Огляд різних системах керування запасами, Постановка задач досліджень - Розробка алгоритму планування запасів
У цей час існують різні системи керування запасами, кожна з яких характеризується певними особливостями планування запасів. Розглянемо основні з даних систем.
Керування по точці замовлення
При використанні методу планування й керування по точці замовлення підприємство формує завдання постачальникам, якщо обсяг його запасів опускається до якогось визначеного мінімального рівня.
Основна формула для розрахунку точки замовлення:
Де R - точка замовлення в одиницях запасу;
D - середньоденна потреба;
T - середня тривалість функціонального циклу.
З урахуванням страхового запасу формула точка замовлення здобуває вид:
Де SS - страховий запас в одиницях продукції.
Основна формула для розрахунку стандартного економічного замовлення (Economic order quantity - EOQ) виглядає в такий спосіб:
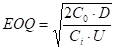
,
Де Co - величина витрат на одне замовлення; Сi - річні витрати на зміст запасів; D - річний обсяг продажів (в одиницях продукції); U - витрати на одиницю продукції [2].
Головне достоїнство методу - його гранична простота. Планування й керування по точці замовлення можна використати для керування запасами категорії С (по класифікації АВС), тобто порівняно недорогими виробами або матеріалами. Недолік методу складається в недостатній гнучкості - в умовах позаказной роботи й часто, що змінюється попиту, керування по крапці замовлення не дає задовільних результатів. Схема планування по точці замовлення представлена на рис 1.5.
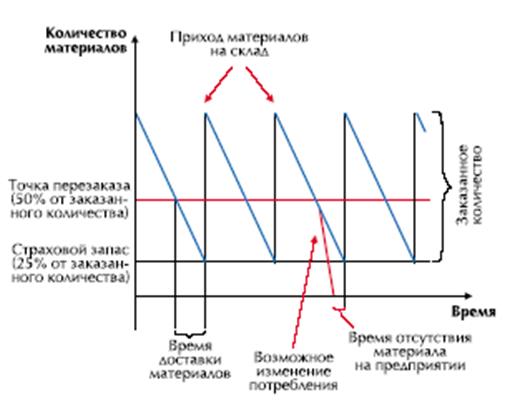
Рисунок 1.5 - Схема планування по точці замовлення.
У вітчизняній практиці керування цей метод також використається при керуванні виробництвом по міжопераційних заділах.
Метод Канбан.
Суть системи "Канбан" полягає в тому, щоб наявні запаси по своїй кількості відповідали потребам початкової стадії виробничого процесу, а не накопичувалися.
Особливості даного методу:
По-перше, передбачається, що заявкам споживачів готової продукції повинні відповідати не її попередньо накопичені запаси, а виробничі потужності, готові переробляти сировина й матеріали, що надходять майже "з коліс". Внаслідок цього обсяг виробничих запасів, що класифікуютьяс як заморожені потужності, мінімізується.
По-друге, в умовах мінімальних запасів необхідна безперервна раціоналізація в організації й керуванні виробництвом, тому що високий обсяг запасів нівелює, у відомому змісті маскує помилки й недоліки в цій області, вузькі місця виробництва, несинхронізовані операції, невикористовувані виробничі потужності, ненадійну роботу постачальників і посередників.
По-третє, для оцінки ефективності виробничого процесу, крім рівня витрат і продуктивності фондів, варто враховувати строк реалізації заявки, так називану тривалість повного виробничого циклу. Короткі строки реалізації заявок полегшують керування підприємством і сприяють росту конкурентноздатності завдяки можливості оперативного й гнучкого реагування на зміни зовнішніх умов.
При даному методі централізоване планування стосується тільки останньої ланки логістичного ланцюга, тобто складу готової продукції. Всі інші виробничі й постачальницькі одиниці одержують розпорядження безпосередньо від чергового, що перебуває ближче до кінця ланки логістичного ланцюга. Приміром, склад готових виробів дав заявку (що рівнозначно видачі виробничого завдання) на певне число виробів у монтажний цех, монтажний цех віддає розпорядження про виготовлення подузлов цехам обробки й відділу кооперування й т. д.
За певних умов (наявність партнерських відносин з постачальниками й клієнтами, серійне виробництво й організація виробничих ліній, низька вартість переналагодження встаткування для зменшення розміру виробленої партії й т. д.) даний метод може давати відмінні результати.
Метод MRP.
Метод MRP (Material Requirements Planning - планування потреб у матеріалах) передбачає ряд стандартних кроків:
На першому етапі робиться розрахунок нетто-потреб у матеріалах на підставі даних про склад виробу (специфікації).
Число необхідних матеріалів, вузлів і компонентів оцінюється з обліком наявного в наявності або в незавершеному виробництві (рис. 1.6).
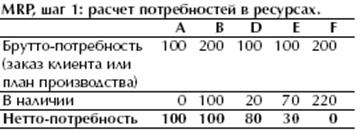
Рисунок 1.6 - Перший етап методу MRP.
Другий крок - розрахунок у часі нетто-потреб у матеріалах на підставі даних про склад виробу. На цьому етапі необхідні кількості розраховуються з урахуванням всіх приходів і витрат матеріалів (рис. 1.7). Якщо при цьому система виявляє зниження рівня матеріалу нижче певного рівня, то визначається кількість, яке потрібно закупити або зробити для задоволення потреби. Також можливий розрахунок нетто-потреб з обліком правила партії (з урахуванням мінімальної партії замовлення, кратності партії, періодичності замовлення).
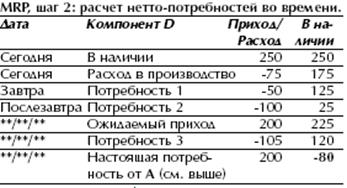
Рисунок 1.7 - Другий етап методу MRP.
Третій крок - визначення строків закупівлі й виготовлення. На цьому етапі для відділів планування й постачання система визначає строки початку дій по реалізації розрахованих нетто-потреб. Алгоритм MRP бере за початок дату реалізації кінцевої потреби й "розкручує" назад у часі процес виготовлення виробу або закупівлі матеріалів, визначаючи дати початку виробничих операцій з компонентами (деталями) нижнього рівня, аж до визначення дат формування замовлень постачальникам (рис. 1.8).
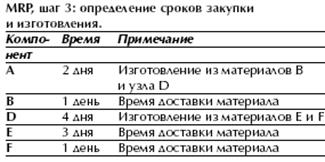
Рисунок 1.8 - Третій етап методу MRP.
Алгоритм розрахунку проілюстрований на рис 1.9.
Однієї з особливостей методу (у порівнянні з керуванням по точці замовлення) є те, що MRP не припускає можливості відсутності необхідних матеріалів на складі. Якщо всі вихідні дані й процедури планування виконані коректно й всі відхилення у виконанні плану враховуються вчасно, то всі поставки деталей і матеріалів повинні бути реалізовані точно вчасно. Крім того, метод MRP не "дивиться" у минуле: необхідні матеріали розраховуються на основі інформації про майбутні потреби й очікувані рівні запасів на складах.
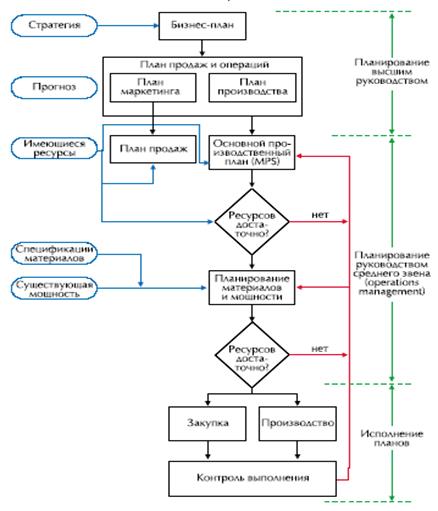
Рисунок 1.9 - Схема планування MRP II.
Достоїнства даного методу - у можливості враховувати майбутні потреби підприємства, формувати замовлення на поповнення запасів у потрібний термін і в потрібних обсягах.
Недолік MRP - неможливість урахувати обмеженість ресурсів підприємства.
Керування за схемою MRP II.
Найбільше широко використовуваний у цей час метод керування виробництвом і запасами - планування виробничих ресурсів (Manufacturing Resource Planning, MRP II).
Відповідний алгоритм включає наступні кроки:
Визначається потреба в готовій продукції, при цьому враховуються всі параметри попиту, а саме:
- - замовлення клієнтів; - прогноз попиту; - заявки для поповнення віддалених баз і дистриб'юторських складів; - прогнозована потреба в запасних частинах і т. д.
На основі цієї інформації формується основний виробничий план (ОВП). Алгоритм розрахунку плану нетривіальний і дуже сильно залежить від того, яким образом відбувається задоволення зовнішнього попиту - шляхом виробництва на склад/під замовлення, зборки під замовлення або розробки під замовлення.
З урахуванням інформації по ОВП і при наявності специфікацій вироби визначаються брутто-потреби на матеріали, що комплектують і проміжні зборки.
При наявності інформації про запаси (незавершене виробництво, запаси матеріалів і комплектуючих, матеріали в шляху) визначаються нетто-потреби на вироблені й закуповувані частини в кількості й у часі.
З урахуванням технологічних маршрутів (із вказівкою поопераційної трудомісткості й норм виробітку), а також інформації про графік роботи встаткування й виконуваних виробничих завдань обчислюється завантаження виробництва. При необхідності (наприклад, у випадку виявлення перевантаження) виробляється перепланування.
До достоїнств цього методу варто віднести можливість одержання дуже точних планів закупівель і виробництва. При цьому методика планування (у випадку її коректного використання на підприємстві) буде відмінно працювати навіть при нестабільних внутрішніх і зовнішніх умовах. Приміром, можна компенсувати такі фактори, як зриви поставок матеріалів і комплектуючих (по строках і кількості), нестабільно працююче встаткування, зміна зовнішнього попиту (скажемо, відмова клієнта від замовлення). Завдяки простому алгоритму метод керування запасами й виробництвом MRP II у цей час використається більшістю західних підприємств; постійно росте число його прихильників і серед українських менеджерів.
Недолік методу полягає в його відносній складності. Сама логіка побудови алгоритму MRP II заснована на проведенні безлічі обчислень, що означає необхідність розвинутої інформаційної системи класу MRP II або ERP. Крім того, досить високі вимоги пред'являються до точності інформації про стан підприємства, що поставляє в систему. Так, кількість наявних запасів повинне оцінюватися з точністю не менш 95%, така ж точність потрібно при плануванні виробничих завдань і замовлень постачальникам, при визначенні специфікацій і технологічних маршрутів і т. д.
Слід зазначити, що складність і вимогливість характерні для всіх високотехнолоігчних сучасних методів керування. Так чи інакше, якщо підприємство прагне вивести своє виробництво на світовий рівень, вимогу до наявності інформаційної системи й точності інформації в ній повинне бути виконано.
Серед недоліків методу, що обмежує його застосування на багатьох українських промислових підприємствах (особливо в компаніях, що випускають складні вироби з безліччю рівнів вкладеності, компонентів, операцій і т. д.), варто також назвати планування без одночасного обліку потужності, планування в минуле (без "обліку сьогодні"), неможливість надійно зв'язати потреба нижнього рівня з "батьківською" потребою.
APS: синхронне планування.
Методика вдосконаленого, або синхронного, планування (Advanced Planning and Scheduling, APS) - одне з новітніх досягнень західної думки в області керування виробництвом і запасами.
Структурно даний метод може бути розділений на дві частини:
Перша пов'язана із плануванням виробництва й постачання;
Друга - з диспетчеризацією виробництва.
Алгоритм роботи першої частини схожий з алгоритмом роботи MRP II. Існує невелике, але істотне розходження: планування по алгоритму MRP II виконується за схемою:
- 1) планується закупівля або виробництво необхідних виробів з розрахунку нескінченних ресурсів; 2) оцінюються ресурси; 3) у випадку невідповідності доступної потужності ресурсу й планованого завантаження виробляється перепланування дати запуску у виробництво з урахуванням кінцевої потужності; 4) потім, оскільки дати змінилися, виробляється перепланування закупівлі або виробництва, знову ж з розрахунку нескінченних ресурсів; 5) далі повторюються кроки 2, 3 і т. д.
Такий процес забирає значний час, тому, як правило, не може вироблятися постійно (на щоденній або навіть на щотижневій основі). У проміжках між переплануванням ніяк або майже ніяк не враховуються відхилення від плану, які у виробництві можуть відбуватися досить часто. Цією обставиною можна зневажити у випадку серійного, щодо стабільного виробництва. Однак при позаказном виробництві, а також в умовах твердої конкуренції алгоритм планування MRP II починає давати незадовільні результати по строках виконання замовлення й по точності дотримання строків.
Алгоритм розрахунку APS позбавлений цих недоліків, тому що за один раз розраховує необхідні закупівлі й виробництво, з огляду на існуючі (обмежені) потужності й виконувані виробничі завдання. Крім того, завдяки використанню іншої математичної моделі розрахунок планів виробляється набагато швидше - він займає всього кілька хвилин (на відміну від декількох годин при використанні стандартних систем MRP II).
Друга частина методу APS, пов'язана з диспетчеризацією, реалізується з обліком всіх критичних місць виробництва. При цьому APS - системи звичайно дозволяють накладати й ураховувати обмеження на процеси оперативного керування виробництвом.
Достоїнства методу APS включають можливість одержання реальних планів на основі моделювання виробничого процесу й оцінки різних варіантів за схемою "якщо". Крім того, використання цього методу (і відповідної інформаційної системи) дозволяє в режимі реального часу, наприклад, у ході телефонної розмови, розраховувати дату виконання замовлень клієнтів з обліком ситуації на підприємстві.
Недоліки методу: по-перше, для його застосування потрібне наявність потужної ERP-системи, у якій підтримуються функції синхронного планування, причому тісно інтегровані з іншими модулями КИСНУВ; по-друге, істотно підвищуються вимоги до точності вихідної інформації. /11/
Порівняльні характеристики методів виробничого планування наведені в таблиці 1.1.
Таблиця 1.1 Порівняльні характеристики методів виробничого планування.
Метод |
Область найбільш ефективного застосування |
Достоїнства |
Недоліки |
Особливості реалізації в ERP - системах |
По крапці замовлення |
Підприємства із простою схемою виробництва |
Простота |
Відсутність гнучкості. Ненадійність при плануванні складних багатокомпонентних виробів. |
У всіх присутніх на ринку західних ERP - системах |
MRP, MRP II |
Серійне, відносно стабільне виробництво |
Їсти можливість ураховувати майбутні потреби підприємства, формувати замовлення на одержання запасів у потрібний термін і в потрібних обсягах. У випадках нескладних виробництв і стабільного попиту дає високу точність планування |
Неможливість урахувати обмеженість ресурсів підприємства, неможливість надійного визначення для будь-якого компонента нижнього рівня джерела потреби. Складність, тривалість розрахунків. |
У більшості присутніх на ринку західних ERP - системах |
По вузьких місцях |
Підприємства з яскраво вираженим критичним ресурсом |
Швидка віддача. |
Незастосовність в умовах мінливості критичних ресурсів |
Preactor APS, TroughPut, SyteLine. net |
APS |
Підприємства, орієнтовані на задоволення зовнішнього попиту під замовлення |
Гнучкість. Можливість одержання реальних планів |
Високі вимоги до функціональності ПО й до точності вихідних даних. |
Убудовані функції в ERP - систему - тільки SyteLine. net, а в якості окремого, не інтегрованого модуля - у більшість західних ERP - систем |
Зведене в таблиці порівняння розглянутих вище методів планування запасів дозволяє оцінити їхнього достоїнства, недоліки, застосовність у конкретних виробничих умовах.
Постановка задач досліджень
Метою даної роботи є розробка програмного та алгоритмічного забезпечення для прийняття рішень при плануванні складських запасів підприємства.
Для досягнення мети дослідження необхідно вирішити наступні задачі:
- - розкрити функціональну роль запасів у виробничому процесі; - розглянути необхідність існування запасів підприємства; - розглянути логістичний підхід до керування запасами; - розглянути різні системи керування запасами; - провести аналіз методів управління запасами; - розробити алгоритмічне забезпечення для прийняття рішень при плануванні складських запасів на підприємстві; - розробити програмне забезпечення для реалізації розробленого алгоритму.
Похожие статьи
-
Як відзначалося вище, створення виробничих запасів на підприємстві забезпечує безперервність виробничого процесу випуску продукції. При цьому, недолік...
-
Відомі два підходи до організації інформаційних масивів: файлова організація та організація у вигляді бази даних. Файлова організація передбачає...
-
Вступ - Розробка алгоритму планування запасів
Стан і ефективність використання виробничих запасів, як самої значної частини оборотного капіталу - є однією з основних умов успішної діяльності...
-
Поняття, сутність і класифікація виробничих запасів підприємства Алгоритмічний програмний складський запас Поняття матеріального запасу є одним із...
-
Варіант Пристрій Переривання Розташування даних Тип даних Тип обміну даними Конфігурування 24 Бітовий процесор + Зовнішнє Блок Пам'ять Програмне Бітовий...
-
Постановка задачи Необходимо разработать программу для поиска автобусных маршрутов. В качестве среды разработки должна использоваться Delphi 7. В...
-
Призначення централізованої промислової КМ підприємства з виробництва сільськогосподарських кормів Проектована система призначена головним чином...
-
Загальні відомості Теплова електростанція (ТЕС) - це електростанція, що виробляє електричну енергію в результаті перетворення теплової енергії, що...
-
Постановка задачи Основной целью дипломной работы является создание комплексной системы информационной безопасности предприятия на примере информационной...
-
Для проверки соответствия требованиям ТЗ, была поставлена задача разработки 3-D модели корпуса Kyocera KD-PB1D79 при помощи системы AutoCAD. В этой части...
-
Выполнения проекта монтажа охранной сигнализации состоит из множества операций, которые складываются в этапы работ проекта. Схематично структура этапов...
-
Для того, чтобы разработать оптимальный метод интеграции сторонних систем в существующую ИТ-инфраструктуру систем компании, требуется точно поставить...
-
Построение модели предметной области с помощью описания структур данных и программного кода является классическим подходом в разработке ИС. Зачастую...
-
Перед написанням драйверу доцільно переконатись чи працює фізичний пристрій як це очікувалось. Майстер можно використати для такої перевірки пристрою....
-
Составьте программу для реализации графического редактора линий, изображенного на рисунке 1.1.: Рисунок 1.1. - Пример работы Целью данной работы является...
-
Сучасні вимоги до ІС "ГППР" надає адміністрації та співробітникам унікальну можливість отримувати повну і достовірну інформацію про наявне устаткування,...
-
Постановка задачи, Описание программы, Алгоритм работы - Алгоритм кодировки RSA
Реализовать клиент серверное приложение для пересылки закодированной информации. В качестве алгоритма реализовать алгоритм RSA. Описание программы...
-
Загальні положення захисту інформації у мережі Мережеві атаки настільки ж різноманітні, як і системи, проти яких вони спрямовані. Деякі атаки...
-
Пересчет симплекс-таблицы. - Транспортная задача
Формируем следующую часть симплексной таблицы. Вместо переменной x в план 1 войдет переменная x1 . Строка, соответствующая переменной x1 в плане 1,...
-
Управление производством и уровнем запасов - Офисные автоматизированные технологии
Другой сферой при обсуждении вопросов компьютеризации является управление уровнем запасов. Аспекты менеджмента в отношении управления производством и...
-
Широкое распространение в операционной системе Windows имеет множество стандартных программ обеспечивающих работу устройств компьютера и служащих для...
-
Операционная система Windows XP была разработана и выпущена на смену операционной системе DOS фирмой Microsoft XP в 2002 году. Именно поэтому она и...
-
Згідно технічного завдання потрібно спроектувати локальну комп'ютерну мережу, яка складається з п'яти поверхів, на кожному з яких знаходиться по п'ять...
-
3.1 Алгоритм функционирования СУ технологического объекта Рисунок 8 - Общий алгоритм функционирования 3.2 Алгоритм запуска технологического объекта...
-
Методы разработки вычислительной сети: 1. Экспериментальный метод - персонал предприятия закупает "новинки" рынка компьютерной техники. Такой метод -...
-
Використання ГІС в екології - Застосування геоінформаційних систем в різних галузях господарства
Причини, які спонукають до застосування ГІС як інформаційного забезпечення систем екологічного управління, пов'язані з такими обставинами: - наявність...
-
Общее описание программного обеспечения, реализующего разработанный алгоритм Основной идеей дипломного проекта, является реализация алгоритма...
-
Умовно функції ГІС можна поділити на п'ять груп, при цьому перші три належать до традиційних функцій геоінформаційних технологій, останні дві - до нових,...
-
Етапи рішення прикладних задач з використанням комп'ютерів 1) Формулювання задачі в термінах певної предметної галузі знань (математика, фізика,...
-
Заповнивши список координат ділянки вручну, або зробивши імпорт із зовнішніх форматів, у Вас виникне природна потреба в перегляді результатів вашої...
-
Розглянемо порядок заповнення інформації про внутрішньогосподарські пристрої земельних ділянок. Для всіх ділянок несільськогосподарського призначення...
-
Поняття бази даних. Системи управління базами даних - Система керування базами даних Access
Під час інформаційної діяльності людина збирає і накопичує відомості про довкілля. До появи обчислювальної техніки вся інформація звичайно зберігалася в...
-
Цель Работы - изучить основные способы работы с пользовательским типом данных "класс", его объектами, методами и способы доступа к ним. - Теоретические...
-
При создании или при классификации информационных систем неизбежно возникают проблемы, связанные с формальным - математическим и алгоритмическим...
-
По завершении работы над первым этапом курсового проекта по компьютерным сетям и телекоммуникациям, мною был составлен список всего ПО установленного на...
-
1. Провести обзор методов автоматического построения профиля нормального поведения веб-приложения. 2. Сформулировать требования к методу, провести...
-
Постановление Правительства Российской Федерации №1119 "Об утверждении требований к защите персональных данных при их обработке в информационных системах...
-
СХЕМА АЛГОРИТМА РАБОТЫ ПРОГРАММЫ, ЗАКЛЮЧЕНИЕ - Основы программирования в операционной системе Unix
Блок-схема главной функции программы (main) изображена на рисунке 4. Рисунок 4 - блок-схема main. cpp Блок-схема модуля (Math. cpp) изображена на рисунке...
-
Вступ - Розробка графічної частини проекту землеустрою засобами геоінформаційних систем
Геоінформацімйна Системма - сучасна комп'ютерна технологія, що дозволяє поєднати модельне зображення території (електронне відображення карт, схем,...
-
Теоретические аспекты поставленной задачи В этой части проекта будут объяснены этапы применения МКЭ для плоской фермы. В первой главе было рассмотрено...
Огляд різних системах керування запасами, Постановка задач досліджень - Розробка алгоритму планування запасів