Выбор способов устранения дефектов и оборудования. - Проектирование единичного технологического процесса восстановления гидропривода
Для восстановления всех наружных поверхностей используем вибродуговую наплавку. Основное преимущество этого процесса - небольшой нагрев детали (не более 100є С ) и возможность регулирования твердости наплавленного слоя, в зависимости от марки наплавочной проволоки и использования охлаждения при наплавке, а также высокая производительность до 2,5 кг/час. Для наплавки используем проволоку Пн50 диаметром 1,5 мм. Охлаждающая жидкость - 5% - ный раствор кальцинированной соды, расход 0,5...1 л/мин. Наплавка ведется постоянным током при обратной полярности при напряжении 12...28 В. Оборудование для наплавки: токарный станок 3А228, выпрямитель ВСГ-3, дроссель РСТЭ-34 и наплавочная головка ГМВК-2.
Резьбовое отверстие ремонтируем наплавкой и нарезанием новой резьбы. Наплавку производим полуавтоматом А-547Р, проволокой Св12ГС ГОСТ 2246-70 в среде СО2. Часть наружной поверхности золотника покрываем хромом Хд24:Хмол12.Х12.тв.(молочным и твердым хромом)
При хромировании золотник обрабатывается специальным составом, кроме поверхностей подлежащих осаждению на них металла, препятствующим реакцию с электролитом. В качестве источника питания для наносимого покрытия используется растворимые аноды из стали 10, 20.
Технологический процесс хромирования включает операции: электрохимическое обезжиривание, анодное травление, хромирование, нейтрализацию с последующими промывками после каждой операции. Далее золотник отправляют в сушку.
В нашем случае будем использовать барабан, позволяющий совмещать операции промывки, нанесения гальвано покрытий и сушки (рис.9).
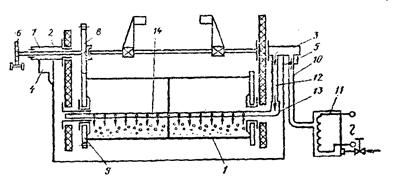
Рисунок 9 - Схема барабана для гальванического осаждения:
1 - шестигранный барабан; 2 - опорная втулка; 3 - воздухоприемная втулка; 4,5 - призмы; 6 - звездочка; 7 - валик; 8,9 - зубчатые колеса; 10 - штуцер; 11 - электрокаллорифер; 12 - воздухопровод; 13 - цапфа; 14 - труба.
Для расточки нового отверстия под резьбу используем сверло ? 9 мм 2300-7195 ГОСТ 886-77 (рис.10), закрепив золотник в зажимном приспособлении. После зенкеруем фаску конической зенковкой 2353-0108 ГОСТ 14953-80 и нарезаем резьбу метчиком М10х1 ГОСТ 9522-60. Размеры контролируются микрометром МК 125-1 ГОСТ 6507-78 и резьбой пробкой М10.
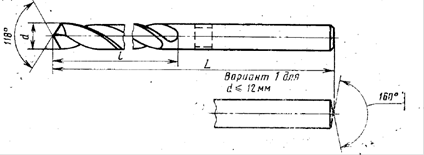
Рисунок 10 - Сверло ГОСТ 886-77.
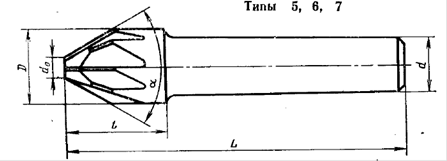
Рисунок 11 - Зенковка коническая ГОСТ 14953-80.
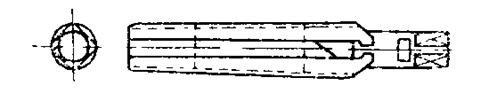
Рисунок 12 - Метчик для метрической резьбы ГОСТ 9522.
Все наплавленные поверхности шлифуем, так как припуск составляет 1 мм Для шлифования используем токарный станок 3А228 . Для шлифования устанавливаем шлифовальный круг вместо резца и приспособление для центровки. Для шлифовки используем круги по ГОСТ 2424-83 типа ПП 80х45х20 2А М28 (рис.13) и 6ТП 100х50х25 2А 40 (рис.14).
Техническая характеристика станка приведена в табл. 2.
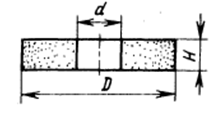
Рисунок 13 - Круг шлифовальный типа ПП.
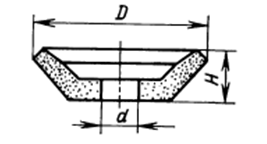
Рисунок 14 - Круг шлифовальный типа 6ТП.
Таблица 2 - Техническая характеристика станка 3А228.
Характеристика |
Ед. измерения |
Значение |
Диаметр обрабатываемых поверхностей: | ||
Наименьший |
Мм |
20 |
Наибольший |
Мм |
200 |
Наибольшая длина точения |
Мм |
125 |
Пределы рабочих подач стола |
М/мин |
210 |
Пределы чисел оборотов изделия |
Об./мин. |
1801200 |
Пределы поперечных подач изделия |
Мм/мин. |
0,051,2 |
Мощность электродвигателя |
КВт |
8,3 |
Для правки золотника используем Пресс "ЕMG-10-550-2" и призмы. Усилие правки выбираем исходя из величины стрелы прогиба, т. е. усилие правки должно быть в 10 раз больше численного значения стрелы прогиба.
Закалку золотника производим на универсальной установке для закалки ТВЧ с использованием индуктора диаметром 25 мм. Охлаждение производим в спрейере. Проверку производим на прессе Роквелла.
Для контроля используем микрометр МК 125-1 ГОСТ 6507-78 и штангенциркуль ШЦ -1-150-0,1 ГОСТ 166-89.
Похожие статьи
-
Для восстановления золотника в зависимости от масштабов производства применяют технологии: А) подефектную; Б) групповую; В) маршрутно-групповую; Г)...
-
При комплектовании деталей распределителя следует руководствоваться величиной допускаемых зазоров в сопряжениях, в соответствии с ГОСТ 16514-96...
-
При эксплуатации гидрооборудования очень важно своевременно и быстро обнаружить детали, нуждающиеся в ремонте. Наиболее эффективным средством обнаружения...
-
Технологический процесс изготовления щитов из ламинированной ДСтП включает следующие операции: 1) раскрой плит на щитовые заготовки (без припусков на...
-
005. Для токарной операции выбираем токарно-винторезный станок модели 16Л20, исходя из его технических характеристик: 1. Наибольший диаметр...
-
Изгиб вала Износ поверхности под подшипник Износ шлицов по ширине Износ резьбы. 005 слесарная 010 токарно-винторезная 015 слесарная 020 наплавочная 025...
-
Изгиб вала Износ поверхности под подшипник Износ поверхности под подшипник Износ шлицов по ширине 005 слесарная 010 токарно-винторезная 015 слесарная 020...
-
Описание конструктивных особенностей и условий работы ремонтируемой детали Условия работы данной детали являются сложными и тяжелыми. Вал постоянно...
-
Введение - Проектирование единичного технологического процесса восстановления гидропривода
Одно из направлений повышения эффективности производства - его переоснащение современной техникой, внедрение передовых технологических процессов и...
-
Схема размещения технологического оборудования - это расположение технологического оборудования и рабочих мест на производственной площади. В курсовом...
-
Токарный станок с ЧПУ RAIS T250 CNC Fanuc 0i-Mate TB Токарный станок с ЧПУ RAIS Т250 CNC Fanuc 0i-Mate TB с наклонной станиной предназначен для...
-
Валики удвоителя работают при постоянных статических нагрузках на износ. В связи с этим их изготавливают их высокопрочной и износостойкой стали 50Х....
-
Задачей правильной эксплуатации оборудования является получение от него наибольшей производительности, при обеспечении его долговечности и точности. Для...
-
В зависимости от типа производства (массовое, серийное, единичное) и требований к качеству изделия выбирают способ изготовления изделия - горячее...
-
Выбор и обоснование баз От правильного выбора технологических баз во многом зависит качество обработки детали. Здесь следует, прежде всего, стрем Иться к...
-
Проектом предлагается для сборки кронштейна специальное приспособление ПС-08. Точная установка деталей кронштейна производится по упорам. Жесткое...
-
Для полуавтоматической сварки проектом предлагается ПДГ-315 Буран. Технические характеристики сварочного полуавтомата ПДГ-315 Буран представлены в...
-
Так как деталь средних размеров, то применение методов пластического деформирования (штамповки, ковки и так далее) не снизит количества механической...
-
Данному виду обработки подлежат следующие поверхности: - Ш16 с фаской 1Ч45° - 30 и 31 соответственно. Обработка поверхностей будет проходить за 2...
-
Выбор сварочных материалов - Технологический процесс сборки и сварки кронштейна
Выбор сварочной проволоки Сварочные материалы при сварке кронштейна принимаются исходя из способа сварки. Для стали 09Г2 сварочная проволока марки...
-
Выбор и обоснование технологического процесса серебрения Предварительная подготовка поверхности металла перед покрытием необходима для того, чтобы...
-
015 операция. Токарная. Для данного вида обработки выбираем токарно-винторезный патронно-центровой станок с ЧПУ модели 16К20Ф3. Токарно-винторезный...
-
Операционная карта выполнена по ГОСТ 3. 1404 - 86 и представлена в приложении 1. Схема наладки станка на выполнение технологической операции...
-
010 операция. Револьверная. Для данного вида обработки выбираем многоцелевой токарно-револьверный патронно-прутковый станок модели 1П420ПФ30 с ЧПУ ( ГОСТ...
-
Работы по санации и восстановлению трубопроводов независимо от применяемого метода в обязательном порядке должны предваряться комплексному...
-
Выбор материала изделия. Обоснование катетов сварных швов Материал изделия для изготовления сварной конструкции, необходимо выбирать в зависимости от...
-
Для Токарных работ выбираем токарный станок с ЧПУ модели 16К30Ф3С32 Наибольший диаметр изделия, устанавливаемый над, мм Станиной 500 Суппортом 320...
-
Технологическая карта на ремонт детали смотреть приложение Б. Выбор размера партии детали Размер партии должен быть выбран с таким расчетом, чтобы...
-
При расчете потребного количества оборудования необходимо привести формулы для расчета производительности с расшифровкой входящих в них параметров и...
-
Выбор схемы базирования и описание работы приспособления Анализируя техническое задание, эскиз детали под выполняемую операцию из ГОСТ 21495-76 выбираем...
-
Деталь "Переходник" предназначена для присоединения электродвигателя к корпусу редуктора и защиты места соединения вала двигателя с валом редуктора, от...
-
Т. к. партия изготовляемых деталей составляет 400шт. Производство не крупносерийное; материал детали не литейная сталь, в исключительных случаях...
-
Для изготовления трикотажного платья целесообразно использовать оборудование представленное в таблице 4. Таблица 4. Характеристика оборудования,...
-
Описание конструктивных особенностей и условий работы ремонтируемой детали Механизм реверса экскаватора ЭО-4112Б предназначен для переключения пути...
-
Выбор вида, способа и формы получения заготовки Метод получения заготовки указан в чертеже - это отливка. Точность отливки - класс 7т-5 по ГОСТ 26645-85,...
-
При проектировании цехов используется 2 метода: детальный и укрупненный. Детальный - технологический процесс разрабатывается на все детали. Укрупненный -...
-
Выбор оборудования для всех операций технологического процесса Определение типа производства. Тип производства определяется по коэффициенту закрепления...
-
Выбор вида заготовки зависит от конструктивных форм деталей, их назначения, условий их работы в собранной машине, испытываемых напряжений. Существует...
-
Обоснование технологического маршрута изготовления детали. План изготовления детали Задача раздела - разработать оптимальный технологический маршрут, т....
-
Технологическая карта включает в себя все основные технологические операции восстановления. В качестве исходных данных для разработки технологической...
Выбор способов устранения дефектов и оборудования. - Проектирование единичного технологического процесса восстановления гидропривода