Окислительное дегидрирование метилового спирта в присутствии катализаторов - Аналитический обзор получения формалина
Другим способом получения формальдегида является окислительное дегидрирование метилового спирта в присутствии катализаторов. Последние можно разделить на две группы:
- 1)металлическая медь или серебро в виде металлической сетки или осажденные на инертном высокопористом носителе (например, на пемзе). 2)оксидные катализаторы, например окисные железо-молибденовые, в некоторых случаях с присадками оксидов других металлов (магния, марганца, кадмия).
Существует множество вариантов технологического оформления процесса окислительного дегидрирования метанола в формальдегид. Однако принципиально все методы основаны на пропускании смеси паров метилового спирта с воздухом над катализатором при повышенных температурах.
Окислительная конверсия метанола в присутствии раскаленной меди (сетка, спирали, трубки) относится к числу старейших химических процессов. В 20-х годах многими исследователями было показано, что серебро и его сплавы более эффективны в качестве катализаторов, чем медь. В последующие годы серебряные катализаторы полностью вытеснили медные, хотя патенты на применение катализаторов на основе меди продолжают появляться и в самое последнее время.
Окислительная конверсия метанола на серебре проводится при соотношении метанол: воздух выше верхнего предела взрывной концентрации, то есть при большом избытке метанола по отношению к кислороду.
Известно, что активность многих катализаторов можно повысить внедрением небольших количеств веществ, которые сами по себе для данного процесса - яды. Типичными каталитическими ядами для серебряных контактов, являются пентакарбонил железа, соединения серы, фосфора, мышьяка, галогенов, селена, теллура и др. некоторые из этих веществ - эффективнейшие модификаторы. Большое распространение приобрело модифицирование серебряного катализатора различными металлами и их оксидами. Так, было выявлено промотирующее действие оксидов цинка, бериллия, циркония, сурьмы (III), марганца (VI), железа (VI), кальция, натрия, титана в той или иной степени ингибируют процесс окислительного дегидрирования метанола [4].
Введение в серебро 10% магния, меди и кадмия увеличивает дегидрирующую способность катализатора, повышая тем самым общую конверсию метанола, а присутствие селена и сурьмы увеличивает селективность процесса. Существенно пониженной каталитической активностью обладают сплавы серебра с цинком, галлием и германием. Сплавы серебра с алюминием, теллуром, оловом по сравнению с чистым серебром также проявляют пониженную активность. Для сплавления с серебром рекомендуется платина (0,45-0,75%).
Есть указания на целесообразность применения в качестве добавок и оксидов некоторых металлов: молибдена (VI) (141), титана (IV), магния и кальция. В последнем случае массовая доля серебра составляет от 5 до 30% от всего катализатора. Предложено использовать в качестве добавок к серебру пероксиды щелочных и щелочноземельных металлов, а так же соли серебра - карбонаты и оксалаты. Однако сведений о практическом применении сплавов и модифицирующих добавок пока нет.
По мнению некоторых исследователей, конверсию метанола можно повысить, практически без потерь селективности, если слой катализатора секционировать. Наибольший эффект был получен при использовании многослойных с ненанесенным катализатором. Применение системы из нескольких слоев серебра, обладающего высокой теплопроводностью, по-видимому, позволяет в значительной мере уменьшить адиабатический разогрев.
Сущность метода состоит в парофазном окислении гидрировании метанола кислородом воздуха в адиабатическом реакторе с последующим поглощением продуктов реакции водой. В процессе подается метаноло-воздушная смесь состава выше верхнего предела взрываемости (36,4% - объемные доли) и с недостатками кислорода по химическому уравнению окисления метанола в формальдегид, т. к. катализатор - окислительно-дегидрирующийся:
СН3ОН + ЅО2 > СН2О + Н2О + Q (147,4кДж/моль)
СН3ОН > СН2О + Н2 - Q (93,4 кДж/моль)
Н2 + ЅО2 > Н2О + Q (241,8 кДж/моль)
Вместе с тем протекают побочные реакции, что снижает выход формальдегида и повышает расход метанола:
СН3ОН+1,5O2 > СО2+2H2O+Q
СН3ОН+Н2 > СН4+H2O+Q
СН2О > СО+Н2+Q
СН2О+O2 > СО2+H2O+Q
Выход формальдегида достигает 80 - 85%, при степени конверсии метанола 85 - 90%. Так как окислительное дегидрирование проводят при недостатке кислорода, процесс глубокого окисления, не получает значительного развития. В то же время само дегидрирование, инициируемое кислородом, протекает быстрее, поэтому процент побочных реакций не велик. Этим способом можно получить формалин двух марок: ФМ - 37% с содержанием метанола до 10% и ФБМ - 50% с содержанием метанола менее 1%. Транспортировке и хранению подлежит формалин марки ФМ, т. к. метанол стабилизирует его.
Технологическая схема производства формальдегида окислительным дегидрированием метанола изображена на рисунке 2.
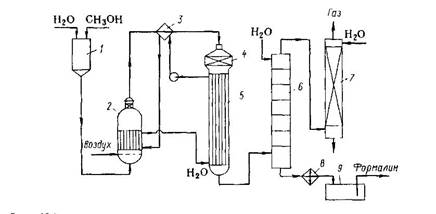
Рисунок 2 - Технологическая схема производства формальдегида окислительным дегидрированием метанола: 1 - напорный бак; 2 - испаритель; 3 - перегреватель; 4 - реактор; 5,8 - холодильники; 6 - абсорбер; 7 - скруббер; 9 - сборник.
Метанол, содержащий 10--12 % воды, из напорного бака 1 непрерывно поступает в испаритель 2. Туда же через распределительное устройство подают воздух, очищенный от пыли и других загрязнений. Воздух барботирует через слой водного метанола в нижней части испарителя и насыщается его парами. В 1 л образующейся паровоздушной смеси должно содержаться ? 0,5 г метанола. Поддержание такого состава смеси очень важно для обеспечения взрывобезопасности и нормального протекания процесса. Поэтому работа испарительной системы полностью автоматизирована: поддерживают постоянные уровень жидкости в испарителе, ее температуру (48 - 50°С) и скорость подачи воздуха, благодаря чему обеспечиваются необходимые температурный режим и степень конверсии в адиабатическом реакторе.
Паровоздушная смесь проходит брызгоуловитель, находящийся в верхней части испарителя, затем перегреватель 3 и поступает в реактор 4, в средней части которого находится катализатор. Реакционные газы сразу же попадают в подконтактный холодильник 5 (смонтирован вместе с реактором), где происходит быстрое охлаждение смеси и предотвращается распад формальдегида. В разных схемах охлаждение осуществляют проточной водой или паровым конденсатом, когда холодильник играет роль генератора пара низкого, среднего или даже высокого давления. Полученный пар (или горячая вода) служит для перегрева поступающей смеси в перегревателе 3 и для обогрева испарителя 2.
Охлажденные реакционные газы поступают в абсорбер 6, выполненный в виде тарельчатой колонны; жидкость на тарелках охлаждают внутренними или выносными холодильниками (на схеме не изображены). Абсорбер орошают таким количеством воды, чтобы в кубе получился 36 - 37 %-й формалин. Стадии абсорбции и разделения продуктов оформляют двумя разными способами.
По одному из них в абсорбере поглощают как формальдегид, так и не превращенный метанол, который содержится в продуктах реакции в количестве, как раз достаточном для стабилизации формальдегида. В этом случае верхнюю тарелку абсорбера охлаждают рассолом, а колонна 7 служит лишь для санитарной очистки газа, в то время как для получения безметанольного формалина (требуемого иногда для различных целей) необходима установка для отгонки метанола.
При втором способе в абсорбере поглощают преимущественно формальдегид; тогда скруббер 7 служит для абсорбции метанола, который отгоняют от воды и возвращают на реакцию. В обоих случаях формалин из куба абсорбера 6 охлаждают в холодильнике 8 и собирают в сборнике 9 [1].
Первое подробное исследование по получению формальдегида из метанола в присутствии смеси оксидов железа и молибдена проведено в начале 30-х годов.
Каталитическая активность оксидов металлов (т. е. конверсия метанола) меняется в ряду MoO3 <TiO2 < Fe2O3 < Cr2O3 < NiO < V2O5 < Mn2O3 < CuO < Co3O4, а селективность по формальдегиду почти в обратной последовательности: Co3O4< CuO < Fе2O3 < Mn203 < Cr203 < NiO < V2O5 < TiO2 < MoO3. Однако наибольшей эффективностью по обоим показателям обладают катализаторы, содержащие избыточный оксид. В этом случае наблюдаются следующие последовательности: по активности -- MoO3 <Na <Sr ? Ni <Pb < Ba < Cd < Co < Ca < Bi < Cr < Fe, а по селективности -- Ва ? Sr < Ni < Ca < Bi ? Pb < Co < Cd < Cr ? Fe.
На практике в качестве катализатора наибольшее распространение получила смесь оксидов железа(III) и молибдена(VI) МоО3 с атомным соотношением молибдена к железу от 1,7 да 2,5. Готовят катализатор соосаждением подходящей соли железа (III), например, хлорида или нитрата, с молибдатом аммония. Окисные катализаторы значительно менее чувствительны к примесям, чем серебряный и его аналоги.
Окисление метанола на оксидных катализаторах протекает по окислительно - восстановительному механизму:
СН3ОН + 2МоО3 > СН2О + Н2О + Мо2О5
Мо2О5 + ЅО2 > 2МоО3
Процесс осуществляется в избытке воздуха при (350 - 430) єС и обычном давлении, иначе под действием метанола и формальдегида катализатор быстро восстанавливается. Реакция протекает при соотношении метанола и воздуха ниже предела взрываемости (7 - 8% - объемные доли).
Процесс отличается высокой степенью конверсии метанола - 99%, а так же сильной экзотермичностью, что заставляет использовать трубчатые реакторы с охлаждением. Этот способ позволяет получать формалин - 37% с содержанием метанола не выше 0,5%. Применение технологий с оксидным катализатором заслуживает некоторого предпочтения, когда требуемая производительность не выше 8 - 10 тыс. т./год. Выход формальдегида на окисных катализаторах высокий -- достигает 90% и более [3].
Сопоставляя достоинства и недостатки обоих методов, естественно предположить, что первые можно объединить, а вторые, в известной мере уменьшить, если вначале пропустить метанол через серебряный, а затем через оксидный контакт. Первое предложение было сделано Пэйном. На первой секции предлагалось поместить кристаллическое серебро, а на второй (но ходу сырья) -- оксидный железо молибденовый катализатор. Поскольку реакция на серебряном катализаторе проводится в недостатке, а на оксидном в избытке кислорода, к смеси газообразных продуктов, выходящей из секции, добавляется расчетное количество воздуха. Как следует из описания патента, суммарная мольная конверсия метанола после обеих секций составляет 99,1% при мольной селективности образования формальдегида 90,5%. В других патентах для второй секции рекомендуются окисные катализаторы, содержащие оксиды фосфора, висмута, молибдена и др.
Комбинированная система из трегерного серебряного и оксидного железомолибденового катализатора обеспечивает практически полную конверсию метанола при мольной селективности около 90%. Содержание формальдегида в контактном газе составляет 17--20%, что приближается к соответствующему значению для односекционного реактора с серебром (21 - 23%) и значительно превосходит этот показатель для односекционного реактора с оксидным контактом (6--8%). Однако практическая реализация комбинированного катализатора встречает ряд трудностей. Так перепад температур между секциями достигает 400°С и более, что сложно реализовать в одном блоке. Обращает на себя внимание большая разница в объемах катализатора на первой и второй секциях (? в 25 раз). При добавлении воздуха и смеси газообразных продуктов из первой секции необходимо перейти через область взрывных концентраций.
Похожие статьи
-
В настоящее время производственные методы получения формальдегида большим разнообразием не отличаются. Так, в реакциях восстановления СО и СО2 Водой...
-
Метиловый спирт [30] - Разработка технологической схемы получения анизола и крезола
Молекулярная формула CH3OH Молярная масса 32,04 г/моль Внешний вид бесцветная жидкость Свойства Плотность и агрегатное состояние 791,8 кг/м?,...
-
При использовании разомкнутых химико-технологических систем в большинстве случаев принципиально невозможно проведение процессов при практически полной...
-
Технологические свойства формалина - Аналитический обзор получения формалина
Формалин - 37% водный раствор формальдегида, в нем формальдегид присутствует в виде гидрата HCHO-H2O и низкомолекулярных полимеров...
-
Применение формалина - Аналитический обзор получения формалина
Формалин используется в производстве: - синтетических смол; - синтетического каучука; - поверхностно-активных веществ; - многоатомных спиртов; - формалей...
-
Таблица 2 - Структура сырья в производстве метанола, %. Сырье В мире Беларусь и Россия Природный газ 73,8 70,7 Нефть и нефтепродукты 24,4 4,0 Отходы...
-
Один из способов повысить селективность - это правильно подобрать катализатор. Рассмотрим этот метод, на примере получения анизола и крезола. Анизол и...
-
Введение - Разработка технологической схемы получения анизола и крезола
Известно в некоторых случаях невозможно достичь высокой селективности химико-технологических процессов. Это происходит вследствие наличия побочных...
-
Получение синтезированного газа - Анализ и технологическая оценка химического производства
Химические методы переработки нефти проводят при высоких температурах без катализатора (термический крекинг), при высоких температурах в присутствии...
-
ПОЛУЧЕНИЕ ОБЖИГОВОГО ГАЗА ИЗ КОЛЧЕДАНА. - Получение серной кислоты
Суммарную реакцию обжига колчедана можно представить в виде реакции (I), где ?Н=-853,8 кДж?моль FeS2, или 7117 кДж ?кг. Фактически она...
-
Получение спиртов - Химические свойства и характеристики спиртов
Некоторые из показанных выше реакций (рис. 6,9,10) обратимы и при изменении условий могут протекать в противоположном направлении, приводя к получению...
-
Качественные методы анализа - Разработка технологической схемы получения анизола и крезола
Рециркуляционных реакционно-ректификационных процессов. При анализе сложных ХТС, характеризующихся большим числом параметров и переменных необходимо...
-
Данные для расчета: Основная реакция: (1) Побочные реакции: Рабочий объем катализатора - 24 м3. Расход оксида углерода и метанола на побочные продукты с...
-
Активность и селективность катализатора - Гомогенный и гетерогенный катализ
Все процессы переработки углеводородного сырья сопровождаются фазообразованием (испарение, катализ, крекинг и др.). Одна из задач физико-химической...
-
Действие на организм, Получение аммиака - Аммиак
Аммиак сильно раздражает слизистые оболочки уже при 0,5%-ном содержании его в воздухе. Острое отравление аммиаком вызывает поражения глаз и дыхательных...
-
Макрокинетика процесса - Каталитический риформинг
Характерной особенностью всех модификаций риформинга является то, что одна из его основных стадий - ароматизация - эндотермична, а другая - гидрокрекинг...
-
ПОЛУЧЕНИЕ ОБЖИГОВОГО ГАЗА ИЗ СЕРЫ. - Получение серной кислоты
При сжигании серы протекает необратимая экзотермическая реакция (II) с выделением очень большого количества теплоты: ?H = -362,4 кДж/моль, или в...
-
Одно дерево бразильской гевеи в среднем, до недавнего времени, было способно давать лишь 2-3 кг каучука в год; годовая производительность одного гектара...
-
Принципы получения гибридных соединений на основе квантовых точек и органических хромофоров В литературе для получения соединений, обладающих...
-
Теоретические основы каталитического пиролиза - Пиролиз углеводородного сырья
Теоретические основы процесса каталитического пиролиза в настоящее время изучены недостаточно. В качестве активных компонентов катализаторов для пиролиза...
-
Получение тиосульфата натрия при мышьяково-содовой очистке газов - Тиосульфат натрия
В процессе очистки от сероводорода коксового и других промышленный газов мышьяково-содовым методом, помимо основной реакции: Протекают побочные реакции,...
-
1. Спирты реагируют со щелочными металлами (Na, K и т. д.) с образованием алкоголятов: 2R--OH + 2Na 2R--ONa + H2 Реакция протекает не так бурно, как при...
-
Получение, Физические свойства, Химические свойства - Кальций и его биологическая роль
Свободный металлический кальций получают электролизом расплава, состоящего CaCl2 (75-80 %) и KCl или из CaCl2 и CaF2, а также алюминотермическим...
-
ПРОМЫШЛЕННОЕ ПОЛУЧЕНИЕ УГЛЕВОДОРОДОВ - Происхождение горючих ископаемых
Алканы, алкены, алкины и арены получают путем переработки нефти (см. ниже). Уголь тоже является важным источником сырья для получения углеводородов. С...
-
АБСОРБЦИЯ ТРИОКСИДА СЕРЫ. - Получение серной кислоты
Последней стадией процесса производства серной кислоты контактным способом является абсорбция триоксида серы из газовой смеси и превращение его в серную...
-
Обзор литературы - Синтез пара-нитродифенила. Теоретические основы нитрования
Нитрование - введение нитрогруппы - NO2 в молекулы органических соединений. Может проходить по электрофильному, нуклеофильному и радикальному механизмам;...
-
Гомогенный и гетерогенный катализ. Механизм действия катализатора - Основы химии
При гомогенном катализе катализатор и реагирующие вещества образуют одну фазу (газовая смесь или раствор). При гетерогенном катализе катализатор и...
-
Аналитический обзор - Выпаривание раствора хлорида калия
Устройство выпарных аппаратов. Разнообразные конструкции выпарных аппаратов применяемых в промышленности, можно классифицировать по типу поверхности...
-
В конце XIX в. началось промышленное производство молочной кислоты при участии молочнокислых бактерий Lactobacillus delbrueckii, L. leichmannii и L....
-
Закономерность управления процессом для реакции - Каталитический риформинг
Управлять ХТП - это означает, меняя технологические параметры процесса (температуру, давление, состав сырья, катализатор, скорость перемешивания,...
-
Обзор литературы, Роль лизина в питании человека и животных - Этапы получения лизина
Роль лизина в питании человека и животных Лизин (б, е-диаминокапроновая кислота) - незаменимая основная алифатическая аминокислота. Это специфичная...
-
Процесс получения винилхлорида сбалансированным методом из этилена состоит из шести стадий: 1. синтез 1,2-дихлорэтана прямым жидкофазным хлорированием...
-
Метод окислительного хлорирования этана - Технология получения винилхлорида
Идея использовать этан для синтеза винилхлорида была реализована в 1965--1967 годах на опытном производстве компаний The Lummus Co. и Armstrong Cork Co.....
-
Экономические показатели процесса можно улучшить и за счет комбинирования двух других способов производства винилхлорида: из этилена и ацетилена, когда...
-
Существует два основных способа получения полиарилатов: переэтерификация и взаимодействие хлорангидридов карбоновых кислот с двухатомными фонолами. 1....
-
Впервые в мире синтез изопрена из изобутилена и формальдегида в промышленном масштабе был осуществлен в СССР В 1964-1965 гг. В 1917 г. голландский химик...
-
Газотранспортные процессы, в основе которых лежат обратимые химические реакции, широко применяются для получения эпитаксиальных структур...
-
КОНТАКТНОЕ ОКИСЛЕНИЕ ДИОКСИДА СЕРЫ. - Получение серной кислоты
Реакция (III) окисления диоксида серы характеризуется очень высоким значением энергии активации и поэтому практическое ее осуществление возможно лишь в...
-
Синтез бромэтана проводили в соответствии с методикой, изложенной в источнике [2]. ХОД РАБОТЫ - Приготовление исходных реактивов и собирание прибора Рис....
-
Бромистый этил представляет бесцветную прозрачную жидкость, обладающую эфирным запахом и сначала сладким, потом жгучим вкусом. Кипит при 38,4°С. В воде...
Окислительное дегидрирование метилового спирта в присутствии катализаторов - Аналитический обзор получения формалина