Окисление природного газа и низших парафинов - Аналитический обзор получения формалина
Одним из способов получения формальдегида является окисление природного газа и низших парафинов.
Данный способ с точки зрения доступности и дешевизны сырья, а также простоты технологии (получение формальдегида прямым окислением природного газа, состоящим в основном из метанола, кислородом воздуха) заслуживает предпочтения перед сравнительно сложными и много ступенчатыми синтезом через метанол (по схеме):
Природный газ > синтез газ > метанол > формалин
Однако на практике возникает ряд трудностей, которые связаны с недостаточной устойчивостью формальдегида в условиях реакции. Окисление метанола происходит при 600 єС, в то же время термическое разложение формальдегида наблюдается уже при 400 єС. Образовавшийся формальдегид, кроме того, в присутствии кислорода, легко подвергается дальнейшему окислению. В силу этих причин на практике окисление метана проводят при малых значениях конверсии, причем и в этих условиях селективность образования формальдегида не высока. Выход формальдегида не превышает 3% при селективности 10 - 25%. Поэтому рассмотренный метод занимает весьма скромное место в балансе производства формалина и только в перспективе используется новые технологические приемы окисления (с учетом возрастания дефицитности метанола и сравнительной доступности природного газа) [4].
С целью интенсификации процесса окисления предложен целый ряд гетерогенных катализаторов. При 600-700°С ускоряющее действие на превращение метана, по-видимому, оказывают многие твердые материалы, например алюмосиликаты, кварц и т. п., благодаря наличию геометрически и энергетически неоднородных участков поверхности и, в особенности, кислотных центров. Реакцию можно проводить как в стационарном, так и в кипящем слое. Для повышения активности алюмосиликаты пропитывают растворами кислот, например фосфорной, борной. Значительное число работ посвящено применению контактов, на которые нанесены оксиды различных элементов, главным образом металлов. Контакт, представляющий собою шарики из алюмосиликата диаметром 0,75 мм (катализатор для крекинга нефтепродуктов), на которые было нанесено 1,5% оксида железа(III), обеспечивал выход формальдегида 1,8- 1,9% на пропущенный метан, а катализатор с 3--7% оксида магния 2,1--2,3%. Несколько более высокие показатели были получены с катализатором, в котором в качестве носителя применился алюмосиликат, содержащий 10--11% оксида алюминия, а в качестве активного компонента - фосфат церия (2%) и оксид фосфора (0,05-0,06%). В этом случае при 750°С выход формальдегида составлял 2,6% [7].
Отдельную группу составляют трегерные катализатopы на основе металлов I группы, а также палладия. Так, в присутствии катализатора 0,5% Pd/Al203, и небольших добавок галогеналкилов конверсия метана при 480°С составила 22,6%, а селективность образования формальдегида 34%. Трегерные контакты, содержащие медь или серебро, по-видимому, сходны с катализаторами окислительной конверсии метанола.
Окисление углеводородов С2-С4 в сравнении с окислением метана имеет много общего хотя и характеризуется некоторыми специфическими особенностями. Как и в случае метана, процесс проводят в области выше верхнего предела взрывных концентраций углеводородов.
Выход формальдегида несколько возрастает при замене воздуха чистым кислородом. Одновременно увеличивается количество и других продуктов окисления. Доля формальдегида, образующегося при окислении бутана, несколько выше по сравнению с пропаном и изобутаном. Более высокая реакционная способность позволяет проводить реакцию при значительно более низких температурах, как правило, не выше 400--480°С. В результате этого удается в значительной мере избежать образования продуктов полного окисления, т. е. оксида и диоксида углерода. Однако селективность образования формальдегида мало отличается от окисления метанола, поскольку в силу самого строения молекул углеводородов С2-С4 при их окислительной конверсии образуется практически весь ассортимент соответствующих альдегидов, кетонов, спиртов и т. д. Для преимущественного образования соединений того или иного класса успешно применяют различные многофункциональные катализаторы.?
Первая промышленная установка по получению формальдегида и других кислородсодержащих продуктов окислением смеси простейших алканов была сооружена в г. Толланте (США) в 1926 г. [6]. Окислению подвергался газ, содержащий 25% этана. Судя по патентному описанию, процесс проводится при 430-480 °С и давлении от 0,7 до 2 МПа, в присутствии твердого катализатора, представляющего собой смесь фосфата алюминия с оксидами металлов. Сконденсированный жидкий продукт содержал 34-36% метанола, 20-23% формальдегида и 5-6% ацетальдегида, а также небольшие количества ацетона, метилаля, воды и т. д.
Технология окисления пропана, бутана или их смесей, разработанная фирмой Celanese Chemical Corp., была реализована в г. Бишоп (Техас, США) в 1946 г. Исходное сырье (в данном случае - бутан) смешивают с воздухом и водяным паром в массовом соотношении 1 : 5 : 34 и пропускают через реактор, нагретый до 400°С, под давлением 2--3 МПа. Принципиальная схема производства формальдегида и других кислотосодержащих продуктов окисления пропан-бутановой фракции представлена на рисунке 3.
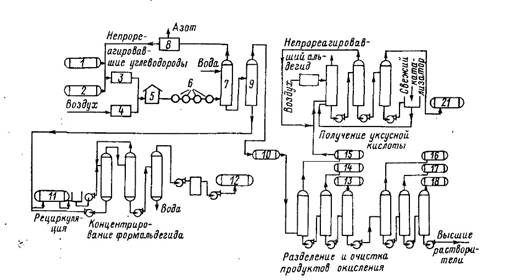
Рисунок 1.3 - Принципиальная технологическая схема производства формальдегида и других кислородсодержащих продуктов окисления пропан-бутановой фракции:1, 2 - сырьевые емкости (для пропана и бутана); 3, 4 - компрессоры; 5 - реактор; 6 - теплообменник; 7 - скруббер; 8 - газосепаратор; 9 - ректификационная колонна;10 - сборник для органических продуктов окисления; 11 - сборник для разбавленного раствора формальдегида; 12 - сборник для 37%-ного раствора СН20; 13 - сборник для метанола; 14 - сборник для ацетона; 15 - сборник для адетальдегида; 16 - сборник для нзопропилового спирта; 17 - сборник для пропанола; 18 - сборник для бутиловых спиртов; 19 - компрессор; 20 - реактор для окисления ацетальдегида; 21 - сборник для ледяной уксусной кислоты.
Окисление проводится в отсутствие катализатора при времени прибывания смеси в реакторе 1,15 с. На выходе из реакторной печи продукты реакции охлаждаются до 150 °С вспрыскиванием воды. Охлажденные реакционные газы под давлением направляются в орошаемый водой скруббер, где из них извлекаются кислородсодержащие продукты реакции. Оставшийся газообразный поток направляется в масляный абсорбер, также работающий под давлением, где поглощаются непревращенные углеводороды. Водный раствор продуктов реакции направляется в ректификационную колонну, в качестве погона которой отбираются все органические вещества, кроме формальдегида, а из куба -- разбавленный водный раствор последнего. Этот раствор направляется на систему концентрирования, состоящую из трех колонн, в которой концентрация формальдегида доводится до 37%. Из смеси органических продуктов последовательно выделяются ацетальдегид (направляется на окисление в уксусную кислоту), ацетон, метанол, пропанол, бутанолы и "высшие растворители". Помимо обычной ректификации, в процессе находит применение экстракция, адсорбция, а также азеотропная и экстрактивная ректификация. Соприкасающаяся с водными растворами аппаратура изготовлена из нержавеющей стали. В примере баланса продуктов, взятого из патента фирмы Celanese, указывается, что из 100 кг бутана получают 15,2 кг формальдегида, 19,6 кг ацетальдегида, 19 кг метанола, 7 кг ацетона, 1 кг пропанола, 0,5 кг бутанола и 11,4 кг карбоновых кислот. Производительность установки по сырью составляет 700 т/сут.
Из приведенного примера следует, что доля получаемого формальдегида по отношению к остальным продуктам составляет всего 20,6%, причем метанол и ацетальдегид образуются в больших количествах. Относительный выход метанола возрастает при повышении давления.
При окислении углеводорода С3-С5 в жидкой фазе получаются преимущественно карбоновые кислоты, а формальдегид практически не образуется [4].
Похожие статьи
-
Другим способом получения формальдегида является окислительное дегидрирование метилового спирта в присутствии катализаторов. Последние можно разделить на...
-
В настоящее время производственные методы получения формальдегида большим разнообразием не отличаются. Так, в реакциях восстановления СО и СО2 Водой...
-
Технологические свойства формалина - Аналитический обзор получения формалина
Формалин - 37% водный раствор формальдегида, в нем формальдегид присутствует в виде гидрата HCHO-H2O и низкомолекулярных полимеров...
-
Применение формалина - Аналитический обзор получения формалина
Формалин используется в производстве: - синтетических смол; - синтетического каучука; - поверхностно-активных веществ; - многоатомных спиртов; - формалей...
-
Получение синтезированного газа - Анализ и технологическая оценка химического производства
Химические методы переработки нефти проводят при высоких температурах без катализатора (термический крекинг), при высоких температурах в присутствии...
-
Процессы окисления. - Методы очистки и получения коллоидных растворов
Наряду с серой в реакциях окисления обычно образуются политио-новые кислоты, главным образом пентатионовая кислота H2S5O6 Реакции двойного обмена....
-
При использовании разомкнутых химико-технологических систем в большинстве случаев принципиально невозможно проведение процессов при практически полной...
-
Таблица 2 - Структура сырья в производстве метанола, %. Сырье В мире Беларусь и Россия Природный газ 73,8 70,7 Нефть и нефтепродукты 24,4 4,0 Отходы...
-
Полимеризация двуокиси азота. Переработка нитрозных газов в азотную кислоту обычно происходит при температурах от О до 50 °С. В этих условиях двуокись...
-
Процессы, основанные на микробиологической ферментации, разработаны и для получения ряда других органических кислот. Среди них -- глюконовая кислота и ее...
-
Метиловый спирт [30] - Разработка технологической схемы получения анизола и крезола
Молекулярная формула CH3OH Молярная масса 32,04 г/моль Внешний вид бесцветная жидкость Свойства Плотность и агрегатное состояние 791,8 кг/м?,...
-
КОНТАКТНОЕ ОКИСЛЕНИЕ ДИОКСИДА СЕРЫ. - Получение серной кислоты
Реакция (III) окисления диоксида серы характеризуется очень высоким значением энергии активации и поэтому практическое ее осуществление возможно лишь в...
-
Принципы получения гибридных соединений на основе квантовых точек и органических хромофоров В литературе для получения соединений, обладающих...
-
При пропускании смеси окиси углерода (СО) и водорода (Н2) над нагретым до 2000С катализатором, содержащим восстановленное железо, образуются смеси...
-
Обзор литературы, Роль лизина в питании человека и животных - Этапы получения лизина
Роль лизина в питании человека и животных Лизин (б, е-диаминокапроновая кислота) - незаменимая основная алифатическая аминокислота. Это специфичная...
-
Аналитический обзор - Выпаривание раствора хлорида калия
Устройство выпарных аппаратов. Разнообразные конструкции выпарных аппаратов применяемых в промышленности, можно классифицировать по типу поверхности...
-
ПОДГОТОВКА ОБЖИГОВОГО ГАЗА К КОНТАКТНОМУ ОКИСЛЕНИЮ. - Получение серной кислоты
Подготовка обжигового газа к контактному окислению заключается в удалении из него примесей, присутствие которых может вызвать затруднения при проведении...
-
Конденсационные методы получения коллоидных систем - Методы очистки и получения коллоидных растворов
Из классификации дисперсных систем по размеру частиц следует, что коллоидные растворы (золи) занимают промежуточное положе-ние между молекулярными и...
-
Мы обнаружили интересный факт в опытах с соляной кислотой (опыты 6,7, таблица 4). Оказалось, что в солянокислой восстановительной среде йод, выделившийся...
-
Что такое гравиметрический фактор F - Основы аналитической химии
Если мы знаем A - навеску анализируемой пробы, b - массу осадка и его состав, то мы можем вычислить содержание определяемого вещества X . X = a*F*100/b...
-
В данной главе мы рассмотрим получение тиосульфата натрия. Поскольку тиосульфат натрия широко используется в медицине, промышленности, фотографии. То...
-
Фенол - Разработка технологической схемы получения анизола и крезола
Фено?л (оксибензол, устар. карболовая кислота) C6H5OH -- бесцветные игольчатые кристаллы, розовеющие на воздухе из-за окисления, приводящего к...
-
Взаимодействие водорода со сложными веществами, Получение водорода - Свойства водорода
Водород проявляет восстановительные свойства и в реакциях со сложными веществами: 1) Восстановление оксидов металлов, стоящих в электрохимическом ряду...
-
Технологическое оформление процесса получения винилхлорида сбалансированным по хлору методом Первой стадией этого комбинированного процесса является...
-
Схема реакции: Реактивы: Тимолфталеин, триэтиламин, хлороформ, дихлоангидрид терефталевой кислоты, гексан. Оборудование: Прибор для поликонденсации при...
-
Получение продукта конденсации карбамида и формальдегида холодным способом - Поликонденсация
Реактивы: Карбамид - 60 г (1 моль); формальдегид 40%-ный - 130 г (1,75 моля); уротропин - 3-4 г, щавелевая кислота - 0,3 г. Оборудование: Трехгорлая...
-
Один из способов повысить селективность - это правильно подобрать катализатор. Рассмотрим этот метод, на примере получения анизола и крезола. Анизол и...
-
Введение., Способы получения перхлоратов - Производство перхлоратов в промышленности
Получение перхлората калия или перхлоратов вообще имеет большое значение для промышленности. Ведь перхлораты широко используются как в проведении...
-
Впервые в мире синтез изопрена из изобутилена и формальдегида в промышленном масштабе был осуществлен в СССР В 1964-1965 гг. В 1917 г. голландский химик...
-
Практическое применение - Йодометрия
Йодометрия является весьма универсальным методом. Йодометрически можно определять восстановители, окислители, кис-лоты и вещества, не обладающие...
-
Окисление органического вещества, Получение хлорной воды, Окисление фосфора - Свойства галогенов
При направлении струи хлора из газоотводной трубки на бумагу, смоченную скипидаром мы наблюдаем С10H16 + 8Cl2 > 10C + 16HCl Вывод: Окисление...
-
Получение спиртов - Химические свойства и характеристики спиртов
Некоторые из показанных выше реакций (рис. 6,9,10) обратимы и при изменении условий могут протекать в противоположном направлении, приводя к получению...
-
Получение тиосульфата натрия при мышьяково-содовой очистке газов - Тиосульфат натрия
В процессе очистки от сероводорода коксового и других промышленный газов мышьяково-содовым методом, помимо основной реакции: Протекают побочные реакции,...
-
Схема реакции: Реактивы: Фенолфталеин - 3,18 г; дихлорангидрид изофталевой кислоты - 2,03 г (мольное соотношение 1:1); едкий натр - 0,8 г;...
-
Существует два основных способа получения полиарилатов: переэтерификация и взаимодействие хлорангидридов карбоновых кислот с двухатомными фонолами. 1....
-
Качественные методы анализа - Разработка технологической схемы получения анизола и крезола
Рециркуляционных реакционно-ректификационных процессов. При анализе сложных ХТС, характеризующихся большим числом параметров и переменных необходимо...
-
ПОЛУЧЕНИЕ ОБЖИГОВОГО ГАЗА ИЗ КОЛЧЕДАНА. - Получение серной кислоты
Суммарную реакцию обжига колчедана можно представить в виде реакции (I), где ?Н=-853,8 кДж?моль FeS2, или 7117 кДж ?кг. Фактически она...
-
Введение - Разработка технологической схемы получения анизола и крезола
Известно в некоторых случаях невозможно достичь высокой селективности химико-технологических процессов. Это происходит вследствие наличия побочных...
-
Получение., Применение. - Свойства фтора как химического элемента
Источником для производства фтора служит фтористый водород, получающийся в основном либо при действии серной кислоты H2SO4 на флюорит CaF2, либо при...
-
КОНТАКТНЫЙ МЕТОД ПОЛУЧЕНИЯ СЕРНОЙ КИСЛОТЫ. - Получение серной кислоты
Рассмотрим процесс получения серной кислоты контактным методом из двух видов сырья: серного (железного) колчедана и серы. Получение H2SO4 из колчедана....
Окисление природного газа и низших парафинов - Аналитический обзор получения формалина