Расчет аппаратов воздушного охлаждения газа - Строительство головной компрессорной станции на Заполярном нефтегазоконденсатном месторождении
Параметры аппарата воздушного охлаждения:
- - поверхность теплообмена Fаво, м2, Fаво = 9860 м2; - число рядов nр, nр = 6; - длина труб, l, м, l = 12; - число ходов nх, nх = 1; - электродвигатель мощностью N, кВт, N =39 кВт; - объемный расход воздуха 1 вентилятора, ?, м3/с, ? = 125 м3/с.
Определим количество АВО газа n, шт.,
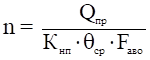
,
Где Qпр - количество тепла отдаваемое охлаждаемым газом, Вт,
Qпр = G Cp (),
Где G - расход газа через АВО, кг/ч,
G = ?ст-Qаво
Где Qаво - расход газа, млн. ст. м3/сут,
= 130,73 млн. м3/сут
G = 0,68130,73 = 88,8964 млн. кг/сут = 37,04105 кг/ч.
Ср - средняя изобарная теплоемкость газа, ккал/кгК,
Ср = 1,695 + 1,838 10-3 Тср + 1,96 106

Где Тср - средняя температура газа, К,

Тср = ,
Т - температура на входе АВО, К, = 322,5 К;
T - температура на выходе АВО, К,
Т= t1 + (10?15),
Где t1 - температура воздуха на входе в АВО, К,
T1 = Ta + ?Ta,
Где Та - среднегодовая температура окружающего воздуха, К, Та = 265К;
?Tа - поправка на изменчивость климатических данных, К, ?Ta = 5 К;
T1 = 265 + 5 = 270 К,
Т= 270 + 15 = 285 К,
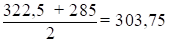
Тср = К,

Ср =1,695 +1,838-10-3-303,75 + 1,96-106 -=
= 1,45 кДж/кг-К = 0,346 ккал/кг-К,
Qпр = 37,04-105-0,346-(322,5 - 285) = 48059,4 кВт.
Кнп - коэффициент теплопередачи, отнесенный к полной поверхности оребренной трубы с учетом загрязнений, Вт/м2К, Кнп = 25 Вт/м2К;
- средний температурный напор, К,
= ??t,
Где - средний логарифмический температурный напор, К,
=

Где - температурный напор в начале аппарата, К,
= Т - t2,
Где t2 - температура воздуха на выходе из АВО, К;
T2 = t1 + ?t0 k?t,
Где ?tо повышение температуры воздуха при нормальных условиях, К,
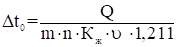
Где Q - количество тепла, передаваемого в аппарате, кВт, Qпр= 58032,76кВт;
? - объемный расход воздуха через один вентилятор, ? = 125 м3/с;
N - количество вентиляторов в аппарате, в зависимости от типа аппарата и длины труб, n = 6;
M - ориентировочное число АВО газа, m = 23;
Кж - коэффициент, учитывающий количество жалюзи; ввиду того, что жалюзи нет, принимаем Кж = 1;
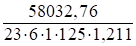
?tо = = 2,78 К,
K?t - поправочный коэффициент, зависящий от высоты местности над уровнем моря и температуры окружающего воздуха
K?t = 0,92
T2 = 270 + 2,78-0,92 = 272,6 К,
= 322,5 - 272,6= 49,9 К,
- температурный напор в конце аппарата, К,
= Т - t1
= 285 - 270 = 15 К,
= К,
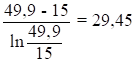
??t - поправочный коэффициент, зависящий от количества ходов.
Для определения поправочного коэффициента ??t, находим следующие вспомогательные величины,
R =


R = = 14,42
Р = .


Р = = 0,05.
??t=0,34
= -0,34 = 10,013 К,
Количество АВО газа n,
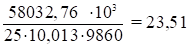
N = ,
Принимаем количество АВО равным n = 24.
К установке на площадке по результатам предварительного расчета потребуется 24 аппарата по типу АВГ-85 МГ для каждого КЦ.
Система подготовки газа собственных нужд.
Система подготовки газа собственных нужд предназначена для подготовки газа с целью использования его на собственные нужды КС и в качестве импульсного газа для управления пневмокранами.
Для качественной подготовки газа собственных нужд, принят блок-бокс разработки ЗАО "Уромгаз".
Производительность блока, м3/ч:
- - на котельную--470 - на водонагреватель "ВЕГА" - 60
Давление на входе в блок - 6,7 МПа (80 кг/см2).
Давление на выходе из блока - 0,6 МПа.
Температура на выходе из блока - плюс 100 °С.
Для подготовки импульсного газа для управления пневмоприводными кранами Ду 200 и менее и КИП предусмотрена установка подготовки импульсного газа автоматизированная (УПИГА).
Расчетный расход газа через УПИГ, Нм3/ч по импульсному газу 500 при давлении на входе в УПИГ 6,7 МПа (80 кг/см2).
Обеспечение ГПА маслом.
Для обеспечения маслом газоперекачивающих агрегатов предусматривается склад масла в таре.
Вместимость склада масла в таре согласно ОНТП 51185* (с изм. 1-7) должна обеспечивать подпитку ГПА маслом в течение шести месяцев, а также 50% запаса объема маслосистемы всех устанавливаемых ГПА.
Подача масла к маслобаку газоперекачивающих агрегатов предусматривается передвижная маслозаправочная установка.
Маслозаправочная установка по типу (МЗУ01-02) конструктивно выполнена для возможности эксплуатации при низких температурах окружающей среды в климатическом исполнении "ХЛ" и предназначена для восполнения безвозвратных потерь масла в маслобаках ГТД и ЦБ нагнетателя.
Для выполнения вышеуказанных работ производятся следующие операции:
- - прием масел в баки МЗУ из стационарных емкостей склада ГСМ с помощью стационарного насоса склада ГСМ или из бочек - переносными насосами - транспортирование масел в баках МЗУ - подогрев масел в баках МЗУ - заправка масел в баки ГТД
Основным конструктивным элементом МЗУ является маслонапорная станция (МНС), состоящая из двух раздельных гидравлических систем для разных типов масел, расположенная в термоконстантном фургоне прицепа.
МНС включает в себя два бака по 300 литров для каждой гидравлической системы, систему маслопроводов с фильтрами и запорной арматурой, а также насосы для перекачивания масел.
Конструкция присоединительных частей маслопроводов обеспечивает быстрое присоединение и отсоединение заправочных шлангов, а также исключает протечки масел во время заправки и операции отсоединения аправочных шлангов.
Все металлические элементы МНС, соприкасающиеся с маслом, выполнены из нержавеющей стали.
МЗУ снабжена системой контроля и сигнализации за основными параметрами, обеспечивающими работу установки -- уровнем масла в баках, давлением в трубопроводах, температурой масла в баках, а также системой автоматического поддержания необходимой температуры воздуха внутри фургона во время простоя в период низких температур наружного воздуха.
Для эффективного прогрева оборудования внутри фургона, а также для снижения теплопотерь при открывании дверей в зимний период, МЗУ снабжена воздушно - тепловыми завесами.
Выносной пульт управления, расположенный на наружной поверхности задней двери фургона, обеспечивает управление установкой без открывания дверей и полностью дублирует работу основного пульта управления, находящегося внутри фургона.
Для очистки масел в маслобаках газоперекачивающих агрегатов предлагается передвижная установка СОГ.
По эффективности очистки от механических загрязнений стенды СОГ эквивалентны 5-микронному авиационному фильтру, но на два порядка выше по грязеемкости. Кроме того, они способны удалять нерастворенную воду. Затраты на эксплуатацию стенда СОГ несоизмеримо малы по сравнению с использованием в процессе очистки жидкостей авиационного фильтра. Это важнейшее конкурентное преимущество по сравнению с традиционными способами очистки.
Компактность и мобильность стендов СОГ позволяют применять их непосредственно на рабочих местах около оборудования. Использование в конструкции сверхтвердых антифрикционных материалов для подшипников быстро вращающихся центрифуг обеспечивает высокую эксплуатационную надежность стендов.
Дренаж масел от ГПА должен предусматриваться в подземные дренажные емкости. Емкость может предусматриваться одна на цех или индивидуальная на каждый ГПА.
Похожие статьи
-
Плотность газа при рабочих условиях , Где Рн, Рвх -- соответственно атмосферное и рабочее (входное) давление, МПа, Рн = 0,1013Мпа, Рвх = Рк = 5,5МПа; Тн,...
-
К основным мероприятиям, обеспечивающим безопасное ведение работ, относятся: -выполнение периодического инструктажа всего персонала, участвующего в...
-
Головная компрессорная станция включает в себя три компрессорных цеха, с подключением каждого к своему магистральному газопроводу. Газ с узлов...
-
Защитные кожухи трубопроводов через автомобильные дороги и на переходах через водные преграды защищаются групповыми протекторными установками из...
-
Электрохимическая защита подземных коммуникаций ГКС на Заполярном НГКМ осуществляется с помощью подсистем коррозионного мониторинга "Пульсар-Л" (ООО...
-
Продолжительность строительства комплекса сооружений определена в календарном графике строительства исходя из очередности ввода основных объектов и...
-
Работающие должны быть снабжены спецодеждой установленного образца, спецобувью, средствами защиты от гнуса, а при работе на высоте - предохранительными...
-
В качестве источника воды для 1 и 2 очереди строительства служат существующие сети промбазы Заполярного НГКМ. Машинисты землеройных и дорожных машин,...
-
До начала свайных работ должен быть составлен ППР, предусматривающий выполнение следующих работ: - освещение территории строительной площадки, проезда и...
-
В связи с тем, что подключение ГКС ведется в непосредственной близости от Заполярного нефтегазоконденсатного месторождения и местности со сложным...
-
Климат района строительства субарктический, отличается суровой холодной зимой и непродолжительным дождливым летом со слабыми ветрами, область...
-
Основные объемы работ в составе первой и второй очереди строительства ГКС на Заполярном НГКМ составляют: - Подготовительные работы - Земляные работы -...
-
При производстве работ по монтажу стальных строительных конструкций, сборных бетонных и железобетонных конструкций необходимо руководствоваться главами...
-
Основные технологические решения Технология газотранспортных производств. Максимальная производительность ГКС 130,77 млрд. м3/год, в том числе 115 млрд....
-
Обилие осадков приводит к развитию озер и обширных заболоченных пространств. Общая заозеренность местности 2-5 %, местами до 10 % и более. Общая...
-
Поступающее технологическое нестандартное оборудование проходит комплектацию и ревизию на строительной базе, после чего доставляется в монтажную зону...
-
Фундамент трубопровод надземный здание Основные объекты и сооружения Проектом предусматривается строительство следующих объектов и сооружений: 1 очередь:...
-
Обеспечение строительства материальными ресурсами осуществляется согласно заключаемым договорам по согласованной Заказчиком транспортной схеме. Доставка...
-
При выполнении земляных работ следует руководствоваться главами СНиП 3.02.0187* "Земляные сооружения. Основания и фундаменты". Весь комплекс земляных...
-
Проектируемые дороги относятся к IV и V категории по СНиП 2.05.0285* "Автомобильные дороги". При прокладке постоянных дорог, укладку грунта следует вести...
-
Подсыпка площадки головной компрессорной станции на Заполярном НГКМ производится без снятия мохово-растительного слоя. По данным изысканий торф в местах...
-
Основным технологическим оборудованием головной компрессорной станции на Заполярном НГКМ являются газоперекачивающие агрегаты, предназначенные для...
-
До начала строительно-монтажных работ выполняются работы подготовительного периода: - досыпка песка и выравнивание площадки под расстановку передвижных...
-
Местонахождение объекта строительства В административном отношении проектируемые объекты и сооружения расположены на территории Тазовского района...
-
Потребность в рабочих кадрах на объекте ГКС на Заполярном НГКМ приведена в таблице. Нормативная трудоемкость с учетом административно-хозяйственного...
-
Организационно-технические противопожарные мероприятия должны выполняться согласно ГОСТ 12.1.00491 "Пожарная безопасность" Общие требования, ППБ 01-03...
-
Строительные машины, транспортные средства, производственное оборудование, средства механизации, приспособления, оснастка, инструмент и т. д. должны...
-
Система обеспечения качества Контроль качества строительства осуществляется со стороны государственных и органов контроля и надзора, техническим надзором...
-
Перечень строительных машин, механизмов и транспортных средств, необходимых для выполнения строительно-монтажных работ, представлен в таблице....
-
В точках дренажа и по трассам внутриплощадочных трубопроводов компрессорных цехов устанавливаются устройства КИП-Л, выполненные на базе стоек...
-
В качестве анодных заземлений применяются глубинные анодные заземления (ГАЗ), выполненные из малорастворимых анодных заземлителей "Менделеевец". При...
-
Структура строительства Строительство предусматривается осуществлять подрядным способом. Функции Заказчика строительства осуществляет инвестиционная...
-
Головная компрессорная станция на Заполярном нефтегазоконденсатном месторождении предназначена для поддержания давления 7,35 МПа в начале системы...
-
СНиП 12.03-2001 Безопасность труда в строительстве. Часть 1 .Общие требования; СНиП 12.04-2002 Безопасность труда в строительстве. Часть 2. Строительное...
-
Строительство фундаментов на площадке ГКС намечено осуществлять: - компрессорный цех №1 - по II принципу строительства - использование грунтов оснований...
-
Перед началом ведения земляных, монтажных и прочих работ на площадках и линейной части объекта, необходимо выполнить расчистку территории. Расчистка...
-
Проектирование электрохимической защиты подземных сооружений ГКС на Заполярном НГКМ выполнено на основании данных и анализа опыта эксплуатации средств...
-
Перед монтажом оборудования производится его внешний осмотр и проверка: - на соответствие оборудования проекту и заводской документации - комплектности -...
-
Потребность в рабочих кадрах для площадочных и линейных сооружений определена исходя из нормативной трудоемкости строительно-монтажных работ. Обеспечение...
-
Полная потребность в воде составляет: Результаты расхода воды заносим в таблицу Таблица 6 Процессы и потребители Ед. изм. Кол-во в смену Нормы расхода...
Расчет аппаратов воздушного охлаждения газа - Строительство головной компрессорной станции на Заполярном нефтегазоконденсатном месторождении