Исследование глубины дефектного слоя обрабатываемой детали при электроэрозионной обработке
ИССЛЕДОВАНИЕ ГЛУБИНЫ ДЕФЕКТНОГО СЛОЯ ОБРАБАТЫВАЕМОЙ ДЕТАЛИ ПРИ ЭЛЕКТРОЭРОЗИОННОЙ ОБРАБОТКЕ
В данной статье, я рассмотрю влияние метода электроэрозионной обработки на технологические характеристики поверностного слоя обрабатываемого материала, изменение твердости и шероховатости поверхности после электроэрозионной обработки твердосплавной фрезы.
Ключевые слова: инструментальная техника, технологии формообразования, цельная твердосплавная фреза, электроэрозионная обработка электроэрозионный обработка твердость шероховатость
В статье рассмотрено влияние метода электроэрозионной обработки на технологические параметры, обрабатываемой поверхности.
За основу исследования была взята экспериментально изготовленная методом электроэрозионной обработки мелкомодульная твердосплавная червячная фреза. Фреза была изготовлена в инструментальном цехе Чистопольского Часового Завода "Восток". Отличительной особенностью данного инструмента является то, что данная фреза имеет диаметр всего 12 мм и толщину 3 мм. Профиль зубьев изготавливается с точностью до 0,01 мм. В технологической цепочке изготовления данной фрезы используются технологии электроэрозии, так как твердосплавная фреза имеет высокую твердость 82-90 HRA и поэтому для ее обработки используется электроэрозионная обработка.
После изготовления мелкомодульной фрезы, она была отправлена в лабораторию для более детального исследования изменений в поверхностной структуре инструмента.
Микрошлиф, изготавливался на автоматическом шлифовально-полировальном станке TegraPol с приспособлением TegraForce. Автоматическая дозировка шлифовально-полировальных суспензий осуществляется с помощью устройства Tegra Doser-5.
Структура поверхностного слоя заготовки фотографировалась с помощью цифровой камеры на микроскопе Polyvar Met (Австрия).
Использованное оборудование:
- - оборудование для изготовления шлифа фирмы Struers (Дания); - пресс Pronto Press-20; - смола для запрессовки эпоксидная с минеральными наполнителями DuroFast, для наилучшего удержания края.
Таблица 1
Микротвердость, измеренная от вершины зуба к сердцевине по трем точкам
H, мкм |
HV0,05(кгс) H=f(h) | ||
1 |
2 |
3 | |
10 |
1609 |
1552 |
1374 |
20 |
1511 |
1479 |
1559 |
30 |
1607 |
1485 |
1609 |
50 |
1572 |
1609 |
1499 |
70 |
1447 |
1441 |
1566 |
100 |
1479 |
1505 |
1512 |
200 |
1447 |
1492 | |
Примечание: d=7,83 мкм |
Таблица 2
Микротвердость, измеренная от впадины зуба к сердцевине по трем точкам
H, мкм |
HV0,05(кгс) H=f(h) | ||
1 |
2 |
3 | |
10 |
1670 |
1732 |
1639 |
20 |
1616 |
1545 |
1630 |
30 |
1559 |
1708 |
1422 |
50 |
1573 |
1566 |
1560 |
70 |
1638 |
1692 |
1499 |
100 |
1566 |
1580 |
1518 |
200 |
1602 |
1573 |
1536 |
Примечание: d=7,83 мкм |
Таблица 3
Микротвердость, измеренная в сердцевине зуба (основании)
HV0,05(кгс) H=f(h) | |
1 |
2 |
1492 |
1492 |
Таблица 4
Микротвердость, измеренная в сердцевине по трем точкам
HV0,05(кгс) H=f(h) | ||
1 |
2 |
3 |
1553 |
1607 |
1588 |
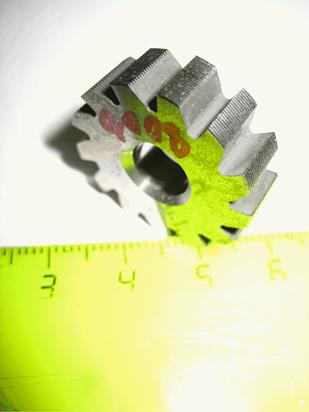
Рис. 1 Мелкомодульная червячная фреза. (Область применения: нарезание зубчатых колес механизмов наручных часов)
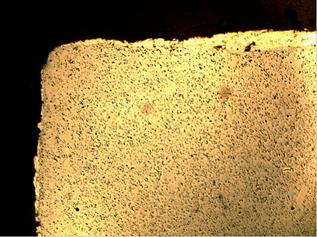
Рис. 2 Микрошлиф передней кромки твердосплавной мелкомодульной червячной фрезы (увеличение Х 500)

Рис. 3 Микрошлиф передней кромки твердосплавной мелкомодульной червячной фрезы (увеличение Х 200)
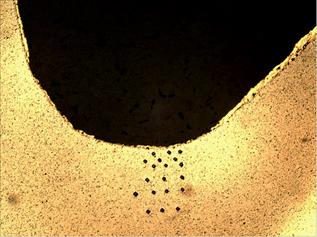
Рис. 4 Микрошлиф впадины зуба стружечной канавки твердосплавной мелкомодульной червячной фрезы (увеличение х 200)
Следующим шагом определялась шероховатость задней поверхности вдоль режущей кромки на заготовке мелкомодульной твердосплавной червячной фрезы. В качестве оценки параметра шероховатости принимаю величину Rа, выражающееся следующим образом:

(1) Или (2)

Где l - базовая длина; n - число выбранных точек профиля на базовой длине; - абсолютное отклонение профиля от средней линии в i-ой точке профиля.
Профиль задней поверхности модульной фрезы контролировали с помощью лазерного конфокального сканирующего микроскопа Olympus LEXT OLS - 3100 (Япония) с вертикальным разрешением сканирующей системы 0,01мкм.
Для анализа выбранной области поверхности с использованием лазерного микроскопического изображения достаточно сложно применять требования стандарта ИСО. Это связано с тем, что просматриваются очень малые поля зрения, а значит, базовая длина будет иметь малый предел. Вместе с тем для числовых значений высотных параметров установлены соответствующие базовые длины в таблице 5.
Таблица 5
Соответствие числовых значений RA, числовым значениям базовой длины из ГОСТ
Ra, мкм |
До 0,025 |
Свыше 0,025 До 0,4 |
Свыше 0,4 До 3,2 |
Свыше 3,2 До 12,5 |
Свыше 12,5 До 100 |
L, мм |
0,08 |
0,25 |
0,8 |
2,5 |
8,0 |
В программном обеспечении Olympus LEXT при расчете параметров шероховатости (волнистости) поверхности используется следующее допущение: базовая длина составляет 1/3 области от центра заданного поперечного сечения поля зрения. При увеличении 200Х поле зрения имеет размер 640Ч 480 мкм, что явно недостаточно для измерения шероховатости покрытия, которое оценили величиной ~ 2,5 мкм.
Для увеличения базовой длины было выполнено последовательное соединение нескольких полей зрения при заданном увеличении с помощью специального режима мозаики, предусмотренного программным обеспечением микроскопа. Соединив четыре поля зрения при увеличении 200Х, мы получили изображение задней поверхности режущей кромки одного из зубьев модульной фрезы. Таким образом, оценка RA происходила на базовой длине 0,85 мм, что соответствует стандарту.
Для установления RA на полученной мозаике произвольно выбирали продольное сечение параллельное режущей кромки и тем самым получали необходимый профиль, на котором рассчитывался высотный параметр по формуле (2) при числе выбранных точек профиля на базовой длине n =1024. Среднее значение RA полученное из 15-ти сечений с надежность 95% составило 2,6 ± 0,3 мкм.

Рис. 5 Изображение участка поверхности вдоль передней поверхности твердосплавной мелкомодульной червячной фрезы, полученное в мозаичном режиме 3D-сканирования на лазерном микроскопе Olympus LEXT
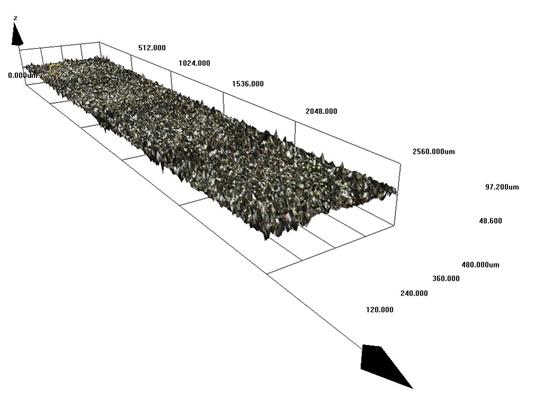
Рис. 6 Топография участка поверхности вдоль передней поверхности твердосплавной мелкомодульной червячной фрезы (задняя поверхность). 3D - изображение, полученное после сканирования на лазерном микроскопе Olympus LEXT
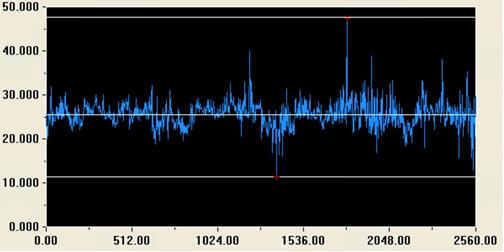
Рис. 7 Профиль (мкм) участка поверхности вдоль передней поверхности твердосплавной мелкомодульной червячной фрезы в произвольном продольном сечении
Из анализа приведенных данных видно, что в поверхностном слое отсутствуют микродефекты, в виде микротрещин после электроэрозионной обработки, как в впадине зуба так и в вершине зуба.
На поверхности просматриваются участки тонкого слоя со структурой отличной от основы толщиной порядка от 5 до 20 мкм, которая меняется по толщине. Этот слой по толщине укладывается в припуск на последующую обработку шлифованием, поэтому он не представляет опасности с точки зрения изменения свойств.
Оценка изменения свойств поверхностного слоя после электроэрозионной обработки проводилась путем измерения микротвердости с небольшой нагрузкой 50 гр = 0,5 Н с помощью приставки к микроскопу Polyvar Met - Microduramat - 4000.
На основании полученных данных, микротвердость практически не меняется по глубине, также микротвердость не меняется ни на вершине, ни на сердцевине. Это косвенно свидетельствует об отсутствии структурных изменений и значимых изменений химического состава при электроэрозионной обработке.
Библиографический список
- 1. Петухов Ю. Е. Формообразование численными методами / Ю. Е. Петухов. М.: "Янус-К", 2004. 200 с. 2. Петухов Ю. Е., Домнин П. В. Формообразование фасонных винтовых поверхностей инструментов на основе применения стандартных концевых и торцевых фрез. М.: ФГБОУ ВПО МГТУ "СТАНКИН", 2012. 130 с. 3. Гречишников, В. А. Математическое моделирование в инструментальном производстве / Гречишников В. А., Колесов Н. В., Петухов Ю. Е.. М.: МГТУ "СТАНКИН". УМО АМ, 2003. 116 с. 4. Петухов Ю. Е. Проектирование инструментов для обработки резанием деталей с фасонной винтовой поверхностью на стадии технологической подготовки производства: дис. ... докт. техн. наук: 05.03.01 / Петухов Ю. Е.. М., 2004. 393 с. 5. Петухов Ю. Е. Численные модели режущего инструмента для обработки сложных поверхностей / Петухов Ю. Е., Колесов Н. В. // Вестник машиностроения. 2003. №5. С. 61-63. 6. Петухов Ю. Е. Профилирование режущих инструментов среде Т-flex CAD-3D / Петухов Ю. Е. // Вестник машиностроения. 2003. №8. С. 67-70. 7. Петухов, Ю. Е. Способ формообразования фасонной винтовой поверхности стандартным инструментом прямого профиля / Петухов Ю. Е., Домнин П. В. // Вестник МГТУ "СТАНКИН". 2011. №3. С. 102-106. 8. Колесов Н. В. Система контроля сложных кромок режущих инструментов / Колесов Н. В., Петухов Ю. Е. // ИТО: Инструмент. Технология. Оборудование. 2003. №2. С. 42-45. 9. Петухов Ю. Е. Компьютерная модель формообразования сложной поверхности / Петухов Ю. Е., Домнин П. В. // Международная научно-техническая конференция "Автоматизация: проблемы, идеи, решения". В 2 т.: сб. науч. ст. Тула, 2010. Т. 1. С. 197-200. 10. Колесов Н. В. Компьютерная модель дисковых фасонных затылованных фрез / Колесов Н. В., Петухов Ю. Е., Баринов А. В. // Вестник машиностроения. 1999. №6. С. 57-61. 11. Домнин П. В. Решение обратной задачи профилирования на базе схемы численного метода заданных сечений /Петухов Ю. Е., Домнин П. В. // Справочник. Инженерный журнал с приложением. 2011. №11. С. 26-29. 12. Колесов Н. В. Математическая модель червячной фрезы с протуберанцем / Колесов Н. В., Петухов Ю. Е. // СТИН. 1995. №6. С. 26-29. 13. Колесов Н. В. Два типа компьютерных моделей режущего инструмента Колесов/ Н. В., Петухов Ю. Е. // СТИН. 2007. №8. С. 23-26. 14. Петухов Ю. Е. Точность профилирования при обработке винтовой фасонной поверхности / Ю. Е. Петухов, П. В. Домнин // СТИН. 2011. №7. С. 14-17. 15. Петухов Ю. Е., Математическая модель криволинейной режущей кромки спирального сверла повышенной стойкости / Ю. Е. Петухов, А. А. Водовозов // Вестник МГТУ "СТАНКИН". 2012. №3. С. 28-32. 16. Петухов Ю. Е. Некоторые направления развития САПР режущего инструмента / Ю. Е. Петухов // СТИН. 2003. №8. С. 26-30. 17. Петухов Ю. Е. Затачивание по передней поверхности спиральных сверл с криволинейными режущими кромками / Ю. Е. Петухов, А. А. Водовозов // Вестник МГТУ "СТАНКИН". 2014. №1 (28). С. 39-43. 18. Петухов Ю. Е. Определение задних кинематических углов при обработке винтовых фасонных поверхностей стандартными фрезами прямого профиля./ Петухов Ю. Е., Домнин П. В.// Вестник МГТУ Станкин. 2014.№ 2 (29). С. 27-33. 19. Петухов Ю. Е.Задачи по формообразованию при обработке резанием /Петухов Ю. Е., Колесов Н. В., Юрасов С. Ю.//Вестник машиностроения. 2014.№ 3. С. 65-71. 20. Петухов Ю. Е.Компьютерное моделирование обработки винтовой канавки на заготовке концевой фрезы./ Петухов Ю. Е, Домнин П. В.//Известия Московского государственного технического университета МАМИ. 2011.№ 2. С. 156-164. 21. Петухов Ю. Е. Cпособ шлифования фасонных валов. Патент на изобретение RUS 863310 04.05.1979. 22. Петухов Ю. Е.Устройство для правки фасонных шлифовальных кругов. Патент на изобретение RUS 823101 21.03.1979. 23. Петухов Ю. Е. Способ обработки цилиндрических поверхностей патент на изобретение RUS 904999 04.05.1979. 24. Петухов Ю. Е. Прибор для профилирования червячных фрез. Патент на изобретение RUS 878467 07.12.1978. 25. Петухов Ю. Е Определение задних кинематических углов при обработке винтовых фасонных поверхностей стандартными фрезами прямого профиля /Петухов Ю. Е., Домнин П. В.// Вестник МГТУ Станкин. 2014.№ 2 (29). С. 27-33. 26. Petukhov Yu. E. Some directions of cutting tool cad system development./ Petukhov Yu. E.// Russian Engineering Research. 2003. Т. 23.№ 8. С. 72-76. 27. Petukhov Yu. E. Curvilinear cutting edge of a helical bit with uniform life./ Petukhov Yu. E.//Russian Engineering Research. 2014. Т. 34.№ 10. С. 645-648. 28. Kolesov N. V. The mathematical model of a hob with protuberances./Kolesov N. V., Petukhov Yu. E.// Russian Engineering Research. 1995. Т. 15.№ 4. С. 71-75. 29. Petukhov, Y. E. Shaping precision in machining a screw surface / Y. E. Petukhov, P. V. Domnin // Russian Engineering Research. 2011. T. 31. №10. С. 1013-1015. 30. Kolesov, N. V. Computer models of cutting tools / N. V. Kolesov, Y. E. Petukhov // Russian Engineering Research. 2007. T. 27. №11. С. 812-814. 31. Petukhov, Y. E. Determining the shape of the back surface of disc milling cutter for machining a contoured surface / Y. E. Petukhov, A. V. Movsesyan // Russian Engineering Research. 2007. T. 27. №8. С. 519-521.
Похожие статьи
-
При конструировании, изготовлении и сборке оптических деталей большое значение имеют базовые поверхности или сокращенно базы. Базами называют...
-
Системы автоматического управления точностью обработки деталей Обработка заготовок на станках с ПУ обеспечивает высокую степень автоматизации и широкую...
-
В дополнение к количественным параметрам в некоторых случаях целесообразно нормировать направление неровностей, например в связи с направлением...
-
Несмотря на высокие качества современных токарных станков, совершенство методов обработки, точность применяемых измерительных инструментов и наличие...
-
Для фрезерной обработки паза выбираем концевую фрезу из твердого сплава, хвостовик по DIN 6535HA. Таблица 11.2.2 - Режущий инструмент и его параметры для...
-
Производственные помещения вычислительного центра характеризуются следующими факторами вредного воздействия на работающего: - Повышенным тепловыделением...
-
Таблица 2.3.4.1. Расчет полноты вложения сырья Наименование Масса, г Влага, г Сухие вещества, г В 100г По рец В 100 г По рец. Яйцо куриное 30 74 22,2 26...
-
Определение потери массы блюда "Молочно-яичный суп" при тепловой обработке Определение массы блюда "Молочно-яичный суп" проводится взвешиванием до и...
-
Особенности механизации и автоматизации сборочных работ Недостаточно высокий уровень механизации и автоматизации сборочных работ в машиностроении...
-
Расчет пищевой ценности проводится на основе рецептуры блюда, содержания основных пищевых веществ в каждом из ингредиентов и в блюде в целом, с учетом...
-
Одним из путей повышения долговечности коленчатого вала автомобиля является повышение износостойкости его шеек. Усовершенствовать способ получения...
-
Припуск - слой материала, удаляемый с поверхности заготовки в целях достижения заданных свойств обрабатываемой поверхности детали. Припуск на обработку...
-
Целью данного исследования было изучение шероховатости поверхности напыленных дисков. В качестве объектов исследования были взяты пять образцов дисков -...
-
Шероховатость поверхности оценивается по неровностям профиля (чаще поперечного), получаемого путем сечения реальной поверхности плоскостью (чаще всего в...
-
Данному виду обработки подлежат следующие поверхности: - Ш16 с фаской 1Ч45° - 30 и 31 соответственно. Обработка поверхностей будет проходить за 2...
-
Данному виду обработки подлежат следующие поверхности: - шпоночный паз (10Н9 глубиной 7) - 27. Глубина резания (мм) пов. 27 будет равняться глубине паза....
-
Особенности механической обработки - Изготовление деталей из пластмасс
При разделительной штамповке, наряду с известными особенностями для штамповки металлов, имеют место особенности, связанные с резкой анизотропией...
-
Типовой технологический процесс ЭЭО на копировально-прошивочных станках заключается в следующем: 1. Заготовку фиксируют и жестко крепят на столе станка...
-
Данному виду обработки подлежат следующие поверхности: - линейные - 4, 16, 7, 9, 13, 19; - диаметральные - 3, 6, 17, 8, 14; - фаски - 2, 5, 10, 12, 15,...
-
Режущий инструмент для токарной, фрезерной и сверлильной обработки будет выбираться из общего инструментального каталога фирмы Walter [6]. Токарная...
-
Резанье металлов - это обработка путем снятия стружки. В процессе обработки рабочее движение сообщаемое заготовке и режущему инструменту обеспечивает...
-
При фиксированной производственной программе эффективный годовой фонд времени, необходимый для ее выполнения, определяется по формуле: Таблица 8.1 -...
-
При фиксированном эффективном фонде времени работы производственная программа в вариантах определяется по формуле: (3.1) Где - годовая производственная...
-
При выполнении курсового проекта была подобрана группа деталей, а также выполнен технологический чертеж комплексной детали. Дана характеристика материала...
-
Зубофрезерование является самой распространенной, но трудоемкой операцией для обеспечения высокого качества изготовления зубчатых колес, ее следует...
-
Схема размещения технологического оборудования - это расположение технологического оборудования и рабочих мест на производственной площади. В курсовом...
-
Обработка поверхности детали без снятия стружки - Методы отделочной обработки поверхности
Методами обработки без снятия стружки получают только те поверхности, которые будут сопрягаться с поверхностями других деталей. Методы обработки основаны...
-
Затраты на обработку можно определить, пользуясь следующей зависимостью: руб., , стр. Где масса заготовки, кг.; масса детали, кг.; 0,55 стоимость...
-
Введение. - Разработка маршрута обработки поверхности деталей
Точность деталей машин характеризуется отклонением действительных размеров элементов детали от заданных (погрешности размеров), отклонениями формы...
-
Токарный станок с ЧПУ RAIS T250 CNC Fanuc 0i-Mate TB Токарный станок с ЧПУ RAIS Т250 CNC Fanuc 0i-Mate TB с наклонной станиной предназначен для...
-
При определении остаточных напряжений используется теория стержней, основанная на гипотезе плоских сечений. Остаточное напряженное состояние...
-
Стратегия ускорения социально-экономического развития страны предусматривает всемерную интенсификацию производства на основе научно-технического...
-
Комплексная деталь "вал-шестерня" предназначена для передачи вращательного момента на другой вал. Вал-шестерня состоит из 8 ступеней. Первая - 40h9,...
-
Токарная обработка Токарная черновая обработка Данному виду обработки подлежат следующие поверхности: - линейные - 3, 6, 21, 24; - диаметральные - 4, 7,...
-
Одним из основных элементов манипулятора является привод. В условиях повышенных требований к вакуумной гигиене широкое применение в качестве приводов...
-
Оценка технологичности детали по точности выполняется с учетом среднего квалитета точности (формула 4.1) и коэффициента точности обработки (формула 4.2)....
-
Существует значительное многообразие деталей, отличающихся размерами, формой, качественно-технологическими характеристиками. Для того чтобы создать общие...
-
Таблица 4 - Режимы термообработки Операция T, °С Охлаждающая среда HRC Цементация 930 Охлаждение медленное в колодцах или ящиках Закалка 820 - 840...
-
Влажно-тепловая обработка полотен, купонов и деталей - Разработка детского платья
Влажно-тепловая обработка (В. Т.О.) трикотаж имеет большое значение для придания устойчивости линейного размера купона и полотна и изготавливаемых из них...
-
Механическая обработка - обработка изделий из стали и других материалов с помощью механического воздействия с применением резца, сверла, фрезы и другого...
Исследование глубины дефектного слоя обрабатываемой детали при электроэрозионной обработке