Сравнительный анализ базового и проектируемого технологического процесса изготовления детали - Конструкция самолетов
Для сравнительного анализа предварительно составим схемы увязки технологической оснастки как базовым (рисунок 36), так и проектируемым (рисунок 37) методами изготовления детали.
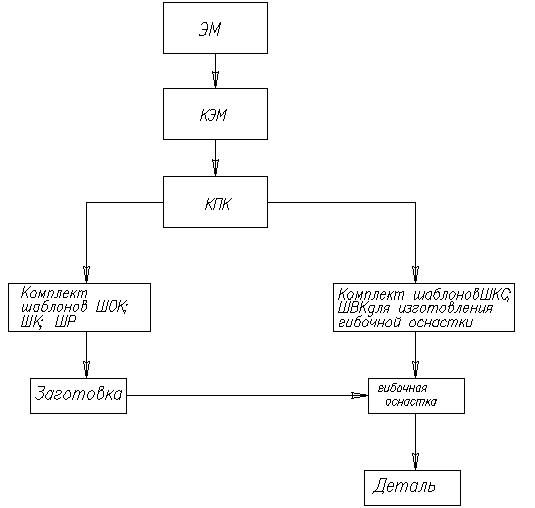
Рисунок 36 - Схема увязки по базовому методу
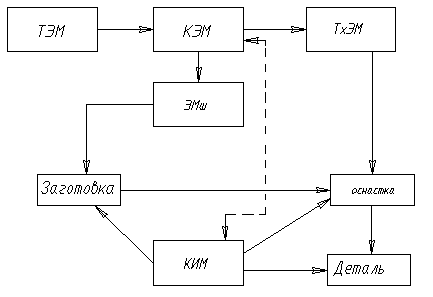
Рисунок 37 - Схема увязки по проектируемому методу
Произведем Расчет По Базовому Методу. При данном варианте увязки технологической оснастки (эталонно - шаблонном методе) операции построения всех сложных поверхностей изделия выполняются при предварительном изготовлении специальных эталонов формы и размеров.
Имея схему увязки и зная допускаемые отклонения размеров контуров выходящих на обвод самолета, не составляет труда сделать размерную цепь для изготовления детали.
Размерной цепью называют всякую замкнутую систему взаимосвязанных размеров.
Размер, с которого начинается перенесение его на деталь, (размер инструмента, плаза) называется первичным.
Технологические размеры и их изменения, входящие в состав технологической размерной цепи, называются составляющими звеньями цепи. Размер, возникающий в результате выполнения всех составляющих звеньев цепи, называется замыкающим звеном технологической размерной цепи.
Погрешности возникают на каждом этапе переноса размеров и формы при образовании действительного размера изделия. В процессе этого накопления происходит накопление погрешностей.
При единичном, мелко - и среднесерийном производстве расчет точности обычно ведут по максимуму и минимуму с учетом того, что суммарная погрешность конечного размера детали определяется алгебраической суммой максимальных значений поэтапных погрешностей.
Составим уравнение погрешности в общем виде:
?п = дэм + дкпк + дшвк+ дшкс + дстанок, (5)
Где ?п - погрешность гибочной оснастки;
ДТэм - погрешность электронного макета (0, 001);

ДКпк - погрешность КПК();
ДКпк - погрешность отрисовки КПК (0, 01);
ДШвк - погрешность ШВК (шаблона внутреннего контура) (-0, 15);
ДШкс - погрешность ШКС (шаблон контура сечения) (0, 2);
ДШр - погрешность изготовления ШР (шаблона развертки) (0, 15);
ДЗаготовки - погрешность изготовления заготовки (0, 1);
ДСтанок - погрешность станка (0, 01).
Величины допустимых значений поэтапных погрешностей при плазово-шаблонном методе, которыми следует пользоваться при расчете суммарной погрешности размеров деталей приведены в таблице 2.
Вычислим значение погрешности:
- ?l =(0, 001)+()+(0, 01)+(-0, 15)+(0, 2)+(0, 015)+(0, 2)+(0, 1)=+0, 826 -0, 811.
Таблица 2 - Допустимые погрешности при изготовлении деталей плазово - шаблонным методом в миллиметрах
Этап переноса размеров |
Допустимая погрешность | |
Контура |
Межцентрового расстояния отверстий | |
ТЭМ |
0, 001 |
0, 001 |
КПК |
-0, 1 +0, 3 |
0, 01 |
Отрисовка КПК |
0, 01 |
0, 01 |
ШВК |
-0, 15 |
0, 01 |
ШКС |
0, 2 |
- |
ШР |
0, 15 |
0, 01 |
Заготовка |
0, 2 |
0, 01 |
Станок |
0, 1 |
0, 01 |
Точность изготовления элементов конструкции сборочной единицы характеризуется отклонением их действительных размеров от номинальных. При этом разница между действительным (д) и номинальным (н) размерами называют производственной погрешностью п т. е.:
Произведем расчет по проектируемому методу. В данном варианте погрешность зависит только от:
- - точности ТЭМ - (0, 001); - точность Эмш - (0, 001); - точности обработки станка - (0, 1); - точность обработки на раскройном центре - (0, 01).
Величины допустимых значений поэтапных погрешностей при бесшаблонном методе, которыми следует пользоваться при расчете суммарной погрешности размеров деталей приведены в таблице 3.
Вычислим значение погрешности:
?п =(0, 001)+ (0, 001)+( 0, 1) +( 0, 01) =+0.112-0.112.
Таблица 3 - Допустимые погрешности при изготовлении деталей бесшаблонным методом в миллиметрах
Этап переноса размеров |
Допустимая погрешность | |
Контура |
Межцентрового расстояния отверстий | |
ТЭМ |
0, 001 |
0, 001 |
ЭМш |
0, 001 |
0, 001 |
ЧПУ |
0, 1 |
0, 001 |
Раскройный центр |
0, 01 |
0, 001 |


Так как допускаемые отклонения размеров на агрегаты фюзеляжа и гондол для самолетов со скоростью полета составляет 0, 8...1, 5 мм. Можно сказать, что проектируемый вариант наиболее предпочтителен, так как погрешность составляет меньшую величину по сравнению с базовым методом изготовления.
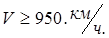
Автоматизация научно - технической инженерной деятельности на предприятии, на этапах проектирования и производства, внедрение в производственный процесс новейших прикладных компьютерных технологий, применение новых обрабатываемых станков (раскройный центр, станки с ЧПУ). Позволило производить продукцию с высоким качеством и высокой точностью, в сжатые сроки.
Похожие статьи
-
Данная деталь изготавливается за два перехода (рисунок 27). Для изготовления оснастки детали необходимо создать ТхЭМ детали первого перехода (рисунок...
-
Технологический анализ чертежа Деталь - колесо зубчатое, изготовляется из легированной стали 45Х ГОСТ 4543-71 (С=0,41% ; Si=0,17% ; Mn=0,5% ; Cr=0,8%),...
-
Технологическая себестоимость изделия складывается из следующих затрат: основной и дополнительной заработной платы производственных рабочих (с...
-
Одной из важнейших задач современного производства является внедрение в производственный процесс новейших прикладных компьютерных технологий. Это вызвано...
-
Анализ методов увязки и обеспечения взаимозаменяемости в самолетостроении - Конструкция самолетов
Многие технологические процессы в самолетостроении основаны на необходимости задания, переноса и воспроизведения геометрической информации о формах и...
-
Определение экономической эффективности При сравнении двух вариантов технологического решения с целью выбора наиболее эффективного, применяется...
-
Анализ проектируемого технологического процесса по опасным и вредным производственным факторам На стационарных конструкторских рабочих местах,...
-
Расчет основной заработной платы произведем по формуле: Где тарифная ставка, руб./час, =25 руб./час; Время, затраченное на производство гибочной...
-
В этом подразделе пояснительной записки необходимо выполнить планировку участка (отделения), имеющуюся на предприятии по месту практики. Планировка...
-
В качестве заготовки для шестерни используем поковку, изготовленную на горячештамповочном кривошипном прессе. Существует ряд основных принципов...
-
Разработка конструктивного плаза компьютерного - Конструкция самолетов
На предприятии корпорации НПК "Иркут" конструктор конструкторского бюро (КБ) оформляет служебную записку на разработку и выдачу предварительного файла...
-
Процесс восстановления деталей в авторемонтном производстве является важным элементом, влияющим на технико-экономические показатели выпускаемой...
-
В результате выполнения данной работы была проведена разработка технологического процесса изготовления партии деталей, установлены и рассчитаны: материал...
-
При устранении износа шеек под шариковый подшипник и восстановлении износа шлицев под фланец ведомого вала по толщине в качестве базовой поверхности...
-
При установлении нормы времени на выполнение данной операции определяется разряд квалификации работы по тарифно-квалификационному справочнику [2]. В...
-
Припуском на обработку называется слой материала, удаляемый с поверхности заготовки в процессе ее обработки для обеспечения заданного качества детали....
-
Припуском на обработку называется слой материала, удаляемый с поверхности заготовки в процессе ее обработки для обеспечения заданного качества детали....
-
Передача информации при комбинированном методе - Конструкция самолетов
Самолетостроение конструктивный плаз геометрический По мере развития программно-технических средств и опыта использования современных компьютерных...
-
Составленный план восстановления поверхностей детали занесен в таблицу 2. Таблица 2 - План восстановления поверхностей Номер и название поверхности...
-
Капитальные затраты по проектному варианту определим по формуле: . Определим капитальные затраты по каждому из суммируемых капиталовложений. Определение...
-
Исходными данными для разработки геометрической информации являются: - сборочные и детальные чертежи самолета (изделия); - электронные геометрические...
-
Технологический процесс - это изменение качественного состояния объекта производства, которое проявляется в изменении формы предметов труда, свойств,...
-
При выборе оборудования для каждой технологической операции необходимо учитывать назначение обработки, габаритные размеры деталей размер партии...
-
Черновое шлифование коренных шеек: Требуемый диаметр: 59,62-0,2 мм; Диаметр шлифуемой детали: 59,9 мм; Используется кругло - шлифовальный станок 3А432....
-
Таблица 5 - Описание выбранного режущего инструмента Номер и наименование операции Название режущего инструмента ГОСТ или ТУ на режущий инструмент...
-
Выбор материала шатуна Для изготовления шатуна бензинового автомобильного двигателя (n=6000 об/мин) выбираем в качестве материала шатуна сталь 18Х2Н4МА,...
-
Рис. 4. Трехслойная печатная плата Многослойные печатные платы имеют ряд достоинств: - В многослойных печатных платах формируется практически полностью...
-
Введение - Разработка технологического процесса изготовления зубчатого колеса
Одной из важнейших задач стоящих перед машиностроением, является всемерное повышение технического уровня производства. Решение этой задачи определяется...
-
Детали современных автомобильных двигателей -- блок цилиндров, головка блока, коленчатый и распределительный валы, шатуны -- изготовляются с высокой...
-
Описание и характеристика детали Восстановление вал передача автомобиль Вал ведомый коробки передач автомобиля ГаЗ 53-А относится к классу деталей...
-
Введение - Технологический процесс восстановления ведомого вала коробки передач
Ремонт автомобилей является объективной необходимостью, которая обусловлена техническими и экономическими причинами. Во-первых, потребность народного...
-
Схема централизованного управления производством при методе технологических комплексов приведена в Приложении А. Схема технологического процесса зоны...
-
В разработку ТП сборки и монтажа входит следующий комплекс работ: Выбор типового или группового техпроцесса. Составление маршрута единичного ТП....
-
Исходя из функционального назначения, гильзы цилиндров относятся к главным элементам поршневых ДВС и являются наиболее ответственной деталью ЦПГ. Стенки...
-
Расчет токов и напряжений до коммутации. Докоммутационная схема приведена на рис. 2. Рис. 2 Докоммутационная схема Расчет токов и напряжений в момент...
-
В настоящее время насчитывают до двухсот методов, способов и вариантов изготовления печатных плат. Однако большинство из них устарело. В современном...
-
Заварка не более двух трещин В (рисунок 1) длиной менее 2/3 периметра сечения основных горячекатаных элементов хребтовых балок (двутавр в полувагонах и...
-
Требуется спроектировать транспортный бензиновый двигатель для автомобиля мощностью: Ne=140 кВт при 6000 об/мин. Основным топливом для данного двигателя...
-
Оценка частоты гармонических сигналов на основе анализа амплитудно-частотной характеристики процесса
Оценка частоты гармонических сигналов на основе анализа амплитудно-частотной характеристики процесса Бордюков Антон Геннадьевич, Аспирант...
-
Многогранность структуры авторемонтного производства, выполняемых работ и используемого технологического оборудования предопределяют многообразие видов...
Сравнительный анализ базового и проектируемого технологического процесса изготовления детали - Конструкция самолетов