Анализ методов увязки и обеспечения взаимозаменяемости в самолетостроении - Конструкция самолетов
Многие технологические процессы в самолетостроении основаны на необходимости задания, переноса и воспроизведения геометрической информации о формах и размерах деталей, узлов и агрегатов конструкции планера самолета. Весь комплекс этих процессов определяется понятием "формообразования изделия". При этом под формообразованием понимается не только собственно воспроизведение форм и размеров отдельных деталей и сборочных единиц, но и их взаимное расположение в пространстве с обеспечением заданных взаимосвязей, то есть задание структуры изделия.
В процессе формообразования изделия решаются две основные задачи: увязка геометрических параметров изделия и обеспечение взаимозаменяемости в процессе его производства и эксплуатации. Под увязкой понимается взаимное согласование форм и размеров элементов конструкции при заданных условиях их взаимного расположения и сопряжения. Обеспечение взаимозаменяемости подразумевает создание производственных условий воспроизведения форм и размеров элементов конструкции на всех этапах изготовления изделия при сохранении заданных условии их сопряжения между собой без выполнения подгоночных или доводочных работ.
В связи с этим определяющую роль в процессе формообразования играет принятый на данном предприятии метод задания, переноса и воспроизведения форм и размеров элементов конструкции планера самолета.
На сегодняшний день в практике самолетостроения существуют следующие методы формообразования изделия: чертежно-инструментальный; чертежно-шаблонный; чертежно-макетный; плазово - инструментальный; плазово - шаблонный; плазово - макетный; эталонно-инструментальный; эталонно-шаблонный; эталонно-макетный; программно-инструментальный; программно-шаблонный; программно-макетный.
При всем разнообразии методов их можно укрупненного подразделить на три основные группы: независимый метод, связанный метод и комбинированный - сочетающий возможности первых двух. Эволюция процессов формообразования в самолетостроении развивалась таким образом, что на заре авиастроения в России использовался независимый метод, принципиальная схема которого приведена на рисунке 1а. При независимом методе этапы переноса форм и размеров для образования конечных сопрягаемых размеров А и Б осуществляются независимо и параллельно, используя единый источник информации - чертеж и единый носитель информации - эталон метра и принятую систему задания допусков и посадок.
А) независимый метод; б) связанный метод; в) расчетно - плазовый метод; г) бесплазовый метод
Рисунок 1 - Эволюция методов формообразования в самолетостроении
Поле погрешности увязки размеров А и Б при независимой схеме запишется в виде:
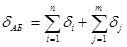
, (1)
Где i, j - поля погрешности i-того и j-того этапов переноса размеров, 1<i<n; 1<j<m, где n и m - количество индивидуальных этапов переноса размеров А и Б соответственно; АБ - поле погрешностей увязки размеров А и Б.
Независимый метод позволит значительно сократить сроки и материальные издержки производства за счет использования универсальных средств изготовления и контроля и распараллеливания работ. Однако, при возрастании габаритных размеров, повышении сложности форм и структуры изделия погрешности переноса информации увеличивались, что при одновременном возрастании требований к точности воспроизведения форм и размеров изделия привело к необходимости выбора иного метода формообразования - связанного.
Схема увязки сопрягаемых размеров А и Б по связанному методу приведена на рисунке 1б. Сущность его состоит в том, что перенос информации о формах и размерах изделия производится непосредственным копированием от одного источника информации к другому, создавая таким образом связанные этапы переноса информации. При переносе информации существует Р общих для двух размеров этапов и q и r раздельных.
Поля производственных погрешностей одного из размеров и увязки двух размеров между собой могут быть описаны следующими уравнениями:
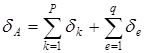
, (2)
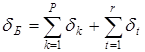
, (3)
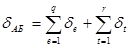
, (4)
Где А, Б - поля производственных погрешностей размеров А и Б соответственно;
АБ - поле производственной погрешности увязки размеров А и Б;
K, E, T - поля производственных погрешностей общего k и индивидуальных e и t этапов.
Как видно из этих уравнений, на точность увязки сопрягаемых размеров А и Б не влияет погрешность общих этапов переноса форм и размеров. Поэтому этапы, дающие большие погрешности переноса информации в каждой из индивидуальных ветвей, нужно перенести в общие для обоих размеров этапы.
Связанный метод формообразования реализован на предприятиях авиастроения в различных вариантах: плазово - шаблонный, плазово - макетный; эталонно - шаблонный и другие. Такой метод формообразования позволяет получить приемлемую точность воспроизведения форм и размеров изделия. Однако обладает рядом недостатков, среди которых можно отметить высокую материалоемкость, трудоемкость, стоимость и длительность цикла подготовки производства, что в условиях возрастающих требований к сокращению цикла производства изделия и ограниченных материальных и трудовых ресурсах становится существенным фактором снижения конкурентоспособности предприятия.
Развитие современных технических средств автоматизации производства и компьютерных технологий позволило вновь вернуться к использованию независимого метода формообразования, но на принципиально новом уровне (рисунок 1г). Сущность этого метода состоит в том, что первоисточником геометрической информации о формах и размерах изделия служит его полная твердотельная математическая модель. Создание математической модели изделия производится в процессе конструкторско-технологического проектирования изделия, что позволяет задачи объемной увязки элементов изделия осуществить непосредственно на стадии проектирования. Обеспечение взаимозаменяемости элементов изделия в условиях серийного производства производится на основе независимого переноса информации о форме и размерах изделия на всех этапах путем использования технических средств автоматизации и программных систем обработки информации. Такой метод носит название бесплазового метода увязки (БМУ) или метода автоматизированного формообразования (МАФО).
Реализация независимого метода автоматизированного формообразования в полном объеме позволит значительно повысить эффективность производства по сравнению со связанным методом.
Невозможность в полном объеме реализации независимого метода формообразования приводит к необходимости выбора эволюционного подхода к его внедрению на предприятии. Такой подход называют расчетно - плазовым методом. Сущность расчетно - плазового метода (РПМ) состоит в том, что на предприятии параллельно используются независимый и связанный методы формообразования с постепенным вытеснением связанного метода из производства (рисунок 1в).
На начальном этапе эволюции такого комбинированного метода создается математическая модель поверхности агрегата - аналог теоретического плаза. На его основе создается конструктивный плаз, но выполненный на машинном носителе - конструктивный плаз компьютерный (КПК). КПК на начальном этапе внедрения РПМ в полном объеме используются по традиционной технологии увязки и обеспечения взаимозаменяемости, то есть служит для плоской увязки конструктивных элементов агрегата планера самолета, изготовления основных и производственных шаблонов. Как известно, при плазово-шаблонном методе последовательная схема увязки и изготовления шаблонов требует значительных затрат времени на подготовку производства и высокой точности выполнения ручных операций. Эти недостатки можно устранить, если плазовое прочерчивание выполнить не ручным способом на металлических заготовках, а с помощью "плоских" систем компьютерного проектирования среднего или низкого уровня по правилам, характерным для ручного прочерчивания. В этом случае выполнение плазов в металле теряет всякий смысл, так как электронный плаз позволяет выполнить работы гораздо быстрее и точнее.
Контроль изготовленных шаблонов возможен с использованием координатно-измерительных машин (КИМ) на основе исходного файла шаблона.
Похожие статьи
-
Наиболее эффективным в современных условиях, обеспечивающим высокое качество летательных аппаратов, является способ сборки, основанный на использовании...
-
Для сравнительного анализа предварительно составим схемы увязки технологической оснастки как базовым (рисунок 36), так и проектируемым (рисунок 37)...
-
Одной из важнейших задач современного производства является внедрение в производственный процесс новейших прикладных компьютерных технологий. Это вызвано...
-
Исходными данными для разработки геометрической информации являются: - сборочные и детальные чертежи самолета (изделия); - электронные геометрические...
-
ВВЕДЕНИЕ - Конструкция самолетов
Целью предприятий авиационной промышленности, и в частности на предприятии корпорации НПК "Иркут", сделавших выбор в пользу автоматизированных систем...
-
Передача информации при комбинированном методе - Конструкция самолетов
Самолетостроение конструктивный плаз геометрический По мере развития программно-технических средств и опыта использования современных компьютерных...
-
ЗАКЛЮЧЕНИЕ, СПИСОК ЛИТЕРАТУРЫ - Конструкция самолетов
Переходный период к бесплазовому методу увязки на головном предприятии рассмотрен как важный технологический этап в жизни завода. Проведена работа, в...
-
Пакет Teamcenter Engineering (ранее известный как IMAN) предназначен для поддержки жизненного цикла изделий на ранних стадиях: от концептуального...
-
Анализ проектируемого технологического процесса по опасным и вредным производственным факторам На стационарных конструкторских рабочих местах,...
-
Используя цифровой регулятор, построенный методом переменных коэффициентов время переходного процесса составляет tПп ? 5,9 сек. при установлении...
-
Основные теоретические сведения Задачи принятия технических решений принято делит на следующие этапы: 1. Формирование целей выбора; покупка изделия и...
-
Для большинства измерений, выполняемых в системах управления технологическими процессами, оценивание погрешности измерений и ее составляющих производится...
-
Основные теоретические сведения Задачи принятия технических решений принято делит на следующие этапы: 1. Формирование целей выбора; покупка изделия и...
-
Цель: вычислить потребляемую мощность схемы программатора. Данные по элементам и рассчитанная мощность сведены в таблицу 2. Таблица 2 - Потребляемая...
-
Постановка задачи Целью данной работы является создание компактной, частично магнитоэкранированной конструкции магнетрона, предназначенного для работы в...
-
Графоаналитический метод анализа Этот метод используется в тех случаях, когда отсутствует отсечка тока. Этот метод известен под названием трех (пяти,...
-
Применение методики передачи геометрической информации, на примере нервюры - Конструкция самолетов
Рассмотрим предлагаемую методику на примере нервюры закрылка, с использованием концепции проектирования на основе мастер - модели. Концепция...
-
Проверка кабеля и его элементов на соответствие конструкции Проверка должна проводиться внешним осмотром без применения увеличительных приборов согласно...
-
При работе нелинейной цепи с большими амплитудами входного сигнала, когда степенная аппроксимация не дает хороших результатов применяется...
-
Определение экономической эффективности При сравнении двух вариантов технологического решения с целью выбора наиболее эффективного, применяется...
-
Проволочные методы Соединения проволокой является в настоящее время, к сожалению, пока наиболее распространенным способом монтажа ИМС. Рассмотрим...
-
Анализ характеристик объекта проектирования трудовой деятельности человека, производственной среды Фотоприемное устройство является модулем приемной...
-
В практике работы АТП обычно применяются два метода организации технологического процесса ТО автомобилей: на универсальных и на специализированных...
-
Метод сравнения с мерой - Структурные методы повышения точности средств измерения
Метод сравнения с мерой основан на том, что размер измеряемой величины сравнивают с помощью компаратора с размером величины, воспроизводимой мерой, а...
-
Рис. 4. Трехслойная печатная плата Многослойные печатные платы имеют ряд достоинств: - В многослойных печатных платах формируется практически полностью...
-
Схема централизованного управления производством при методе технологических комплексов приведена в Приложении А. Схема технологического процесса зоны...
-
Анализ организации охраны труда Охрана труда - это система обеспечения безопасности жизни и здоровья работников в процессе трудовой деятельности,...
-
За основу программного обеспечения для микроконтроллера ATtini2313 была заимствована программа для микроконтроллера ATmega8, разработанная на программном...
-
Технологии "последней мили". Сравнительный анализ Термин "последняя миля" стал часто употребляться в отечественной технической литературе сравнительно...
-
Повышение точности измерений в промышленности является одним из существенных резервов повышения качества продукции и эффективности производства. На...
-
Расчет токов и напряжений до коммутации. Докоммутационная схема приведена на рис. 2. Рис. 2 Докоммутационная схема Расчет токов и напряжений в момент...
-
Операционный усилитель имеет Ки?1, очень большое (несколько МОм) Rвх и Rвых?0. Исходные данные: Rвх=2МгОм; Rвых=1кОм; Rвх. д=2МгОм; Rн=2МгОм;...
-
Данная деталь изготавливается за два перехода (рисунок 27). Для изготовления оснастки детали необходимо создать ТхЭМ детали первого перехода (рисунок...
-
Микроклимат производственного помещения - Конструкция самолетов
В производственных помещениях, в которых работа с использованием ПЭВМ является основной, обеспечиваются оптимальные параметры микроклимата для категории...
-
Электробезопасность - Конструкция самолетов
Причины Поражения Электрическим Током. При работе на ПК используется энергия напряжения 220В переменного тока с частотой 50Гц. Для местного освещения...
-
.1 Освещенность производственного помещения Помещения с ПЭВМ имеют естественное и искусственное освещение. Естественное освещение должно осуществляться...
-
Устройства для отображения информации применяются в системах, где информацию требуется представить в форме, удобной для визуального восприятия. Их...
-
Требуется спроектировать транспортный бензиновый двигатель для автомобиля мощностью: Ne=140 кВт при 6000 об/мин. Основным топливом для данного двигателя...
-
Анализ вредных и опасных факторов Темой данного раздела является обеспечение безопасности при эксплуатации автомобильного бензинового поршневого...
-
Общие сведения Поселок Федоровка находится за удаленной чертой г. Караганды. Так как на балансе нет распределительных сетей, схем распределения, то...
Анализ методов увязки и обеспечения взаимозаменяемости в самолетостроении - Конструкция самолетов