием подложки.
Однако, для повышения производительности или нанесения покрытий на стационарные подложки желательно двухмерное увеличение площади нанесения покрытий. Поскольку ширина полого катода коррелирует с длиной свободного пробега электронов и ионов, то она ограничена диапазоном нескольких сантиметров. Решением этой проблемы авторы считают создание мультикатодного плазменного источника. Разработанный источник, состоящий из пяти параллельно расположенных плоских полых катодов, имеет поперечное сечение размером (10х10) см и позволяет получать достаточно однородное покрытие на площади 160 см2. Хотя следует отметить, что в разряде с полым катодом невозможно достичь очень высоких степеней однородности. В работе [4] для нанесения тонких пленок использовалась линейно протяженная плазма, возбуждаемая СВЧ излучением. Экспериментальная установка схематически представлена на рис.4.
Источник плазмы был установлен в цилиндрической вакуумной камере 1 диаметром 800 мм. Система вакуумной откачки 2 позволяла работать в диапазоне давлений от 5 до 500 Па. Газ в вакуумную камеру подавался через распределительную систему 5, обеспечивающую его равномерное распространение по объему камеры.
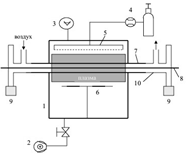
Рис.4. Схематическое изображение источника СВЧ плазмы
- 1 - вакуумная камера; 2 - система откачки; 3 - вакуумметр; 4 - расходомер; 5 - распределитель газа; 6 - подложки; 7 - кварцевая трубка; 8 - медный стержень; 9 - магнетрон; 10 - коаксиальный волновод.
Два коаксиальных параллельных волновода располагались на расстоянии 90 мм друг от друга. Они представляли собой кварцевые трубки 7 с расположенными внутри них медными стержнями 8. СВЧ излучение генерировалось двумя магнетронами 9 с частотой 2,45 ГГц и мощностью 1,2 кВт, связанными друг с другом через коаксиальную линию 10. Микроволны распространялись в основном вдоль медного стержня и кварцевой трубки, заполненной воздухом при атмосферном давлении. При увеличении СВЧ мощности, плазма, возникающая на концах кварцевой трубки, постепенно распространялась к ее центру, до тех пор, пока вся поверхность трубки не покрывалась плазмой. Рекомбинация частиц на поверхности кварцевой трубки приводила к ее нагреву, поэтому применялось охлаждение трубки потоком воздуха, пропускаемым внутри нее. Пригодность данного источника плазмы для технологических применений демонстрировалась нанесением кварцеподобных пленок из смеси гексаметилдисилоксана с кислородом. В данном случае однородность толщины наносимых пленок достигается, главным образом, за счет использования распределенного газонапуска.
Похожие статьи
-
Цель работы - разработка оборудования для нанесения равномерных антидеструкционных покрытий на подложки большой площади (топливные и кислородные баки...
-
Теплопроводящая трубка представляет собой полую медную трубку, которая в вакуумной среде заполняется жидкостью и запаивается с обеих сторон. Эта жидкость...
-
Согласно международной классификации поврежденные трубопроводы подвергаются восстановлению путем нанесения на внутреннюю поверхность стенки трубопровода:...
-
В зависимости от конструкции устройства в качестве теплостока может быть использован специальный радиатор, шасси или корпус устройства. Во всех случаях...
-
Установки плазменного нанесения покрытий - Электротехнологические плазменные установки
Нанесение коррозионно-стойких, жаропрочных и других защитных покрытий осуществляется методами напыления и наплавки. При напылении плазмой частицы...
-
Формирование интерференционного многослойного покрытия осуществлялось с помощью установки вакуумного напыления ВУ-1А (рисунок 4), оснащенной источником...
-
Вакуумные покрытия - Упрочнение и восстановление деталей машин
Наносят их в вакууме в результате образования газовой фазы (генерация паров, летучих продуктов), переноса атомов и частиц газовой фазы на покрываемую...
-
Электронно-лучевые пучки широко используются в технологическом оборудовании для нагрева, сварки, плавки, размерной обработки, распыления, фундаментальных...
-
Hewlett Packard намеревается применить для охлаждения интегральных схем технологии, разработанные для струйных принтеров. Эта разработка позволит...
-
Керамико-полимерные материалы на стеклотканевой или полиимидной основах применяются для изолирования посадочных поверхностей полупроводниковых приборов...
-
Актуальность и современное состояние проблемы Теплопроводящий охлаждающий агрегат электронный Основными тенденциями электронных средств в...
-
Специальные чугуны - Характеристика и структурные методы исследования металлов
К этой группе чугунов (ГОСТ 7769--82) относятся жаростойкие, которые обладают окалиностойкостью, ростоустойчивостью и трещиноустойчивостью, жаропрочные,...
-
Литье с водяным паром, Многокомпонентное литье - Специальные методы литья пластмасс
В процессе данного вида литья при каждом цикле подают перегретый водяной пар в каналы пресс-формы. В горячую пресс-форму происходит впрыскивание...
-
Нанесение металлических покрытий, Никелирование - Технологические советы
Химическое покрытие одних металлов другими подкупает простотой технологического процесса. Действительно, если, например, необходимо химически...
-
Обоснование метода геотехнологии к конкретным условиям - Добыча угля через подземную газификацию
Для данного месторождения подходит геотехнологический способ подземной газификации угля. Подземная газификация угля (ПГУ) - индустриальный процесс,...
-
Введение - Электронно-лучевой синтез TiO2 покрытий с использованием золь-гель мишеней
Интерференционные покрытия применяют для получения высоких коэффициентов отражения (зеркальные покрытия), для увеличения пропускания и контрастности...
-
Кручение под высоким давлением (КВД) (Рисунок 6а) впервые было применено для обработки металлических материалов П. Бриджменом в 1935 году. Свое второе...
-
Характеристика обрабатываемых деталей. Обоснование вида и толщины покрытий Серебро широко применяется в гальванотехнике. Серебро - ковкий, пластичный...
-
Электролитическое хромирование. - Гальванические покрытия
Хромирование подразделяют на коррозионностойкое, износоустойчивое, пористое и декоративное. Различают три группы деталей, наращиваемых хромом,...
-
Разнообразие свариваемых веществ и способов сварки предполагает широкий спектр используемых электродов. Но все они должны отвечать общим требованиям: 1....
-
Напыление (газотермический метод) - Упрочнение и восстановление деталей машин
Суть газотермического напыления газовым потоком заключается в воздействии на поверхность детали нагретых (расплавленных) частиц вещества, имеющих высокую...
-
Особенности технологии изготовления обоев - Обойная бумага
Грунтование обоев - это нанесение покровной композиции на бумагу - основу в целях улучшения ее оптических и печатных свойств. Кроме того, улучшаются...
-
Рис. 1.3. Типовые конструкции охлаждающих агрегатов серии "LAM" Для рассеивания большого количества тепла в маленьком объеме, использование охлаждающих...
-
Результирующая вольт-амперная характеристика туннельного диода определяется комбинацией туннельных и тепловых свойств и имеет довольно необычный вид. В...
-
Одна из основных тенденций современной микроэлектроники - увеличение степени интеграции, объединение на одном кристалле или в одном корпусе максимального...
-
Плазменная технология - молодая отрасль промышленности, интенсивное ее развитие началось в 50-х годах нашего столетия и бурно продолжается в разных...
-
Секция нанесения конверсионного покрытия - Агрегат полимерных покрытий
1). Станция центрирования полосы №6. Металлическая конструкция с гидроцилиндром, двумя роликами и индуктивным определением кромок полосы. Диаметр роликов...
-
Резины специального назначения - Характеристика и структурные методы исследования металлов
Маслобензостойкие резины получают на основе каучуков хлоропренового (наирит), СКН и тиокола. Резины на основе наирита обладают высокой эластичностью,...
-
Литье с водой - Специальные методы литья пластмасс
Литье с водой представляет собой процесс, аналогичный литью с газом. Техническое оснащение водоинжекционного способа литья аналогично газоинжекционному и...
-
Сущность метода и область применения. Сущность заключается в том, что вместо разовой песчано-глинистой используют металлическую форму, называемую...
-
Высокоскоростные методы штамповки - Способы формообразования конструкционных материалов
Особенностью таких методов является высокая скорость деформирования в соответствии с высокими скоростями преобразования энергии. Кратковременное...
-
Под временем перерывов понимается часть рабочего дня, в течение которой трудовой процесс не осуществляется по различным причинам. Время работы в свою...
-
Методы обслуживания потребителей Методы обслуживания потребителей - способ реализации потребителям продукции общественного питания. Различают два метода...
-
Пластическими массами (пластмассами) называются материалы, получаемые на основе природных или синтетических полимеров. Они обладают рядом ценных свойств:...
-
Цианирование - Характеристика и структурные методы исследования металлов
Цианирование в сталелитейном производстве -- процесс диффузионного насыщения поверхностного слоя стали одновременно углеродом и азотом при температурах...
-
Азотирование - Характеристика и структурные методы исследования металлов
Азонирование -- это технологический процесс химико-термической обработки, при которой поверхность различных металлов или сплавов насыщаютазотом в...
-
Поверхностная закалка - Характеристика и структурные методы исследования металлов
Это закалка, при которой только поверхностный слой изделия нагревают до заданной температуры. При поверхностной закалке на некоторую (заданную) глубину...
-
Классификация методов консервирования пищевых продуктов - Способы сохранения пищевых продуктов
Биоз - поддержание жизненных процессов в продуктах с использованием для этой цели иммунитета. Этот принцип применяют при хранении плодов и овощей,...
-
Фальсификация мука масло качественный Идентификация товара и ее методы Идентификация, как правило, требует многосторонних исследований как опытными...
-
Электролитическое железнение - Гальванические покрытия
При железнении, как и при других электролитических процессах, состав и свойства осажденного металла зависят от состава электролита и режимов наращивания....
Специальная часть, Вакуумные ионно-плазменные методы нанесения покрытий, Плазмохимическое газофазное осаждение (ПХГО) - Нанесение антидеструкционных покрытий на топливные и кислородные баки космических аппаратов