Установки плазменной резки и сварки металлов - Электротехнологические плазменные установки
Плазменная резка осуществляется путем выплавления и испарения металла в полости реза за счет энергии, выделяющейся в опорном пятне дуги и вносимой струей плазмы Энергетический баланс резки складывается из энергии дуги, химических реакций плазмы с металлом (если они возможны) и расхода энергии на расплавление, перегрев, испарение металла в полости реза, теплопередачу в твердый металл и унос с отработавшим потоком плазмы.
Отсюда следует, что процесс плазменной резки необходимо вести с максимальной мощностью и максимальной скоростью, обеспечиваемой вспомогательными операциями и применением ЭВМ. Это условие выполняется при выборе тока, напряжения, плазмообразующего газа и конструкции режущего плазмотрона. Ширина реза, определяющая экономичность процесса, связана с диаметром сопла плазмотрона, током дуги и скоростью перемещения плазмотрона.
При оптимальном соотношении между толщиной металла, мощностью дуги, диаметром сопла и скоростью резки струя плазмы погружается на всю толщину металла, а анодная область дуги располагается вблизи нижней кромки реза. Уменьшение мощности дуги, равно как и увеличение скорости продвижения плазмотрона, ведет к сужению полости реза.
Чрезмерное увеличение мощности и снижение скорости движения плазмотрона приводит к увеличению ширины реза, особенно в нижней его части, и перегреву всего разрезаемого металла. Коэффициент полезного действия плазменной резки возрастает с повышением мощности дуги и скорости движения плазмотрона, достигая 80-90 %, тепловой КПД принимают равным 40 %. Для увеличения мощности струи плазмы в пределах заданного тока дуги целесообразно принимать меры по повышению линейного градиента потенциала столба дуги применением высокоэнтальпийных плазмообразующих газов (азота, водорода, воздуха, углекислого газа, паров воды и др.) и интенсивным сжатием столба дуги соплом плазмотрона.
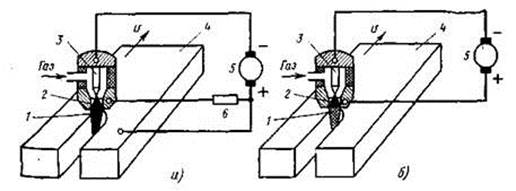
Рис. 8. Схема резки металла плазменной дугой (а) и плазменной струей (б): 1 - струя плазмы; 2 - дуга; 3 - катод; 4 - разрезаемый материал; 5 - источник питания; 6 - сопротивление, ограничивающее ток дежурной дуги
Режущий плазмотрон (рис. 8) с газовой стабилизацией дуги имеет стержневой вольфрамовый (или циркониевый) электрод 3, соосно расположенный в полости сопла 2. Стабилизирующий газ подается между ними и обеспечивает проникновение плазмы в глубину металла. При включении установки существует такая последовательность операций: включается подача воды, охлаждающей сопло и электрод, устанавливается необходимый расход газа; поджигается дежурная дуга, ток которой ограничивается сопротивлением 6, и возникает факел плазмы. При касании дежурным факелом кромки металла возникает цепь силовой плазменной дуги и начинается интенсивный процесс резки. При случайных погасаниях режущей дуги дежурная дуга восстанавливает процесс. При резке металла малых толщин применяется плазменная струй без включения металла в цепь тока (рис. 8, б).
Промышленные установки разных типов работают на токах до 1000 А при напряжении холостого хода до 350 В, обеспечивая скорость резки от 3-4 до 10 м/мин.
Наряду с мощными плазмотронами для автоматизированной машинной резки применяется плазморежущая аппаратура для переносных машин и ручной резки. Плазмотроны этих установок имеют низкое (до 180 В) напряжение холостого хода источника питания, ток - до 400 А.
Плазмотроны, выполняемые по схеме (рис. 8, а), являющейся основной при плазменной резке, рассчитывают на рабочий ток, а напряжение дуги формируется в полости реза. Вследствие этого вольт-амперные характеристики дуги здесь падающие, а источники питания имеют вертикальные или крутопадающие внешние ВАХ.
Высокая мощность плазмотрона и динамическое воздействие плазмы позволяют сваривать металлы разных толщин без подачи присадочной проволоки в сварочный шов, заваривать отогнутые кромки состыкованных деталей, сваривать детали без разделки кромок, осуществлять сварку металла большой толщины за один проход.
Применение вторичного фокусирующего газового потока, направленного под углом к оси плазмотрона, позволяет сконцентрировать нагрев на малой площади сварочной ванны. Применяемые газы обеспечивают защиту сварочного шва от воздействия атмосферы.
В зависимости от рода свариваемого металла применяют аргон, смеси аргона с гелием или водородом.
В состав установки входит источник питания, представляющий собой трехфазный двух полупериодный выпрямитель с регулируемым значением сварочного тока и крутопадающей ВАХ; высокочастотный генератор - осциллятор, служащий для возбуждения дежурной дуги между внутренним соплом и электродом в потоке аргона. Ток дежурной дуги ограничивается сопротивлением R, а емкость С служит для облегчения пробоя напряжением высокой частоты межэлектродного промежутка. Для начала процесса сварки необходимо коснуться свариваемого изделия светящейся частью струи плазмы. Тогда по цепи потечет сварочный ток, разогревающий металл в точке воздействия плазмы и образующий сварочную ванну, если бы в плазменную горелку подавался только один газ, как это делалось ранее то помимо чрезмерно большого расхода аргона технологические свойства плазменной дуги были бы недостаточны для выполнения качественной сварки. Столб дуги, окруженный потоками холодного газа, имеет возможность самопроизвольно перемещаться по поверхности сварочной ванны.
Для более четкого ориентирования плазмы в точку сварки и улучшения проникновения столба дуги в глубину сварочного шва с одновременным уменьшением расхода аргона применяются плазменные горелки. Здесь помимо аргона, подаваемого для зажигания дежурной дуги и образования плазмы, подается фокусирующий менее дефицитный газ2, производящий сжатие и фокусировку плазменной струи. При этом значительно повышается температура плазмы, что благоприятно влияет на процесс сварки. Защитный газ3предотвращает возможность попадания в зону сварки вредных компонентов из окружающей среды. Размеры электродов зависят от тока дуги и расхода газов, а расстояние между горелкой и деталью выбирают в пределах 80-15 мм из условия формирования качественного сварочного шва.
В цепях включения источника питания имеется блокировка, не позволяющая включить плазмотрон без подачи охлаждающей воды и газов.
Источники питания обеспечивают сварочный ток до 450-600 А при напряжении дуги 60-80 В и скорость сварки, например алюминиевого сплава толщиной 4 мм при токе 250 А и расходе плазмообразующего газа 5 л/мин, равную 70 м/ч.
В институте электросварки им. Е. О. Патона АН УССР разработан способ и создана аппаратура микроплазменной сварки на постоянном токе 0,5-10 А деталей из нержавеющей стали, меди, титана, никеля толщиной 0,2-0,6 мм.
Похожие статьи
-
Сварка и резка плазменной струей - Виды сварки и способы их применения
Сущность способа. Плазма -- ионизированный газ, содержащий электрически заряженные частицы и способный проводить ток. Ионизация газа происходит при его...
-
К энергетическим характеристикам плазмотрона относятся зависимости параметров дуги от условий работы - рода плазмообразующего газа, давления,...
-
Плазменные плавильные установки - Электротехнологические плазменные установки
Существует два основных направления использования плазмы в металлургии: 1) интенсификация известных процессов плавки с помощью плазменного подогрева или...
-
Плазменная технология - молодая отрасль промышленности, интенсивное ее развитие началось в 50-х годах нашего столетия и бурно продолжается в разных...
-
Аргон имеет низкое значение энтальпии, что делает его малопригодным для использования в качестве однокомпонентной плазмообразующей среды. Высокая...
-
Плазменная сварка - Сварочное производство. Сварка плавлением
Плазменная струя, применяемая для сварки, представляет собой направленный поток частиц или полностью ионизированного газа, имеющего температуру...
-
Введение - Электротехнологические плазменные установки
Установки, в которых происходит превращение электрической энергии в другие виды с одновременным осуществлением технологических процессов, называют...
-
Сварка плавлением - Процессы сварки металлов плавлением
Сварка плавлением осуществляется нагревом свариваемых кромок до температуры плавления без сдавливания свариваемых деталей. При нагреве с повышением...
-
Для изготовления передней рамы фронтального погрузчика МоАЗ 40484 применяется механизированная сварка, для сварки в защитном газе плавящимся проволочным...
-
Ионизация газов. Понятие плазмы - Электротехнологические плазменные установки
В обычных условиях различные газы и их смеси (воздух, аргон, водород, гелий, углекислый газ и др.) не проводят электрический ток. Проводимость возникает...
-
Подготовка металла к сварке Подготовка металла под сварку заключается в очистке, правке, разметке, резке и сборке под сварку. Разделка кромок в моем узле...
-
Неполный отжиг, Лазерная резка металла - Механическая обработка металлов
Неполный отжиг доэвтектоидной стали проводят при нагреве до температур выше Ас1 , но ниже Ас3 . При таких температурах происходит частичная...
-
РЕЗКА НЕРЖАВЕЮЩИХ СТАЛЕЙ, ГАЗО-ДУГОВАЯ РЕЗКА - Газовая резка нержавеющей стали
Применяют следующие виды резки нержавеющей стали: дуговую электрическую: газо-дуговую, кислородно-флюсовую и газоэлектрическую. В данном реферате...
-
Технология полуавтоматической сварки - Электрическая дуговая сварка на полуавтоматах
При электродуговой полуавтоматической сварке используют защитные газы. В качестве защитных используются активные газы, т. е. такие, которые могут...
-
В проектируемом варианте при производстве передней рамы фронтального погрузчика МоАЗ 40484 используется механизированная сварка. Режимы сварки плавящимся...
-
Выпрямитель многопостовой сварочный типа ВДМ, предназначен для питания сварочных постов электрической сварочной дугой, постоянным током при ручной...
-
Выбор режима ручной дуговой сварки часто сводится к определению диаметра электрода и сварочного тока. Скорость сварки и напряжение на дуге...
-
Схема резки металла на ножницах различных типов - Заготовительные операции
Резка и обработка кромок. Резка деталей с прямолинейными кромками из листов толщиной до 40 мм, как правило, производится на гильотинных ножницах...
-
Общие сведения о режиме сварки Режимом сварки называют основные показатели, определяющие процесс сварки, которые устанавливаются на основе исходных...
-
Ручная дуговая сварка металлическими электродами с покрытием Качество швов зависит не только от техники сварки, но и от других факторов, таких как состав...
-
Заготовительное производство в технологической цепочке изготовления продукции занимает важное место, поскольку решает вопросы повышения коэффициента...
-
Электрошлаковая сварка. - Сварочное производство. Сварка плавлением
Сущность процесса заключается в том, что тепловую энергию, необходимую для расплавления основного и присадочного металла, дает теплота, выделяемая в...
-
Техника газовой сварки - Технологии сварочного производства
Качество сварочного соединения зависит от правильного выбора режима и техники выполнения сварки. При ручной сварки пламя горелки направляют на...
-
Техника и режимы аргонодуговой сварки - Аргонодуговая сварка алюминия
Питание дуги осуществляется переменным током от источников с падающими внешними характеристиками. Перед тем как приступить к сварке, необходимо как можно...
-
Общие сведения о дефектах Дефекты в сварных соединениях могут быть вызваны плохим качеством сварочных материалов, неточной сборкой и подготовкой стыков...
-
Целью анализа литературы и патентов является поиск более перспективных и современных материалов, оборудования и других более совершенных изобретений для...
-
Наиболее широко используется при изготовлении всевозможных сварных конструкций. В зависимости от материала сварной конструкции, ее габаритов, толщины...
-
Лучевые способы сварки - Сварочное производство. Сварка плавлением
Электронно-лучевая сварка. Сущность процесса состоит в том, что свариваемые детали, собранные без зазора, помещают в вакуумную камеру и подают на них...
-
Техника сварки - Технология сварки трубных конструкций из низколегированной стали
Изделия чаще собирают на сварочных прихватках. Сварочные прихватки представляют собой неполноценные короткие швы с поперечным сечением до 1/3 сечения...
-
Выбор режима сварки - Технология сварки трубных конструкций из низколегированной стали
Режимом сварки называется группа показателей, определяющих характер протекания процесса сварки. Основными показателями режима сварки являются: диаметр...
-
Электрошлаковая сварка - Виды сварки и способы их применения
Этот способ широко используют в промышленности для соединения металлов повышенной толщины: стали и чугуна различного состава, меди, алюминия, титана и их...
-
Основные принципы ресурсосбережения в сварочном производстве основываются: - на эффективном использовании оборудования; (внедрении механизации и...
-
Сварка плавлением - Сварочное производство. Сварка плавлением
Дуговая сварка Источником теплоты является электрическая дуга, которая горит между электродом и заготовкой. Сварочной дугой называется мощный...
-
Технологические параметры процесса электрошлаковой сварки (ЭШС). - Электрошлаковая сварка
Сущность метода принудительного формирования состоит в искусственном охлаждении поверхности металлической ванны. Основное назначение шлаков при эшс -...
-
Введение - Технология сварки трубных конструкций из низколегированной стали
История развития сварочного производства В решение задач научно-технического прогресса важное место принадлежит сварке. Сварка является технологическим...
-
У - для сварки углеродистых сталей Д - с толстым покрытием Е - международное обозначение плавящегося покрытого электрода 51 - предел прочности на...
-
Введение - Сварка вертикальных швов стенки резервуара для хранения нефтепродуктов
Ведущее место в машиностроении занимает сварочное производство. Многие узлы и детали, входящие в состав изготавливаемых изделий, машин и оборудования и...
-
Электробезопасность - Сварка вертикальных швов стенки резервуара для хранения нефтепродуктов
Все электрооборудование сварочных участков должно соответствовать "правилам устройства электроустановок и действующим ГОСТам: ГОСТ 12.2.007-75, ГОСТ...
-
Анализ опасных и вредных производственных факторов на рабочем месте При выполнении сварки, наплавки металлов на рабочих могут воздействовать вредные и...
-
Выбор стандартного оборудования Автомат тракторного типа АДГ-602 ГОСТ 8213-75 Автомат предназначен для дуговой сварки протяженных швов в нижнем положении...
Установки плазменной резки и сварки металлов - Электротехнологические плазменные установки