Выбор и обоснование схемы установки, режима осуществления процесса - Гидрокрекинг вакуумного газойля
В зависимости от состава исходного сырья, назначения процесса, применяемых катализаторов и инженерных решений технологические схемы гидрокрекинга могут быть разделены на три основных категории:
Одноступенчатая одностадийная;
Одноступенчатая двухстадийная;
Двухступенчатая.
Технологические схемы принципиально схожи с установками гидроочистки - сырье, смешанное с водородосодержащим газом (ВСГ), нагревается в печи, поступает в реактор со слоем катализатора, продукты из реактора отделяются от газов и поступают на ректификацию. Однако, реакции гидрокрекинга протекают с выделением тепла, поэтому технологической схемой предусматривается ввод в зону реакции холодного ВСГ, расходом которого регулируется температура. Гидрокрекинг - один из самых опасных процессов нефтепереработки, при выходе температурного режима из-под контроля, происходит резкий рост температуры, приводящий к взрыву реакторного блока.
Аппаратурное оформление и технологический режим установок гидрокрекинга различаются в зависимости от задач, обусловленных технологической схемой конкретного НПЗ, и используемого сырья. Например, для получения малосернистого вакуумного газойля и относительно небольшого количества светлых (легкий гидрокрекинг), процесс ведется при давлении до 80 ат на одном реакторе при температуре около 350°С. Для максимального выхода светлых (до 90%, в том числе до 20% бензиновой фракции на сырье) процесс осуществляется на 2-х реакторах.
При этом, продукты после первого реактора поступают в ректификационную колонну, где отгоняются полученные в результате химических реакций светлые, а остаток поступает во второй реактор, где повторно подвергается гидрокрекингу. В данном случае, при гидрокрекинге вакуумного газойля давление составляет около 180 ат, а при гидрокрекинге мазута и гудрона - более 300. Температура процесса, соответственно, варьируется от 380 до 450°С и выше.
Совместное строительство установок гидрокрекинга и каталитического крекинга в рамках комплексов глубокой переработки нефти представляется наиболее эффективным для производства высокооктановых бензинов и высококачественных средних дистиллятов.
С разработкой эффективных аморфных и цеолитсодержащих алюмосиликатникельмолибденовых катализаторов, устойчивых к действию каталитических ядов, двухступенчатые схемы были заменены па одноступенчатые. При этом в случае производства среднедистиллятных продуктов (в основном, дизельного топлива) и сырья для пиролиза применяется одностадийная схема (процессы Эйч-Си Юнион фирмы UOP, гидрокрекинг фирмы Linde AG, гидрокрекинг фирмы BASF и Французского института нефти, гидрокрекинг фирмы British Petroleum International, изокрекинг фирмы Shevron Research, гидрокрекинг институтов ВНИИ НП -- ВНИПИНефть).
На рис. 2.1. показана типовая технологическая схема одностадийного варианта процесса. Смесь свежего сырья, рециркулирующего остатка, циркулирующего и свежего водорода нагревается до температуры реакции и подается в реактор. Продукты, выходящие из реактора, отдают тепло сырьевой смеси и поступают в сепаратор высокого давления, где отделяется циркулирующий газ, возвращаемый в реактор. Жидкие продукты, покидающие сепаратор высокого давления, проходят последовательно сепаратор низкого давления, колонну дебутанизации и поступают в ректификационную колонну, где они разделяются на компоненты.
Двухстадийная схема используется для получения более широкого ассортимента продуктов: сжиженного газа, бензина, реактивного топлива, дизельного топлива и др. (процессы юникрекинг фирмы Union Oil of California, гидрокрекинг фирмы Houdry-Giilf, хайкрекинг фирмы Exxson Research and Engineering, гидрокрекинг фирмы BASF и Французского института нефти, гидрокрекинг институтов ВНИИ НП и ВНИПИНефть).
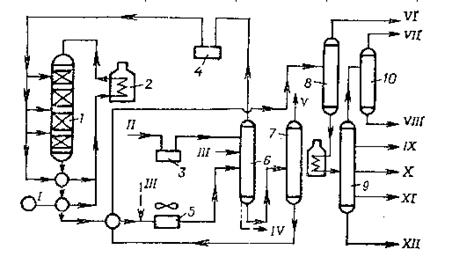
Рис 2.1. Одноступенчатая установка одностадийного гидрокрекинга: 1 - реактор; 2 - сырьевая печь; 3 - компрессор добавочного водорода; 4 - циркуляционный компрессор; 5 - воздушный холодильник; 6 и 7 - газожидкостные сепараторы высокого и низкого давления; 8 - стабилизационная колонна; 9 - фракционирующая колонна; 10 - колонна вторичной перегонки бензина; I - сырье; II - добавочный водород; III - вода; IV - кислые стоки; V - газ на очистку; VI - сжиженный нефтяной газ; VII - легкий бензин; VIII - тяжелый бензин; IX - лигроин; X - керосин; XI - газойль; XII - остаток.
В двухстадийном варианте процесса (рис. 2.2.) нагретое сырье и циркулирующий водородсодержащий газ смешивают и пропускают через реактор первой стадии для очистки от серы, азота и частично от ароматических углеводородов, после чего газосырьевая смесь вместе с рециркулирующим остатком и добавочным количеством водорода поступает во второй реактор для контакта с катализатором гидрокрекинга. Продукты, выходящие из второго реактора, отдают тепло сырьевой смеси и поступают в сепаратор высокого давления. Последующее движение продуктов реакции не отличается от предшествующей схемы.
Большинство промышленных установок гидрокрекинга работает под давлением 15--17 МПа с циркуляцией водородсодержащего газа, объемное содержание водорода о котором находится в пределах 80--85%. В отдельных случаях, например при производстве масел, давление поддерживается на уровне 20--25 МПа.
В последние годы получает распространение одностадийный процесс легкого гидрокрекинга вакуумного дистиллята при давлении 5--7 МПа с целью получения дизельного топлива и малосернистого сырья для каталитического крекинга.
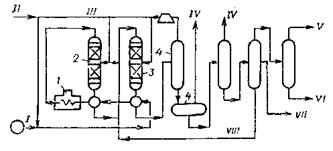
Рис. 2.2. Одноступенчатая установка двухстадийного гидрокрекинга: 1 - печь; 2 и 3 - первый и второй реакторы; 4 - газожидкостные сепараторы; I - сырье; II - добавочный водород; III - циркулирующий водород; IV - газ на ГФУ; V - легкий бензин; VI - тяжелый бензин; VII - среднедистиллятное топливо; VIII - рециркулирующий остаток.
Кратность циркуляции водородсодержащего газа по отношению к перерабатываемому сырью принимается, в зависимости от назначения процесса, в пределах 800--2000 м3/м3 (указан объем газа при нормальных условиях).
Характерным интервалом температур для процесса является 360--440 ОС постепенным повышением от нижней границы к верхней по мере отработки катализатора.
Объемная скорость подачи сырья зависит от качества сырья, применяемого катализатора, давления процесса и получаемых продуктов. При безостаточной переработке вакуумного дистиллята в моторные топлива она оставляет 0,2--0,5 ч-1, при ведении процесса в режиме легкого гидрокрекинга -- до 1 ч-1.
Окислительная регенерация катализатора проводится, как правило, без его выгрузки в токе инертного газа при давлении 3-5 МПа, температуре 480-520 °С.
Осернение катализатора выполняется при температуре 150-- 350 ОС, давлении 2--5 МПа в потоке циркулирующего водородсодержащего газа, содержащего (по объему) 0,5--5,0 % H2S, либо с помощью сераорганических соединений (меркаптаны, сульфиды, дисульфиды), а также легкими сернистыми нефтепродуктами.
Оборудование установок гидрокрекинга аналогично оборудованию установок гидроочистки нефтяного сырья. Различия имеются в реакторном блоке и обусловлены необходимостью работы при более высоком давлении. Реакторы гидрокрекинга имеют диаметр до 4 м, высоту до 30 м и массу до 500 т. Корпус обычно в многослойном горячей исполнении, рулонированный либо собранный из отдельных обечаек. В отдельных случаях применяются монолитные аппараты с в пут рент и; плакирующим покрытием из нержавеющей стали для предотвращения сероводородной коррозии.
Внутреннее пространство реактора разделено колосниковыми решетками на несколько секций, куда загружается катализатор. Над каждым слоем катализатора размещается контактно-распределительное устройство для смешения реагирующего потока с холодным водородсодержащим газом, его охлаждения и последующего равномерного распределения.
Газосырьевая смесь поступает в реактор через верхний штуцер, распределяется над слоем катализатора и движется последовательно через все секции. Продукты реакции выводятся через нижний штуцер.
В верхней части реактора необходимо предусматривать фильтрующее устройство для улавливания продуктов коррозии и механических примесей во избежание роста перепада давления и засорения слоя катализатора,
Единичная мощность однопоточного реакторного блока находится в пределах 300--1000 тыс. т/год по перерабатываемому исходному сырью. Мощности отечественных двухпоточных установок гидрокрекинга типа 68-2К и 68-ЗК составляют I млн. т/год по сырью и до 2 млн. т/год по суммарной сырьевой загрузке с учетом переработки непревращенного остатка. Производительность зарубежных установок находится на таком же уровне.
Наиболее широко в процессе гидрокрекинга применяется алюмокобальтмолибденовый катализатор, в последние годы стали также использовать катализаторы, содержащие никель и вольфрам.
Процесс гидрокрекинга остатков имеет в настоящее время два направления:
- 1) гидрообессеривание мазутов с целью получения маловязкого и малосернистого котельного топлива или сырья для каталитического крекинга; 2) углубленный гидрокрекинг с целью получения дополнительных ресурсов моторных топлив.
Процесс гидрообессеривания мазутов протекает в сравнительно мягких условиях на стационарном катализаторе. Предварительно мазут можно подвергать деасфальтизации - удалению смолистоасфальтеновых веществ. Технологическая схема процесса, его аппаратурное оформление ничем не отличаются от двухступенчатой установки гидрокрекинга вакуумного газойля.
В зависимости от качества сырья параметры процесса варьируются в следующих пределах:
Температура, ОС315-426
Давление, ат42-200
Объемная скорость, ч-11,0-4,5
Кратность циркуляции водорода, объем/объем700-1000
В результате процесса сера удаляется на 80%, металлы - на 60-70%, на 60% снижается коксуемость, падает содержание азота и вязкость. Кроме того, образуется небольшое количество газа и бензина.
Кроме установок со стационарным катализатором разработаны также установки с кипящим слоем катализатора, на которых можно перерабатывать более разнообразное остаточное сырье: мазуты, гудроны, тяжелые газойли коксования и каталитического крекинга, смолистые нефти.
Существует процесс гидрокрекинга в трехфазном кипящем слое, где твердая фаза представлена мелкосферическим алюмокобальтмолибденовым катализатором, жидкая фаза - смесью еще непрореагировавшего сырья с уже образовавшимися низколетучими продуктами, а газовая фаза - смесь водорода, сероводорода, аммиака и паров углеводородов. На этой установке можно перерабатывать даже тяжелое остаточное сырье с получением дизельного и котельного топлива. Спад активности катализатора полностью устраняется его регулярным обновлением без изменения и нарушения технологического режима.
Примером процесса с движущимся слоем катализатора может служить установка гидроойл (Н-ойл), где сырье и циркулирующий газ пропускают через слой алюмокобальтмолибденового катализатора восходящим потоком. Вследствие высоких линейных скоростей потока слой катализатора взрыхляется и зерна катализатора приходят в движение. В противоположность системам с кипящим слоем выноса катализатора из реактора с потоком газа и паров продуктов не происходит. Между поверхностью взрыхленного слоя катализатора и расположенным над ним паровым пространством существует резкая граница. Взрыхление катализатора сопровождается уменьшением гидравлического сопротивления слоя, что позволяет снизить размеры зерна катализатора до 0,8мм и обеспечить таким образом более эффективный контакт катализатора и сырья. В реакторе поддерживается температура 430-460ОС, давление 200-210 ат объемная скорость 1ч-1, расход водорода 2% на сырье.
В процессе применяется реактор с двумя реакционными зонами. Съем избыточного тепла реакции и регулирование температуры легко осуществляется при помощи рециркуляции жидкого продукта для каждой зоны. Такая рециркуляция одновременно облегчает задачу поддержания требуемой степени взрыхления слоя катализатора. Для сохранения активности катализатора на определенном уровне часть катализатора периодически выводится из системы и заменяется соответствующими порциями свежего катализатора. Выводится катализатор с низа входной зоны, где он наибольшей степени дезактивируется вредными компонентами сырья. Расход катализатора в зависимости от качества сырья составляет лт 0,0085 до 0,57кг/м3. Истирание катализатора в данном случае незначительно, так как движущиеся частицы обволакиваются пленкой сырья. В результате процесса можно получить до 50-60 вес.% малосернистых фракций с концом кипения 350-360ОС, состоящих на ? из парафино-нафтеновых углеводородов.
Широкое развитие гидрогенизационных процессов переработки нефти невозможно без достаточных ресурсов водорода. Основное количество водорода на нефтеперерабатывающих заводах получается в процессе каталитического риформинга. Однако при производстве малосернистых продуктов из сернистых и высокосернистых нефтей, а также при гидрокрекинге нефтепродуктов в больших объемах потребность в водороде не может быть удовлетворена только за счет платформинга. Дополнительно водород может быть получен двояким путем.
Во-первых, водород может быть выделен из водоросодержащих газов, метано - водородной фракции установок газоразделения, отдувочных газов установок гидроочистки и гидрокрекинга. Содержание водорода в этих газах колеблется от 30 до 60 объемн. %. Наиболее перспективные методы получения водорода с концентрацией 96-99 объемн. % - низкотемпературное фракционирование, адсорбция на молекулярных ситах, адсорбция нефтяными фракциями.
Во-вторых, водород можно получить специальными методами: каталитической конверсией углеводородных газов с водяным паром, термическим разложением углеводородных газов, газификацией тяжелого углеводородного сырья.
Установки гидрокрекинга, как правило, строятся большой единичной мощности - 3-4 млн. тонн в год по сырью. Обычно объемов водорода, получаемых на установках риформинга, недостаточно для обеспечения гидрокрекинга, поэтому на НПЗ сооружаются отдельные установки по производству водорода путем паровой конверсии углеводородных газов.
При использовании в качестве сырья прямогонного вакуумного газойля с относительно высоким содержанием серы, азота и полициклических ароматических углеводородов катализатор при работе в одну ступень быстро отравляется и теряет активность. Поэтому необходимо предварительно подготавливать сырье, т. е. проводить процесс в две ступени.
Вакуумный газойль, выделенный из нефти месторождения Танатар отличается невысоким содержанием серы, азота и полициклических ароматических углеводородов. Следовательно, для получения топлива из вакуумного газойля нефти Танатара выбираем одноступенчатый гидрокрекинг на алюмокобальтмолибденовом катализаторе.
Технологический режим процесса одноступенчатого гидрокрекинга вакуумного газойля:
Температура, ОС
На входе в реактор400-410
В сепараторе 50
Давление в реакторе, ат 50
Объемная скорость, ч-1 1
Кратность циркуляции водорода, объем/объем 600
Содержание водорода в циркулирующем газе
На входе в реактор, объемн. % 75
Тепловой эффект реакции, ккал/кг сырья 30-60
Пробег между регенерациями, ч 2000
Похожие статьи
-
Литературный обзор - Гидрокрекинг вакуумного газойля
Процесс гидрокрекинга предназначен для получения светлых нефтепродуктов -- бензина, керосина, дизельного топлива, а также сжиженных газов С3--С4 при...
-
Характеристика сырья, изготовляемой продукции и материалов В качестве основного сырья гидрокрекинга используется дистиллятный продукт вакуумной перегонки...
-
Для расчета схемы принимается 7,25 содержание класса. Согласно схемам I cтадия дает 20%. Q0=Q10=Q12=Q16 Q0= т/ч Q14=Q15=CIIQ10 Q13=Q10 т/ч QЧас=612,75...
-
Обобщенная схема выбора оборудования при бурении скважины - Буровые установки
Выбор бурового оборудования для бурения скважины является многофакторной задачей, решение которой в значительной мере способствует успешному проведению...
-
Выбор, обоснование и расчет схемы дробления - Джезказганское месторождение
Схема рудоподготовки, включающая операции дробления, грохочения и измельчения, намечается исходя из свойств руды на основе результатов исследований...
-
Расчет количественной схемы заключается в определении массы и выходов всех продуктов, а также характеристик крупности продуктов 5, 9 и 10(рисунок)....
-
Сечение линии выбирается по экономической плотности тока и по току нормального режима. Так как часов (режим работы двухсменный по 12 часов), то (для...
-
Обоснование выбора рекомендуемых способов эксплуатации скважин, устьевого и внутрискважинного оборудования С начала разработки месторождения ограниченные...
-
ОБЩИЕ СВЕДЕНИЯ, Назначение буровой установки - Анализ кинематической схемы буровой установки
Назначение буровой установки Буровая установка предназначена для бурения скважин различного назначения, отличающихся глубиной, диаметральными размерами и...
-
Критерии выбора скважин, Процесс ГРП - Гидравлический разрыв пласта
Критерии выбора скважин были определены исходя из особенностей строения Сугмутского месторождения и схемы его разработки. 1 Для проведения ГРП...
-
На 1 очереди применена коллекторная, а на 2 очереди ниточная схема. После компримирования на дожимной компрессорной станции, сырой газ с давлением до 9,5...
-
Рекомендации по выбору различных буровых станков и установок - Буровые установки
Основными факторами, определяющими выбор буровой установки, являются целевое назначение, глубина бурения, конечный диаметр скважин, характер и свойства...
-
Выбор схемы циркуляции жидкости - Объемный гидропривод
При решении этого вопроса надо учесть следующие обстоятельства. В открытой схеме всасывающая линия насоса и сливная - гидродвигателя разомкнуты между...
-
Выбор технологического режима бурения - Буровые установки
Под Режимом бурения понимается совокупность параметров, определяющих эффективность процесса разрушения пород тем или иным способом. Для равных способов...
-
Поскольку: То принимаем рабочее давление ОП 11,5 МПа. Выбираем обвязку колонковую клиньевую исходя из конструкции скважины и рабочего давления -...
-
Температурный режим пласта, скважин, промысловых и магистральных газопроводов является одной из важнейших характеристик, существенно влияющих на...
-
Выбор мельниц Расчетная производительность цеха измельчения определяется по заданной суточной производительности фабрики (т): = ;. = 13500 т/сут, = =...
-
Расчет и выбор дробилок Диаметр отверстия грохотов перед дробилками мелкого дробления и ширину разгрузочной щели дробилки принимаем равными диаметру...
-
Используя устройства СИНВ-П с разным временем замедления и соединения их в разной последовательности можно получить различные схемы инициирования. Это...
-
Буровые установки 3--го класса - Анализ кинематической схемы буровой установки
Примечание: Буровые установки БУ 80 БРД, БУ 2500 (приложение 3) и БУ 2500/160 ДГУ-М имеют практически одинаковые кинематические схемы. В случае нехватки...
-
Общая характеристика производства Проектная производительность Установки Комплексной Подготовки Газа -1В составляет 21 млрд. м3/год газа. Из-за...
-
Режимы работы газовых залежей - Основы добычи нефти и газа
Определение и виды режимов. Под режимом газовой залежи или режимом работы пласта понимают проявления доминирующей формы пластовой энергии, вызывающей...
-
Различаются два вида технологического режима: фактический и расчетный. Фактический технологический режим работы скважины устанавливается геологической...
-
Диагональные схемы проветривания, Выбор схемы проветривания шахты - Проектирование вентиляции шахт
Диагональные схемы характеризуются прямоточным движением воздуха от воздухопадающего ствола к вентиляционному стволу (рис.3). Достоинства диагональной...
-
Новый взгляд на процессы переработки минерального сырья
В статье рассмотрены вопросы изменения парадигмы переработки минерального сырья; предложены новые подходы, позволяющие снизить энергозатраты, улучшить...
-
Исходными данными при выборе буровой установки являются проектная глубина и конструкция скважины. Параметр "максимальная грузоподъемность" характеризует...
-
Схема дробления -- это графическое изображение последовательности операций при дроблении. Схемы дробления состоят из одной или нескольких стадий...
-
Технико-экономический анализ вариантов разработки, обоснование выбора рекомендуемого к утверждению варианта Оценка экономической эффективности проекта...
-
Одной из основных задач инженерной геологии является изучение и оценка геологических факторов, влияющих на условия строительства и эксплуатации...
-
Компьютерная обработка аэрокосмических снимков Для ГИС, предназначенной для решения различных научно-практических задач, важно использование информации,...
-
Обоснование выбора летательного аппарата - Проектирование аэрофотосъемки
Требования к летательному аппарату (ЛА), применяемому при аэрофотосъемке: ЛА должен обладать высокой продольной, поперечной и курсовой устойчивостью; ЛА...
-
Взрывная подготовка горных пород Исходные данные: - Разрушаемые горные породы - Крепкие мергели; - Коэффициент крепости - 8-10; - Категория...
-
Длина запроектированного теодолитного хода ([s]) составляет 595,624 м. Число сторон в ходе 6. Длины сторон хода: Sp1 - T1 = 62,367 м; Т1 - Т2 = 102,663...
-
Расчет и выбор дробилок Выбор дробилки для второй стадии дробления, так же как и для первой стадии, начинаем с определения ширины загрузочного и...
-
Большая часть месторождений природного газа разрабатывается в условиях водонапорного режима. Разработка газовых залежей в условиях водонапорного режима...
-
Полевые шпаты - 55% Пироксены и амфиболы - 15 Кварц и его разновидности - 12 Глинистые минералы - 1.5 Кальцит - 1.5 Вода в свободном и поглощенном...
-
Сначала определяем показатель трудности бурения МПа; МПа; МПа, Где усж, ур, усдв - соответственно пределы прочности на сжатие, растяжение и сдвиг; Г=2,9...
-
Конструкция скважины должна выбираться с учетом следующих условий: геологических условий проводки; условия совершенства применяемой техники и технологии...
-
КИНЕМАТИЧЕСКИЕ СХЕМЫ БУРОВЫХ УСТАНОВОК - Анализ кинематической схемы буровой установки
Кинематическая схема буровой установки представляет собой графическую модель, которая указывает, какими средствами реализуется движение составных звеньев...
-
Технологический цикл бурения включает: разрушение горных пород, извлечение выбуренного шлама на дневную поверхность и крепление стенок скважины. При...
Выбор и обоснование схемы установки, режима осуществления процесса - Гидрокрекинг вакуумного газойля