Эмали и покрытия, Технология эмалей и неорганических покрытий, Физико-химические основы эмалирования - Стекло и эмали
Технология эмалей и неорганических покрытий
Физико-химические основы эмалирования
Эмаль представляет собой стеклообразное (или преимущественно стеклообразное) вещество, в основном состоящее из оксидов, полученное плавлением или фриттованием (неполным плавлением), которое одним или несколькими слоями наносят на металлическое изделие. В технологии эмали существует та же проблема, что и при изготовлении металлостеклянных спаев -- согласование физико-механических характеристик металлической и оксидной систем для обеспечения их прочного сцепления и допустимого уровня напряжений в обеих составляющих. В связи с этим разные металлы эмалируют разными эмалями. Известно и общее требование: обычно формирование бездефектного покрытия и процессы, обеспечивающие сцепление, следует вести при вязкости эмали около 100 Па-с и поверхностном натяжении около 300 мДж/м2.
Химический состав эмали определяется назначением эмалевого покрытия и характеристиками защищаемого металла. Области применения эмалевых покрытий столь разнообразны, что выделение каких-либо общих физико-химических их характеристик, как и у стекол, невозможно. В отличие от стекла, структурные превращения в эмали оказывают значительно большее влияние на совокупность эксплуатационных свойств покрытия. Эти преобразования имеют существенное значение и для достижения прочного сцепления эмали в твердом состоянии с металлом.
Процессы, обусловливающие сцепление эмали с металлом, более подробно исследованы для черных металлов. В этом случае применяют эмали на основе щелочноборосиликатных стекол с введением в качестве способствующих адгезии и сцеплению оксидов переходных металлов -- кобальта, никеля, марганца, меди и т. д. (так называемых оксидов сцепления). Эти исследования привели к возникновению ряда гипотез (электрохимическая, механическая и др.), имеющих описательный характер и взаимно дополняющих друг друга. Начальными стадиями процесса, обеспечивающего сцепление твердой эмали с металлом, являются смачивание и химическое взаимодействие металла с эмалью или стекловидной составляющей неорганического эмалевого покрытия. А. А. Аппен показал целесообразность анализа при исследовании этого процесса следующих основных критериев: изобарных потенциалов реакций, протекающих в моноатомном пограничном слое и определяющих состав и строение новообразований на поверхности раздела соприкасающихся фаз; средних энергий единичных связей металл -- кислород (или другой анион), либо средних значений энергий атомизации соединений на поверхности раздела эмаль -- металл; нормальных электродных потенциалов на этой границе; степени недостроенности электронных оболочек атомов на границе раздела соприкасающихся фаз и статистического веса атомов со стабильными электронными конфигурациями; разрядного потенциала и плотности заряда на границе металл -- неорганический диэлектрик (стекло).
Во многих случаях сцепление определяется не столько этими критериями, сколько составом и свойствами переходного слоя толщиной в десятки микрометров, образующегося в результате взаимодействия эмали с металлом. Однако во всех случаях особо велика роль площади действительного контакта металла с эмалевым покрытием, которая зависит не только от состава эмали, но и от всей технологии формирования покрытия.
Первоначально целью эмалирования было создание декоративного эффекта, в основном, на изделиях из драгоценных металлов. Высокого художественного уровня декоративное эмалирование достигло в начале нашей эры в Византии, что оказало существенное влияние на развитие этой техники в других странах, в том числе и в Киевской Руси. При изготовлении украшений с использованием техники "перегородчатых" и "выемчатых" эмалей ювелир должен был решать задачу прочного соединения эмалей с металлами и обеспечить многообразие цветов и оттенков покрытия. Для изготовления эмалированных ювелирных изделий и в настоящее время применяют низкопробные сплавы драгоценных металлов, при их эмалировании можно использовать многообразные возможности окрашивания стекла.
Наряду с традиционным применением в качестве декоративных покрытий на изделиях бытового и технического назначения, эмалевые покрытия все в возрастающей степени призваны решать задачу антикоррозийной защиты металлов в самых разнообразных областях. Известно, что в результате коррозии ежегодно теряется около 10 % мирового выпуска черных металлов.
Развитие науки и техники связано с использованием все более высоких температур. По этой причине непрерывно возрастают требования к защите разнообразных металлов и, в первую очередь, жаропрочных сталей и сплавов от газовой коррозии, в особенности от окисления. Эту задачу призваны решать жаропрочные эмали и покрытия. Современная техника нуждается, например, в аппаратуре, работоспособной в парах серы до 1000°С, йода и иодидов -- до 1100°С, в хлоре и хлористом водороде--при 400--600°С, в парах пентоксида ванадия, содержащихся в продуктах сгорания и переработки нефти,--при 500--700°С. При таких высоких температурах многие стекла ведут себя не как твердое тело, а как высоковязкая жидкость, и не могут обеспечить длительной эксплуатации изделия. В указанных условиях работоспособными могут быть лишь кристаллические соединения. Таким образом, для решения подобных задач технология эмалирования должна использовать метод направленной кристаллизации эмалей или основываться на введении в покрытие при его формировании значительных количеств кристаллических огнеупорных наполнителей.
В то же время усиливающийся интерес вызывает и технология эмалирования легких сплавов, особенностью, которой является применение возможно более легкоплавких эмалей. Например, алюминий чистотой 99,5 % имеет температуру плавления 658°С, а температура плавления эвтектик в литейных алюминиевых сплавах лежит около 450°С. Таким образом, температура формирования эмалевого покрытия на этих сплавах должна существенно различаться, чтобы избежать деформации изделий. Особые трудности возникают при необходимости обеспечения электрической изоляции или антикоррозионной защиты полупроводниковых металлов -- кремния, германия и т. п., так как для сохранения их характеристик температура их нагрева не может превышать 300-350 °С.
При выборе металла и соответствующей эмали наряду с температурой плавления металла и температурой, обеспечивающей достаточно низкую вязкость эмали при формировании покрытия, следует учитывать и температуры, до которых работоспособны металлическая основа и эмаль. Ползучесть и рекристаллизация металла и релаксационные процессы в эмали могут приводить к изменению напряженного состояния системы, способного вызвать разрушения связи металл -- эмалевое покрытие. Другими важными факторами разрушения могут быть при более низких температурах тот или иной вид коррозии, при достаточно высоких температурах -- диффузионные процессы на границе раздела металл -- эмаль. Действие этих факторов проявляется во время эксплуатации покрытия; неблагоприятные напряжения могут вызвать разрушение покрытия уже в процессе его нанесения.
Величинами, определяющими напряженное состояние системы эмаль -- металл при заданной температуре, являются разница термических коэффициентов линейного расширения, соотношение модулей упругости и сдвига и толщины слоев металла и эмали. Значения указанных свойств материалов существенно изменяются с температурой. В случае стекла (эмали) эти изменения особенно значительны вблизи температуры стеклования, где ТКЛР, например, может возрастать в 2-Зраза.
Многие сплавы, особенно чугун, меняют свою структуру при нагревании до температуры формирования покрытия. Эти преобразования находят свое выражение в изменении не только ТКЛР, но и объема металла, что создает дополнительные трудности при эмалировании. Жаростойкие металлы, например, Та, Мо, Mb, W и V, и некоторые их соединения относительно легко окисляются на воздухе. Оксиды этих металлов, образующиеся на поверхности, летучи и непрочно связаны с металлом; рост пленки оксидов при обжиге покрытия и недостаточная скорость ее растворения в эмали часто являются причиной потери адгезии и отслаивания покрытия. Вместе с тем экспериментально установлено, что достаточно хорошее сцепление эмалевого покрытия с большей частью металлов достигается при обжиге в кислородсодержащей среде. В этом случае на поверхности образуется пленка из оксидов (например, железа), взаимодействующих с эмалью и растворяющихся в ней с образованием переходного слоя. При эмалировании черных металлов процесс сцепления стимулируют добавками в эмаль или на поверхность эмалируемого изделия указанных выше оксидов сцепления -- Ni2O5 И т. д. При обжиге в инертной атмосфере сцепление эмали с некоторыми металлами обеспечивается образованием переходного слоя, содержащего новые соединения, например, интер-металлиды.
За исключением эмалей на чистых драгоценных металлах, эмалевое покрытие представляет собой в основном трехслойную композицию металла, переходного слоя и слоя эмали. Напряженное состояние такой системы в области упругого состояния может быть достаточно точно рассчитано, причем, как правило, напряжения в металле невелики и не оказывают определяющего влияния на прочность композиции в целом.
Напряженное состояние эмалевого покрытия зависит от геометрии поверхности и эти зависимости также могут быть рассчитаны. Композиции могут разрушаться как вследствие рассмотренных нормальных напряжений, так и связанных с ними тангенциальных напряжений, особенно на выпуклых поверхностях.
При эксплуатации изделия в меняющихся температурных полях напряжения, возникающие вследствие различия свойств материалов, будут суммироваться с термоупругими напряжениями, возникающими из-за различий средних температур металла, переходного слоя и эмалевого покрытия. Коэффициенты тепло - и температуропроводности эмалей, как и всех стекол, существенно ниже, чем металлов. Поэтому во время охлаждения на поверхности эмалевого покрытия возникают опасные растягивающие напряжения. По этой причине характеристики эмалевого покрытия подбирают таким образом, чтобы при эксплуатации оно находилось под действием допустимых сжимающих нагрузок. Например, при эмалировании стали и чугуна переходный слой формируют при помощи так называемых грунтовых эмалей, а требуемых эксплуатационных характеристик покрытия достигают, применяя соответствующие покровные эмали.
При эмалировании наряду с достижением заданного напряженного состояния и адгезии необходимо получать бездефектные покрытия. Важное значение при этом имеют физико-химические процессы смачивания и растекания. Существенная роль принадлежит состоянию поверхности металла и составу газовой среды, в которой формируется эмалевое покрытие. О характере новообразований на поверхности раздела металл -- эмалевое покрытие, возникающих вследствие их химического взаимодействия при заданных температурах, можно судить на основе расчета изобарно-изотермических потенциалов вероятных химических реакций. В результате этих реакций образуются поверхностные фазы, заметно влияющие на процессы смачивания, растекания и сцепления, причем важную роль играет состав среды.
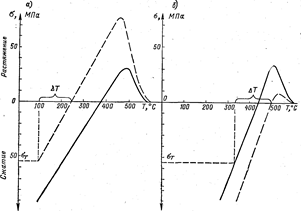
Рис. 33.1. Изменение напряжений в стекловидном эмалевом покрытии при изотермической выдержке (а) и при направленной кристаллизации (б)
-------- исходное покрытие; -- -- -- покрытие после термической обработки
Собственно процесс получения бездефектного покрытия определяется убылью свободной поверхностной энергии в системе в целом, т. е. в конечном счете, поверхностным натяжением на границах раздела металла, эмали и газовой среды при обжиге. Анализ этих явлений в практической технологии затруднен тем, что покрытие формируется в меняющемся температурном поле, и система не находится в состоянии равновесия. Несомненно, одно, что задачи, поставленные перед технологией эмалирования, требуют как учета состава и структур используемых материалов, так и целенаправленного осуществления технологического процесса.
Похожие статьи
-
Смеси следует приготовлять, как правило, в смесителях принудительного перемешивания. Разгрузку и подачу каменных материалов в приемные бункера...
-
Подготовка оснований под асфальтобетонные покрытия - Технология строительства дорожного полотна
Подготовка основания включает следующие операции: проверка качества основания и исправление имеющихся в нем дефектов, очистка поверхности основания от...
-
Классификация стекол по составу - Стекло и эмали
Согласно определению Комиссии по терминологии АН СССР (1932г.) "стеклом называются все аморфные тела, получаемые путем переохлаждения расплава независимо...
-
Устраивать бетонные покрытия и основания следует при температуре воздуха от +5о С до +30о С и перепаде температуры воздуха за сутки не более 12о С....
-
Технология устройства отделочных покрытии - Инженерная подготовка строительной площадки
Работы по устройству отделочных покрытий выполняют на завершающем этапе строительства зданий и сооружений. Их назначение - придать зданию законченный...
-
Технология устройства отделочных покрытии - Технологии в строительстве
Работы по устройству отделочных покрытий выполняют на завершающем этапе строительства зданий и сооружений. Их назначение - придать зданию законченный...
-
Технологическая карта составлена на производство работ по устройству внутриплощадочных автомобильных дорог из сборных железобетонных плит. В состав...
-
Устраивать покрытия и основания из щебня, обработанного по способу пропитки битумом, дегтем или эмульсиями, следует в сухую погоду при температуре...
-
Бинарные щелочно-силикатные стекла - Стекло и эмали
Бинарные щелочно-силикатные стекла систем Ме 2О-- SiО2 (где Me--Li, Na, К, Rb, Cs, Tl). Введение в состав стекла оксидов щелочных металлов приводит к...
-
Влияние сухого жаркого климата на технологию бетона Районы с сухим жарким климатом характеризуются большими перепадами температуры, относительной...
-
Технология устройства слоев увеличенной толщины должна соответствовать требованиям Руководства по строительству дорожных асфальтобетонных покрытий, а...
-
Устройство асфальтобетонных покрытий из горячих и теплых асфальтобетонных смесей допускается и в период, когда температура воздуха осенью ниже 10°С,...
-
Выбор защитного покрытия металлоконструкций от коррозии - Разработка схемы стального каркаса рамы
Не защищенная от действия влажной атмосферы, а иногда (что еще хуже) атмосферы, загрязненной агрессивными газами, сталь коррозирует (окисляется), что...
-
Микронеоднородное строение стекол - Стекло и эмали
Согласно современным представлениям, все однофазные стекла имеют микронеоднородное строение. Речь идет об образовании в структуре микрообластей размером...
-
Строительство покрытий с применением дерева - Технология строительства дорожного полотна
Для обеспечения временного проезда в условиях залесенной и болотистой местности эффективны покрытия с применением дерева. В зависимости от конструкции и...
-
Бетонные покрытия при пониженных температурах воздуха строят с целью увеличения продолжительности строительного сезона. Эти работы требуют дополнительных...
-
Земляные работы, выполняемые при строительстве автомобильных дорог, как правило, не однородны по длине строящейся дороги. Объемы земляных работ...
-
Применяемый иногда в малоэтажном строительстве неорганизованый водоотвод может быть оправдан только в исключительных случаях, так как очень часто он...
-
Технология устройства мастичных кровель - Устройство кровель и изоляционных покрытий
Мастичные кровли получили распространение сравнительно недавно. Они экономичнее кровель из рулонных материалов и позволяют механизировать процессы по их...
-
Предварительно напряженные монолитные железобетонные и бетонные дорожные покрытия обеспечивают требуемую прочность и несущую способность при существенном...
-
Дорожный строительный асфальтобетонный армирование Чистовую профилировку основания следует производить на ширину, обеспечивающую движение ходовой части...
-
Важнейшей задачей службы эксплуатации автомобильных дорог является поддержание высоких сцепных качеств дорожных покрытий. Сцепные качества дорожных...
-
Эмалевые краски, Лакокрасочные защитные покрытия - Лакокрасочные материалы
Эмалевой краской (или сокращенно эмалью) называют композицию из лака и пигмента. Пленкообразующими веществами в эмалевых красках являются полимеры --...
-
Цементно-песчаную черепицу выпускают многие производители. За столетие технология производства цементно-песчаной черепицы шагнула далеко вперед, и...
-
Важнейшей проблемой строительства является дальнейшее совершенствование технологии бетона и железобетона, главным образом, позиции экономии цемента,...
-
ФОРМИРОВАНИЕ МИКРОКЛИМАТА ПОМЕЩЕНИЙ ГРАЖДАНСКИХ ЗДАНИЙ В ПЕРЕГРЕВНЫЙ ЛЕТНИЙ ПЕРИОД В климатических условиях Узбекистана летний микроклимат помещений...
-
Технология устройства защитных покрытии - Инженерная подготовка строительной площадки
Гидро - и пароизоляционные работы выполняют по завершению изготовления конструкции или монтажа сборных конструкций. Однако эти работы могут вестись...
-
Развитие механики грунтов позволило не только установить, какие грунты хорошо зарекомендовали себя в земляном полотне, но и создать теоретическую базу...
-
Классификация дорожных одежд, покрытий и оснований - Технология строительства дорожного полотна
Дорожной одеждой называют совокупность конструктивных слоев разной прочности, обычно уменьшающейся книзу, устраиваемых из различных материалов....
-
Пластмассами называют обширную группу органических материалов, основу которых составляют искусственные или природные высокомолекулярные соединения -...
-
Сборные покрытия из бетонных и железобетонных плит устраивают на участках дорог с неблагоприятными гидрогеологическими условиями земляного полотна, на...
-
Бетонные покрытия устраивают одинаковой толщины по всей ширине проезжей части с односкатным поперечным профилем для проезжей части с разделительной...
-
Исследование и разработка технологии получения бетона с использованием переработанных отходов стекла
Данная статья об использовании переработанного отхода стекла в качестве наполнителя в производстве бетона. Проведенное исследование позволяет утверждать,...
-
Рассмотрены теплоизоляционные и звукоизоляционные материалы на основе жидкого стекла, отверждаемые при повышенной температуре. Данные материалы...
-
Цементные и известковые краски В цементных красках связующим веществом является белый портландцемент; пигменты должны быть щелочестойкими. Для увеличения...
-
Технология устройства черепичных кровель - Устройство кровель и изоляционных покрытий
Из черепицы устраивают кровли с уклоном не менее 50%. Чрепичные кровли огнестойки, долговечны, экономичны в эксплуатации, но имеют весьма значительную...
-
Керамические материалы получают из глиняных масс путем формования и последующего обжига. При этом часто имеет место промежуточная технологическая...
-
Установки по приготовлению смесей необходимо размещать непосредственно у строящейся дороги, или в притрассовых карьерах, или у железнодорожных, водных...
-
Способ смешения на дороге. При этом способе щебень (гравий, грунт) смешивают непосредственно на дороге с органическим вяжущим. Для устройства покрытий...
-
Технология устройства рулонных кровель - Устройство кровель и изоляционных покрытий
Рулонные кровли устраивают из рулонных материалов, которые в зависимости от вида вяжущего делят на битумные и дегтевые, а по структуре - на покровные и...
Эмали и покрытия, Технология эмалей и неорганических покрытий, Физико-химические основы эмалирования - Стекло и эмали