Обрубка отливок - Выбор способа получения отливки для конкретных деталей из различных литейных сплавов, назначение оборудования и оснастки
Обрубка отливок заключается в отделении от нее литников, выпоров, прибылей и заливов по разъему формы и в местах сопряжения стержневых знаков с формой.
Основными факторами, определяющими выбор способа обрубки, является вязкость сплава, из которого изготовлена отливка, масса отливки и серийность производства.
Для отличающихся хрупкостью серого и белого чугунов удаление литников не представляет трудности и производится ударом по литнику молотком. В отдельных случаях могут быть использованы пневматические зубила и для массового производства - отламывание на прессах.
Для
Для крупных отливок чаще используют ацетиленокислородную резку.
В условиях массового производства для отрезки прибылей и, реже, литников могут быть применены токарные станки, работающие с поперечной подачей.
Большинство цветных сплавов отличается вязкостью, что исключает применение ударов в связи с возможным короблением отливок. В этом случае широко применяются ленточные пилы, хотя не исключена возможность использования токарных станков и прессов.
Очистка отливок заключается в удалении пригара и улучшении чистоты поверхности.
Очистку можно производить галтовкой, дробеметной, дробеструйной, вибрационной и электрохимической обработкой, а зачистку - абразивными кругами и электроконтактным методом.
Выбор оборудования для очистки в основном зависит от размеров отливок и серийности производства.
Очистку галтовкой применяют для средних отливок, для чего в барабан, футерованный внутри броневыми листами загружают отливки и звездочки из белого чугуна и с помощью опорно-приводных роликов барабан приводят во вращение. Перекатываясь, отливки трутся друг о друга и о звездочки и очищаются от пригара.
В массовом производстве применяют барабаны непрерывного действия (приходные), а в серийном - периодического действия.
Для очистки средних и крупных отливок из черных сплавов широко применяют дробеметные барабаны и камеры. В дробеметные барабаны отливки загружают через окно загрузки-выгрузки на пластинчатый транспортер. При движении транспортера отливки перекатываются, подставляя различные поверхности под струю стальной или чугунной дроби, подаваемой дробеметной головкой. Дробь вместе с песком собирается в воронке днища и после отделения от песка на магнитном сепараторе подается в оборотную систему. Для крупных отливок массой свыше 50 кг вместо барабанов применяют камеры, куда отливки подаются подвешенными на крючьях и в которых по ходу движения расположены дробеметные головки.
Для мелких отливок, как правило полученных методом литья по выплавляемым моделям, применяют вибрационную, химическую и электрохимическую очистки.
Порядок выполнения работы
- 1 Ознакомиться с заданием практической работы и по своему варианту выбрать исходные данные (таблица 3); 2 Изучить общую характеристику литейного производства и способы изготовления отливок; 3 Сделать вывод о проделанной работе.
Задание
- 1 Проанализировать чертеж заданной детали; 2 Выбрать и описать несколько методов литья для получения данной отливки; 3 Определить оптимальный метод в зависимости от типа производства и материала детали; 4 Выбрать оборудование для обрубки и очистки отливок. 1 Деталь Шестерня изготавливается из стали 35Л - это литейная сталь; производство детали массовое, габаритные размеры: Ш 120х25 мм; средняя толщина стенки отливки - 20мм. (рисунок 1).
Поверхности детали, подвергающиеся механической обработке, условно обозначаются знаком. Остальные поверхности механической обработке не подлежат, на что указывает знак () в правом углу эскиза.
Для шестерни обрабатываемыми поверхностями являются: венец зубчатого колеса 1; отверстие 2; зубья 3.
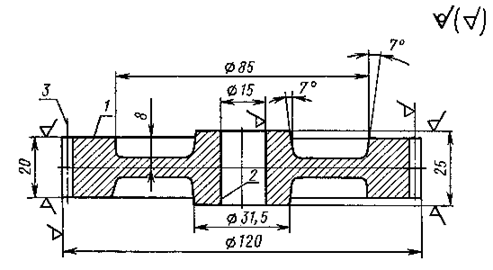
Рисунок 1 - Шестерня: материал - сталь 35Л, производство - массовое
- 2 Для изготовления отливки шестерни подходят методы: литье в кокиль и центробежное литье на машинах с вертикальной осью вращения. 1) При литье в металлические формы (кокиль) расплавленный металл заливают в многократные металлические формы под действием сил тяжести расплава.
В качестве материала для металлических форм применяют серый чугун, углеродистую сталь, алюминиевые сплавы. Толщина стенок кокиля составляет от 20 до 100 мм и зависит от толщины стенок отливки.
Литьем в кокиль получают фасонные заготовки из серого, ковкого и высокопрочного чугунов, сталей, алюминиевых, магниевых и медных сплавов в массовом и крупносерийном производстве (блоки и головки блоков двигателей, поршни из алюминиевых сплавов, ступицы колес из ковкого чугуна, станины электродвигателей из серого чугуна, стойки плуга из высокопрочного чугуна, крышки, втулки из медных сплавов и др.).
Достоинства процесса:
- - повышенные точность и качество поверхности отливки; - повышенные механические свойства металла (кроме чугуна). Прочность возрастает на 50-70%, пластичность в 3-4 раза; - отсутствие формовочных материалов и их переработки; - резкое уменьшение отходов производства; - высокая производительность в условиях массового производства: до 50 циклов в час на однопозиционных машинах, до 120 циклов в час на многопозиционных машинах и автоматических линиях; - возможность полной автоматизации процесса. - более благоприятные условия труда по сравнению с литьем в песчаные и оболочковые формы.
Недостатки процесса:
- - образование отбела при литье серого и высокопрочного чугунов, анизотропность свойств по сечению отливок из других сплавов; - низкая стойкость кокиля (100 - 2000 заливок) при литье черных сплавов (в то время как при литье цветных сплавов стойкость достигает 100 000 заливок); - сложность получения тонкостенных отливок вследствие быстрого затвердевания металла; - ограничение отливок по размерам (до 1000 мм) и массе (до 100 кг). 2) При центробежном способе литья расплавленный металл заливают во вращающуюся форму. Процессы заливки металла, а также его кристаллизации протекают под влиянием центробежных сил.
При необходимости во вращающуюся металлическую форму вставляют песчаные стержни, с помощью которых можно получать сложные наружные или внутренние поверхности отливки.
Для регулирования температуры металлических форм используют водяное, как правило, струйное охлаждение.
Центробежным способом получают тела вращения (кольца, втулки, гильзы цилиндров двигателей, заготовки для поршневых колец, вкладыши для подшипников, трубы, венцы, шестерни, бандажи, колеса, фланцы, шкивы, маховики), а также фасонные отливки из стали, чугуна, алюминиевых, магниевых, медных и цинковых сплавов.
При получении центробежным способом фасонных заготовок используют, как правило, песчано-глинистые, оболочковые формы, а также формы по выплавляемым моделям и др.
Масса литых заготовок при центробежном литье составляет от нескольких десятков грамм (при литье в резиновые формы) до 60т, диаметр - до 1500мм, длина - до 10м.
Достоинства центробежного литья:
- - возможность получения пустотелых отливок без стержней; - экономия металла (до 30 и более процентов) на литниковой системе; - повышенные механические свойства наружных слоев отливки; - возможность полной автоматизации и роботизации; - относительно благоприятные условия труда.
Недостатки центробежного литья:
- - низкие точность и качество внутренней поверхности отливок; - высокая неоднородность структуры металла (ликвация); - - низкая стойкость изложниц при литье черных сплавов; - недостаточная производительность при литье небольших отливок на машинах с горизонтальной осью вращения (10...15 отливок в час); - образование отбела при литье чугуна в металлические вращающиеся формы-изложницы. 3 Исходя из материала детали, типа производства шестерни оптимальным методом производства отливки будет литье В кокиль.
Так как необходимо получить высокую точность и высокое качество поверхности отливки, что возможно благодаря литью в кокиль. Отпадет необходимость в формовочных материалах, уменьшаются отходы производства. Достигается высокая производительность в условиях массового производства, появляется возможность полной автоматизации процесса. Условия труда более благоприятные по сравнению с литьем в песчаные и оболочковые формы.
4 Для обрубки Литников, выпоров, прибылей и заливов применим пневматическое зубило, так как масса стальной отливки не велика. Технические данные: Длина с зубилом 300 - 400 мм. Масса ударника 0,2 - 0,6 кг. Частота ударов 1100 - 2120 в минуту. Производительность: До 15 - 20 м на швах толщиной 4 - 6 мм.
Для очистки пригара и улучшении чистоты поверхности отливки применим дробеметный ленточный барабан. Технические данные: Расход дроби 3 - 5 кг/т. Вместимость барабана 0,3 - 0,7 т. Диаметр барабана 0,7 - 1,2м. Производительность: до 4000кг.
Содержание отчета
- 1 Тема и цель работы; 2 Оснащение; 3 Задание, чертеж детали и ее анализ; 4 Выбор И описание нескольких методов литья для получения данной отливки; 5 Определение оптимального метода в зависимости от типа производства и материала детали; 6 Выбор оборудования для обрубки и очистки отливок; 7 Выводы по работе.

Похожие статьи
-
Литье в оболочковые формы применяется для изготовления сложных тонкостенных отливок из черных и цветных сплавов. Сущность процесса заключается в...
-
Сущность процесса заключается в заливке расплавленного металла и формировании отливки под давлением 0,1 - 0,8 МПа. Способ позволяет автоматизировать...
-
Это способ получения фасонных отливок в металлических формах, при котором заполнение формы и кристаллизация металла производится под принудительным...
-
Сущность процесса, заключается в свободной заливке расплавленного металла в металлическую форму - кокиль. Для получения внутренних полостей отливок...
-
Основной продукцией литейного производства являются сложные (фасонные) заготовки деталей, называемые отливками. Отливки получают заливкой расплавленного...
-
Состав материалов должен обеспечивать получение в отливке заданных физико-механических и физико-химических свойств; свойства и структура должны быть...
-
Литье в песчано-глинистые формы Для изготовления песчаной формы используют модельный комплект, опочную оснастку и формовочные материалы. В модельный...
-
Характеристики методов получения заготовок Вопросы по теме: Производство заготовок литьем. Производство заготовок пластическим деформированием. Получение...
-
При центробежном литье сплав заливается во вращающиеся формы. Формирование отливки осуществляется под действием центробежных сил, что обеспечивает...
-
Характер производства Для мелкосерийного и единичного производства характерно использование в качестве заготовок горячекатаного проката, отливок,...
-
Основные положения к выбору способа литья - Технология конструкционных материалов
При выборе способа литья для получения заготовки в первую очередь должен быть рассмотрен вопрос экономии металла. Металлоемкость можно снизить...
-
Таблица 1. Приспособления, инструмент для разборочно-сборочных работ Наименование инструмента Обозначение инструмента Стандарт Ключ гаечный с открытым...
-
Определение припусков на механическую обработку Припуски назначают по ГОСТ Р 53464-2009 Основные припуски на мех. Обработку назначают для каждого допуска...
-
Общая характеристика литой детали Габаритные размеры 308 х 308мм, масса отливки 22.7 кг, средняя толщина стенок 17 мм, сплав - чугун марки СЧ15-32 ГОСТ...
-
Основными промышленными методами получения порошков на основе титана и циркония являются следующие: А) метод металлотермического восстановления; Б)...
-
Технологическая часть, Выбор способа изготовления отливки - Проект цеха стального литья на 10000 т
Произведем анализ конструкции отливки "Кронштейн передней рессоры задний". Отливка по конструкции несложная, компактная. Толщина стенок по всей длине...
-
Валики удвоителя работают при постоянных статических нагрузках на износ. В связи с этим их изготавливают их высокопрочной и износостойкой стали 50Х....
-
В зависимости от типа производства (массовое, серийное, единичное) и требований к качеству изделия выбирают способ изготовления изделия - горячее...
-
Магниевые сплавы. - Технологическое оборудование литейных цехов
При плавки необходимо защищать эти сплавы от окисления и насыщения водородом, так как это приводит образованию микропористости в оливках. Плавку литейных...
-
Выбор метода и способа получения заготовки Необходимость экономии материальных ресурсов предъявляет высокие требования к рациональному выбору заготовок,...
-
Характеристика способов горячего формования - Изготовление деталей из пластмасс
Литье под давлением применяют для изготовления деталей из термо - и реактопластов. При литье под давлением (рис.16) материал в гранулированном или...
-
Литье в металлические формы - Изготовление отливок в песчаных формах. Специальные способы литья
Литье в металлические формы (кокили) получило большое распространение. Этим способом получают более 40% всех отливок из алюминиевых и магниевых сплавов,...
-
Выбор вида, способа и формы получения заготовки Метод получения заготовки указан в чертеже - это отливка. Точность отливки - класс 7т-5 по ГОСТ 26645-85,...
-
Т. к. партия изготовляемых деталей составляет 400шт. Производство не крупносерийное; материал детали не литейная сталь, в исключительных случаях...
-
Песчаная литейная форма для получения отливки
1. Выбор способа получения заготовки Материал заготовки: Чугун Марка материала: СЧ 20 Предел прочности при растяжении, МПа 200 Твердость по Бринеллю HB,...
-
Выбор материала при проектировании конструкции кузова инновационного подвижного состава обусловлен тенденций современного вагоностроения направленного на...
-
Сущность метода и область применения. Сущность заключается в том, что вместо разовой песчано-глинистой используют металлическую форму, называемую...
-
Алюминиевые сплавы. - Технологическое оборудование литейных цехов
В зависимости от видов сырья, масштабов и специфики производства для плавки алюминиевых сплавов применяют в основном тигельные, отражательные и...
-
Сборка литейной формы Включает: установку нижней полуформы; установку стержней, устойчивое положение которых обеспечивается стержневыми знаками; контроль...
-
Выбрана боковая литниковая система расположенная в плоскости разьема. Литниковая система состоит из: воронки, стояка, шлакоуловителя, и питателя. Расчет...
-
Электроискровую обработку применяют для повышения точности и уменьшение шероховатости поверхностей, обработанных электроэрозионным методом. Метод основан...
-
Выбор материала и технология производства заготовок деталей и инструментов
ВЫБОР МАТЕРИАЛА И ТЕХНОЛОГИЯ ПРОИЗВОДСТВА ЗАГОТОВОК ДЕТАЛЕЙ И ИНСТРУМЕНТОВ Цель работы - провести анализ условий работы заданного изделия, выбор...
-
Классификация моделей Модели классифицируются по размерам. Модель отливки "Кронштейн", относится к малым моделям. При проектировании данной отливки была...
-
Способы изготовления отливок. Изготовление отливок в песчаных формах - Способы изготовления отливок
Для изготовления отливок служит литейная форма, которая представляет собой систему элементов, образующих рабочую полость, при заливке которой...
-
Введение - Технологическое оборудование литейных цехов
Литейное производство - одно из древнейших ремесел, освоенных человечеством. Первым литейным материалом была бронза. В древности бронзы представляли...
-
Приготовление расплава Приготовление литейных сплавов связано с плавлением различных материалов. Для получения заданного химического состава и...
-
Для литья под давлением обычно используют не первичные, а вторичные сплавы, что обусловлено экономическими соображениями. Наилучшими литейными свойствами...
-
Литейные сплавы - Заготовительное и литейное производство
1. Чугун является наиболее распространенным материалом для получения фасонных отливок. Чугунные отливки составляют около 80 % всех отливок. Широкое...
-
Анализ технологичности литой детали - Проблема повышения качества отливок
Под технологичностью литой детали подразумевают вариант ее конструкции с надежными эксплуатационными качествами, обеспечивающий удобство ее изготовления...
-
Успешное выполнение ремонта в значительной мере зависит от качества разборки. Разборочный процесс принято изображать в виде технологической схемы. При...
Обрубка отливок - Выбор способа получения отливки для конкретных деталей из различных литейных сплавов, назначение оборудования и оснастки