Полученные результаты и их обсуждение, ВЫДЕЛЕНИЕ И ОЧИСТКА НИЗКОМОЛЕКУЛЯРНОГО ПОЛИЭТИЛЕНА - Получение и изучение углеводородов из отходов Шуртанского газо-химического комплекса
ВЫДЕЛЕНИЕ И ОЧИСТКА НИЗКОМОЛЕКУЛЯРНОГО ПОЛИЭТИЛЕНА
Отход ШГХК, содержащий НМПЭ представляет собой суспензию светло желтого цвета с резким характерным запахом. При отстаивании происходит расслоение и появляется белый осадок, который представляет собой собственно НМПЭ.
Известно, что до последнего времени наибольшее применение при промышленном производстве полиэтилена низкого давления имела каталитическая система Циглера-Натта. Но технология использования этой системы сопровождается образованием значительного количества низкомолекулярных фракций - восков при сополимеризации этилена с другими б-олефинами, что ухудшает механические и теплофизические свойства сополимеров и увеличивает расход мономеров на единицу массы сополимера. Для удаления восков из сополимеров проводится отмывка их горячим растворителем с последующим отжимом. Образованная при этом жидкая фракцияудаляется. [1].Однако, в литературе не раскрыты конкретные технологические приемы - как именно указанная жидкая фракция являющаяся сопутствующим отходом производства по известной технологии удаляется, перерабатывается или утилизируется.
Тем не менее, указанный отход производства содержит низкомолекулярный полиэтилен и многокомпонентную смесь растворителей и его также необходимо подвергать переработке с целью получения полезных продуктов используемых в других производствах. При этом повышается КПД и доходность основной технологии.
Известен способ выделения компонентов из растворов полиолефинов в органических растворителях [14].Изобретение относится к способу выделения полиолефинов. Способ включает охлаждение раствора полиолефина в органических растворителях до комнатной температуры. Образовавшуюся парафиноподобную массу измельчают и смешивают с водой, полученную смесь нагревают до температуры не выше температуры плавления полимера в присутствии исходного органического растворителя. Выделение полимера проводят путем выдерживания этой смеси при остаточном давлении 15-40 мм рт. ст. до полной отгонки растворителя и последующей фильтрации полимера от оставшейся воды. После чего, его сушат. На стадии вакуумирования осуществляют конденсацию паров растворителя и воды при температуре - 5-0OС с последующим их разделением. Способ согласно изобретению позволяет удешевить, упростить и ускорить технологический процесс.
Присутствиенизкомолекулярного полиэтилена ( воска) в бензине не мешает определению. Типичная газовая хроматограмманизкомолекулярного полиэтилена, полученная при программируемом подъеме температуры колонки от ПО до 350 С со скоростью 10 С / мин.
При термической деструкции сравнительно низкомолекулярного полиэтилена в вакууме и в атмосфере азота при нормальном давлении обнаружено [3], что летучие продукты деструкции состоят из низкомолекулярных осколков полиэтиленовых макромолекул. При дальнейшем нагревании происходит более плавное снижение молекулярной массы полимера. При деструкции полиэтилена в атмосфере азота обнаружен рост ненасыщенности с увеличением степени его разложения, что может быть связано с лиспропор-ционированием более низкомолекулярных макрорадйкалов по концевым связям или переносом атомов водорода от двух соседних углеродных атомов главной цепи.
Однако известный способ характеризуется нерациональной организацией тепловых процессов: раствор полимера сначала охлаждают до комнатной температуры, затем после измельчения и смешения с водой образовавшеюся суспензию, масса которой в 3-4 раза превышает массу исходного раствора, нагревают до температуры, близкой к температуре плавления полимера. Кроме того, использование вакуумной перегонки, также усложняет процесс.
Наиболее близким по технической сущности и существенным признакам является способ выделения компонентов из раствора полиэтилена в органических растворителях, применяемый в производстве этого полимера при низком и среднем давлении, который предусматривает использование осадителей.[15]. Способ осуществляют, проводя следующие операции: раствор полиэтилена в органическом растворителе, образовавшийся в ходе процесса полимеризации, освобождают от катализатора и непрореагировавшего этилена; - охлаждают раствор до 30-35OС. Затем смешивают охлажденный раствор с жидкостью-осадителем, в качестве которой используют спирт, так как он неограниченно смешивается с растворителем и не взаимодействует с полимером. При этом образуется суспензия закристаллизовавшегося полиэтилена в смеси двух жидкостей. Полиэтилен выделяют, проводя следующие операции:фильтруют образовавшуюся суспензию;промывают осадок осадителем;сушат при 60-70OС;- разделяют жидкости, проводя:
Очистку смеси жидкости от низкомолекулярных фракций полиэтилена;ректифракцию жидкостей.
Однако известный способ также сложен из-за многостадийности и необходимости применения сложного и крупногабаритного оборудования.
Он неэкономичен, так как требует значительных количеств осадителя-спирта. Велика продолжительность процесса - не менее 2,5 ч. К тому же способ небезопасен с пожарной и экологической точек зрения вследствие выделения паров растворителя в атмосферу на стадиях сушки и фильтрования. Кроме того, известный способ предусматривает фильтрацию полученной суспензии, что в случае низкомолекулярного полиэтилена фильтрация неэффективна вследствие забивания его частицами пор фильтра.
Таким образом, из уровня техники неизвестен более простой и быстрый способ выделения компонентов из растворов полиолефинов, в частности низкомолекулярного полиэтилена, в органических растворителях.
В связи с этим, нами была поставлена задача разработки простого способа выделения компонентов из раствора полиэтилена в органических растворителях, с низкой энергоемкостью и минимумом аппаратных средств.
Известен ряд технологических приемов разделения суспензий. К основным из них относится отстаивание, фильтрация, центрифугирование. Для установления возможного метода разделения фаз нами был определен размер частиц НМПЭ в суспензии для этого был использован метод оптической микроскопии. Выявлено, что размер частиц суспензии колеблется от 5.7 мкм (таких частиц больше всего 80%) до 200 мкм. Средний размер частиц 36.88 мкм. Такие размеры частиц позволяют в принципе использовать все известные методы для разделения суспензии. Метод отстаивания в данном случае неэффективен из за небольшой разницы в плотностях жидкой и твердой фаз. Метод фильтрации оказался неприемлем, поскольку фильтр быстро забивался воскоподобным НМПЭ и фильтрация становилась невозможной. В связи с этим, нами был использован метод центрифугирования для разделения фаз. Здесь следует отметить важный момент, который следует учитывать при выборе центрифуги. Существующие в данное время модели центрифуг по существу работают или по принципу фильтрации - центрифуги фильтрующего типа и по принципу осаждения - сепараторы. Применение центрифуг фильтрующего типа для разделения суспензии неэффективно, поскольку процесс по существу сводится к фильтрации и неприемлем по вышеназванным причинам. Поэтому для разделения суспензии приемлемы являются только центрифуги осадительного типа - сепараторы. В нашем случае, исследования в лабораторных условиях проводили на центрифуге MLWТ23. С целью установления оптимальных технологических режимов, изучена зависимость эффективности разделения суспензии от числа оборотов центрифуги при постоянном времени центрифугирования (рис.1). При этом, за эффективность разделения принимали объемное отношение растворителя и фазы, содержащей НМПЭ.
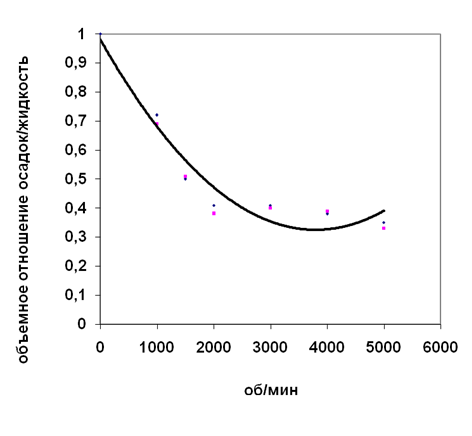
Рис.1 Зависимость объемного отношения осадок/жидкость от частоты вращения ротора центрифуги. Время центрифугирования 20 мин.
Видно, что при постоянном времени центрифугирования, увеличение угловой скорости вращения приводит к росту эффективности разделения суспензии. Причем, оптимальное число оборотов от 2000 до 3000 об/мин. При этой частоте исследована зависимость разделения суспензии от времени центрифугирования (рис.2).

Рис.2 Зависимость объемного отношения осадок/жидкость от времени центрифугирования. Частота вращения ротора центрифуги 2000 об/мин (1),3000 об/мин (2) .
Выбор конструкции центрифуги зависит от того, предназначается ли она для непрерывной работы с большими объемами или для периодического центрифугирования малых количеств. Учитывая, что объем отхода составляет 1.5 - 2 тыс. тонн в год, производительность центрифуги должна соответствовать этим объемам. Существует много типов промышленных центрифуг. В общем, все они делятся на центрифуги фильтрующего типа и центрифуги осадительного типа. Для целей разделения суспензии с размером частиц дисперсной фазы от 5 до 200 мкм, наиболее подходящими являются центрифуги осадительного типа. Применение центрифуг фильтрующего типа связано с затруднениями. Главной частью этих центрифуги такого типа является барабан из перфорированного листа металла, вращающийся с большой скоростью вокруг своей оси. Внутренняя стенка барабана покрыта фильтровальным материалом (х/б ткань). Из барабана суспензия продавливается центробежной силой через фильтрующий материал. Преимущество центрифуги такого типа состоит в их большой емкости и скорости отделения твердой фазы, что позволит эффективно перерабатывать большой объем отхода. Однако, по существу, процесс центрифугирования на фильтрующей центрифуге представляет собой процесс фильтрации, который в нашем случае затруднен из за быстрого забивания пор низкомолекулярным полиэтиленом. В связи с этим, для наших целей оптимальным является применение центрифуги осадительного типа. Оптимальное число оборотов 3000 об/мин. Обязательно противопожарное исполнение, поскольку смесь растворителей пожаро взрывоопасна.
Выделенный методом центрифугирования низкомолекулярный полиэтилен представляет собой воскоподобную массу светло желтого цвета, содержит в своем составе остаточное количество растворителей и для практического применения должен быть подвергнут дополнительной очистке [14]. Для очистки использовали следующие методы:
- 1. Вылежка 2. Экстракция органическим растворителем 3. Сушка под вакуумом
Метод вылежки давно используется на практике. В частности, он применяется при производстве изделий из полистирола. Для снижения доли остаточного мономера в изделиях они прежде чем поступить в продажу вылеживают на складе в течение нескольких месяцев. При этом выветривается мономер и исчезает запах, связанный с его присутствием. Нами предпринята попытка удалить летучие вещества из НМПЭ путем его вылежки. Для этого образец НМПЭ после центрифугирования раскладывали тонким слоем на ровной поверхности и выдерживали в комнатных условиях в течение месяца. При этом резко снижался характерный неприятный запах. Образец после вылежки представлял собой мазеподобный продукт светло желтого цвета.
Для экстракции органическим растворителем использовали гексан, ацетон и этанол. Экстракцию образцов НМПЭ после центрифугирования осуществляли на приборе сокслет в течение 3-х часов. После экстракции образцы сушили при 400С до постоянной массы. Результаты приведены в таблице 2.
Таблица 2. Экстракция образцов НМПЭ органическими растворителями
Растворитель |
Масса образца до экстракции, г |
Масса образца после экстракции и сушки, г |
Потеря массы, % |
Гексан |
32.6 |
21.4 |
34.4 |
Этанол |
28.5 |
19.6 |
31.2 |
Ацетон |
34.1 |
22.8 |
33.1 |
Из результатов видно, что посредством экстракции удаляется больше 30% веществ, содержащихся в НМПЭ, причем потеря массы примерно одинакова и не зависит от природы растворителя. НМПЭ после экстракции представляет собой воскоподобную массу светло желтого цвета с характерным запахом полиолефинов.
Также для очистки НМПЭ был использован метод сушки под вакуумом. Для этого образец НМПЭ после центрифугирования помещали в вакуум сушильный шкаф и выдерживали при определенной температуре под вакуумом. (рис.3).
Сушка в вакуум сушильном шкафу не позволяет полностью удалить растворитель из НМПЭ. По внешнему виду образцы похожи на те, которые получаются при вылежке. Здесь следует отметить, что полученные результаты не свидетельствуют о непригодности вакуумной сушки для отделения летучих из НМПЭ.

Рис. 3. Потеря массы образцом НМПЭ в вакуум сушильном шкафу при 1000С (1) и при 600С (2).
В лабораторных условиях трудно добиться низких давлений. В промышленных условиях представляется как раз целесообразным удаление летучих по той же схеме, как оно осуществляется для высокомолекулярного полиэтилена. Ниже приводятся ряд примеров, которые иллюстрируют комплексную технологию переработки отхода НМПЭ.
- 1. Отход производства линейного сополимера этилена с бутеном 1 центрифугируют на центрифуге при 2000-3000 об/мин. в течение 20-30 мин. Отделяют осадок низкомолекулярного полиэтилена и раскладывают его на ровной поверхности для вылежки с целью удаления летучих. Время вылежки при комнатнойтемпературе 20суток. Выходнизкомолекуляного полиэтилена 1,5 %. Выход смеси углеводородов - 95%. 2. Переработка отхода осуществляется как указано в примере 1., жидкая фракция - смесь углеводородов подвергается перегонке при температуре 125-1650С. Выход низкомолекулярного полиэтилена 1,5 %. Выход смеси углеводородов с температурой кипения 125-1650С - 41,7%. Кубовый остаток с температурой кипения 165-2800С - 56,8%. 3. Переработка отхода осуществляется как указано в примере 1., жидкая фракция - смесь углеводородов подвергается перегонке при температуре 125-1350С. Выход низкомолекулярного полиэтилена 1,5 %. Выход низкокипящей смеси углеводородов с температурой кипения 125-1350С - 5,7%. Кубовый остаток с температурой кипения 135-2800С - 92,8% 4. Переработка отхода осуществляется как указано в примере 1., жидкая фракция - смесь углеводородов подвергается перегонке при температуре 125-1450С. Выход низкомолекулярного полиэтилена 1,5 %. Выход низкокипящей смеси углеводородов с температурой кипения 125-1450С-14,2 %. Кубовый остаток с температурой кипения 145-2800С-84,3 %. 5. Переработка отхода осуществляется как указано в примере 1., жидкая фракция - смесь углеводородов подвергается перегонке при температуре 125-1500С. Выход низкомолекулярного полиэтилена 1,5 %. Выход низкокипящей смеси углеводородов с температурой кипения 125-1500С-27,0 %. Кубовый остаток с температурой кипения 145-2800С-71,0 %. 6. Переработка отхода осуществляется как указано в примере 1., жидкая фракция - смесь углеводородов подвергается перегонке при температуре 125-1600С. Выход низкомолекулярного полиэтилена 1,5 %. Выход низкокипящей смеси углеводородов с температурой кипения 125-1600С - 32,7 %. Кубовый остаток с температурой кипения 160-2800С - 65,3 %. 7. Переработка отхода осуществляется как указано в примере 2., жидкая фракция - смесь углеводородов подвергается перегонке при температуре 125-1600С. Отделяют осадок низкомолекулярного полиэтилена и не подвергают его вылежке. Выход низкомолекулярного полиэтилена 3,3 %. 8. Переработка отхода осуществляется как указано в примере 2.. Отделяют осадок низкомолекулярного полиэтилена, помещают его в прибор сокслет и экстрагируют летучие ацетоном в течение 2 часов, после чего низкомолекулярный полиэтилен высушивают при комнатной температуре до постоянной массы. Выход низкомолекулярного полиэтилена 2,2 %. 9. Переработка отхода осуществляется как указано в примере 2.. Отделяют осадок низкомолекулярного полиэтилена, помещают его в прибор сокслет и экстрагируют летучие гексаном в течение 2 часов, после чего низкомолекулярный полиэтилен высушивают при комнатной температуре до постоянной массы. Выход низкомолекулярного полиэтилена 2,3 %. 10. Переработка отхода осуществляется как указано в примере 2.. Отделяют осадок низкомолекулярного полиэтилена и помещают его в центрифугу. Осуществляют повторное центрифугирование при условиях, указанных в примере 1. Отделяют осадок низкомолекулярного полиэтилена и не подвергают его вылежке. Выход низкомолекулярного полиэтилена 2,5 %.
Похожие статьи
-
ВВЕДЕНИЕ - Получение и изучение углеводородов из отходов Шуртанского газо-химического комплекса
Актуальность проблемы. Ключевую роль в сохранении высоких темпов экономического роста играет поддержка отечественных производителей. Особое внимание...
-
ИСХОДНЫЕ ВЕЩЕСТВА Для получения низкомолекулярного полиэтилена были использованы отходы Шуртанского газо-химического комплекса. Для проведения экстракции...
-
Известно, что в аналогичных производствах зарубежных стран низкомолекулярный полиэтилен является одним из видов продукции, выпускаемых предприятием [5]....
-
ПРИМЕНЕНИЕ НИЗКОМОЛЕКУЛЯРНОГО ПОЛИЭТИЛЕНА В начале 50-х годов произошло революционное событие в химии XX столетия, значение которого невозможно...
-
ПРОМЫШЛЕННОЕ ПОЛУЧЕНИЕ УГЛЕВОДОРОДОВ - Происхождение горючих ископаемых
Алканы, алкены, алкины и арены получают путем переработки нефти (см. ниже). Уголь тоже является важным источником сырья для получения углеводородов. С...
-
Здесь следует подчеркнуть, что вторичной переработке могут быть подвергнуты только ТПО из термопластичных синтетических материалов, т. е. материалов,...
-
Подготовка сырья. - Переработка твердых отходов промышленных стройматериалов и машиностроения
Механическая обработка, девулканизата. Девулканизация резины. Остающаяся после регенерации РТИ текстильные волокна применяются для получения технической...
-
Исходя из технологии получения стекла и стеклоизделий главными компонентами стекла являются диоксид кремния SiO2, содержание которого в стекле составляет...
-
Для всех индивидуальных веществ температура кипения при данном давлении является физической константой. Так как нефть представляет собой смесь большого...
-
Получение тиосульфата натрия при мышьяково-содовой очистке газов - Тиосульфат натрия
В процессе очистки от сероводорода коксового и других промышленный газов мышьяково-содовым методом, помимо основной реакции: Протекают побочные реакции,...
-
Задача регрессии. Метод наименьших квадратов Ищу функцию регрессии в виде (1*). Оценки коэффициентов нахожу с помощью Метода Наименьших Квадратов (МКВ),...
-
Основная масса высокооктановых, бензинов как автомобильных, так и авиационных представляет собой смесь преобладающего по объему основного (базового)...
-
Для получения монокристаллов арсенида индия с высокими и стабильными электрофизическими параметрами необходимо использовать высокочистые исходные...
-
Известен способ получения мономерного формальдегида термической деполимеризацией низкомолскулярных полиоксиметиленов, получаемых при обработке водных...
-
Способы получения насыщенных растворов - Синтез ацетата натрия ("Горячий лед")
Простейший способ приготовления насыщенных растворов - длительное настаивание растворителя с избытком растворяемого вещества, лучше всего при...
-
На холоду даже дымящаяся серная кислота (олеум) почти не действует на предельные углеводороды, но при высокой температуре она может их окислять. При...
-
Производство кормового препарата ЖКЛ (жидкого концентрата лизина) - Этапы получения лизина
Технология производства ЖКЛ основана на упаривании готовой культуральной жидкости до содержания 40% АСВ. Для этого предварительно нагретую до температуры...
-
Однородные (гомогенные) смеси - это смеси, в которых компоненты смешаны на молекулярном уровне (однофазный материал); их невозможно обнаружить при...
-
Актуальность темы. В современных условиях глобальной конкуренции на все более интегрирующихся мировых рынках, развитие химической промышленности...
-
Схема реакции: Реактивы: Тимолфталеин, триэтиламин, хлороформ, дихлоангидрид терефталевой кислоты, гексан. Оборудование: Прибор для поликонденсации при...
-
Существует два основных способа получения полиарилатов: переэтерификация и взаимодействие хлорангидридов карбоновых кислот с двухатомными фонолами. 1....
-
Получение синтезированного газа - Анализ и технологическая оценка химического производства
Химические методы переработки нефти проводят при высоких температурах без катализатора (термический крекинг), при высоких температурах в присутствии...
-
Получение, Применение - Арены. Толуол
Известны следующие способы получения ароматических углеводородов. 1) Каталитическая дегидроциклизация алканов, т. е. отщепление водорода с одновременной...
-
Методы получения полимера - Важнейшие представители полимеров
Полистирол в промышленности получают главным образом свободно-радикальной полимеризацией стирола, используя вес известные методы: блочный, эмульсионный,...
-
Процесс нитрования углеводородов смесью азотной и серной кислот протекает в гетерогенной среде, так как образуются две фазы - органическая...
-
Способ получения диметилфосфита - Реакция диметилфосфита
Изобретение относится к области технологии органических соединений, а именно к усовершенствованному способу получения диметилфосфита. Описывается способ...
-
В промышленности синтез глиоксаля окислением этиленгликоля протекает в адиабатических условиях, оптимальный температурный режим процесса зависит от...
-
Запатентован способ получения глиоксаля окислением этиленгликоля в жидкой фазе при обработке кислородом или кислородсодержащим газом. Окисление проводят...
-
При анализе состава бензиновых фракций широко используют газожидкосую хроматографию. Для получения достоверных результатов хроматографического разделения...
-
В какой-то мере не много мы коснулись этих вопросов в предыдущем параграфе. Однако, весь комплекс переработки ТПО металлургических производств нами не...
-
Размер, не более 1000х800х2000 мм (без предварительного измельчения) Максимальная прочность кирпичного фрагмента 25 кг/см2 Металлическая арматура Класс...
-
Получение магния. - Химический элемент Магний
Преобладающий промышленный способ получения магния - электролиз расплава смеси MgCl2 расплава в безводных MgCl2, KCl, NaCl. Для получения расплава...
-
Применение H2O2 связано с его окислительными свойствами и безвредностью продукта его восстановления (H2O). Его использую для отбеливания тканей и мехов,...
-
Вакуум-термическое получение металлических рубидия и цезия - Металлургия лития, рубидия и цезия
Вакуумтермический метод является основным методом полу-чения металлических рубидия и цезия. Для восстановления рубидия и цезия используются следующие...
-
Одно дерево бразильской гевеи в среднем, до недавнего времени, было способно давать лишь 2-3 кг каучука в год; годовая производительность одного гектара...
-
Вязкость и плотность - Разработка рецептур и компаундирование моторных топлив
Вязкость -- один из важнейших показателей качества моторного топлива. От вязкости зависит надежность работы топливной аппаратуры, возможность...
-
Макрокинетика процесса - Каталитический риформинг
Характерной особенностью всех модификаций риформинга является то, что одна из его основных стадий - ароматизация - эндотермична, а другая - гидрокрекинг...
-
КОЛЛИГАТИВНЫЕ СВОЙСТВА РАСТВОРОВ - Растворы
Коллигативными свойствами называют физико-химические свойства растворов, которые обусловлены Природой растворителя и числом частиц растворенного вещества...
-
Природа растворов полимеров - Физико-химические свойства растворов полимеров
Размеры макромолекул соизмеримы с размерами коллоидных частиц. Поэтому растворы полимеров обнаруживают ряд свойств, характерных для коллоидных золей...
-
При пропускании смеси окиси углерода (СО) и водорода (Н2) над нагретым до 2000С катализатором, содержащим восстановленное железо, образуются смеси...
Полученные результаты и их обсуждение, ВЫДЕЛЕНИЕ И ОЧИСТКА НИЗКОМОЛЕКУЛЯРНОГО ПОЛИЭТИЛЕНА - Получение и изучение углеводородов из отходов Шуртанского газо-химического комплекса