Контрольно-измерительные приборы и автоматика - Характеристика реконструкции компрессорного цеха
Контрольно-измерительные приборы, применяемые на компрессорной станции
Для осуществления контроля различных технологических параметров на КС используется определенный комплекс контрольно-измерительных приборов (КИП).
Для контроля температуры природного газа, воздуха, воды, масла и баббита подшипников ГПА на КС используются:
- - ртутные термометры, с помощью которых измеряется температура в различных точках по месту установки технологического оборудования; - электроконтактные манометрические термометры общепромышленного исполнения ТПП-СК и взрывозащищенные ТПП 4-1У - как датчики-реле с дискретным выходом в системах автоматического управления и как показывающие приборы по месту их установки; - термометры сопротивления медные ТСМ и платиновые ТСП как первичные преобразователи; - вторичные приборы различных конструкций и назначений, с помощью которых совместно с термометрами сопротивления осуществляют непрерывный или периодический контроль температуры (сигнализацию, показания, регистрацию) и автоматическое управление.
Основным параметром, определяющим экономические и режимные показатели ГПА, КС и магистрали, является производительность (расход). Для определения расхода газа в качестве исходного параметра берется объемная производительность, определяемая при помощи различных автоматических измерительных систем (например, "СИГНАЛ -1М").
Контроль вибрации подшипников ГПА осуществляется с помощью измерений вибросмещений, виброскоростей или виброускорений (в зависимости от типа применяемой аппаратуры). Аппаратура контроля вибрации обеспечивает показания параметров вибрации и формирует сигналы на защиту ГПА от превышения допустимых значений этих параметров. Защита по вибрации является одной из основных защит ГПА. Она резервирует действия других технологических защит ГПА: по перегреву подшипников, по осевому сдвигу, по понижению объемной производительности и по возникновению помпажа. Контроль уровня вибрации является обязательным для всех ГПА с центробежными нагнетателями.
Для обеспечения нормальной эксплуатации технологического оборудования КС предусматривается контроль уровня в различных резервуарах масла, воды и конденсата. В основном для этого применяются поплавковые устройства, с помощью которых обеспечивается визуальный контроль (показания) уровня по месту и сигнализация крайних значений, используемых в аппаратуре автоматического управления и регулирования (например, автоматического слива и долива жидкости).
Необходимое превышение давления масла уплотнения над давлением газа в полости нагнетателя (0,2 - 0,3 МПа) поддерживается автоматически с помощью РПД, который осуществляет постоянный сброс излишнего количества масла из системы уплотнения, таким образом, чтобы поддерживался заданный перепад "масло-газ".
Противопомпажная защита газоперекачивающего агрегата
Для устойчивой и надежной работы центробежных нагнетателей устанавливают специальные противопомпажные регуляторы, предотвращающие работу нагнетателя в помпажной зоне, и сигнализаторы помпажа. Противопомпажный регулятор предназначен для защиты нагнетателя от помпажа путем открытия перепускного клапана при уменьшении расхода или повышении сжатия. В этом случае происходит увеличение объемных расходов нагнетателя за счет перепуска части газа на вход нагнетателя. Противопомпажный регулятор состоит из измерителя расхода с золотником и измерителя перепада давления на нагнетании тоже с золотником. Работа измерителя расхода основана на использовании закона пропорциональности между гидравлическим сопротивлением входного патрубка и расходом.
Схема сигнализатора помпажа НЗЛ, реализующий данный принцип приведен в графической части выпускной квалификационной работы.
При нарушении равновесии сил, действующих со стороны большого сильфона 4, соединенного с верхним рычагом 3, и малого сильфона 1, соединенного с нижним рычагом 2, поворачивается ось верхнего рычага 3. Укрепленные на этом рычаге в масляной камере заслонка 9 и сопло 7 могут изменить давление в трубопроводе от 0,5 до 0,15 МПа, измеряемые электроконтактным манометром. В предпомпажной зоне заслонка 9 полностью открывает сопло 7. Это достигается путем настройки корректора 5. при открытом сопле 7 происходит замыкание контакта электроконтактного манометра и выдается импульс в систему сигнализаций или в цепь управления клапаном обводной линии. Недостатком сигнализаторов данного типа является прекращение их работы при наступлении помпажа.
Контроль осевого сдвига нагнетателя
Контроль осевого сдвига на центробежных нагнетателях всех типов электроприводных ГПА осуществляется с помощью устройства, состоящего из гидравлического реле и двух электроконтактных манометров (рис.7), контакты которых используются для подачи сигнала на защиту ГПА по осевому сдвигу ротора нагнетателя. Масляное реле осевого сдвига подает импульс на отключение привода нагнетателя при аварийном осевом сдвиге ротора (на 0,3-0,35 мм от установленной величины) и в случае выработки упорных колодок подшипника выше допустимой величины.
Назначение установки А-705-15-09М
Установка централизованного контроля и управления газоперекачивающими агрегатами, А-705-15-09М, предназначена для работы в составе систем автоматизации управления ГПА, компрессорной станции магистральных газопроводов, а также может быть использована для централизованного контроля и управления другими технологическими процессами, имеющими аналогичный объем контроля и алгоритмы управления.
Установка предназначена для выполнения следующих функций:
- 1. Предупредительная и аварийная, световая сигнализация, отклонений контролируемых параметров от значений установок с предоставлением информации на групповых и индивидуальных сигнальных индикаторах; 2. Автоматическая выдача команд на включение внешней звуковой сигнализации при отклонении параметров от предупредительных или аварийных уставок сигнализации; 3. Индикация прохождения этапов пуска, нормального или аварийного останова, а также нормального режима работы агрегата на табло индикации; 4. Индикация положения запорной арматуры и устройств агрегата на мнемосхеме объекта или табло индикации; 5. Регистрация событий, связанных с действиями оператора, или положения исполнительных механизмов, отклонениями значений параметров за значения аварийных установок сигнализации; 6. Непрерывное предоставление и регистрация в аналоговой форме текущих значений наиболее важных контролируемых параметров; 7. Непрерывное предоставление в аналоговой форме по вызову оператора текущих значений контролируемых параметров с помощью многоканального показывающего прибора; 8. Расчет в аналоговой форме значений ряда контролируемых параметров; 9. Формирование команд управления исполнительными механизмами, а также режимами пуска, нормального и аварийного останова с пульта управления; 10. Автоматическое управление пуском, нормальным и аварийным остановом и аварийной защитной сигнализацией; 11. Выдача ряда сигналов в аналоговый и дискретной форме, в цеховую систему контроля и управления; 12. Автоматический контроль исправности устройств, входящих в установку, контроль цепей питания, целостность датчиков и линий связи с исполнительными механизмами с соответствующими сигналами световой и звуковой сигнализацией, неисправности.
Установка предназначена для работы во взрывоопасных помещениях. Искробезопасность входных цепей установки обеспечивается применением устройств нормализации и сигнализации.
При исчезновении напряжения питания основной сети, установка осуществляет блокировку сигналов аварийных защит по каналам частоты вращения, вибрации и давления от аналоговых датчиков на время, заданное алгоритмом управления для восстановления этих функций при последующем после аварии появления основной сети в течение заданного времени. Если напряжение основной сети не восстанавливается в течение заданного времени, установка осуществляет аварийный останов агрегата. При исчезновении напряжения питания 220В 50Гц основной сети и при наличии резервных напряжений 220В и 27В постоянного тока, установка обеспечивает работоспособность агрегата с сохранением основных функций контроля, управления и защиты по каналам температуры с индикацией перехода на резервное питание.
Состав установки определяется числом и типом контролируемых параметров, объемом выполняемых функций в соответствии с требованиями автоматизации агрегата.
В состав установки входят следующие функционально и конструктивно законченные устройства: устройство нормализации и непрерывной сигнализации (УНС) А323-31-18; устройство логической обработки информации (УЛО) А353-33-02; устройство предоставления информации (УПИ) А690-06-09; устройство связи с объектом (УСО) А323-41-01; комплект кабелей; комплект ЗИП одиночный, к установке А705-15-09М; совместно с установкой поставляется комплект датчиков.
Устройство нормализации и непрерывной сигнализации - предназначено для преобразования (нормализации) сигналов первичных преобразователей постоянного тока, в унифицированный выходной сигнал 0 - 10В, в отрицательной полярности, пропорциональный значению контролируемого параметра (температура, давление и т. д.) и для сравнения унифицированных сигналов с уставками предельных значений параметров. УНС состоит из:
- - блоков преобразования (БП) постоянного тока с обычными или искробезопасными входами; - модулей преобразования (МП на 4 канала каждый) сигналов тока 0 - 20 мА в напряжение 0 -10 В; - блоков непрерывной сигнализации (БНС) на 40 каналов сигнализации; - блок питания основной (БПО); - блок питания резервный (БПР).
Градуировка, предел измерения, искробезопасность и число блоков питания определяется типом и числом датчиков, устанавливаемых на агрегате.
Структурная схема УНС содержит коммутационное поле. Это коммутационное поле позволяет задавать для каждого параметра, необходимое количество установок сигнализации. Подключение сигналов датчиков к блокам преобразования, осуществляется посредством клемных колодок, установленных в изотермических коробках на задней стороне УНС. Изотермическая коробка предназначена для выравнивания температуры холодных спаев термопары и медной катушки, компенсации Э. Д.С. холодных спаев, а также для подключения и пломбирования искробезопасных цепей.
УСО содержит приборы и устройства, преобразующие сигналы от датчиков вибрации, частоты вращения, осевого сдвига ротора нагнетателя и прочее, в унифицированные аналоговые сигналы и дискретные сигналы отключений указанных параметров от норм. Аналоговые сигналы используются в каналах индивидуального и группового представления параметров. Дискретные сигналы, выдаваемые из УСО в устройство логической обработки информации, используются для сигнализации отклонений контролируемых параметров от нормы, автоматического управления и аварийных защит агрегата. В стойке УСО размещаются:
- - электронный блок БЭ - 39-2 аппаратуры измерения, вибрации и оборотов ИВ-Д-ПФ; - счетчик импульсов СИ206-1ХЛ4, 24 В; - тахометрические системы ТЭ-АКСМ; - блоки питания БА.07-046; - блоки питания БА.07-048; - трансформаторы 220/170 В, Б-13.654.93; - автоматические выключатели; - блок контроля питания Б-12.622.86; - плата контроля Б-15.095.90; - сигнализатор нормального режима СНР;
Аппаратура измерения вибрации ИВ-Д-ПФ, предназначена для контроля вибрации опор двигателя и силовой турбины. Аппаратура формирует выходные аналоговые сигналы 0-5 В, пропорциональные текущим значениям вибрации, и обобщенные двухпозиционные сигналы предупредительной и аварийной сигнализации, о выходе вибраций за пределы установок. Аналоговые сигналы после преобразования в УНС к уровню 0-10 В, используются в каналах индивидуального и группового представления параметров на ВКУ; двухпозиционные сигналы используются в каналах защит агрегата в соответствии с алгоритмом управления.
Тахометрическая система ТЭ-АКСМ, предназначена для преобразования частоты вращения валов турбины низкого давления (ТНД), высокого давления (ТВД) и силовой турбины (СТ), в электрический аналоговый сигнал 0-10 В, пропорциональный частоте вращения, а также для формирования позиционных сигналов отключения частоты вращения за аварийные уставки, используемые в алгоритме управления агрегатом.
В состав системы ТЭ-АКСМ входят первичные преобразователи (ППТ), размещенные на агрегате, и вторичная аппаратура, размещаемая в УСО, в составе:
- - преобразователь частоты в аналоговый сигнал (ПТЛ); - сигнализатор частоты (ПТС); - сигнализатор останова (ПТО).
Аппаратура контроля вибросмещения и контроля осевого сдвига, состоит из преобразователя электромагнитного перемещения ВВТ-133, и вторичного прибора, размещенного в УСО. Аппаратура контролирует вибросмещение валов из ферромагнитных хромоникелевых сталей, в диапазоне от 10 до 250 мкм.
Преобразователь ВВТ-133, предназначен для работы во взрывоопасных помещениях всех классов, вторичный прибор, относится к электрооборудованию общего назначения.
Устройство логической обработки информации, предназначено для управления двухпозиционными механизмами в режимах автоматического пуска агрегата, нормального и аварийного останова, аварийной защиты и других операций, заданных алгоритмом управления.
Работа УЛО основывается на следующих принципиальных решениях:
- - хранение программы работы в энергозависимом запоминающем устройстве; - строго последовательное выполнение программы, повторяющееся циклически; - упрощенное программирование устройства за счет малого количества команд; - модульный принцип построения логического контроллера и блока ввода - вывода; - использование схем и способов резервирования для повышения надежности выдачи наиболее ответственных выходных воздействий; - введение аппаратных и программных средств контроля входных и выходных линий связи; - организация системы резервного питания.
Структурная схема УЛО включает:
- - нормализаторы входных высоковольтных и низковольтных двухпозиционных сигналов (Н); - коммутатор нормализованных высоковольтных и низковольтных входных двухпозиционных сигналов (КДС); - оперативную память (ОП); - блок реализации временных задержек - таймер (Т); - блок логики (БЛ); - постоянную память (ПП); - двоичный счетчик адресов ПП (С); - блок управления (БУ); - распределитель входных дискретных сигналов (РДС); - блоки входных реле (БВР); - модуль связи с УПИ (МС).
Блок логики, оперативная память, таймер и модуль связи с устройством предоставления информации - конструктивно размещены на одной плате и образуют логический процессор (ЛП) - блок экстренного аварийного останова (БЭАО).
Организация управления КС
Организация управления компрессорными цехами непосредственно зависит от типа ГПА, установленных в цехах, и места расположения диспетчерского пункта относительно КС. При использовании ГГПА из-за высокой температуры воздуха в помещении машинного зала местные щиты управления каждым агрегатом не устанавливаются, и вся информация о работе агрегата и управление им осуществляется с главного щита управления, размещенного либо на диспетчерском пункте КС, либо в аппаратной компрессорного цеха. Современная КС многониточного магистрального газопровода является сложным технологическим объектом, в состав которого входят несколько компрессорных цехов (КЦ), связанных общим режимом работы, и различные вспомогательные службы.
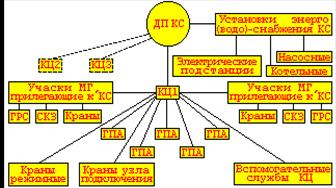
Рисунок 8 - Структура управления КС с диспетчерского пульта
[3] Для централизации контроля и управления процессами перекачки газа на каждой КС имеется диспетчерский пункт, с которого осуществляется управление технологическим и энергетическим оборудованием КС, а также прилегающими к КС участками магистрального газопровода (рис. 8). С диспетчерского пункта КС осуществляется управление КЦ, каждый из которых имеет свой главный щит управления. С главного щита управления каждого цеха осуществляется управление ГПА, кранами узла подключения, режимными кранами, вспомогательными службами компрессорного цеха, а также участками магистрального газопровода, прилегающими к КС с линейными кранами, станциями катодной защиты газопровода и ГРС.
Похожие статьи
-
Оборудование компрессорного цеха - Характеристика реконструкции компрессорного цеха
Оборудование компрессорного цеха до реконструкции Центробежный нагнетатель типа 280-12-7 (неполнонапорный) с выносным блоком маслосистемы предназначен...
-
Технологическая схема компрессорной станции - Характеристика реконструкции компрессорного цеха
Принципиальная схема коммуникаций, обеспечивающая проведение операций по перекачке, называется ТЕХНОЛОГИЧЕСКОЙ. Главное требование при разработке...
-
Расчет режима работы компрессорной станции - Характеристика реконструкции компрессорного цеха
Все расчеты выполнены в соответствии с требованиями нормативно-технической документации. 1. Определяем относительную плотность газа: , Где - плотность...
-
Введение - Характеристика реконструкции компрессорного цеха
Единственно возможным видом транспорта для природного газа является трубопроводный транспорт. Современные магистральные газопроводы большого диаметра...
-
1. Выбираем по таблице тип теплообменного аппарата АВЗ с наружной поверхностью охлаждения H = 10200 м2 и коэффициентом оребрения =14,6. 2. . Все расчеты...
-
Характеристика объекта и обоснование реконструкции КС "Долгое" относится к предприятию ООО "Газпром трансгаз Москва", является промежуточной...
-
Автоматический контроль за установкой осуществляется с помощью следующих приборов: - Температура в камере контролируется термометром манометрическим...
-
В настоящее время потребности пищевой промышленности в приборах для измерения расхода, массы и объема различных пищевых продуктов удовлетворяются в...
-
Основной характеристикой магнитного усилителя является зависимость действующего или среднего значения тока в нагрузке от тока управления: . Графическое...
-
В СИ с мультипликативной коррекцией погрешностей осуществляется выделение погрешностей СИ и управление ею коэффициентом преобразования СИ для минимизации...
-
Хотя габаритные размеры всех трех холодильников почти одинаковые, однако сильно отличается объем холодильной камеры и морозильного отделения. Таблица...
-
Столовая посуда . На предприятиях общественного питания используется посуда различных видов: фарфоровая, фаянсовая, керамическая, стеклянная,...
-
Указания по выполнению проекта - Автоматика и автоматизация технологических процессов
Схема автоматизации технологического процесса является основной частью проекта Она определяет структуру автоматического контроля и управления, а также...
-
ОБЩАЯ ХАРАКТЕРИСТИКА УСЛОВИЙ РАБОТЫ АВТОМАТИЧЕСКИХ СИСТЕМ - Надежность систем автоматизации
Автоматические системы, а также их отдельные элементы при эксплуатации находятся под воздействием различных факто-ров, которые будем называть нагрузками....
-
Характеристика устройств УЗП Питание Устройств заграждения переезда осуществляется от однофазной сети переменного тока напряжением 220 (+5%,-10%) В,...
-
К энергетическим характеристикам плазмотрона относятся зависимости параметров дуги от условий работы - рода плазмообразующего газа, давления,...
-
Диод Шоттки (назван в честь немецкого физика Baльтера Шоттки) - полупроводниковый диод с малым падением напряжения при прямом включении. Диоды Шоттки...
-
В процессе эксплуатации в стартере возникают главным образом механические повреждения привода, связанные с пробуксовкой муфты свободного хода, износом...
-
В качестве объектов для разработки схемы автоматического контроля и управления студентам предлагаются современные процессы переработки...
-
Формовочные машины классифицируют по методам: 1) уплотнения смеси; 2) удаления модели из формы; 3) приведения машины в действие. Классификация машин по...
-
Особенности выпечки булочных изделий. - Характеристика процесса хлебопечение
Изделия смазывают яйцом, яйца разводятся с водой в соотношении 1/1. Листы смазывают маслом, укладка изделий происходит на некотором расстоянии друг от...
-
В дополнение к количественным параметрам в некоторых случаях целесообразно нормировать направление неровностей, например в связи с направлением...
-
Для построения винтовых характеристик воспользуемся формулой: (1) Где - мощность, срабатываемая винтом; - скорость вращения винта; - постоянный...
-
Основная цель курсовой работы Основной целью курсовой работы является анализ работы судовой энергетической установки при заданных условиях эксплуатации,...
-
Целью курсового проекта является закрепление теоретических знаний по курсу "Системы управления технологическими процессами" ("Автоматика и автоматизация...
-
Краткая характеристика работ на копировально-фрезерных станках, Резцы-фрезы - Машинное гравирование
Копировально-фрезерный станок предназначен для выполнения копировальных работ на плоскости и по объему с использованием соответствующих копиров и...
-
Технологическая линия производства йогурта (Дополнение 1) состоит из следующего наименования оборудования: 1. Двухслойный резервуар 3000 л из пищевой...
-
Виды работ по техническому обслуживанию устройств автоматики на переезде Техническое обслуживание это комплекс операций по подержанию работоспособности...
-
Одним из основных элементов манипулятора является привод. В условиях повышенных требований к вакуумной гигиене широкое применение в качестве приводов...
-
Построение приборов для автоматического титрования
Построение приборов для автоматического титрования Все приборы для автомагического титрования характеризуются следующей обобщенной функциональной...
-
Кондиционеры предназначены для создания благоприятных температурно-влажностных условий в жилых и служебных помещениях. Кондиционеры классифицируют по...
-
Парк хранения очищенного конденсата обеспечивает буферное (промежуточное) хранение продукта в случае нарушения нормальной работы перерабатывающих...
-
Широкое внедрение автоматизации - наиболее эффективный путь повышения производительности труда. На многих объектах для организации правильного...
-
Стандарт BTX, который по прогнозам, в ближайшие два года станет основным форм-фактором при производстве персональных компьютеров, требует и новых систем...
-
Согласно [13] должны быть предусмотрены следующие мероприятия по обеспечению электробезопасности электроустановки: - режим контроля питающей сети; -...
-
В системе социально-экономических мероприятий, направленных на повышение благосостояния людей, важное место отводится развитию общественного питания....
-
Тип подъемника - канавный, передвижной Количество стоек - 1 Грузоподъемность одной стойки - 5 т. с. Скорость подъема - 10 мм/сек Высота подъема - 0,5 м...
-
Эффективным способом снижения действия помех, а, следовательно, и погрешностей в АЭП является фильтрация. Наиболее часто применяется линейная фильтрация....
-
Рис.2. Принципиальная схема сортировочно-инспекционного конвейера ТСИ Конвейер сортировочно-инспекционный ТСИ предназначен для сортировки плодов и ягод...
-
Средства измерений и вспомогательная аппаратура выбираются, в основном, из типовой аппаратуры, выпускаемой отечественной приборостроительной...
Контрольно-измерительные приборы и автоматика - Характеристика реконструкции компрессорного цеха