КАРБОНАТНОЕ ВЫЩЕЛАЧИВАНИЕ УРАНОВЫХ РУД. - Кучное биовыщелачивание
Карбонатное выщелачивание урана основано на образовании шестивалентным ураном растворимых комплексов натрия и аммония:
. По реакции (5.69) на 1 моль триоксида урана выделяется 2 моля щелочи. В сильно щелочной среде (при рН>11,6) может произойти частичное осаждение урана: NaOH6])CO(UO[Na2 OH3CONa6OUNa 3324 + - 722 +v + 232 (5.70). 137 По этой реакции регенерируется сода и ее в дальнейшем можно использовать для выделения урана из карбонатного раствора химическим осаждением. Но на стадии выщелачивания этот процесс вреден. Чтобы предотвратить накопление щелочи и осаждение урана для выщелачивания применяют смесь, состоящую из соды (70-90%) и бикарбоната натрия (10-30%). Последний нейтрализует выделяющуюся щелочь: NaOH NaHCO OHCONa + > + 2323 (5.71). Четырехвалентный уран не дает растворимых карбонатных комплексов и не переходит в раствор, поэтому его необходимо окислить до шестивалентного состояния. Для этого можно использовать перманганат калия, но эффективность данного окислителя в щелочной среде составляет 60% от его эффективности в кислой среде (в кислой среде марганец восстанавливается до 2+ Mn, принимая 5 электронов, в нейтральной и щелочной - только до MnO2 ). Кроме того, перманганат калия дорог и поэтому практически не применяется. Чаще всего окисление четырехвалентного урана при карбонатном выщелачивании производится кислородом воздуха при повышенном давлении в автоклавах по следующей реакции: + + + = 332422322 + NaOH2])CO(UO[NaOHO2/1CONa3UO (5.72). Это окисление становится заметным при температуре выше 70о С. Но скорость окисления мала, требуется несколько суток для завершения процесса (на канадском заводе Биверлодж при 75-80°C процесс выщелачивания длился 96 часов) [1, стр.120]. Форвард и Халперн дают следующее эмпирическое уравнение скорости карбонатного выщелачивания [46]: RT 50000 2 1 o O 83 ePFK d ]OU[d 2 ? ???= ф ? (5.73), где F - поверхность твердой фазы, K - o константа скорости реакции, О2 Р - парциальное давление кислорода в атмосферах, 50000 - энергия активации, Дж/моль. Согласно этому уравнению, для повышения скорости выщелачивания нужно увеличивать температуру и парциальное давление кислорода. Если руду месторождения Бивердлодж, содержащую уран в виде уранинита и настурана выщелачивать в автоклаве при давлении воздуха 7,7 атм. и температуре 104°C, при концентрациях карбоната натрия 138 40 г/л и бикарбоната натрия 20 г/л, то время выщелачивания сокращается до 16 часов [35, стр. 40]. Температура 104°C выбрана для того, чтобы сброс давления пульпы перед направлением ее на четырехступенчатую противоточную декантацию проводить без ее охлаждения. Если же выщелачивание проводить при 130-150°C, то перед сбросом давления пульпу нужно охладить до 104°C, то есть до температуры ниже температуры кипения раствора, которая выше 100°C за счет того, что растворенные соли снижают упругость паров воды и тем самым повышают температуру кипения раствора. При автоклавном выщелачивании достигается степень извлечения урана 90-95%. Скорость окисления и выщелачивания можно также увеличить, снизив энергию активации при применении катализаторов. Каталитическим действием обладают аммиакаты двухвалентной меди и железисто-синеродистый натрий [1, стр. 118], [35, стр. 82]. Автоклавное карбонатное выщелачивание нельзя проводить при повышенном содержании сульфидов из-за большого расхода соды [35, стр. 46]: ( ) 3 22322 3 42 NaHCO8 SONa4OHFe2OH7O 2 1 7CONa8FeS2 + + -++ +v + (5.74). Помимо этого получающиеся сульфаты осложняют последующий анионный обмен. При содержании сульфидов более 4% карбонатное автоклавное выщелачивание становится невыгодным. Для руды с содержанием серы 6,5% расход соды на выщелачивание увеличивается до 750 кг на тонну руды (вместо среднего расхода 30-40 кг/т). С другой стороны, полезным является вскрытие молибденита с получением молибдата натрия [13, стр. 202]: + -+ + CO6SONa4MoONa2O9CONa6MoS2 242422322 ^+ (5.75). Подобные руды лучше подвергать окислительному обжигу, в результате которого получатся трудновскрываемый оксид трехвалентного железа и легко вскрываемый кислотными и карбонатными растворами триоксид молибдена. Карбонатные растворы вскрывают примеси в гораздо меньшей степени, чем кислотные растворы (исключение составляют только сульфиды при автоклавном процессе). Карбонаты кальция и магния практически не затрагиваются, лишь ничтожная их часть переходит в раствор в виде бикарбонатов: NaOH2)HCO)(Mg(CaOHCONaCO)Mg(Ca + + 2323 - 23 + (5.76). Концентрация бикарбонатов кальция и магния в растворе составляет 0,05-0,06г/л в пересчете на сумму оксидов. Расход соды повышается, если кальций и магний присутствуют в виде сульфатов или оксидов: 139 324 СО SONa 423 + > )Mg(CaCONaSO)Mg(Ca +v (5.77), NaOH2CO)Mg(CaOHCONaO)Mg(Ca + 232 >+ 3 +v (5.78). Поэтому окислительный обжиг перед карбонатным выщелачиванием при большом содержании карбонатов кальция и магния нежелателен. Кремнезем очень мало вскрывается карбонатами даже при повышенной температуре: + - SiOHOHSiO 3222 + - + + COOHSiONaCONaSiOH 22323232 (5.79). Концентрация растворимого стекла ( SiONa 32 ) составляет 0,07- 0,4 г/л (в пересчете на SiO ), 2 что гораздо меньше, чем концентрация SiO2 в кислых растворах. Следовательно, первая стадия процесса (образование коллоидного раствора кремнекислоты) в присутствии серной кислоты идет более интенсивно. Сода в малой степени реагирует с OFe 32 , небольшое количество железа переходит в раствор в виде карбонатных комплексов, например: NaOH6])CO(Fe[NaOH3CONa6OFe + + 23232 - 333 + (5.80). Концентрация OFe 32 в растворе составляет 0,07-0,1 г/л (почти на 2 порядка меньше, чем при кислотном выщелачивании). В карбонатный раствор переходит незначительная часть алюминия в виде алюмината натрия (концентрация OAl 32 в растворе 0,09-0,6 г/л). + + 23232 > 2 + NaHCO2NaAlO2OHCONa2OAl 3 (5.81) Фосфор и ванадий вскрываются довольно полно с образованием растворимых ортофосфата и метаванадата натрия: P (5.82), + > CO3PONa2CONa3O 2433252 ^+ V (5.83). + 3252 > NaVO2CONaO CO23 ^+ Триоксид молибдена легко выщелачивается: MoO + > COMoONaCONa 242323 ^+ (5.84). Молибденит (MoS ) 2 вскрывается содой только в актоклавном процессе. Концентрация урана в растворе ~0,5-1 г/л. Концентрация урана в солевой части раствора (без учета избыточной концентрации соды ~20- 40 г/л) составляет 30-40%, что на порядок больше, чем при кислотном выщелачивании. Содержание урана в солевой части раствора в 200-300 раз больше, чем в руде. Высокая селективность карбонатного выщелачивания является основным преимущством его по сравнению с кислотным выщелачиванием. Другие преимущества карбонатного выщелачивания: 140 а) возможность регенерации соды, б) малая скорость коррозии аппаратуры, в) применимость к рудам с большим содержанием карбонатов. Следует отметить и недостатки карбонатного выщелачивания по сравнению с кислотным: а) необходимость более тонкого измельчения, так как оболочка минералов пустой породы содовыми растворами не вскрывается и поэтому нужно обеспечить обнажение зерна уранового минерала хотя бы в одной плоскости, в связи с чем измельчение ведут до 0,07-0,13 мм в зависимости от вкрапленности, б) меньшая скорость выщелачивания, большая продолжительность процесса, в) меньшая степень извлечения урана, хотя с применением автоклавного выщелачивания эта разница сокращается.
Бактериальное кучное - выщелачивание полезного компонента при участии определенных видов бактерий, способных окислять и ускорять растворение минералов полезного компонента [13].
Фирма "Mt. Leyshon" предлагает перерабатывать упорные золотые руды в присутствии минералов меди, разрушение которых способствует выходу меди в раствор. При этом медь удаляется из раствора, а последующее выщелачивание золота цианидом протекает при значительном сокращении реагента. Такой комбинированный подход возможно использовать для переработки сложных руд, а также для переработки отходов медно - обогатительных фабрик, содержащих золото и медь.
Технология, разработанная фирмой "Geobiotics", получившая название "GeocoatТМ" и прошедшая опытные испытания, включают в себя нанесение концентратов упорной золотой руды на грохоченную породу, которая может быть представлена пустой породой или забалансовой золотосодержащей рудой. Обработанный материал укладывается в кучу. После бактериальной обработки окисленный материал перерабатывается традиционными гидрометаллургическими методами. Авторами также разработана технология цикличного извлечения металлов из оборотных растворов. После биокоррекции рН выходящего раствора и добавления части осадка, содержащего трехвалентное железо, раствор возвращают на кучу для продолжения микробиологического орошения [14].
В одном из вариантов кучного выщелачивания предлагается использовать в качестве выщелачиваемого реагента как руду, так и концентрат. При этом золотомышьяковистый концентрат с содержанием золота 53,3 г/т гранулируют с использованием портландцемента марки 500 и закисного железа. Полученные гранулы укладывают в кучу и орошают бактериальным раствором Acidithiobacillus ferrooxidans в течение 80 суток до полного разрушения гранул. Окисленный концентрат подвергается цианированию [15].
Наиболее удачными экспериментами по кучному бактериальному выщелачиванию золотосульфидных руд являются исследования, проведенные фирмой "Newmont corporation" и ее главным микробиологом J. Brierley, завершившиеся созданием промышленных куч по 1 млн. тонн. Проведенные ими экспериментальные исследования позволили выявить, что при кучном выщелачивании руды месторождения Карлин температура внутри кучи может подниматься до 700 в отдельных ее участках и мезофильная ассоциация бактерий, состоящая преимущественно из Acidithiobacillus ferrooxidans, Acidithiobacillus thiooxidans и Leptospirillum ferrooxidans погибает. Таким образом, процесс бактериально - химического окисления сульфидных минералов практически прекращался.
Brierley et all было предложено вносить в кучу и в рудный материал ассоциацию бактерий, состоящую из Acidithiobacillus ferrooxidans, Acidithiobacillus thiooxidans, Leptospirillum ferrooxidans, Acidithiobacillus organoparus, Acidithiobacillus acidophillus, Sulfobacillus thermosulfidooxidans, Sulfolobus acidocaldarius [15]. Выращенные в отдельных емкостях мезофильные и термофильные бактерии подавались вместе с небольшим количеством глины и цемента, а также руды, дробленной до 12,7 мм, в специальный смеситель, в котором осуществлялась агломерация клеток на руду. Затем агломерационная руда доставлялась на участок кучного выщелачивания, где ее укладывали в кучу. Орошение кучи проводилось 1 - 2 раза в неделю раствором питательной среды, который по мере орошения обогащался окисленным железом, ионами кобальта, никеля и др. Куча вентилировалась и процесс кучного выщелачивания длился от 100 до 270 суток. Окисленная руда затем удалялась с подушки, нейтрализовалась, измельчалась и подвергалась цианированию с последующей сорбцией металлов на активированный уголь. Извлечение золота составляло от 60 до 80% от исходного содержания в зависимости от минералогического и гранулометрического состава руды.
Следует отметить принципиально новый подход, осуществленный авторами - это агломерация бактерий на руду и орошение питательными растворами, что предполагает развитие микроорганизмов на кусочках руды. С целью интенсификации бактериально - химических процессов в агломерирующую смесь добавляли синтетический полимер, что способствовало склеиванию мелких частиц руды, а также увеличивало степень прикрепления бактериальных клеток на руду.
Успешные лабораторные и опытно - промышленные испытания позволили "Newmont corporation" перейти к промышленным масштабам внедрения технологии биоокисления сульфидных минералов в варианте кучного выщелачивания [16, 17].
Проведенный анализ современного состояния проблемы кучного выщелачивания с применением микроорганизмов показывает, что необходимо строгое апробирование метода выщелачивания, т. к. региональный состав руд и вмещающих пород требует индивидуальных подходов к технологии ведения процесса. Так, высоко карбонатные руды менее податливы к бактериальному выщелачиванию. Но предварительное кислотное орошение, которое успешно применяется при кучном выщелачивании меди, способствует использованию этих руд в режиме бактериального выщелачивания.
Возможности применения бактериального выщелачивания
Из-за огромных масштабов операций по выщелачиванию отвалов активность бактерий, развивающуюся в ходе процесса, можно контролировать только в ограниченной степени. Для наиболее эффективного использования бактериального выщелачивания необходимо создавать такие инженерные схемы, которые позволяли бы осуществлять определенный контроль за активностью микробов. Помимо выщелачивания отвалов в горнорудной промышленности существуют и другие средне - и высокотехнологичные процедуры, при которых для экстракции металлов используются гидрометаллургические процессы (реакции, происходящие в воде). Эти технологии (выщелачивание in situ, чановое выщелачивание, кучное выщелачивание) применимы и к процессам бактериальной экстракции металлов.
Выщелачивание in situ с успехом используют для извлечения урана из песчаниковых формаций с низким содержанием рудного минерала. Выщелачивающие растворы вводят в неразрушенное урансодержащее рудное тело через инъекционную скважину. Эти растворы, содержащие химический окислитель (например, перекись водорода), взаимодействуют с минералом, окисляя уран и переводя его в растворимую форму. Далее урансодержащие растворы выкачивают из минерализованной зоны через выходные скважины (рис. 5.2).
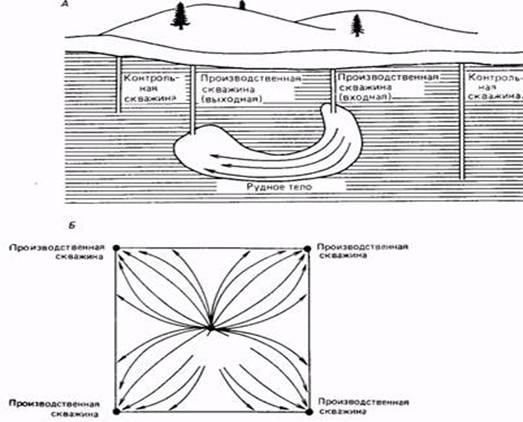
Рис. 5.2. Схематическое изображение процесса выщелачивания in situ. А. Контрольные скважины для отбора проб с целью наблюдения за передвижением выщелачивающего
На западе США и в южном Техасе, где широко практикуется выщелачивание in situ, применяют карбонатные растворы с нейтральным рН. По всей видимости, бактерии в этом процессе экстракции не участвуют. Технология in situ находит применение не только при выщелачивании урана. Тот же подход возможен и при экстракции других металлов, присутствующих в низких концентрациях в глубоко залегающих месторождениях. Бактерии могут использоваться для выщелачивания сульфидных минералов или для разрушения жильных минералов при извлечении металлов с помощью других гидрометаллургических технологий. Большинство исследований по использованию бактерий для выщелачивания in situ было проведено в лаборатории при высоких давлении и температуре. Эти исследования показали, что гидростатическое давление в 30,4 МПа (эквивалентное давлению на глубине в 3000 м) не сказывается на жизнедеятельности раствора из рудного тела. 5. При обычно используемой для выщелачивания in situ схеме "пяти точек" объем выщелачивающего раствора, выкачиваемого из четырех рабочих скважин, больше, чем объем вводимого раствора. Это сводит к минимуму возможность загрязнения подпочвенных вод.
Железоокисляющих бактерий. Однако при закачивании растворов на большую глубину ограничивающим фактором для использования бактерий может оказаться гипербарический кислород. Влияние высокой температуры, существующей на большей глубине, недостаточно изучено. Не исключено также, что из-за более низкой проницаемости для бактерий монолитных, сильно уплотненных включений в месторождениях эффективность выщелачивания резко уменьшается. Эта возможность также не изучалась детально. Несмотря на все эти пробелы в наших знаниях, можно утверждать, что достоинством технологии in situ является то, что она представляет собой систему, в которой можно контролировать много факторов, в том числе содержание кислорода и питательных веществ, рН т. д.
Перспективы извлечения золота методом кучного выщелачивания в холодных климатических регионах России
Необходимость вовлечения в переработку нетрадиционного сырья (бедные и забалансовые руды, кондиционные руды маломощных месторождений, отходы горнообогатительного производства и др.) вызвана истощением запасов богатых золотосодержащих руд. Переработка такого сырья по традиционной фабричной технологии нерентабельна, а вовлечение в промышленную эксплуатацию этих продуктов позволяет значительно увеличить сырьевую базу и добычу благородных металлов.
Наибольшее распространение в мировой практике получил метод кучного выщелачивания (КВ). Этот метод используется за рубежом в промышленной практике с начала 1970-х годов. В настоящее время метод КВ прочно вошел в промышленную практику золотодобычи США, Австралии, Канады, Мексики, Бразилии, Саудовской Аравии, Индонезии, Новой Гвинеи, Чили, Зимбабве, Ганы и др. Более 40 % мировой золотодобычи приходится на технологию КВ.
Многолетняя практика работы зарубежных предприятий КВ подтверждает их высокую технико-экономическую эффективность. По сравнению с традиционными фабричными технологиями КВ характеризуется низкими капитальными вложениями и эксплуатационными затратами, меньшим энерго - и водопотреблением, высокой производительностью труда, щадящим экосистему уровнем производства, низкой себестоимостью добычи золота и серебра, что позволяет вовлекать в отработку бедное золотосодержащее сырье с содержанием золота выше 0,5 г/т. Основными недостатками КВ по сравнению с фабричной технологией является, как правило, меньшее извлечение и сезонность работы.
Особенно актуальна в настоящее время проблема внедрения КВ в России. Из-за отсутствия государственных инвестиций в разработку новых месторождений строительство фабрик стало невозможным. Из-за низкой мировой цены на золото и увеличения цен на энергоносители большинство действующих предприятий стали убыточными, некоторые законсервированы и объявлены банкротами. Даже старательская золотодобыча многих россыпных месторождений стала нерентабельной.
Опыт внедрения за последние три года первых куч в России на месторождениях "Майское", "Чазы-Гол" (Хакасия), "Холодное", "Лопуховское", "Канавное", "Центральное" (Алданский район) /1,2,3,4/ показал высокую эффективность КВ: получено более 2 т золота.
В 1993 г. для месторождения "Майское" был разработан ОАО "Иргиредмет" технологический регламент, а институтом "Сибгипрозолото" выполнен проект КВ на 100 тыс. т. в год. В начале 1994 г. ЗАО ЗДК "Золотая звезда" был достроен рудник Майский, а в июне 1994 г. произведен запуск первой блок - секции в 50 тыс. т.
Технология КВ включала: рудоподготовку -- дробление по классу -10+0 мм; укладку руды в штабель, орошение рудного штабеля раствором цианистого натрия с концентрацией 0,4-0,5 г/л и рН=10-11 при плотности орошения 150-160 л/м2 сут; сбор золотосодержащих растворов; осаждение из растворов цинковой стружкой; обработку золотоцинковых осадков кислотой; сушку и прокалку осадков; плавку осадков с флюсами и получение золота лигатурного в слитках; обезвреживание отработанных руд.
Добытая в карьере руда доставляется на дробильно-сортировочный комплекс (ДСК) автосамосвалами грузоподъемностью 27 тонн. Дробление руды осуществляли в две стадии в щековой дробилке СМД-186 и конусной дробилке КМД-1200. Руда перед дроблением подвергается грохочению для отделения глинистой фракции, которая в дальнейшем смешивается бульдозерами с готовым классом руды. Формирование штабеля производилось бульдозерами Т-130, а доставка руды в штабель -- автосамосвалами грузоподъемностью 27 т. Укладка руды производилась на специально подготовленное основание. На спланированное естественное грунтовое основание с продольным уклоном 0,05 и поперечным уклоном 0,01, был уложен послойно с уплотнением каждого слоя дорожным катком слой глины толщиной 500 мм и на него уложена поливинилхлоридная пленка толщиной 0,45 мм марки "ОН", выпускаемая АООТ "Химпласт" г. Новосибирск. Соединения пленки проводили методом склеивания раствором поливинилхлоридной хлорированной смолы в ацетоне. На пленку был уложен защитный слой из отсева руды толщиной 100 мм и в нем смонтирована дренажная сеть из перфорированных труб для вывода продуктивных растворов, после чего был отсыпан слой руды высотой 6 м.
Первоначально для орошения рудного штабеля была смонтирована система капельного орошения, замененная впоследствии на прудковую систему орошения. Системы орошения с применением разбрызгивателей типа газонных или качающихся трубок также не нашли применение из-за практически постоянно дующих ветров.
В сезоне 1994 г. было переработано 108 тыс. т. руды с содержанием 4,9 г/т и было получено 278,5 кг золота. Всего за четыре сезона эксплуатации переработано более 400 тыс. т руды и получено более 1,8 т золота, при этом среднее извлечение составило 73,1 %.
Успешная эксплуатация Майского рудника позволила компании не только выжить в непростых условиях, но и продолжать наращивание производственных мощностей. В 1995 г. ОАО "Иргиредмет" выдал технологический регламент, а специалисты компании выполнили рабочий проект по производству золота методом КВ на участке Кузнецовский месторождения "Чазы-Гол" в Хакасии. Параллельно с разработкой и утверждением проекта осуществляли строительство ряда промышленных объектов и в 1997 г был проведен запуск первой блок-секции в 180 тыс. т и получено более 100 кг золота в виде слитков пробностью более 85 %. На участке запланировано перерабатывать около 500 тыс. т руды в год с содержанием 2,6-3 г/г и извлечением 75 % золота.
(25 тыс. т), "Центральное" (24 тыс. т), "Лопуховское" (100 тыс. т). Содержание в рудах колебалось от 1г/т "Лопуховское" до 8 г/г "Холодное", при этом извлечение золота составило не менее 60%.
В 1998 г ЗАО Артелью старателей "Амур" и ОАО "Иргиредмет" на месторождении "Комсомольская залежь" успешно произведен запуск технологии кучного выщелачивания в условиях вечной мерзлоты. Месторождение "Комсомольская залежь" находится на северо-западе Хабаровского края на южных отрогах Станового хребта. Было заложено 5,5 тыс. т. окомкованой руды со средним содержанием золота 35 г/т и серебра 152 г/т. За весь период выщелачивания было получено более 800 кг лигатурного сплава. В 1999 г. ЗАО АС "Амур" планирует увеличить производительность кучного выщелачивания до 25 тыс. т. руды.
Начиная с 1965 г. в ОАО "Иргиредмет" накоплен опыт по разработке технологии КВ золотосодержащего сырья (руд, рудопроявлений, отвалов, хвостов эолотоизвлекательных фабрик). Наши специалисты могут провести геологическую оценку, лабораторные и полупромышленные испытания по технологии КВ, разработают технологический регламент и проект, окажут помощь в его согласовании и осуществят руководство внедренческими работами.
В 1999-2000 гг. по разработкам ОАО "Иргиредмет" планируется запуск установок КВ на месторождениях "Синюхинском" в республике Горный Алтай, "Тас-Юрях" в Хабаровском крае, "Самсоновское" в Красноярском крае, "Бамское"в Амурской области, "Чертово корыто" в Иркутской области, "Таборное"в Якутии.
Месторождение "Тас-Юрях" и "Комсомольская залежь" расположены географически на близкой широте и в климатических условиях (минимальные зимние температуры, продолжительность сезона положительных температур, резко континентальный климат), подобных Бруверли Крик (провинция Юкон, Канада). Их промышленное освоение по технологии КВ имеет принципиально важное значение как в качестве опытно-показательного полигона для наработки опыта эксплуатации данной технологии в суровых северных условиях, в которых расположено подавляющее большинство золоторудных месторождений России, так и в качестве убедительного аргумента в пользу дальнейшего широкого вовлечения в эксплуатацию по технологии КВ подобных месторождений залицензировавшими их предприятиями.
Опыт Брувери Крик показывает, что даже в очень суровых климатических условиях (в зимние месяцы температура достигает -45 0С и ниже) возможно ведение процесса КВ круглогодично. Для чего в зимний период разработаны специальные конструктивные решения: линия капельных эммитеров погружается непосредственно в руду и до наступления зимы покрывается 4 метровым слоем руды с целью изоляции, все наружные трубопроводы изолируются, насыщенный раствор непосредственно поступает на фабрику, а обезметалленный раствор поступает сразу в систему орошения кучи. На фабрике предусмотрена система подогрева (в случае необходимости) растворов.
Широкое внедрение КВ позволит значительно поднять объем золотодобычи в России.
Геомембраны (полимерные листы) для гидротехнических сооружений и кучного выщелачивания золота и их технические характеристики
Геомембрана, или ее также называют "полимерный лист", - это интетический гидроизоляционный материал, изготовленный из специальных сортов полиэтилена. Она поставляется в рулонах шириной от до 5 м. Ее раскатывают на участке, где требуется гидроизоляция. Швы между соседними листами свариваются специальными аппаратами, так что вся поверхность становится абсолютно герметичной. Таким образом, поверхность, покрытая геомембраной (полимерными листами), становится водонепроницаемой.
Геомембраны (полимерные листы) находят широкое применение в строительстве гидротехнических сооружений: бассейнов, отстойников, хвостохранилищ, плотин. При добыче золота кучным выщелачиванием они укладываются под основание рудных штабелей и на дно бассейнов для продуктивных и отработанных растворов.
Требования к геомембранам, применяемым в кучном выщелачивании, самые высокие. На то есть важные причины:
Причина первая - при прорыве геомембраны могут возникнуть большие неприятности, так как цианистые растворы ядовиты и их попадание в грунт и грунтовые воды недопустимо.
Причина вторая - при прорыве геомембраны вместе с цианистым раствором будет потеряно золото, которое в нем содержится. Это может быть причиной снижения извлечения золота из руды.
Найти и заменить испорченный участок геомембраны в ходе производственного процесса практически невозможно.
В настоящее время выпускают геомембраны для различного применения. Они отличаются по типу сырья, из которого изготовлены полимерные листы (HDPE - полиэтилен высокой плотности низкого давления, MDPE - полиэтилен средней плотности, LDPE - полиэтилен низкой плотности высокого давления, LLDPE - линейный полиэтилен), толщине и размеру листов, а также по техническим характеристикам и цене.
Основные характеристики геомембран следующие:
Прочность на разрыв при растяжении
Относительное удлинение при разрыве
Трещиностойкость
Химическая стойкость
Устойчивость к ультрафиолету
Морозоустойчивость
Важнейшее свойство геомембран - прочность на разрыв (минимальное значение напряжения при растяжении, при котором происходит разрушение материала). В зависимости от типа исходного сырья прочность геомембран на разрыв может изменяться как в меньшую, так и в большую сторону. При использовании полиэтилена марки LDPE эта величина может достигать 25 МПа, если же используется полиэтилен HDPE, эта величина может достигать 35 МПа. Чем выше этот показатель, тем более устойчива к разрыву геомембрана.
Относительное растяжение также относится к важным свойствам для ответственных гидротехнических сооружений и, особенно, для кучного выщелачивания. В рудных штабелях геомембрана работает под большим давлением грунта, кроме того грунт может двигаться и просаживаться. Даже мембрана высокой прочности не может противодействовать движениям грунта. Здесь нужна ее пластичность, то есть при движениях грунта геомембрана должна не рваться, а растягиваться без разрывов. Для хороших современных геомембран растяжение достигает от 400 до 1000% .
Трещиностойкость - способность геомембраны воспринимать действующие на нее ударные нагрузки без образования трещин. Ударные нагрузки могут возникать при отсыпке первых слоев рудного штабеля. Учитывая различные климатические условия, геомембрана должна обладать повышенной трещиностойкостью также при низких температурах северных регионов России.
Устойчивость к ультрофиолету и термоокислению очень важные показатели, от них на прямую зависит срок службы геомембраны, геомембраны применяемые в кучном выщелачивании должны обладать высокой стойкостью к ультрафиолетовому излучению (неизменяемость физико-механических характеристик при длительном воздействии ультрафиолета) и термоокислению (один из наиболее распространенных и важных процессов, в котором участвуют полимерные материалы. Этот процесс сопровождает получение геомембран, эксплуатацию и обычно приводит к ухудшению свойств материала), от этих показателей зависит как долго прослужит геомембрана без разрушения.
Толщина и тип геомембраны (соответственно цена) выбираются в зависимости от будущих условий ее эксплуатации. При этом необходимо учитывать характер поверхности, нагрузку на геомембрану, возможную величину просадки и подвижки грунта, агрессивность среды и др. При расчетах и проектировании можно руководствоваться "Рекомендациями по проектированию и строительству противофильтрационных экранов с применением геомембраны "ПромГеоПласт". Они разработаны Новосибирским Государственным Проектным Институтом в помощь проектным организациям, с учетом применения существующих современных геосинтетических материалов при строительстве противофильтрационных экранов в гидротехнических сооружениях.
На заводе "ПромГеоПласт" выпускается геомембрана из специальных сортов полиэтилена высокого (LDPE), линейного (LLDPE), среднего (MDPE), или низкого (HDPE) и имеет сертификаты (ГОСТ Р, Стройсертификация).
Современное оборудование завода обеспечивает выполнение любых по объему заказов. Производительность оборудования до 33 тонн в сутки.
Качество каждой партии продукции оперативно контролируется в лаборатории предприятия и имеет сертификаты (ГОСТ Р, Стройсертификация).
Специалисты "ПромГеоПласт", инженеры-гидротехники, оказывают проектировщикам помощь в расчетах при выборе геомембраны и конструкции покрытия.
"ПромГеоПласт" также предоставляет услуги по укладке геомембраны. Раскрой полотен, монтаж и сварка производятся опытными специалистами, имеющими современное сварочное оборудование. Комплексные работы (производство и монтаж), обеспечивают гарантированное качество гидроизоляции в любых условиях и надежную защиту грунтовых вод от вредных воздействий продуктов жизнедеятельности, в том числе техногенных, вплоть до 1 класса опасности.
Завод "ПромГеоПласт" находится в г. Новосибирске. Это обеспечивает быструю и недорогую отгрузку продукции всем предприятиям России любым видом транспорта.
Похожие статьи
-
Кислотно-содовое выщелачивание - Кучное биовыщелачивание
Поскольку кислотное выщелачивание обеспечивает высокую скорость процесса и большую степень извлечения урана, а карбонатное выщелачивание дает более...
-
Введение, Биовыщелачивание. Основные понятия - Кучное биовыщелачивание
На сегодняшний день гидрометаллургия является одним из важнейших производственных процессов. Именно поэтому проблема получения металлов, как можно с...
-
Опыт освоения технологии кучного биовыщелачивания - Кучное биовыщелачивание
Технология кучного выщелачивания характеризуется многими достоинствами, в том числе небольшими капитальными вложениями. Однако, упрощенное отношение к...
-
Кучное биовыщелачивание - Кучное биовыщелачивание
Кучное биовыщелачивание -- способ переработки химическим или бактериальным выщелачиванием попутно добытых забалансовых и бедных балансовых...
-
Основные этапы развития кучного биовыщелачивания - Кучное биовыщелачивание
Современная технология кучного выщелачивания благородных металлов получила свое развитие в основном в последние 20 лет, хотя применение этого метода...
-
Вывод, Список литературы - Обогащение золотосодержащих руд
Процесс обогащения представляет собой единую систему, в которой отдельные элементы являются взаимосвязанными. Добиться высоких результатов можно только с...
-
Цианирование золотосодержащих руд - Обогащение золотосодержащих руд
Реакция растворения золота в слабых растворах цианистых солей в присутствии кислорода, открытая П. Р.Багратионом, в сравнительно короткий срок нашла...
-
Сырье для получения золота - Обогащение золотосодержащих руд
Источниками получения металлического золота являются собственно золотые руды, полиметаллические сульфидные руды и вторичное сырье - промышленный и...
-
Осаждение золота из цианистых растворов - Обогащение золотосодержащих руд
Растворы после цианирования, отделенные от кека и содержащие избыточный цианид, щелочь и кислород, поступают на осаждение золота. Для осаждения золота из...
-
Аффинаж благородных металлов - Обогащение золотосодержащих руд
Золото сырье руда цианирование Аффинаж - металлургическая технология очистки благородных металлов от примесей и разделения их друг от друга. На...
-
Введение - Обогащение золотосодержащих руд
Источниками получения металлического золота являются: - собственно золотосодержащие руды; - полиметаллические золотосвинцово-цинковые и...
-
"Переработка животноводческой продукции" - Переработка животноводческой продукции
Способы пастеризации, длительное, кратковременное и мгновенное. Эффективная пастеризация. Критерии Пастера Действие пастеризации на микроорганизмы,...
-
Завод по производству алюминия, Руды алюминия - Металлургия аллюминия
Производство этих металлов росло и продолжает расти очень быстро. Алюминия сейчас производят в мире больше, чем меди или цинка, магния - почти столько...
-
Сплав Д1 - относится к числу дюралюминов. Такой вид сплавов обладает достаточно высокой прочностью, пластичностью и относится к числу нормальных...
-
Практическая часть, Органолептическое исследование меда - Ветеринарно-санитарная экспертиза меда
Методы исследования меда довольно разнообразны. Дело в том, что мед является многокомпонентным продуктом и для него до сих пор не определен общий...
-
Гравитационное обогащение золотосодержащих руд - Обогащение золотосодержащих руд
Для выделения наиболее крупного золота из кварцевых золотосодержащих руд успешно используют гравитационные методы. Иногда гравитационный концентрат или...
-
Применение золота - Обогащение золотосодержащих руд
Широкое применение благородных металлов и сплавов в современной технике и быту связано в первую очередь с такими свойствами, как химическая и...
-
Щебень для дорожного строительства Щебень является одним из основных материалов, применяющихся для строительства, ремонта и содержания, автомобильных...
-
Производство стали - Разработка технологического процесса изготовления детали "зубчатое колесо"
Сущность процесса Основными материалами для производства стали являются передельный чугун и стальной лом (скрап). Содержание углерода и примесей в стали...
-
Паровые машины высокого давления - Паровые машины
В паровых машинах пар поступает из котла в рабочую камеру цилиндра, где расширяется, оказывая давление на поршень и совершая полезную работу. После этого...
-
Сплавы алюминия - Особенности выплавки алюминиевых сплавов
Прочность чистого алюминия не удовлетворяет современные промышленные нужды, поэтому для изготовления любых изделий, предназначенных для промышленности,...
-
Термином "золь-гель технология" обозначают технологию получения технически ценных неорганических и органо-неорганических материалов (катализаторы,...
-
Результирующая вольт-амперная характеристика туннельного диода определяется комбинацией туннельных и тепловых свойств и имеет довольно необычный вид. В...
-
Основой большинства современных легированных сталей является феррит, легированный одним или несколькими элементами. Легирование феррита сопровождается...
-
Что такое чугун? Применения чугуна. - Чугун и сталь
Чугун -- сплав Fe (основа) с С (обычно 0...0 %), содержащий постоянные примеси (Si, Mn, S, Р), а иногда и легирующие элементы (Cr, Ni, V. А0 и др.); как...
-
Особенности эксплуатации гидропривода в условиях низких температур
Особенности эксплуатации гидропривода в условиях низких температур Широкое применение гидравлического привода в самой разной технике и промышленном...
-
По объему, качеству и сортаменту выпускаемых ферросплавов промышленность Казахстана находится на уровне технически развитых стран, но при этом отстает от...
-
ХАРАКТЕРИСТИКА МОЛОКА РАЗЛИЧНЫХ ЖИВОТНЫХ, СЛИВКИ - Кисломолочные продукты
Наряду с коровьим в народном хозяйстве используют молоко других животных. ОВЕЧЬЕ МОЛОКО по сравнению с коровьим богаче жиром и белком и характеризуется...
-
Алюминиевые бронзы - Термообработка деталей и инструментов
Алюминиевые бронзы - сплавы на основе меди, в которых главным легирующим элементом является алюминий. Применяют двух - и многокомпонентные сплавы....
-
Свойства масляных СОЖ условно разделяют на пять групп: физико-химические и функциональные свойства; химическая активность; эксплуатационные и...
-
Хранить пшено нужно в чистых, хорошо вентилируемых, не зараженных амбарными вредителями помещениях, соблюдая санитарные нормы и правила. Тару с крупой...
-
Газонаполненные пластмассы - Характеристика и структурные методы исследования металлов
Газонаполненные пластмассы представляют собой гетерогенные дисперсные системы, состоящие из твердой и газообразной фаз. Структура таких пластмасс...
-
Действие уксусных бактерий приводит к превращению этанола в уксусную кислоту (СН3СООН). Это обстоятельство используется при производстве уксуса. Примерно...
-
Поверхностная закалка - Характеристика и структурные методы исследования металлов
Это закалка, при которой только поверхностный слой изделия нагревают до заданной температуры. При поверхностной закалке на некоторую (заданную) глубину...
-
Получение сульфата аммония основано на поглощении аммиака из коксового газа раствором серной кислоты и протекании реакции нейтрализации....
-
Плавка стали в основной дуговой электропечи. - Производство стали
Сырые материалы. Основным материалом для электроплавки является стальной лом. Лом не должен быть сильно окисленным, так как наличие большого количества...
-
В настоящее время резка металла приобретает все большее значение. Это происходит в первую очередь за счет увеличения объемов производства с которыми не...
-
Рассчитаем необходимое число единиц гипсоварочных котлов, согласно формуле: N=Pп/(Pч-K), Где Pп - требуемая часовая производительность предприятия; Pч -...
-
Подготовка сырья к производству - Производство хлеба бородинского
Для получения полуфабрикатов (опары, закваски, теста) требуемого качества и нужных свойств необходимо соответствующим образом подготовить сырье к пуску в...
-
Основные нормы технологического режима работы аммиачного абсорбера приведены в таблице 2. Таблица 2 - Показатели технологического режима [5] Наименование...
КАРБОНАТНОЕ ВЫЩЕЛАЧИВАНИЕ УРАНОВЫХ РУД. - Кучное биовыщелачивание