Вертикально-сверлильный станок 2А135 - Металлорежущие станки и инструменты
На рис.3.1 ВЕРТИКАЛЬНО-СВЕРЛИЛЬНЫЙ СТАНОК 2А135
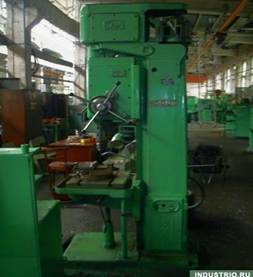
Рис3.1 ВЕРТИКАЛЬНО-СВЕРЛИЛЬНЫЙ СТАНОК 2А135
Станок предназначен для сверления, рассверливания, зенкерования, развертывания отверстий, а также для нарезания резьбы метчиками.
Таблица 3.1 - Технические характеристики 2А135
Условный диаметр сверления |
35 мм |
Max допустимое усилие подачи |
1600 кг |
Электродвигатель |
2870 об/мин |
Max глубина сверления |
225 мм |
Max вертикальное перемещение салазок шпинделя |
200 мм |
Max вертикальное перемещение ствола |
325 мм |
Вес |
1415 кг |
Габариты |
1240х810х2563 мм |
ВЕРТИКАЛЬНО-СВЕРЛИЛЬНЫЙ СТАНОК 2А135
Общая характеристика станка
Назначение станка. Станок предназначен для сверления, рассверливания, зенкерования и развертывания отверстий в различных деталях, а также для торцевания и нарезания резьб машинными метчиками в условиях индивидуального и серийного производства. На станке модели 2А135 обрабатываются детали сравнительно небольших размеров и веса.
Техническая характеристика станка
- - Наибольший диаметр сверления в мм - 35 - Расстояние от оси шпинделя до лицевой стороны станины в мм -300 - Наибольшее расстояние от торца шпинделя до стола в мм -750 - Наибольший ход шпинделя в мм - 225 -Наибольшее установочное перемещение шпиндельной бабки в мм - 200 - Размеры рабочей поверхности стола в мм:
Длина - 500
Ширина - 450
- - Наибольшее вертикальное перемещение стола в мм - 325 - Число скоростей вращения шпинделя - 9 - Пределы чисел оборотов шпинделя в минуту 68-1100 - Количество величин подач - 11 - Пределы величин подачи в мм/об.0,115--1,6 - Мощность главного электродвигателя в кВт 4,5
Основные узлы станка А -- стол; Б -- шпиндельная бабка с коробкой подач и подъемным механизмом; В -- коробка скоростей; Г -- станина (колонна); Д -- основание станины. Органы управления. 1 -- рукоятка перемещения стола; 2 -- штурвал для подъема и опускания шпинделя и для включения механической подачи. Движения в станке. Движение резания -- вращение шпинделя с режущим инструментом. Движение подачи -- осевое перемещение шпинделя с режущим инструментом. Вспомогательные движения -- ручные перемещения стола и шпиндельной бабки в вертикальном направлении и быстрое ручное перемещение шпинделя вдоль его оси. Принцип работы. Обрабатываемая деталь устанавливается на столе станка и закрепляется в машинных тисках или в специальных приспособлениях. Совмещение оси будущего отверстия с осью шпинделя осуществляется перемещением приспособления с обрабатываемой деталью на столе станка. Режущий инструмент в зависимости от формы его хвостовика закрепляется в шпинделе станка при помощи патрона или переходных втулок. В соответствии с высотой обрабатываемой детали и длиной режущего инструмента производится установка стола и шпиндельной бабки. Отверстия могут обрабатываться как ручным перемещением шпинделя, так и механической подачей. Конструктивные особенности. Станок обладает высокой жесткостью, прочностью рабочих механизмов, мощностью привода и широким диапазоном скоростей резания и подач, позволяющим использовать режущий инструмент, оснащенный твердым сплавом. Наличие электрореверса, управляемого как автоматически, так и вручную, обеспечивает возможность нарезания резьбы при ручном подводе и отводе метчика. В конструкции вертикально-сверлильного станка модели 2А135 предусмотрено автоматическое включение движения подачи после быстрого подвода режущего инструмента к обрабатываемой детали и автоматическое выключение подачи при достижении заданной глубины сверления. Заданная глубина сверления несквозных отверстий обеспечивается специальным механизмом останова с упором. Этот механизм является одновременно предохранительным устройством, предохраняющим механизм подач от поломок при перегрузках. Шпиндель станка смонтирован на прецизионных подшипниках качения. Нижняя опора состоит из радиального шарикового подшипника класса АВ. В верхней опоре установлен один шариковый подшипник класса В. Заводом предусмотрена возможность смены приводных шкивов клиноременной передачи, что позволяет устанавливать пределы чисел оборотов шпинделя в соответствии с технологическими задачами. Для сокращения вспомогательного времени на станке модели 2А135 обеспечена возможность включения и выключения подачи тем же штурвалом, который осуществляет ручное быстрое перемещение шпинделя. Модели вертикально-сверлильных станков. На машиностроительных заводах получили распространение следующие модели вертикально-сверлильных станков: 2118, 2118А, 2Б118 для сверления отверстий в мягкой стали диаметром до 18 мм; 2125 и 2А125 для сверления отверстий диаметром до 25 мм; 2135, 2А135 для сверления отверстий диаметром до 35 мм; 2150, 2А150 и 2170 для сверления отверстий диаметром соответственно до 50 и 70 мм. Выпущен станок модели 2Н135А.
Кинематика станка модели 2AI35
Движение резания. Шпиндель V (рис. 8) приводится в движение электродвигателем мощностью 4,5 кВт через клиноременную передачу 140 --178 и коробку скоростей.
На валу I коробки скоростей находится тройной подвижной блок шестерен Б1 , обеспечивающий валу II три скорости вращения. От вала II через шестерни 34--48 вращение передается валу III, на котором расположен тройной подвижной блок шестерен Б2 , приводящий в движение полый вал IV, связанный шлицевым соединением со шпинделем V. Как видно из графика (рис.8), шпиндель V имеет девять скоростей вращения. Наибольшее число оборотов шпинделя nmax с учетом упругого скольжения ремня определяется из выражения Движение подачи. Движение подачи заимствуется от шпинделя V.
Движение передается через шестерни 27 --50 и 27 --50, коробку подач с выдвижными шпонками, предохранительную муфту М1 вал IX, червячную передачу 1--47, зубчатую муфту М2 , вал X и реечную передачу гильзе шпинделя. В коробке подач расположены трех - и четырехступенчатый механизмы с выдвижными шпонками. От вала VI три скорости вращения сообщаются валу VII, на котором жестко закреплены шестерни 60, 56, 51, 35 и 21. От вала VII четыре скорости вращения передаются валу VIII. Теоретически коробка подач обеспечивает 12 скоростей вращения, однако, как видно из графика), одна из них повторяющаяся, поэтому станок модели 2А135 имеет только 11 различных величин подач.
От вала VIII через кулачковую муфту М1 движение сообщается валу IX, на котором закреплен червяк. Червячное колесо 47 расположено на одном валу с реечной шестерней 14, находящейся в зацеплении с рейкой, нарезанной на гильзе шпинделя. Муфта М1 служит для предохранения механизма подач от поломок при перегрузках, а также для автоматического выключения подачи при работе по упорам.
Наибольшая величина подачи smax определяется из выражения Вспомогательные движения. Перемещение шпиндельной бабки осуществляется от рукоятки Р1 через червячную передачу 1--32 и реечную шестерню 18,сцепляющуюся с рейкой т = 2 мм, закрепленной на станине. Вертикальное перемещение стола достигается поворотом рукоятки Р2 через вал XI, конические шестерни 16--43 и ходовой винт XII. Быстрое перемещение шпинделя с гильзой производится штурвалом Ш, связанным специальным замком с валом X. Замок позволяет штурвалу свободно поворачиваться на валу X в пределах 20°, а в дальнейшем связывает их в одно целое.
Спиральное сверло
Сверла - это осевые режущие инструменты, предназначенные для образования отверстий в сплошном материале, а также для обработки (рассверливания) отверстий, предварительно изготовленных ковкой, штамповкой, литьем или сверлением. Они широко применяются в машиностроении, занимая по этому признаку второе место после резцов. Кинематика процесса сверления состоит из двух движений: главного - вращательного вокруг оси инструмента (заготовки), поступательного - движения подачи вдоль той же оси. По конструктивному исполнению сверла отличаются большим разнообразием, которое можно свести к следующим основным типам: перовые (лопаточные); спиральные (с винтовыми канавками); специальные (для сверления глубоких отверстий, кольцевые, комбинированные и др.). В качестве материала рабочей части в основном используются быстрорежущие стали и прежде всего сталь марки Р6М5. В последние годы в нашей стране и особенно за рубежом в больших объемах выпускаются различные конструкции сверл, оснащенных твердыми сплавами. Спиральные или, правильнее, винтовые, сверла были впервые показаны на Всемирной торговой выставке в 1867 г. американской фирмой Морзе. До настоящего времени основные особенности их конструкции сохранились практически неизменными. Из всех известных конструкций сверл спиральные сверла нашли наибольшее применение благодаря следующим достоинствам:
- 1) хорошему отводу стружки из обрабатываемого отверстия из-за наличия винтовых канавок; 2) положительным передним углам на большей длине главных режущих кромок; 3) большому запасу на переточку, которая производится по задним поверхностям и может выполняться вручную или на специальных заточных станках, в том числе станках-автоматах; 4) хорошему направлению сверла в отверстии из-за наличия калибрующих ленточек на наружной поверхности калибрующей части инструмента.
Основные конструктивные элементы и геометрические параметры спиральных сверл. На конической режущей части с углом 2. при вершине расположены две главные режущие кромки - линии пересечения винтовых передних и задних поверхностей. Форма задних поверхностей определяется методом заточки. В результате пересечения двух задних поверхностей образуется поперечная режущая кромка, наклоненная к главной режущей кромке под углом. Эта кромка располагается на сердцевине сверла с условным диаметром d0 =(0,15...0,25)d, где d - диаметр сверла. Две вспомогательные режущие кромки лежат на пересечении передних поверхностей и цилиндрических калибрующих ленточек, направляющих сверло в отверстии и образующих калибрующую часть сверла. Угол наклона вспомогательных кромок к оси сверла? определяет в основном величину передних углов. на главных режущих кромках, которые, как будет показано ниже, переменны по величине в разных точках этих кромок. Режущая и калибрующая части сверла составляют его рабочую часть, по длине которой сверла делятся на короткую, среднюю и длинную серии. Стандартные спиральные сверла изготавливают диаметром 0,1...80 мм с допусками по А8...А9. За рабочей частью стерла следует шейка, которая используется для нанесения маркировки сверла: диаметра, материала режущей части, товарного знака завода-изготовителя. Хвостовики бывают двух типов: конические с лапкой на конце для сверл d = 6...80 мм и цилиндрические для сверл d=0,1...20 мм. У сверл d > 8 мм хвостовики делают из конструкционной стали 45 или 40Х, свариваемой с рабочей частью. Для увеличения силы трения в месте крепления сверла в патроне и возможности правки сверл по длине хвостовики термически не обрабатывают. Лапки сверл для упрочнения закаливают, так как они используются для выбивания сверл из отверстия шпинделя станка или из переходной втулки. Геометрические параметры спиральных сверл. Спиральные сверла имеют сложную геометрию режущей части, что объясняется наличием большого числа кромок и сложных по конфигурации передних и задних поверхностей. Угол при вершине 2 , который играет роль главного угла в плане. У стандартных сверл 2 = 116... 120° . При этом главные режущие кромки строго прямолинейны и совпадают с линейчатой образующей винтовой передней поверхности. При заточке сверл угол заточки может быть изменен в пределах от 70° до 135°. При этом режущие кромки становятся криволинейными, меняются соотношение ширины и толщины срезаемой стружки и величины передних углов на главных режущих кромках. Соответственно меняются степень деформации срезаемого припуска, силы и температура резания и условия отвода стружки. Задний угол на главных режущих кромках создается путем заточки перьев сверл по задним поверхностям, которые могут быть оформлены как части плоской, конической или винтовой поверхностей.
НАЗНАЧЕНИЕ РЕЖИМА РЕЗАНИЯ ПРИ СВЕРЛЕНИИ
Исходные данные
В качестве детали, в которой сверлением необходимо получить три сквозных вертикальных отверстия диаметром М8 (l = 18 мм) на станке 2А135, выбираем ступицу из стали 20Х (в = 580 Мпа), чертеж которой представлен Порядок назначения
1. Выбор станка
Выбираем станок модели 2А135
2. Выбор инструмента
Сверло 6,4 ГОСТ 10903 - 77
3. Определение глубины резания t
Где D - диаметр отверстия;
4. Выбор подачи S
По [1, табл. 1] выбираем диапазон подач? S = 0,15 - 0,2 мм/об.
По [1, табл. 2 - табл. 5] находим K, , ,
Тогда
Скорректируем диапазон подач:
Мм/об
По паспортным данным станка 2А135 для данного диапазона подач находим подачу S=0,13 мм/об.
5. Определяем теоретическую скорость резания
По табл. определяем:
По табл. 6 находим T=25 мин, а по [1, табл. 7 - табл. 10] выбираем:
Тогда, а
М/мин
6. Определяем теоретическую частоту вращения шпинделя станка
Об/мин
7. Определяем действительную частоту вращения шпинделя станка
Согласно паспортным данным станка 2А135
Об/мин
8. Определяем действительную скорость резания и сравниваем ее с расчетной
М/мин
Расхождение между и составляет 4,4%, т. е. станок по скоростным параметрам выбран правильно.
- 9. Проверяем выбранный режим резания А) Проверка по мощности
По [1, табл. 12] находим: а по [1,табл. 13]
Тогда
Кг*м, и
По [1, прил.1] , поэтому
Т. е проверка по мощности выполняется ()
Б) Проверка по осевой силе
По [1, табл.12] находим а по [1, табл.13] определяем
Тогда кг
По [1, прил.1] находим Q=1600 кг, т. е. проверка по осевой силе тоже выполняется ().
Таким образом, данный режим резания назначен правильно.
10. Определяем основное технологическое время T мин
Похожие статьи
-
Горизонтально-расточной станок 2А620Ф2 - Металлорежущие станки и инструменты
Технологические возможности станка Станок предназначен для консольной обработки крупных заготовок с точными отверстиями, оси которых связаны между собой...
-
Токарно-револьверный одношпиндерный прутковый 1Б140 - Металлорежущие станки и инструменты
На рис. 1.1 приведен автомат токарно-револьверный одношпиндерный прутковый 1Б140 Рис.1.1 Автомат токарно-револьверный одношпиндерный прутковый 1Б140...
-
Введение - Металлорежущие станки и инструменты
Шпиндельный режущий станок сверлильный Вся история техники представляет собой борьбу за постепенное освобождение человека от непосредственного участия в...
-
Выбор оборудования Выбираю вертикально сверлильный станок модели 2Н135. Станок предназначен для сверления, рассверливания, зенкерования, развертывания...
-
Назначение и классификация сверлильных станков - Сверлильные станки
В зависимости от области применения различают универсальные и специальные сверлильные станки. Находят широкое применение и специализированные сверлильные...
-
Настольный сверлильный станок 2М112 (2М-112) - Сверлильные станки
Сверлильный станок 2М112 предназначен для сверления отверстий в деталях из черных и цветных металлов, а также других материалов, диаметром не более 12...
-
Долбежные станки - Исследование рычажного механизма долбежного станка
В данной курсовой работе представлен рычажный механизм долбежного станка. Долбежные станки предназначены для строгания вертикальных плоскостей, канавок,...
-
В условиях массового производства повышение производительности труда достигается автоматизацией технологических процессов, внедрением в производство...
-
При обработке жаропрочных, коррозионностойких сталей показатели упрочнения достаточно высоки, что требует приложения значительных сил. Кроме того, они...
-
Приспособление служит для сверления радиальных отверстий, фрезерования пазов и выполнения других фрезерных операций. Ось шпинделя расположена...
-
Системы автоматического управления точностью обработки деталей Обработка заготовок на станках с ПУ обеспечивает высокую степень автоматизации и широкую...
-
Нам дана кинематическая схема зубофрезерного станка, работающего по методу обката (деления) червячной фрезы. Рис. 1. Кинематическая схема зубофрезерного...
-
Введение, Харктеристика сверлильных станков - Сверлильные станки
Целью данной работы является рассмотрение характеристики группы сверлильных станков. Задачи работы: 1. рассмотреть характеристику сверлильных станков,...
-
Дефектация деталей узла и используемый инструмент - Ремонт токарного станка
Дефектная ведомость является документом, обосновывающим метод и трудоемкость ремонта узла. Она составляется (для дипломных работ) на 10-12 деталей,...
-
По общности технологического метода обработки различают станки: токарные, фрезерные, сверлильные и др. По назначению различают станки:...
-
При обработке на металлорежущих станках очертания, форма деталей (производящие линии) образуется в результате согласованных между собой вращательных и...
-
Порядок выполнения заданной детали. Обработка заготовки на токарно-винторезном станке (черновая) I-центра; II-заготовка; III - резец черновой токарный...
-
Несмотря на высокие качества современных токарных станков, совершенство методов обработки, точность применяемых измерительных инструментов и наличие...
-
Расчет режимов резания - Ремонт токарного станка
Операция 010. Токарная. Переход 1. Обточить поверхность Ш30+0,35 на длину 155 мм за 3 прохода. Рис. Схема установки заготовки при обработке поверхности...
-
Система питания. Источник питания - трехфазная сеть переменного тока, напряжением 380* 10%, частотой 50 Гц. Напряжение вторичных источников: А)...
-
Глубина резания при сверлении, мм: t =0,5-D, [4, с. 276] Где D - диаметр отверстия, мм. Глубина резания при зенковании, мм: t=0,5-(D-d); t2=0,5-9=4,5 мм....
-
Перечень составных частей станка приведен в таблице 2.2. Таблица 2.2 - Перечень составных частей станка Наименование Обозначение Кол Примечание Станина...
-
Оборудование и инструмент - Технология литейного производства
Оборудование. Для обработки дерева применяют циркулярные и ленточные пилы, станки: фуговальные, рейсмусовые, фрезерные, шлифовальные, шипорезные....
-
ВЫБОР ОПТИМАЛЬНОГО ВАРИАНТА КОРОБКИ СКОРОСТЕЙ Выбор оптимального варианта коробки скоростей очень сложен. Здесь большое значение имеют группы и типы...
-
ВВЕДЕНИЕ - Проектирование коробки скоростей токарного станка
Машиностроение является основой научно - технического прогресса в различных отраслях народного хозяйства. Непрерывное совершенствование и развитие...
-
Устройства для загрузки на станке - Виды автоматизированных производств
При обработке на станках-автоматах штучных заготовок их загрузку и выгрузку выполняют с помощью бункерных или магазинных механизмов питания,...
-
Устройства для автоматической смены инструмента - Виды автоматизированных производств
Особенность многоцелевых станков с ЧПУ -- наличие устройств автоматической смены инструментов, основное назначение которых -- сокращение времени простоя...
-
Маршрутная технология процесса изготовления деталей - Ремонт токарного станка
Выбор заготовки: при выборе заготовки для механической обработки заменяемой детали нужно учитывать технические требования, предъявляемые к детали....
-
Расчетно-пояснительная записка, Назначение станка. Описание - Долбежные станки
Назначение станка. Описание Долбежные станки предназначены для обработки плоских и фасонных поверхностей, шпоночных пазов, канавок в цилиндрических и...
-
Испытание и сдача оборудования в эксплуатацию, Обкатка оборудования - Ремонт токарного станка
Обкатка оборудования Отремонтированное и отрегулированное оборудование подлежит испытанию в целях уточнения годности его для дальнейшей эксплуатации....
-
Контроль качества ремонта и методы испытания - Деревообрабатывающие станки и их эксплуатация
Качество капитального ремонта оценивается по факторам, характеризующим ремонт и определяющим качество отремонтированного оборудования. К факторам,...
-
Краткая характеристика работ на копировально-фрезерных станках, Резцы-фрезы - Машинное гравирование
Копировально-фрезерный станок предназначен для выполнения копировальных работ на плоскости и по объему с использованием соответствующих копиров и...
-
Металлообрабатывающий инструмент - Инструментальные товары
Этот инструмент подразделяют на инструмент для опиловки, рубки и пробивки отверстий, сверления, нарезания резьбы, резки металла, а также ударный и...
-
Система смазки консоли включает в себя плунжерный насос золотниковый распределитель, маслораспределитель и отходящие от него трубки, подающие масло к...
-
СВЕРЛЕНИЕ - Операции ручного изготовления ювелирных украшений
Процесс образования отверстия в сплошном материале при помощи режущего инструмента -- сверла -- называется сверлением. Процесс увеличения при помощи...
-
Введение - Деревообрабатывающие станки и их эксплуатация
Деревообрабатывающие станки и их эксплуатация Деревообрабатывающий станок -- рабочая машина, на которой изготовляют детали и обрабатывают изделия из...
-
Режущие инструменты выбраны для каждого перехода, предусмотренного в маршруте обработки детали. В соответствии с методикой изложенной в [13]. Результаты...
-
Работать нужно заточенным инструментом. Ручки инструмента не должны быть расколоты, иметь задирав и заусенец. Хранить инструмент нужно в специально...
-
Кинематическая схема долбежного станка - Долбежные станки
На рис. 3 приведена кинематическая схема долбежного станка. Привод главного движения долбяка Долбяк приводится в движение от электродвигателя в следующей...
-
Монтаж оборудования - Ремонт токарного станка
Легкие и средние металлорежущие станки поступают на монтажную площадку в собранном виде или с несколькими узлами, снятыми из-за их габаритности, поэтому...
Вертикально-сверлильный станок 2А135 - Металлорежущие станки и инструменты