Технологическое оборудование - Мельница производительностью 150 т/сутки
Расположение оборудования по этажам
В размольном отделении расположено следующее технологическое оборудование.
На седьмом этаже расположены вальцовые станки А1-БЗН, весы ДН-50, головки норий.
На шестом этаже расположены вальцовые станки А1-БЗН.
На пятом этаже расположены деташеры А1-БДГ, компрессоры ЗАФ-49, фильтры-циклоны типа РЦИ, рассевы Р3-БРБ.
На четвертом этаже расположены ситовеечные машины А1-БСО, бичевые машины МБО-1.
На третьем этаже расположены вальцовые станки А1-БЗН, весы ДН-20, фильтры-циклоны типа РЦИ.
На втором этаже расположены компрессоры ЗАФ-49, рассевы Р3-БРБ, бичевые машины МБО-1.
На первом этаже расположены компрессоры ЗАФ-57, два винтовых конвейера Р3-БКШ-200, башмаки норий.
Принцип работы основного технологического оборудования
Шестиприемный рассев РЗ-БРБ (рисунок 1) представляет собой сборную конструкцию шкафного типа и состоит из следу ющих основных узлов: корпуса, приемных и выпускных устройств, балансирного механизма с приводом.
Корпус 10 шестиприемного рассева конструктивно объединяет все основные его узлы. Он представляет собой стальную несущую конструкцию, в которой смонтированы два каркаса с тремя секциями в каждом. Между каркасами в центральной секции 13 корпуса установлен балансирный механизм. Корпус состоит из основания 12, крышки 15 и вертикальных стенок. Центральная секция корпуса закрыта панелью, в которой имеется съемная крышка 14 для доступа к балансирному механизму. Панель крепится к основанию, крышке и стенкам корпуса болтами. Основные элементы корпуса соединены между собой с помощью кронштейнов и скреплены болтовыми соединениями. Все угловые соединения закрыты кожухами. Пыленепроницаемость соединений корпуса обеспечивается установкой войлочных прокладок и уплотнительной замазкой.
К внешним стенкам крепятся кронштейны для зажима четырех пакетов гибких подвесок 7, по восемь прутьев из морского камыша или стекловолокна. Корпус рассева подвешивают к потолочной раме 4. Каркас рассева представляет собой неразборную деревянную конструкцию с левым и правым исполнениями. Каждый каркас состоит из четырех вертикальных стенок, образующих остов трех секций. С обеих торцевых сторон стенок закреплены кронштейны для дверей.
В каждой секции к вертикальным брусьям с одинаковым шагом прикреплены шурупами направляющие уголки для ситовых рамок с поддонами. В зависимости от сочетания форм исполнения каркасов, лючков и заглушек в днище корпуса и приемных коробов в верхней части каждой секции корпус шестиприемного рассева имеет 12 модификаций.
Двери закрывают каждую секцию рассева с обеих сторон и выполняют важную технологическую функцию -- распределение фракций по ситам в соответствии со схемой их обработки. Каждая дверь состоит из корпуса 2 (рис. 53), панели 7, перепускных каналов 4, шарнирного кронштейна 10 и бугеля 9. Двери имеют различную высоту, причем укороченные по вертикали установлены со стороны приема, где стоят двух - или трех-приемные питающие короба 5, а с противоположной стороны секции высота корпуса соответствует высоте двери.
Каждая дверь шарнирно подвешена к каркасу рассева и запирается винтовыми замками. Корпус двери скреплен с панелью болтами и бугелями. Бугели выполняют не только крепежные функции. В них устанавливаются ключи-ручки для открывания и закрывания двери. В верхней и нижней частях панели имеются два штыря для установки двери в шарниры. Внутренние поверхности дверей и панели облицованы металлическим листом. Для обеспечения плотного прилегания к каркасу нижний торец двери оклеен кожей, а все поверхности, прилегающие к ситовым рамкам, -- войлоком.
Внутри корпуса двери установлены сменные лотки и заглушки, с помощью которых в дверях образуются перепускные каналы для передачи сходовых фракций с одних сит на другие по технологической схеме и вывода их из рассева. В соответствии с этим в корпусе дверей установлены различные типы съемных элементов: скобообразные или дугообразные лотки и горизонтальные или наклонные перекрытия -- заглушки. Лотки имеют различную форму и размеры, они выполнены из алюминиевого листа, на торцах которого установлен профиль из того же материала. В паз, образованный между лотком и профилем, вставлен уплотняющий материал. Заглушки имеют деревянную основу, к которой прикреплен алюминиевый лист, а с торцов -- уплотняющий материал. Сочетания панелей, корпусов, лотков и заглушек дают различные варианты исполнения дверей, которые соответствуют технологическим схемам и месту установки двери: со стороны приема или с противоположной стороны.
В каждой секции рассева установлены 22 ситовые рамки с поддонами. Рамка (рис. 1) представляет собой деревянный каркас 1, разделенный на три части. Размеры всех рамок одинаковы. Для повышения износостойкости внутренняя поверхность каркаса каждой секции рамки покрыта металлической лентой. Сверху к деревянному каркасу рамки металлическими скобками прикреплено сито 2, окаймленное по пepиметpy тесьмой. В рассевах для сепарирования всех продуктов, кроме муки, применяют металлотканые сита, а для высеивания муки - синтетические. Сита устанавливают в соответствии с технологической схемой. Кроме ситовых рамок, применяют рамку, закрытую металлическим листом, - непроходную. К нижней части рамок скобками крепится поддон из металлотканой сетки с фиксированными отверстиями размером Юл 10 мм. Для плотного прилегания рамки к направляющим шкафа на нижних продольных планках установлено уплотнение из плюша.
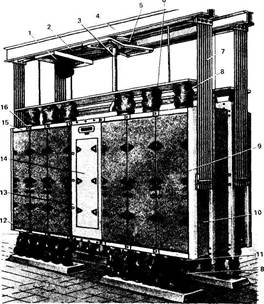
Рисунок 1 - Рассев РЗ-БРБ.
1 - Электродвигатель; 2 - Передача клиноременная; 3 - Вал; 4 - Рама потолочная; 5 - шкив; 6 - Доска приемная; 7 -- подвески гибкие; 8 -Рукава; 9 - секция рассева; 10 - корпус; 11 -- Патрубок выпускной; 12 - Основание корпуса; 13 - секция центральная; 14 - крышка съем-ная; 15 - крышка корпуса; 16 - Патрубок приемный.
Для очистки сит в каждую из трех секций рамки помещен инерционный очиститель 3. Он выполнен из прямоугольной текстильной пластины с металлической кнопкой в центре. Каждый очиститель движется по сетчатому поддону кнопкой вниз и очищает сито махровыми краями. По мере изнашивания площадь пластины постепенно уменьшается, очиститель округляется вокруг кнопки и подлежит замене.
На верхнюю часть каждой рамки устанавливают поддон для вышележащей рамки. Поддоны предназначены для сбора и транспортирования проходов сит на другие рамки в соответствии с технологической схемой. Поддон представляет собой металлическую конструкцию с пластмассовыми ограничителями. К верхней части ограничителей прикреплены уплотнения из плюша для плотного прилегания поддона к направляющим шкафа.
Все поддоны имеют одинаковые размеры, но в зависимости от места в схеме рассевы различаются по конструктивному исполнению, обеспечивая выход фракции на одну или две стороны. На каждом поддоне установлен пластмассовый инерционный побудитель для ускорения вывода проходового продукта.
По направляющим уголкам ситовая рамка вставляется внутрь шкафа вместе с установленным на ней поддоном. Вертикальные брусья каркаса рассева вместе с рамками и поддонами образуют в секциях шкафа вертикальные каналы для проходовых фракций. В зависимости от технологической схемы рассева эти каналы перекрыты по высоте съемными перекрышами.
Приемные устройства предназначены для подачи в рассев продуктов размола зерна. Приемники каждой секции монтируют на неподвижной металлической приемной доске, подвешенной к потолочной раме. На приемной доске установлены между двумя фланцами, скрепленными стержнями, прозрачные стаканы для визуального контроля наличия продукта. Стакан сверху и снизу прикрепляют к фланцам при помощи хомутов через войлочные прокладки. С нижней стороны приемной доски смонтирован стакан с конической воронкой внутри. На бортик стакана надевается матерчатый рукав, соединяющий приемное устройство с приемным патрубком корпуса рассева. Через коническую воронку продукт подается на дисковый распределитель с круглыми отверстиями, который установлен в каждой секции рассева.
Выпускные устройства представляют собой напольные поддоны с патрубками, закрепленными на них болтовыми соединениями. На каждый патрубок надет матерчатый рукав, соединяющий его со шкафом рассева. Для отбора контрольных образцов фракций на патрубках установлены съемные резиновые крышки. Количество выпускных патрубков соответствует технологической схеме рассева.
Концентратор А1-БЗК-18 (рисунок 2) состоит из следующих основных узлов: ситового корпуса, аспирационной камеры, приемных и выпускных устройств, привода и станины.
Ситовой корпус состоит из двух ситовых кузовов 13, соединенных между собой поперечными траверсами и стяжками. В каждом кузове установлен под небольшим углом к горизонтали один ситовой ярус, состоящий из двух ситовых рам 15, 16 с ситами с отверстиями 2 и 9 мм. Рамы вставляют в кузов по направляющим, установленным на ее боковых стенках, и зажимают упором и двумя подпружиненными поворотными рукоятками. Каждая ситовая рама состоит из деревянного остова, в верхней части которого укреплено рабочее сито, а в нижней -- сетчатый поддон. Сита очищаются резиновыми шариковыми очистителями, движущимися по поддону.
В нижней части боковых стенок кузова по всей его длине выполнены круглые отверстия, закрытые сеткой, для забора воздуха под сито. Сдвоенный ситовой корпус подвешен на четырех подвесках, угол наклона которых составляет 15 ±0,5° к вертикали. Этот угол определяет направление колебаний кузова. Пе-
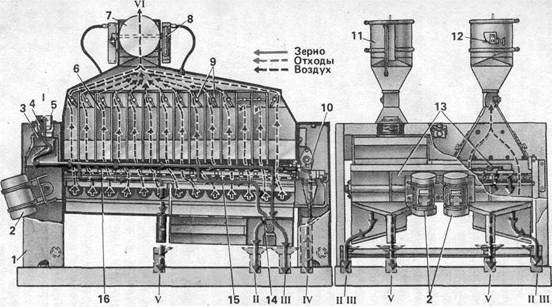
Рисунок 2 - Концентратор А1-БЗК-18.
1 - станина; 2 -- вибратор; 3 -- устройство приемное; 4 -- рукав; 5 -- патрубок приемный; 6 - камера аспирационная; 7-заслонка дроссельная; 8 - манометр; 9, 12-- регуляторы воздушного потока; 10 -- механизм винтовой; 11 -- патрубок аспи-рационный; 13 -- кузов ситовой; 14 - клапан поворотный; 15, 16 -- рамы ситовые; / --зерно исходное; II -- фракция зерна тяжелая; III - фракция зерна легкая; IV - примеси трудноотделимые легкие; V -- примеси мелкие; VI - воздух с легкими примесями.
Передние (со стороны приема) подвески отличаются от задних наличием цилиндрической пружины, удерживающей подвески и корпус в заданном положении.
Аспирационные камеры установлены неподвижно над каждым ситовым кузовом и укреплены к станине. Каждая камера разделена на 14 независимо регулируемых секций. Для этого в верхней части каждой секции установлен регулятор 9 настройки воздушного режима над каждым участком сита. Необходимое разрежение в концентраторе устанавливается дроссельными заслонками 7, установленными в аспирационных патрубках 11 с помощью регуляторов 12. Разрежение в каждой аспирационной камере контролируют манометром 8. Для наблюдения за работой концентратора и удобства регулирования воздушного режима боковые стенки аспирационных камер имеют смотровые окна, а рабочее пространство освещается светильником.
Приемное устройство 3 каждого кузова состоит из патрубка 5, соединительного гибкого рукава 4 и приемной коробки с клапаном, обеспечивающим равномерное распределение зерна по всей ширине сит. Приемное устройство с торцевой стороны машины закрыто прозрачной съемной дверкой.
Выпускные устройства выполнены раздельно для сходов и проходов. Сходовая фракция (отходы) выходит через регулируемую щель между двумя вертикальными планками, установленными под углом на сходовом конце сита и образующими сужение. Расстояние между планками регулируют винтовым механизмом 10 с рукояткой. Сходовая фракция выводится через выпускной патрубок, установленный в станине.
Мелкие примеси (проход) выводятся через выпускной патрубок в воронку самотечной трубы, а очищенное зерно поступает в сборник под второй ситовой рамой, где установлен поворотный клапан 14 для разделения зерна на две фракции по плотности.
Привод сдвоенного ситового корпуса осуществляется от двух электромеханических вибраторов 2, конструкция и установка которых аналогичны применяемым в камнеотделительных машинах типа РЗ-БКТ. Станина сборная сварной конструкции предназначена для размещения всех основных узлов концентратора.
Вымольная машина А1-БВГ предназначена для отделения частиц эндосперма от оболочек сходовых фракций драных систем при переработке зерна пшеницы в сортовую муку и применяется на мукомольных заводах с механическим и пневматическим транспортом.
Вымольная машина (рисунок 3) состоит из следующих основных узлов: корпуса, приемно-питающего устройства, бичевого ротора, ситового полуцилиндра, привода, выпускных устройств, подставки.
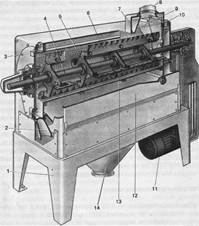
Рисунок 3 - Вымольная машина А1-БВГ.
1 - подставка; 2 - патрубок для вывода отрубей; 3 - корпус; 4 - вал; 5 - розетка; 6 - бич; 7 - камера приемная; 8 - патрубок приемный; 9 - клапаны спаренные; 10 - отверстия для аспирации; 11 - электро-двигатель; 12 - дверка; 13 - полуцилиндр ситовой; 14 - конус выпуск-ной для проходовой фракции.
В корпусе сварной конструкции установлены основные рабочие органы вымольной машины. На боковой стороне корпуса установлены съемные дверки 12, которые фиксируют ручными зажимами. Торцевые части корпуса закрыты крышками.
Приемно-питающее устройство состоит из приемного патрубка 8, выполненного в виде прозрачной смотровой вставки с двумя фланцами, и приемной камеры 7. В ней установлены спаренные клапаны 9, которые распределяют продукт по всей длине рабочей зоны. Положение клапанов указано на шкале, установленной на передней стенке приемной камеры.
Для обеспечения нормального технологического процесса и обеспыливания машины предусмотрено два варианта аспирации с верхним или нижним отсосом воздуха. Для организованного подвода воздуха в верхней части боковой стенки корпуса по всей его длине предусмотрено отверстие.
Технологический процесс в машине А1-БВГ осуществляется следующим образом. Продукт через приемный патрубок 8 поступает в приемную камеру 7 и затем в рабочую зону. Здесь вращающиеся бичи подхватывают продукт и отбрасывают его к поверхности цилиндрического сита. Частицы эндосперма отделяются от отрубей, просеиваются через сито и выводятся из машины через конус 14. Благодаря отогнутым гонкам и наклону бичей относительно оси вала сходовая фракция (отруби) продвигается в осевом направлении и выводится через выпускной патрубок.
Отличительные особенности вымольной машины А1-БВГ состоят в том, что ситовая часть выполнена в виде полуцилиндра; наклон бичей и гонков обеспечивает наряду с вращательным осевое движение продукта от приема к выходу; управление спаренными клапанами позволяет оперативно изменять время обработки исходного продукта и соответственно эффективность и производительность машины.
Деташер А1-БДГ предназначен для измельчения промежуточных продуктов после вальцовых станков 1-й, 2-й шлифовочных и 4...10-й размольных систем с микрошероховатой рабочей поверхностью вальцов.

Рисунок 4 - Деташер А1-БДГ.
1 - корпус; 2 - Патрубок приемный; 3 - боковина; 4 - электродвига-тель; 5 - дверка; 6 - Патрубок выпускной; 7-вал ротора; 8 - бич; 9-розетка.
Деташер (рисунок 4) состоит из следующих основных узлов: бичевого ротора, корпуса, приемных и выпускных патрубков, привода.
Бичевой ротор - основной рабочий орган деташера, выполнен в виде вала 7, на котором при помощи шпонок закреплены две розетки 9. На розетках жестко установлены четыре стальных бича 8. Каждый бич с рабочей стороны имеет 10 зубьев высотой 15 мм (два зуба из десяти прямые, восемь отогнуты под углом 16° в направлении движения продукта). Расстояние между зубьями 6 мм. Длина бича 380 мм, зазор (нерегулируемый) между бичами ротора и корпусом деташера составляет 4,8-5,6 мм. Ротор вращается в шарикоподшипниках.
Для приема и вывода продукта имеются патрубки 2, 6 диаметром 120 мм, к которым с помощью специальных хомутов с зажимами присоединяются подводящий и отводящий самотеки.
Технологический процесс обработки продукта в деташере осуществляется следующим образом. После вальцового станка продукт самотеком или через систему пневмотранспорта направляют через приемный патрубок 2 в рабочую зону. Здесь он подхватывается бичами 8 вращающегося ротора, отбрасывается к внутренней поверхности корпуса и постепенно перемещается к выпускному патрубку 6. Шесть приваренных к корпусу по всей его длине пластинок обеспечивают торможение продукта и усиливают его разрыхление. Под воздействием наклонных участков косозубых бичей продукт перемещается к выходу. На этом пути в результате многократных ударов и трения частиц о бичи и обечайку происходит разрушение агломератов частиц.
По данным испытаний, извлечение муки, полученной при измельчении продукта в вальцовом станке 1-й шлифовочной системы и деташерах А1-БДГ, составляет 14,0...14,5 %, зольность муки - около 0,44 %.
Ситовеечная машина А1-БС0 (рисунок 5) предназначена для обогащения промежуточных продуктов размола зерни. Она состоит из следующих основных узлов: ситового кузова, приемного и выпускных устройств, аспирационной камеры, привода с колебателем и станины.
Ситовой корпус состоит из двух параллельно работающих кузовов 11, жестко соединенных между собой кронштейнами с обеих торцевых сторон. Каждый кузов собран из листов алюминиевого сплава, соединенных между собой болтами. Сдвоенный ситовой корпус подвешен к станине на трех подвесках: со стороны приема -- на двух 3, а с противоположной стороны -- на одной 12 с пружиной, установленной посередине корпуса. Направление колебаний ситового корпуса регулируют изменением угла наклона подвесок к вертикали.
В каждом ситовом кузове размещены один над другим три ситовых яруса 6, установленные с различным углом наклона к горизонтали в пределах 1...1,5°. В каждом ярусе установлены четыре ситовые рамки. Сита на сходовом конце фиксируются зажимом 13. Поворотом подпружиненной ручки зажима на 90° до горизонтального положения ситовые рамки освобождаются от фиксации, и их можно вынуть из корпуса. При вертикальном положении ручек - рамки зажаты.
Сита очищаются инерционными щетками 3. В каждой ситовой рамке установлена одна щетка с двумя рядами пучков, волос которых направлен в противоположные стороны. В рабочем положении щетка одним рядом пучков упирается в сито и под действием сил инерции при колебаниях ситового корпуса может перемещаться только в сторону пучков, которые не касаются сита. Перемещению в обратную сторону препятствуют противоположно направленные пучки волоса, которые в данном цикле движения щетки очищают сито.
Технологический процесс обогащения осуществляется следующим образом. Исходный продукт поступает в приемное устройство каждого ситового кузова и равномерно распределяется по ширине ситовых рам верхнего яруса. Воздух засасывается из подситового пространства, пронизывает все три яруса сит, аэрирует продукт и поступает в аспирационную сеть. Совместное воздействие колебаний сит и восходящего потока воздуха обеспечивает самосортирование разнородных компонентов смеси и последовательное просеивание наиболее плотных частиц эндосперма через ситовые рамки верхнего, среднего и нижнего ярусов, т. е. проход вышележащей рамки просеивается на соответствующую нижележащую. Проходовые фракции поступают в корпус-сборник, а сходовые -- в камеру сходов, где формируются в соответствии с технологической схемой и выводятся из машины.

Рисунок 5 - Ситовеечная машина А1-БСО.
1 - электродвигатель; 2 - шкив с грузом; 3 - подвеска передняя; 4 - устройство приемное; 5 - патрубок приемный; 6 - ярусы ситовые; 7 - секция аспирационной камеры; 8 - диффузор вытяжной; 9 - камера аспирационная; 10 - щетка; 11 - кузов ситовой; 12 - подвеска задняя; 13 - зажим ситового яруса; 14 - камера сходов; 15 - клапан перекидной; 16 - патрубок выпускной для сходов; 17 - брусок-опора скольжения корпуса-сборника; 18 - патрубок выпускной для проходов; 19 - лоток наклонный; 20 - корпус-сборник; 21 - станина.
Характерная особенность ведения ситовеечного процесса заключается в получении трех сходов с каждой ситовеечной системы, причем верхний сход самой высокой зольности, а нижний - самой низкой. В результате обогащения крупо-дунстовых продуктов в ситовеечных машинах можно максимально получить с каждого ситового кузова по три сходовые фракции IV и четыре проходовые.
Отличительной особенностью ситовеечной машины является одноступенчатая последовательная трехъярусная схема обогащения круподунстовых продуктов, которая обеспечивает высокую эффективность процесса при больших удельных нагрузках. В результате эффективного обогащения ни одна фракция не возвращается после ситовеечной машины на повторное обогащение. Это сокращает протяженность ситовеечного процесса, значительно снижает оборот продукта и подсушивание его. Возможность регулирования направления колебаний ситового корпуса наряду с кинематическими параметрами является действенным фактором повышения эффективности и производительности машины. Конструкция инерционных очистителей способствует восстановлению живого сечения сит, они надежны в работе.
Похожие статьи
-
Схема переработки пшеницы в пшеничную крупу 1 - магнитная колонка; 2 - шелушильно - шлефовальная машина А1-ЗШН-3; 3 - аспиратор; 4 - вальцовый станок; 5...
-
Вместо обоечных машин на двух системах или только на второй можно применять шелушильно-шлифовальные машины типа ЗШН. После шелушильных систем количество...
-
В гомогенизаторах измельчение происходит в результате течения продукта под большим давлением через узкие кольцевые щели. Схемы конструкций...
-
Технологическая линия производства йогурта (Дополнение 1) состоит из следующего наименования оборудования: 1. Двухслойный резервуар 3000 л из пищевой...
-
Технологическое оборудование, применяемое при выполнении работы - Технология приготовления блюд
Машина МКП-60 используется в столовых, в горячих цехах для приготовления картофельного пюре. Эта машина состоит из электрокотла, КПЭ-60 и привода,...
-
Состояние вопроса - Основы технологического оборудования
Для приготовления моющего раствора (раствор CaCl2 0,7%) используется аппарат с механическим перемешивающим устройством. Основными элементами аппарата...
-
Технологическая схема подготовительного отделения при производстве пшеничной крупы Схема подготовки пшеницы к переработке в крупу 1 - автоматические...
-
Размольное отделение мельницы - Мельница производительностью 150 т/сутки
Технологическая схема размольного отделения приведена в Приложении Г. Схема размольного процесса мельницы состоит из четырех драных и семи размольных...
-
Характеристика предприятия, Крупозавод - Мельница производительностью 150 т/сутки
Крупозавод Крупозавод производительностью 25 т/сутки. На крупозаводе перерабатывают 3 вида сырья: горох, ячмень и пшеницу. Из гороха вырабатывают в...
-
Полтавскую крупу подразделяют на 4 номера: № 1 -- проход через сито с отверстиями 3,5 и сход -- 3,0 мм; № 2 --3.0 и 2,5 мм; № 3 -- 2,5 и 2,0 мм; № 4 --...
-
На предприятии ОАО "Серпуховхлеб", на линии для производства батона "Нарезной" используется следующее основное оборудование: тестомесильные машины,...
-
Гомогенизатор А1-ОГМ (рис. 2), предназначенный для получения тонкоизмельченного однородного продукта, состоит из электродвигателя 1, станины 2,...
-
При размещении оборудования руководствовались технологическими, техническими требованиями и регламентированными нормами. При выборе варианта компоновки...
-
Требования к технологическому оборудованию - Технология производства конфет марки "Буревестник"
Машины и аппараты для производства конфет "Буревестник" должны иметь высокие показатели, под которыми имеются в виду отдельные параметры, отнесенные к...
-
Подбор и определение потребного количества оборудования для подготовительного отделения крупяного завода Расчетная емкость буккеров для неочищенного...
-
Введение - Основы технологического оборудования
Гомогенизация раствор перемешивание дробление Перемешивание - это вспомогательный процесс, применяющийся в пищевой промышленности для приготовления...
-
Подбор и расчет вальцедековых станков и других шелушителей Общая длина волков вальцовых станков определяется по формуле(9): L= (9) Где L-длина вальцового...
-
Электрические печи, Печи сопротивления. - Технологическое оборудование литейных цехов
Печи сопротивления. Тигельные электропечи сопротивления используют для плавки алюминиевых сплавов, масса получаемого сплава до 250 кг. Эти печи применяют...
-
Генеральный план предприятия ЗАО "Союзмука" - Мельница производительностью 150 т/сутки
Территория ЗАО "Союзмука" расположена по адресу улица Звездная 15. Площадь территории 2,37 га, площадь зданий и сооружений 4920 м. Площадь проездов и...
-
Технологическое оборудование, правила т/б и эксплуатация - Мучные кондитерские изделия
Машина для просеивания муки МПМ-800 Правила эксплуатации. Перед началом работы проверяют санитарно-техническое состояние и наличие заземления. В рабочую...
-
Рабочие места поваров оснащены модулированным секционным тепловым оборудованием периодического действия. Рабочие места оснащены также модулированными...
-
Введение - Мельница производительностью 150 т/сутки
Объектом прохождения практики является мельница, расположенная на территории предприятии ЗАО "Союзмука". Кроме мельницы на территории располагается...
-
Тепловая обработка продуктов - основной процесс при приготовлении абсолютного большинства блюд. Наиболее востребованными "представителями" тепловых...
-
1) Надеть спецодежду. 2) Привести в порядок рабочее место, не заграждать проходы. 3) Подготовка продуктов. 4) Кулинарная обработка продуктов. 5)...
-
Просеиватель МПМ-800м Этот просеиватель предназначен для просеивания муки. Подвешенный мешок с мукой подается к загруженному бункеру, в который...
-
Описание процесса приготовления цементного клинкера в трубной шаровой мельнице Измельчение материалов в цементном производстве - один из технологических...
-
Выбор и обоснование выбора технологического оборудования - Приготовление горячего блюда "Гуляш"
Ножи. Будьте предельно осторожны в обращении с кухонными ножами! Не соблюдение правил использования кухонных ножей, является самой распространенной...
-
Введение - Технологическое оборудование предприятий молочной промышленности
Гомогенизацией называется механический процесс разделения частиц вещества на части с очень малыми размерами (100-200 мкм и меньше) частиц с целью...
-
Мельница, Зерноочистительное отделение мельницы - Мельница производительностью 150 т/сутки
Мельница производительностью 150 т/сутки (планы этажей и разрезы приведены в приложении А). На ней осуществляется сортовой помол. На мельнице...
-
К факторам сохраняющим качество продовольственных товаров, относятся тара и упаковочные материалы, условия и сроки транспортирования, хранения и...
-
В кафе "Калинка" используется специализированное оборудование для облегчения работы и ускорения процесса обработки продукта. Подбор оборудования...
-
Рассчитываем сменную производительность станка (линии) при выполнении соответствующих технологических операций. 1. Форматно-раскроечный станок Formula...
-
Для обработки деталей и узлов пальто используется высокопроизводительное оборудование, значительную часть которого составляют швейные машины в заданном...
-
Разработка теоретической схемы базирования Базирование - определение положения деталей сборочной единицы, относительно друг друга, либо сборочной единицы...
-
Технологический процесс должен осуществляться с соблюдением настоящей технологической инструкции, правил ветеринарно-санитарной экспертизы мяса и мясных...
-
Технологическая, Общие положения. - Оборудование участка железной дороги устройствами заграждения
Общие положения. При выполнении ремонтных работ по замене УЗ или его крупных узлов и деталей, при которых нарушается работа УЗП и дей-ствие автоматики на...
-
Классификация плавильных печей - Технологическое оборудование литейных цехов
По виду используемой для плавки сплавов энергии плавильные печи подразделяют на пламенные и электрические. Пламенные печи (рис.3) подразделяют на...
-
Т. к производство крупносерийное и деталь зубчатое колесо с большой разницей в диаметре, заготовку рационально получать штамповкой на...
-
Рассчитаем необходимое число единиц гипсоварочных котлов, согласно формуле: N=Pп/(Pч-K), Где Pп - требуемая часовая производительность предприятия; Pч -...
-
Расчет технологического оборудования - Детское кафе "Балапан"
Технологический расчет оборудования сводится к выбору типов и определению необходимого количества единиц оборудования для выполнения тех или иных...
Технологическое оборудование - Мельница производительностью 150 т/сутки